General information about the device of the greenhouse stove, options for its execution. The simplest designs of the heating unit, instructions for self-production. Safety precautions and basic recommendations. A greenhouse oven is a device that allows you to maintain a given temperature for a required period of time. Greenhouse heating can be carried out using both factory equipment and home-made devices.
Basic information about greenhouse oven
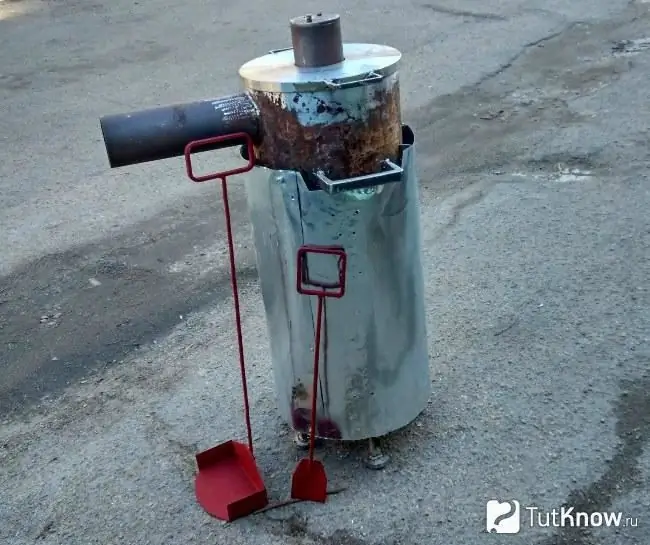
Growing plants in greenhouse conditions provides an opportunity to obtain an early, high and sufficiently high-quality harvest. Artificial heating helps to increase the efficiency of using appropriate structures, which not only improves the thermal characteristics of the building, but also allows you to grow crops throughout the year.
Establishing a normal heating system in a greenhouse is not easy, since the generated heat must be evenly distributed throughout the entire free space. Furnace heating of air in a greenhouse is especially relevant due to its economy, ease of adjustment and durability.
The most advantageous is the operation of traditional furnaces, which have many advantages over other heater options. Interestingly, different types of fuel can be used in the operation of the equipment. Modern devices are designed for natural gas, firewood, charcoal and other fuels.
One of the significant disadvantages of the oven is its rapid, sometimes excessive heating, which negatively affects the normal air humidity inside the greenhouse. For this reason, the use of the Buleryan furnace is considered an ideal choice, the outer walls of which practically do not heat up, and the equipment itself is highly reliable and easy to control. Its cost is commensurate with other types of heating units, in addition, it is in no way inferior to them in ease of adjustment and maintenance.
Features of the oven for the greenhouse
It is not difficult to choose a stove for a greenhouse, besides there are a lot of offers on the market. But it is necessary to understand the specifics of the operation of each device, its technical characteristics, capabilities, power, installation rules and a number of other parameters. A competently executed decision will allow you to get a good harvest at any time of the year.
Continuous combustion furnace
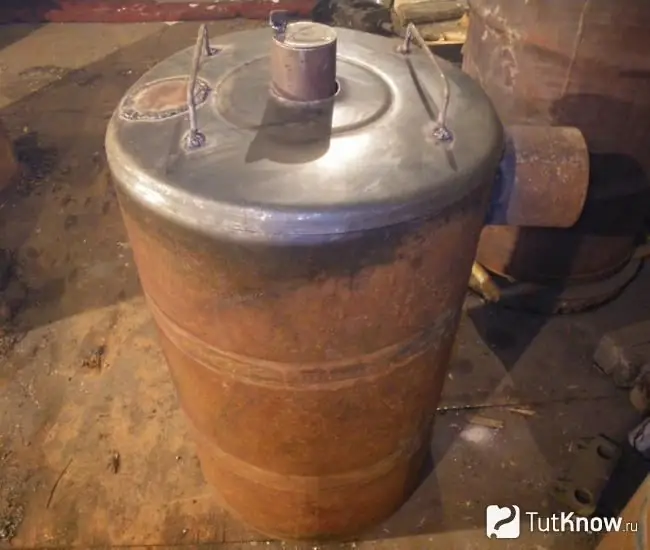
There are several types of long-burning furnaces. Let's take a quick look at each of them.
Buleryan stove
The device is widely used, including for heating greenhouses. Externally, the device looks like a barrel with a two-tier firebox. Curved pipes are made around the perimeter. The power and quality of heating depends on the number of metal pipes. The main elements of the device are: a smoke damper, a loading shaft with a metal door, and a draft control system.
It runs on wood and is relatively safe to use. The oven can function according to the following principles: heat transfer, convection, heat radiation.
The fuel gradually smolders as it enters, while generating gas, which subsequently circulates through the air pipes. Due to this, heat transfer occurs.
Since the oven is operated with an open flame source, basic safety precautions must be followed. It is advisable to place an urn with sand and a fire extinguisher nearby.
Butakov's stove
There are no significant differences in the specifics of work from the Buleryan device. The difference lies in the shape of the unit, which resembles a parallelepiped. Inside the system, nozzles are laid through which warm air passes. The stove has the following main elements: chimney, a series of dampers, an ash pan.
Furnace performance is similar to the previous type. It is not demanding, practical, allows you to easily achieve the desired result and the required air temperature.
Bubafonya stove
This is the simplest and most reliable design that will not be difficult to do on your own, which cannot be said about the devices described earlier. Furnaces for heating greenhouses of this design have an elementary body, often made from a conventional thick-walled cylindrical container or gas cylinder.
In the central part of the body, a loading opening is usually made with a corresponding door, whereby the fuel is loaded. At the bottom of the apparatus there is an ash pan for waste disposal. The release of heat occurs due to the smoldering of materials under the influence of constant pressure due to the mass of the unit itself.
Stove stove
Another name for the device is slobozhanka. It is the most optimal greenhouse heater and consists of the following elements: a combustion chamber for materials, a convection jacket, ducts for the supply and distribution of air, special components used for specific conditions.
Burning in the oven can be top, center or side. Air supply is provided to the lower or central side part or through the L-shaped branch pipe. The unit is capable of operating on wood and alternative fuels, including coal, pressed sawdust, and more.
A long-term combustion furnace will allow high-quality heating of the greenhouse with minimal human participation in this process. The stove works great on peat briquettes, brown or charcoal.
The specificity of the furnace lies in the gradual smoldering of the charged materials, as a result of which gas is released, which rises above the area where the fuel burns out. This process leads to the generation of significant heat. One batch of fuel can be enough for several hours of operation. The heat released during smoldering is several times greater than during normal combustion.
A special feature of the furnace is a portioned oxygen supply, which is provided by adjusting the corresponding mechanism. After complete combustion of the materials, the furnace branch pipe is closed, due to which air is supplied. This leads to a weakening of the combustion draft.
Advantages of a long-term combustion furnace:
- Relative autonomy of work;
- Significant service life;
- Favorable heat consumption and high performance.
The process of building a long-term combustion furnace for a greenhouse is simple, for which you need metal fittings, corners or a channel, an iron barrel with a volume of 100-200 liters, and a steel pipe.
The barrel is placed horizontally, after which one of its side parts is cut off. Places where the edges are rolled must be leveled. Instead of the bottom, a pipe is installed, which in the future will be a chimney. At the other end of the container, a hole is cut for the air supply, where the channel is additionally welded.
After assembling the furnace, you can proceed to testing it. It should be loaded with 30% solid fuel, and then brought into working condition. From the start of ignition to the use of fuel, at least 5-8 hours must pass. The maximum load will allow it to work up to 3 days.
It is not recommended to use anthracite coal for the operation of the stove. The loading of the unit must be maximized to achieve its best efficiency and performance.
Brick greenhouse stove
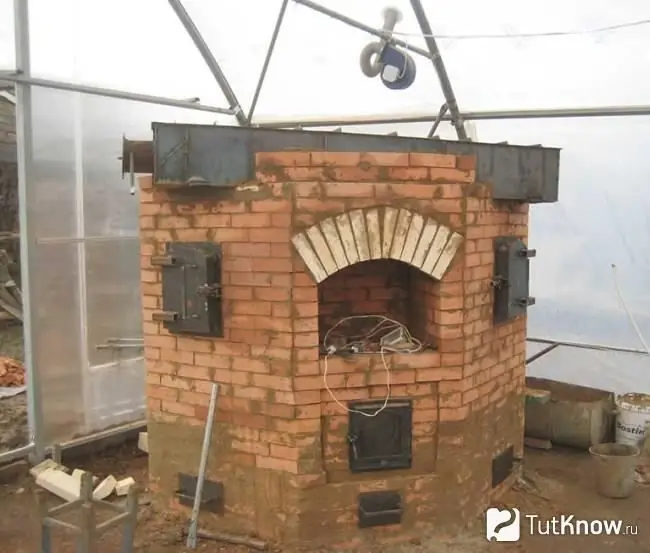
A practical and reliable way to heat a greenhouse is to use a wood-fired brick oven with a hog. Its main advantage is the ability to apply maximum lift and sufficient traction.
To build a furnace you will need:
- Metal pipes;
- Iron floors, which can be taken from the corresponding used unit;
- Up to 500 pieces of fireclay or ordinary building bricks.
Initially, preparatory work is being carried out to organize the foundation. Preference is given to monolithic structures made on the basis of cement mortar.
During the construction of the furnace, it is necessary to provide two steel pipes in its upper base, through which the oxygen supply will be carried out. Additionally, a water tank is installed, which serves to humidify the air. The furnace is lined with bricks over the entire surface, using cement or clay as a binder.
During the operation of the oven, it may be necessary to service the ventilation ducts, for which it is necessary to provide an inspection hole.
Heating unit made of iron barrels
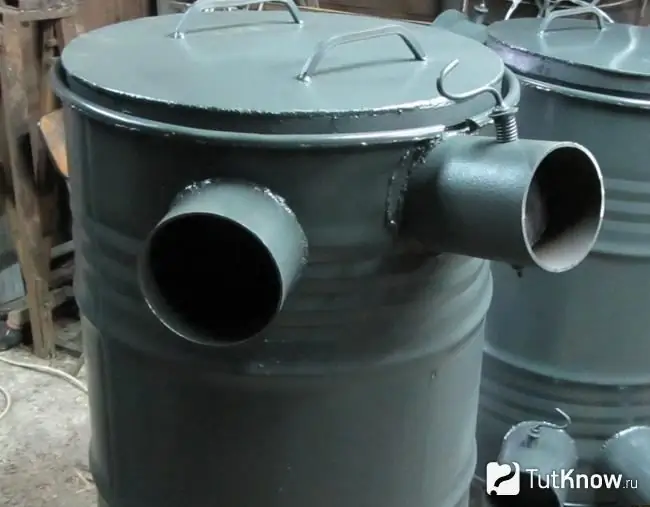
The main components of the furnace are metal containers with a volume of up to 150-200 liters, steel pipes, metal strips and fittings. It is allowed to make a similar structure from one barrel, which will require more welding work.
The unit has a simple design with a cover. It is divided in the center by a steel partition. In the lower part, supports are welded for installing the furnace, and a door is installed, which serves for loading fuel and unloading ash. A chimney is attached to the upper element.
The sequence of steps for assembling the oven is as follows:
- The flange of the barrel is cut off, after which a chimney is installed on the seat.
- A hole with a diameter of 100-120 mm is opened from below.
- The second barrel is cut across so that one of the parts is at least 250 mm in height.
- Places for loading fuel and installing a locking device are marked.
- Furnace supports are made using fittings and other metal waste.
- The firebox, chimney and the main part of the stove are welded together.
- The cover is made from the remnants of the material.
- After the installation of the furnace, it is checked for operability.
To load the oven with sawdust, you will need to have a special device. It is made in a conical shape with a socket diameter of 150 mm. The device is bookmarked before refueling the furnace. It is not recommended to load the unit by more than a third of the total volume. At the end of the relevant work, the cone is removed, after which the fuel is ignited with the closure of the furnace lid. Usually, one such operation is sufficient to ensure the operation of the unit for 48 hours, without operator intervention.
As a fire safety element, an additional gate filled with ordinary sand can be used. As necessary, including for stopping the furnace, material is added.
The quality of welds should be controlled at every stage of work, which will allow you to get a safe, reliable and durable product.
Oil oven
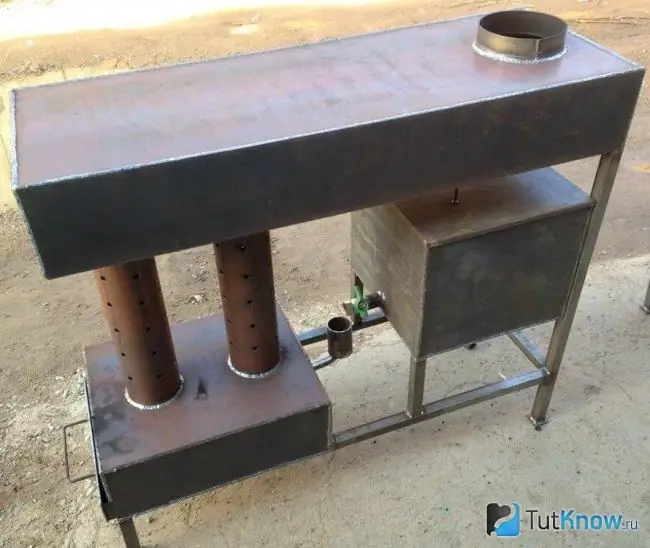
Oil ovens are widely used not only for heating greenhouses, but also for heating water and preparing food.
Before making a furnace for a greenhouse, you need to pay attention to a design that allows you to work on waste engine oil. It is especially relevant in the presence of direct supplies of such fuel, the price of which is insignificant.
The main elements of the oven are:
- Smoke evacuation system;
- Filling hole for oil;
- Regulating dampers, whereby it will be possible to set the required combustion mode of materials;
- Fuel tanks for storage and oil supply.
The chimney is often positioned vertically and is a regular steel pipe.
The device is controlled by filling in the required amount of oil, with the required flow and opening of the damper. The greatest efficiency from the use of an oil furnace is achieved when a water heating circuit is connected to it.
The principle of operation of the device is quite simple, for which it is performed:
- Loading up to 3 liters of oil;
- Setting the wick on fire with its subsequent installation in the corresponding hole of the furnace;
- Partial closing of the damper with a hole of 10-20 mm;
- Adjustment of the intensity of combustion of the flame;
- Exit to the operating mode for 4-6 minutes.
Construction of a traditional oven
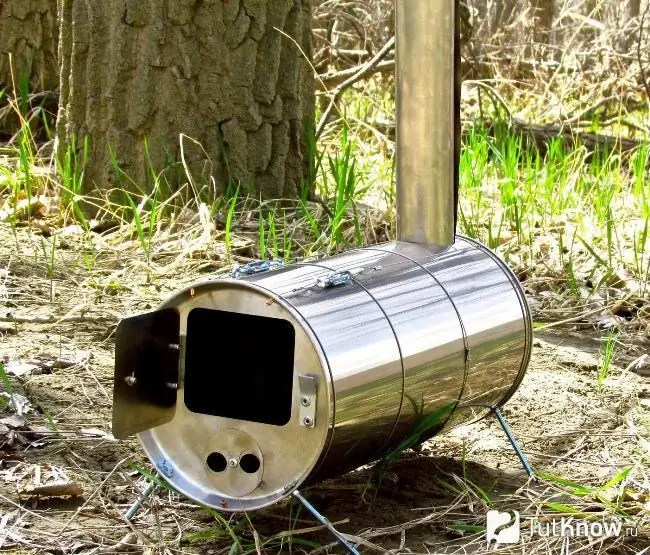
A simple, convenient and reliable option for a greenhouse furnace is its construction using traditional technology. A feature of the design is its simplicity in work. The fuel can be wood waste, chips, sawdust. Loading of material is carried out on a third of the furnace volume.
The classic design includes:
- Loading compartment;
- Bottom;
- Chimney;
- Blown;
- Locking device;
- Fuel line.
It is necessary not only to understand how to install an oven in a greenhouse, but also how to make it. To this end, you will need to select the following materials: a pipe with a diameter of 40 cm, from which the fuel tank is made, a tin sheet up to 5 mm thick for a grate and other elements, a pipe with a diameter of 10 cm for a chimney.
To make a fuel tank in a pipe, you will need to make a hole with a diameter identical to the chimney pipe. Then, through the use of a grinder, the bottom is made. At this stage, it is important to correctly mark and measure the furnace firebox. Several longitudinal cuts are made in the pipe itself, the size of which should be up to 10 mm. The maximum number of sections must be at least 50. Then this element is welded to the bottom of the furnace.
The grate and the furnace cover are made of sheet material, taking into account its tight fit on the pipe. A hole is made in the center through which air is supplied. The connection of the branch pipe to the chimney is carried out with a clamp followed by welding. At the final stage, it will be necessary to ensure the sealing of the formed seam.
The finished unit is installed on a support platform, most often made of steel profiles. Due to its strong heating during operation, it is not recommended to place the stove near combustible objects and plants.
How to make an oven for a greenhouse - watch the video:
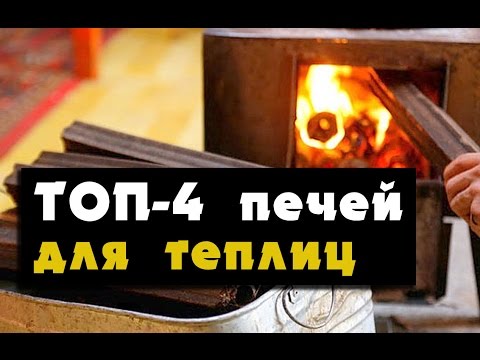
Currently, the range of greenhouse heating units is incredibly large. Each equipment runs on a specific type of fuel. Given the simplicity of some designs, the oven is not difficult to make with your own hands.