Variants of using expanded polystyrene for insulating floors of different types, the advantages and disadvantages of this method of thermal insulation, the choice of consumables. Thermal insulation of the floor with expanded polystyrene is an affordable and simple option for keeping heat indoors at any stage of building construction. The use of this material brings other benefits: it absorbs noise on interfloor ceilings and serves as a good vapor barrier. Where insulation is used and how to install it, we'll talk in this article.
Features of work on floor insulation with expanded polystyrene
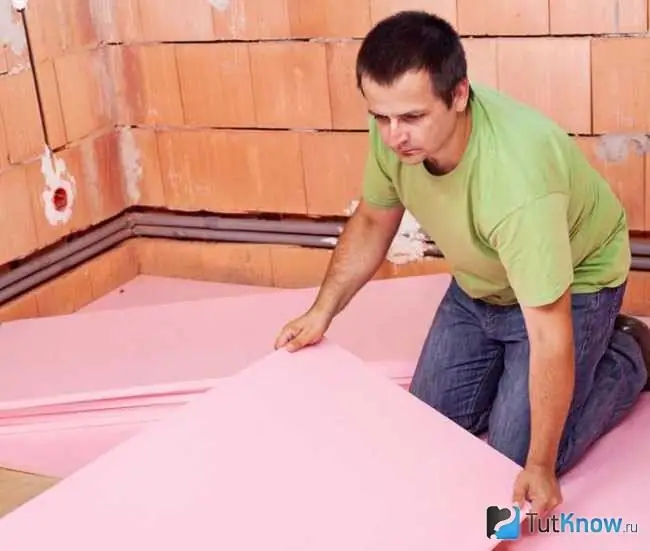
Extruded polystyrene foam is a granular heat insulator made from polystyrene and styrene copolymers with the addition of natural or carbon dioxide. It is made by extrusion from an extruder, hence the name. The result is a high-quality porous substance with a uniform distribution of cells, the dimensions of which do not exceed 0.1-0.2 mm.
The material is marked with XPS and other letter and number designations, each manufacturer has their own. For example, Styrofoam extruded polystyrene foam is marked 1B-AXPS-EN13164-Tl-C5 (10 / y) 250DS (TH) -TR100. In encrypted form, there is information about thickness, density, weight and other important characteristics.
Due to the increased resistance to steam movement, the product is used in such cases:
- For insulation of a concrete floor above a high basement, for which it is mounted to floor slabs from the outside. In high humidity conditions, the coating will serve as additional waterproofing.
- For the protection of concrete floors on top of existing subfloors, followed by screed filling. In this case, the height of the room will decrease by at least 15 cm.
- For thermal insulation of the subgrade. The material is laid directly on the sand and gravel bed, and then poured with concrete.
- To create an insulating layer in warm floors.
- Granular polystyrene foam can be added to the cement slurry. In this case, the screed acquires thermal insulation properties.
Advantages and disadvantages of floor insulation with expanded polystyrene
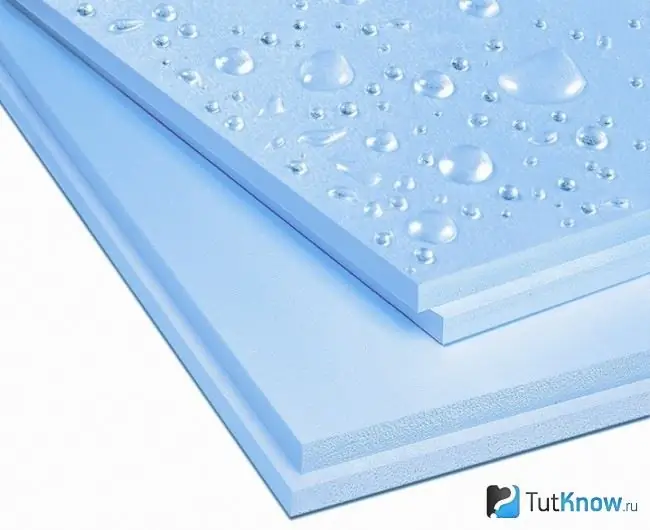
The material has become popular due to its unique qualities that distinguish it from other types of sheet heat insulators:
- Insulation does not absorb ground water. Under the influence of moisture, it does not change its size and does not deform.
- The high density allows the panels to withstand significant loads.
- It goes well with cables and pipes of the "warm floor" system.
- Samples are easy to handle. They can be easily cut into small segments of any geometric shape.
- The insulator has properties that allow the floors to be used for a long time. Microorganisms, bacteria and fungi do not start in the stoves. The product is resistant to biological and chemical influences, does not rot.
- Expanded polystyrene soundproof interfloor ceilings.
- The material is environmentally friendly. It does not irritate the skin during installation work, does not create dust and does not emit an unpleasant odor.
The negative properties include deformation of sheets at a temperature of + 80 + 90 degrees and the ability to ignite. Therefore, it is not used in fire hazardous areas. The product costs significantly more than other samples.
Technology of floor insulation with extruded polystyrene foam
Insulation of the floor with expanded polystyrene is carried out in two stages. First, there is a process of preparation for the main operations, during which the base is cleaned and leveled. At this stage, consumables are purchased - glue and other components of the insulating layer. Next, the heat insulator is laid in accordance with the selected installation technology, which depends on the type of flooring, the design of the "pie" and the requirements for it. Let's take a closer look at all the stages of installation work.
Features of the choice of expanded polystyrene

Before buying, it is necessary to determine the main characteristics of polystyrene foam for floor insulation in each case. These include the density and thickness of the material.
Features of the choice of expanded polystyrene, depending on its density:
- Products with a density of up to 15 kg / m3 used for thermal insulation of bases without load;
- 15 to 20 kg / m3 - for floors with low load;
- 25 to 35 kg / m3 - for self-leveling structures that can withstand heavy weight;
- 36 to 50 kg / m3 - are used to insulate especially loaded decks.
It is recommended to calculate the thickness of expanded polystyrene foam for floor insulation according to SNiPs or, simplified, according to our recommendations:
- The thickness of the insulation for laying above the basement or on the ground: at least 10 cm - for the southern regions, at least 15 cm - for the northern ones.
- For thermal insulation of floors in pile houses, the sheets must be: for the southern regions - at least 10 cm, for the regions of the middle lane - at least 15 cm, for the north - at least 20 cm.
Only high-quality insulation is capable of reliably insulating the warp. At home, it is difficult to check its characteristics, but a fake can be determined by indirect signs:
- Examine the end of the sheet carefully. A quality product has a uniform structure, without seals. The cells are small and difficult to distinguish. If they can be distinguished with the naked eye, then this is a sign of poor quality workmanship. Large pores neutralize one of the main advantages of the material - the lack of water absorption. When laying on the ground, moisture will seep through them, and when insulating wooden floors, insects will appear in the slabs.
- Break off the fragment and press in this place with your finger. A fake can be identified by the crackle that appears when the thin walls of the cells burst. After laying, cracks appear in such slabs, which leads to their destruction.
- Also, a fake can be detected by smell. The quality material contains harmless chemical elements, and at the break you can feel a faint smell of alcohol or plastic.
- It is recommended to buy the product in branded stores, packed in a protective film. The label must indicate the manufacturer and his data, brand, characteristics, application information, plate dimensions and other information.
Rules for the selection of glue for expanded polystyrene
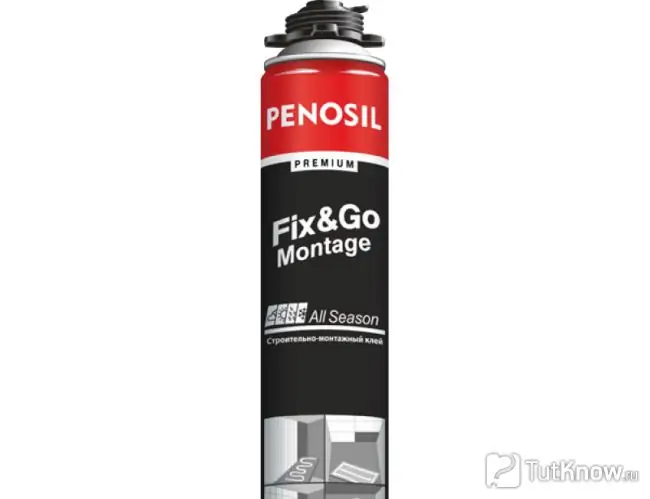
To create an insulating layer, you may need special adhesives such as Kliberit, Knauf, Ceresit on a polyurethane basis. They are sold dry, packaged in 25 kg bags. For cooking, it is enough to dilute them with water in the proportions indicated in the instructions.
Inexperienced users are advised to buy solutions with a long cure time, so that there is time to adjust the position of the sheets.
The insulation can be glued with universal means that do not contain gasoline, kerosene, formalin, acetone or toluene. They destroy polystyrene foam.
The instructions for the product always indicate its consumption per 1 m2, but you need to buy it with a margin on an uneven base.
More recently, Penosil iFix Go Montage foam in cylinders has appeared on the market, designed to fix the product to any surface. It is applied with a mounting gun.
Warming of floors with expanded polystyrene on the ground
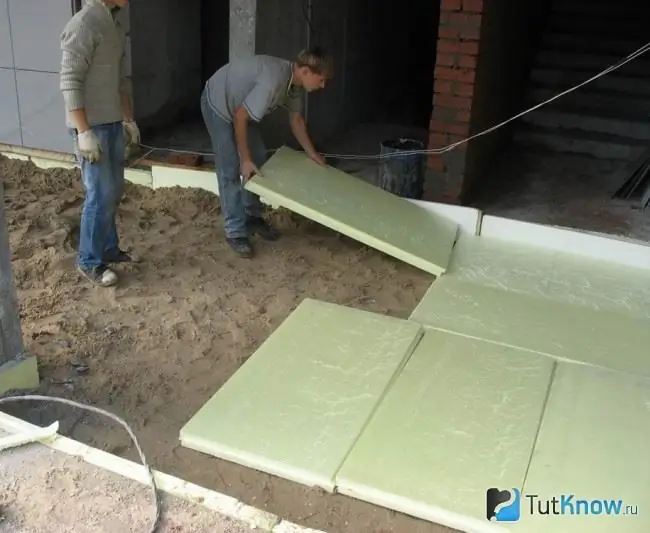
For decks that are erected on a subgrade, thermal insulation with extruded polystyrene foam is essential.
The technology of floor insulation with polystyrene foam on the ground looks like this:
- Level the area under the base. If the soil is loose, compact it and let it sit for a month. During this time, the soil will shrink.
- Fill in a layer of coarse gravel 10 cm thick and tamp. On top, make a layer of sand of the same thickness and also compact.
- Put a waterproofing film on the pillow, make the joints with an overlap of 10 cm, and then glue it with mounting tape.
- Lay the insulation sheets in a checkerboard pattern. The elements must fit snugly together. Fill the slots with the rest of the material.
- Cover the panels with a layer of vapor barrier with a slight overlap on the walls. Thus, they will be maximally protected from moisture from below and from above.
- Place a metal mesh over the membrane.
- Pour the base with concrete or cement mortar more than 60 mm thick and level it horizontally. The surface must meet the requirements of the flooring.
Warming of floors on the ground in the presence of lags is found in private houses that have already been in operation for a long time. In this case, the use of extruded insulation is justified if high-quality vapor barrier of the base is required.
The work is carried out as follows:
- Remove the planks of the old floor.
- Compact the soil.
- Spread a layer of expanded clay or sand and gravel cushion on it and also compact.
- Place a waterproofing sheet on the pillow. The joints should be made with an overlap of 10-15 cm. After laying, glue them with assembly tape. It is only necessary to waterproof the gaps between the lags, with the entrance to them.
- Fill the cells with a sheet of insulation, cutting them exactly in place. Zap the remaining gaps.
- Nail the finishing boards to the logs from above.
To quickly cut extruded polystyrene foam, you will need the following tools:
- Sharp clerical or wallpaper knife. It is in every home.
- An electric jigsaw will quickly cut any sheet thickness, but the edges of the cut are uneven.
- A heated kitchen knife will cut the material without crumbling.
- Nichrome wire, heated to reddening, will cut a workpiece of any shape.
Floor insulation with expanded polystyrene on a concrete base
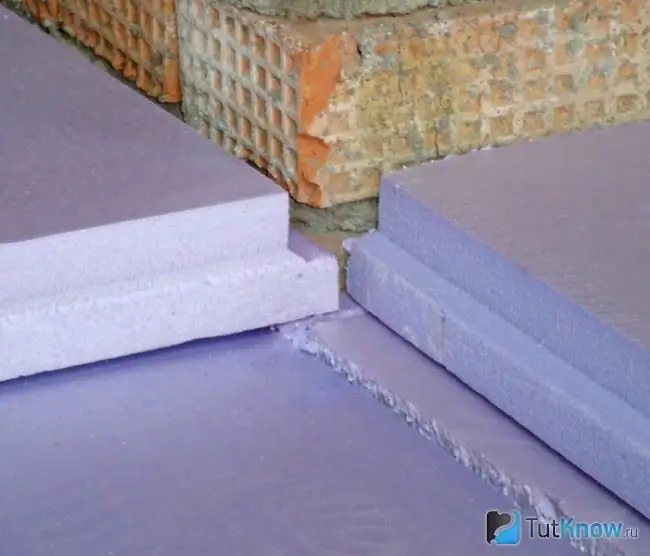
Extruded polystyrene sheets can be attached to the concrete base from the outside (eg from the cellar). This option has its advantages, since allows you to keep warm not only of the floor slabs, but also of the walls in contact with it. Also, the ceiling height in the room does not decrease.
The work on insulation of the floor from the basement side is carried out as follows:
- Clean the concrete slab and rinse with water.
- If cracks, grooves or other defects are present, seal them up with cement mortar or expanded polystyrene glue. Knock down the ledges.
- Prime the floor.
- Apply a 12 cm layer of glue to the sheet and smooth with a notched trowel. Place the board to the surface and press down for a snug fit.
- Join the following panels without gaps. If any gaps do appear, fill them with pieces of glue-on material. Do not use polyurethane foam to seal the gaps due to its complete waterproofness.
- Insulate the basement walls at a distance of 60 cm from the floor slab down with the same material. In this way, heat leaks through the flooring and partitions into the ground are eliminated.
- Cover the insulation with fiberglass construction mesh and glue with plaster. For reliability, fix it with dowels with wide heads with a plastic core. Place the fasteners every 40 cm.
Insulation on concrete from the inside of the room is used to protect floors in high-rise buildings with expanded polystyrene plates, including above basements.
The work is performed in the following sequence:
- Prepare the base in the same way as in the previous case.
- Using a hydrostatic level, check the deviation of the slab surface from the horizon. If the difference is more than 0.5 cm at the maximum length of the room, level it with a self-leveling mixture.
- After the mortar has solidified, fill in a finishing layer 3-5 cm thick, which will eliminate minor irregularities. Further work on floor insulation with extruded polystyrene foam can be carried out only after the surface has completely dried.
- Glue a damper tape to the walls around the perimeter of the room, above the screed, which should compensate for thermal expansion.
- To prevent moisture from getting on the screed, cover it tightly with plastic wrap with an exit to the wall. You can also use a waterproofing membrane. On the middle floors, the film can be omitted. If the floor is not floating, the sheets of insulation are placed on the polyurethane glue directly on the concrete.
- Lay the slabs on the foil close to the wall. Lay the sheets in a checkerboard pattern, no gaps between them are allowed. If necessary, seal the gaps with the rest of the material.
- Cover the products with vapor barrier foil overlapping the wall and adjacent pieces. Seal membrane joints.
- Lay the reinforcing mesh on top and coat with a thin layer of screed to secure.
- Fill the "cake" with a screed 3-5 cm thick.
- Once it has cured, the floor covering can be laid.
In the case of thermal insulation of attic and attic floors, the construction of the "pie" is somewhat different from that used on the middle floors. On the floor, not a waterproofing film, but a vapor-permeable film is placed. This is due to the fact that the attic flooring serves as the ceiling of the upper floor, which must "breathe".
Put insulation on it and cover with the same vapor barrier. Sheets can be stacked in several layers with offset vertical joints. They can be glued with special solutions. Then you can fill in the screed or assemble the crate and nail the boards of the finished floor.
Thermal insulation of the floor with expanded polystyrene with lags
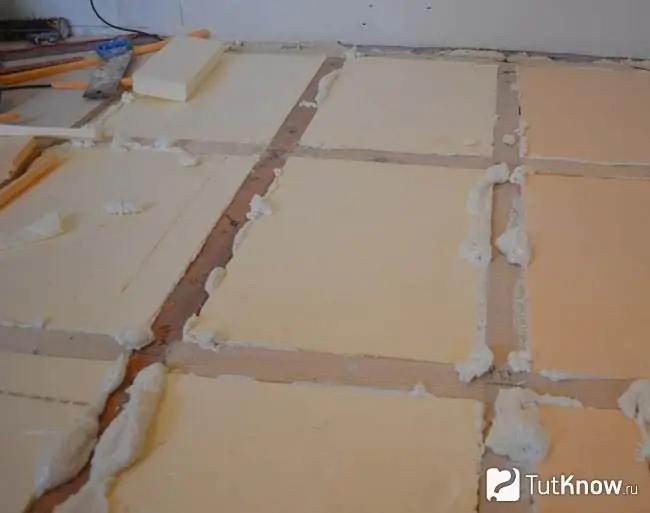
Thermal insulation of floors of a similar structure is performed in the following sequence:
- Clean and level the concrete base as previously described.
- Lay the waterproofing film on the floor, going up the walls. Lay its fragments on top of each other with an overlap of 10 cm. Glue the joints with assembly tape.
- Install the lags. The width of the cells should correspond to the size of the insulation sheet. Choose the height of the slats so that it is greater than the thickness of the insulation. Fix the lags to the base with hammer-in dowels.
- Place expanded polystyrene plates in the cells.
- Place a vapor barrier on top of the beams.
- Next, fix the finishing floor from boards or OSB boards. Leave a small gap between them for thermal expansion.
To protect concrete floors with extruded crumbs, you will need expanded polystyrene granules, which can be found in hardware stores. The solution is prepared in the following sequence: pour a little water into a concrete mixer and add dry cement, mix the mixture until a homogeneous consistency, add granules in a ratio of 1: 3, 1: 4 or with other values. The larger the insulator, the better the heat will be retained, but the strength of the coating will deteriorate. It can crumble during operation. Fill the overlap with this solution. How to insulate the floor with expanded polystyrene - watch the video:

The method of thermal insulation of the base with this sheet material is so effective and simple that it is deservedly considered the best of all possible options. The main thing when insulating the floor with polystyrene foam with your own hands is to follow the work technology exactly, since negligence can easily negate what has been done.