Features of welding of polypropylene pipes, devices for installing a water supply system. The volume and sequence of work during soldering, the reasons for the appearance of leaks in the line. Soldering price for polypropylene pipes.
Soldering polypropylene pipes is a connection of water supply elements heated to the softening temperature of the material. After solidification of the material, a monolithic unit is formed, which retains all the properties of the plastic. We will talk about the technological methods of welding products made of polypropylene used in the construction of a water supply system in our article.
Soldering methods for polypropylene pipes
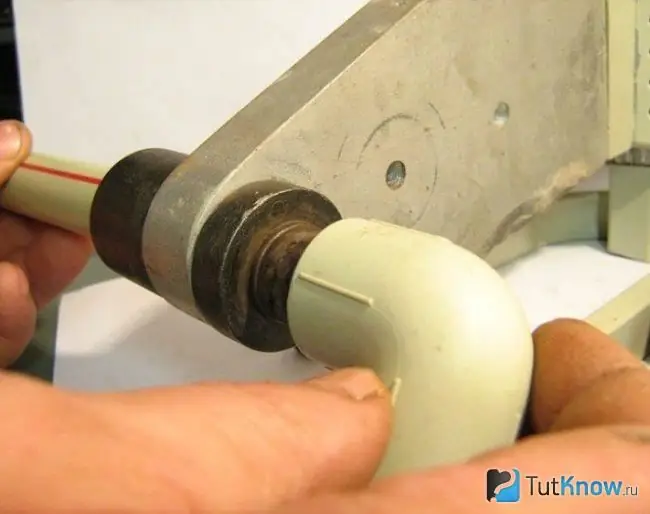
Installation of a water supply system consists in the serial connection of previously prepared elements to create a water supply line from the source to the point of consumption. Polypropylene blanks are attached to each other by welding. This method is based on the property of plastic to soften when heated and diffusion occurs between the elements to be joined. After solidification, a monolithic structure is formed, which retains all the properties of the original material.
Polypropylene pipes for water supply can be soldered in various ways:
- Butt welding method … A rarely used method of joining workpieces with a diameter of up to 50 mm with a wall thickness of more than 4 mm.
- Socket welding … Designed for products with a diameter of up to 50 mm. The work is carried out using a special technology using a soldering iron and some other devices.
- Saddle welding … First, a socket seat is soldered to the product at a 90 degree angle. Then a piece of pipe is welded to it, resulting in a T-shaped adapter.
Socket welding is most often used at home. The method involves the use of a special element that connects two pieces of pipe. Fittings of various types, couplings and connecting sections of taps, mixers and other elements can serve as such parts. After heating the coupling and pipe to a certain temperature, it is necessary to dock them and leave them under pressure for a while to allow diffusion, cooling and polymerization processes to take place.
The quality of the joint is influenced by several factors: the heating temperature of the elements, the state of the abutting surfaces, the diameter of the products, etc. Practice shows that the heating temperature and the diameter of polypropylene pipes are in direct proportion. To facilitate the work, tables have been developed in which the master can find information on the temperature conditions of soldering for each specific case.
Tools and equipment for preparation and welding of polypropylene pipes
It is impossible to weld pipes to each other well without special tools. To perform the work, you will need devices, the brief characteristics of which are given below.
Soldering irons for connecting polypropylene pipes
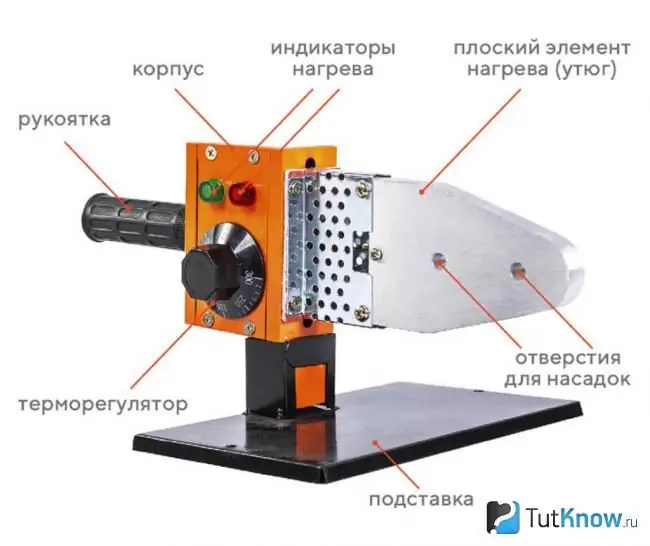
Soldering iron diagram for connecting polypropylene pipes
The welding machine for polypropylene pipes is designed to heat pipes and fittings to a plastic state. It consists of a housing with a handle, a thermostat and a heating element in a casing. The set of the device also includes nozzles of various diameters for pipes and fittings.
After plugging into the network, the device heats up to the set temperature, which is controlled thermostat … It does not allow the soldering iron to heat up more than necessary. Without this element, the soldering iron will quickly burn out or melt the plastic more than necessary.
Cheap appliances are equipped with unstable thermostats, which either overheat the stoves or underheat. Quality devices are equipped with a temperature regulator with a scale.
Important for welding are nozzleswith which fittings and pipes are heated. To prevent plastic from sticking to them, they are covered with a non-stick coating. High-quality nozzles are covered with a thick protective layer that does not burn out and retains its properties throughout the entire life of the device.
When installing a domestic water supply system, nozzles of 16, 24, 30 and 32 mm are most often used. To warm them up, you need a 680 W soldering iron. More precisely, the power is determined by a simple formula: multiply the pipe diameter in mm by 10, and you will get the optimal power of the device.
Before buying a soldering iron for polypropylene pipes, pay attention to device weight … It often has to be kept suspended, and pipes and fittings will need to be installed on it. In this case, hands will become numb and there is a risk of burns and damage to the connection.
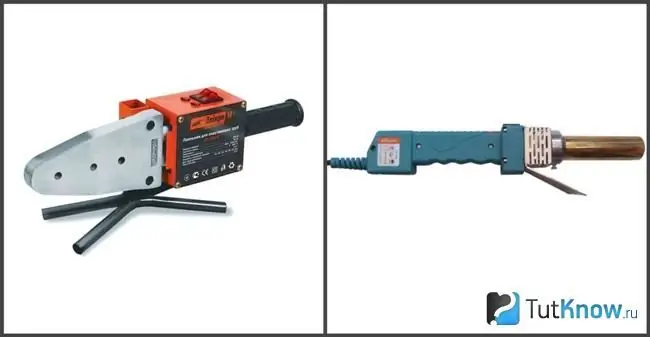
In the photo, the types of soldering irons for polypropylene pipes
There are two types of machines for welding polypropylene pipes, which differ in the shape of the heating element:
- Appliance with flat plate heater … It has holes for installing removable nozzles. Several adapters with different diameters can be fixed to the plate of a flat product, which is convenient when installing a water supply system consisting of sections of different diameters. Flat heaters are available in a wide range of capacities and are designed to work with large diameter pipes - up to 125 mm.
- Soldering iron for cylindrical polypropylene pipes … The attachments are attached to it as clamps. Users choose them due to their compactness, which allows them to connect pipes even in hard-to-reach places. They are lightweight and can weld pipes up to 63 mm in diameter.
Pipe cutters for polypropylene pipes
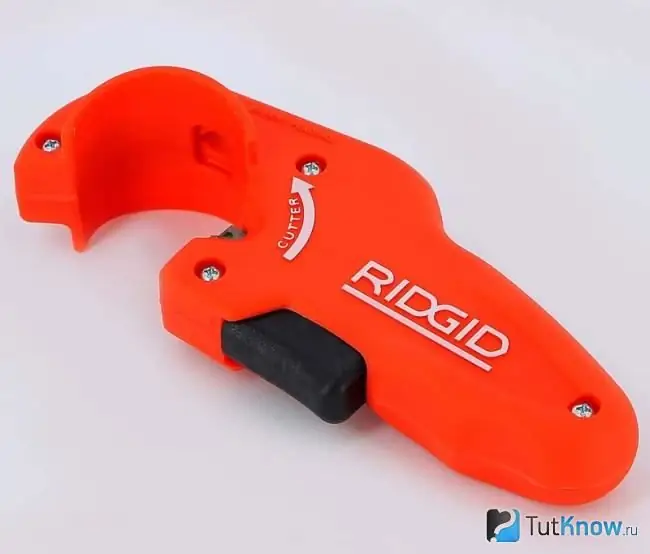
Pipe cutters are used to cut workpieces into pieces. These are not universal tools, only a certain type of cutter is suitable for each material. For the installation of polypropylene pipes with plastic products, choose roller or cutter type fixtures.
When buying pipe cutters, pay attention to the following points:
- The blades must be made of alloy steel.
- The range of sizes of the device corresponds to the diameter of the pipes for your plumbing.
- Choose a tool with an aluminum body, as it is lighter than a steel body, but withstands the pressure generated when cutting plastic.
- The pipe cutters are equipped with replaceable or non-replaceable cutters. The latter are cheaper. Over time, the blade wears out and must be replaced, but if you do not plan to constantly solder, the non-separable device is enough for you.
Pipe cutters are selected according to the following characteristics:
- Manual or electric. Hand-held PP pipe machines are muscle-powered and used for small jobs. After them, the cutting site often has to be finalized in order to eliminate defects. However, such a tool is inexpensive and suitable for one-time work. Electrical devices are powered by mains power or replaceable batteries. They have a number of advantages over manual counterparts: the edges are smooth, there are no mechanical forces during work, the work is done quickly. But not everyone can buy them because of the high price, and the size does not allow them to be used in an inconvenient place.
- Cutting method. The pipe cutters are reminiscent of a steel clip in which the pipe cutting discs are fixed. The device can cut workpieces with a diameter of up to 10 cm. The ends are flat and smooth and do not require rework. Hand-held pipe cutters are composed of guide rollers and cutting rollers. The diameter of the workpiece that can be cut depends on the number of cutting elements. The maximum pipe diameter for the roller pipe cutter is 10 cm.
Scissors for polypropylene pipes
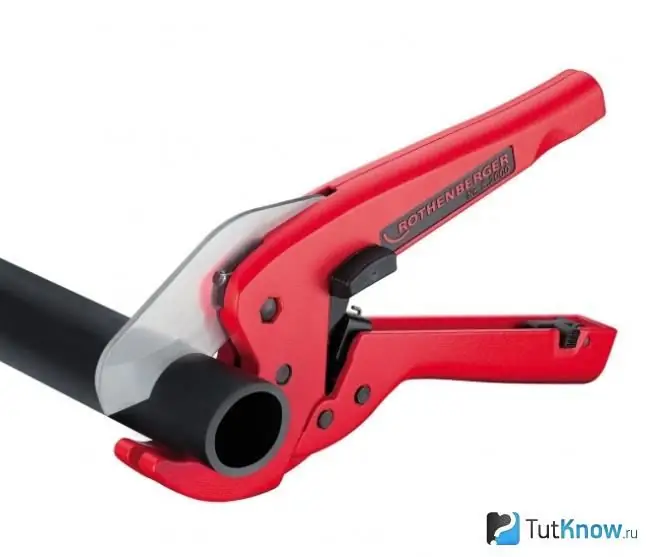
Thin plastic pipes are perfectly cut with special scissors for polypropylene pipes. They are cheaper than pipe cutters and are easier to work with.
Plastic shears are made of two types:
- Guillotine … The pipe is cut while the knife is lowered onto it at an angle of 90 degrees. The soft plastic is literally ripped open with a sharp Teflon-coated blade. The product does not deform due to the smooth movement of the knife, so the end is flat and smooth. The guillotine knife is intended for processing pipes up to 70 mm in diameter. The only drawback of the device is the low speed of work.
- Ratchet … In appearance, they resemble scissors, only they have a blade on one side. On the other hand, there is a semicircular stop on which the pipe is placed. The product is equipped with a ratchet so that the force is applied smoothly. The disadvantages of the device include the danger of getting an oblique cut and crushing of the end during careless work.
Calibrators for preparing polypropylene pipes for brazing
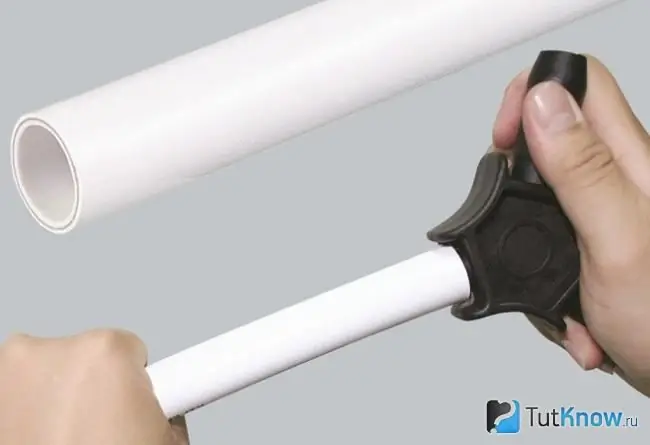
Calibrator is a technological tool for preparing surfaces of pipeline elements for brazing. With its help, workpieces are calibrated, chamfered and shape defects are eliminated. For each diameter of the workpiece, you must use its own device.
Calibrators are on sale for pipes with a diameter of 12, 16, 20, 26 and 33 mm. It is prohibited to use devices that do not correspond to the diameters of the products.
When installing a water supply system, two types of products are used. Plastic ones are designed to eliminate the ovality of the ends. After the procedure, the process of brazing the deformed pipes proceeds without problems. The second type of calibrators is used for fast and high-quality chamfering and deburring. For pipes reinforced with aluminum, there are a variety of calibrators - shaver and trimmer.
Shaver
remove the outer aluminum layer from the blanks before joining the polypropylene pipes. It is made in the form of a clutch with internal blades. To remove the metal foil, insert the pipes into the tool and twist several times. The process stops when the pipe reaches the stop in the fixture. After processing, the surface is smooth, which ensures a high-quality joint of the workpieces.
Trimmer
is designed to form a chamfer on the inner surface of a pipe, reinforced with aluminum foil from the inside. This removes a small area of the metal layer, which can degrade the quality of the joint. The principle of operation and the device of the trimmer are similar to the shaver.
Other devices for cutting polypropylene pipes
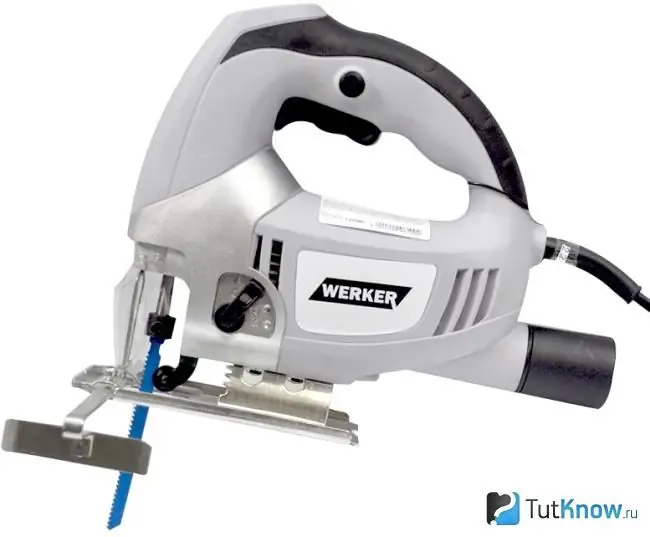
In addition to special devices, polypropylene pipes can be cut with universal tools - a hacksaw, a low-speed electric jigsaw, a drill with a nozzle for working from the inside of the pipe.
However, you can use the tools at hand only in extreme cases for the following reasons:
- The edges of the cuts are torn, with a lot of burrs.
- When using a grinder, the plastic overheats and melts. The same problem occurs when working with a jigsaw turned on at full power.
- With strong pressure, structural changes occur in polypropylene pipes that cannot be noticed. Over time, in these places, the water supply can burst. In addition, after a sharp application of the load, the walls are deformed and the section turns into an oval, which worsens the connection with the fitting. To avoid trouble, insert a round piece of wood that is slightly smaller than the hole in the pipe before cutting into the pipe.
- Do not cut polypropylene with a band saw or circular saw. These units are very powerful, the product can be pulled out of the hands, and cracks and chips will appear in the places of the cut.
- Do not use metal cutters to cut polypropylene. Such tools do not cut the material, but tear, so the end will turn out to be of poor quality. The exception is universal devices, which are designed to work with any material, but they are very expensive.
Brazing technology for polypropylene pipes
The process of welding polypropylene pipes is a series of operations performed in a specific sequence. Below is the technology for assembling a water supply system by the method of coupling soldering using special devices.
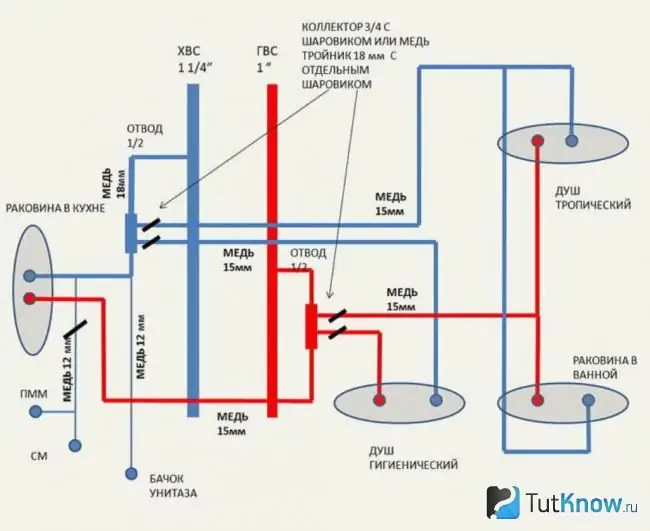
Plumbing diagram in the apartment
Before soldering polypropylene pipes, perform a number of operations to ensure comfortable continuous work during the installation of the structure:
- Make a plumbing plan to determine the number of pipes and connectors and their dimensions. This data will allow you to choose the soldering technology and tool for work.
- Prepare a table or workbench where you can solder the bulk of the pipes. Thus, a large amount of work can be done without an assistant in a place convenient for you.
- Prepare the soldering iron for work. For normal welding, the tool must be heated to a temperature of 255-265 degrees. Products without a thermostat are already set to this temperature. If there is a regulator, set the scale to this value. After the indicator has triggered, check the heating temperature with a special core temperature probe. Fix the device securely on a rigidly fixed standard support. Install pipe adapters and fittings onto the soldering iron.
- Stock up on suede gloves for safe handling of hot workpieces. Think about how the room will be ventilated, because when the plastic is heated, a gas with a pungent odor is released.
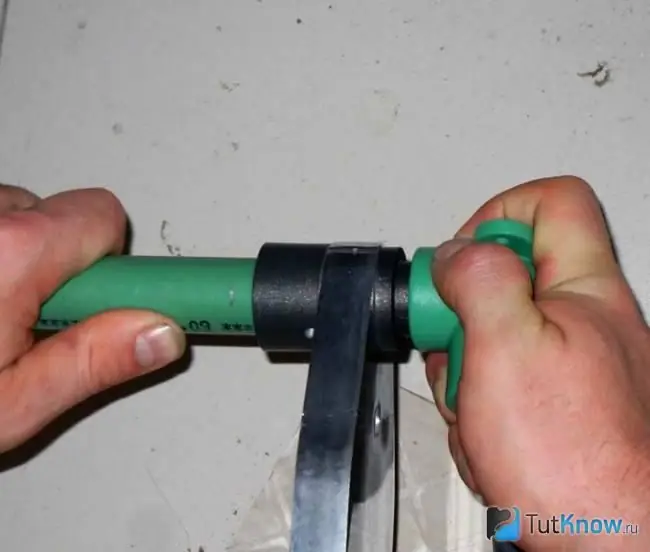
The photo shows how to solder polypropylene pipes
The process of welding polypropylene pipes is performed in the following sequence:
- Determine the exact dimensions of the polypropylene pipes that need to be soldered to each other. The size will be equal to the length of the section on the plumbing plan plus the size of the entry of the product into the fitting.
- Make a cutting ring mark on the surface.
- Cut the workpiece along the mark with special scissors. To do this, spread the handles of the device and install the tube between the blades. Bring the knives to contact the surface and make sure they are positioned exactly on the mark. Apply force to the handles and cut the product. For cutting large-diameter or thick-walled products, it is recommended to use pipe cutters.
- Inspect the ends of the products. The sections of the products should be round, and the thickness should be the same in diameter. Burrs, sagging and roughness are not allowed.
- Use a calibrator to remove burrs from the cut.
- Calibrate the pipes to eliminate ovality. To do this, you need a special calibrator, the diameter of which corresponds to the diameter of the pipe. Insert the connection of the device into the workpiece as far as it will go. Make sure the knives touch the surface of the product. Turn the calibrator and remove the plastic layer from the product.
- Try to dock the pieces. If you managed to put the fitting on the pipe, then one of the elements or both are defective. High-quality workpieces can only be joined after heating. To always be able to remove defective areas, buy pipes and fittings with a margin.
- On polypropylene reinforced pipes, remove the metal layer with a shaver or trimmer.
- Degrease the joints with a product recommended by the pipe manufacturer, usually chloroethylene, trichloroethane, ethyl alcohol or isopril alcohol.
- On the pipe, measure the distance it will fit into the fitting, add 1 mm and mark with a ring mark. Perform measurements with any measuring tool. When determining the distance "by eye", you can make a mistake, which will then affect the quality of the joint. A ring-shaped mark will allow you to control the absence of distortions of the elements during soldering.
- If a corner is being mounted, mark its orientation on the surface.
- Turn on the soldering iron and wait until the heating indicator to the desired temperature comes on.
- The time is given for an air temperature of +20 degrees. In a cold room, increase the heating by 2-3 seconds. At temperatures below +5 degrees, prolong the heating by 50%.
- Install the pipe and fitting on the soldering iron adapters at the same time. The pipe should go up to the mark, the coupling - all the way.
- After the heating time has elapsed, quickly remove the parts from the soldering iron and connect them, checking the correct position and alignment. Carry out the docking very quickly, until the plastic has frozen. The elements can be rotated within 1-2 seconds.
- Hold the elements still until they solidify, usually 25-30 seconds. More precisely, the retention time can be determined from the table. Forced cooling of the joint is prohibited.
- Check the weld quality at the first joint. If everything is done correctly, a bead is formed inside, protruding above the surface by 1 mm. If the plastic covers the hole, reduce the depth of the winding part of the pipe by 1-2 mm.
- After finishing work, clean the soldering iron and all its elements from plastic residues.
The joint acquires maximum strength only after some time, during which the pipe should not be loaded. One day after assembling the water supply, pressurize the system and check for leaks at all joints.
Table for determining the heating time of the elements:
Index | Diameter, mm | ||||||
16 | 20 | 25 | 32 | 40 | 50 | 65 | |
Length of the abutting area, mm | 13 | 14 | 16 | 16 | 20 | 23 | 26 |
Heating time, sec. | 5 | 5 | 7 | 8 | 12 | 12 | 24 |
Time for connecting elements after heating, sec. | 4 | 4 | 4 | 6 | 6 | 6 | 8 |
Initial retention time, sec. | 6 | 6 | 10 | 10 | 20 | 20 | 30 |
Full hardening time, min. | 2 | 2 | 2 | 4 | 4 | 4 | 6 |
Typical mistakes when welding polypropylene pipes
At the last stage of the installation work, the reliability of the joints is monitored. When leaks are found, the first step is to determine the cause of their occurrence.
Typical mistakes when connecting polypropylene pipes, leading to re-installation of the system:
The cause of the defect | Signs | Effects |
Rejection of blanks | Cracks, sagging, uneven wall thickness on pipes | Leakage in the joints due to the presence of defects in the areas to be joined |
Deviation from welding technology | Overheating or underheating of plastic, incorrectly selected compression forces | Leakage in places where diffusion has not occurred, decrease in the flow area of pipes |
Poor cleaning and degreasing of surfaces | Dirt on the surface | Leakage in areas where diffusion has not occurred |
Changing the position of elements during welding | Correction of the position of pipes and couplings during plastic hardening | Leakage in areas where diffusion has not occurred |
Poor removal of foil from a reinforced pipe | Small fragments of foil remain on the site | Leakage in areas where diffusion has not occurred |
Fastening pipes and couplings from different manufacturers | The dimensions of the connected elements differ by the value of the tolerance | Leakage in areas where diffusion has not occurred |
Note! The consequences of some errors may appear only after the start of the operation of the water supply system.
The price of welding polypropylene pipes
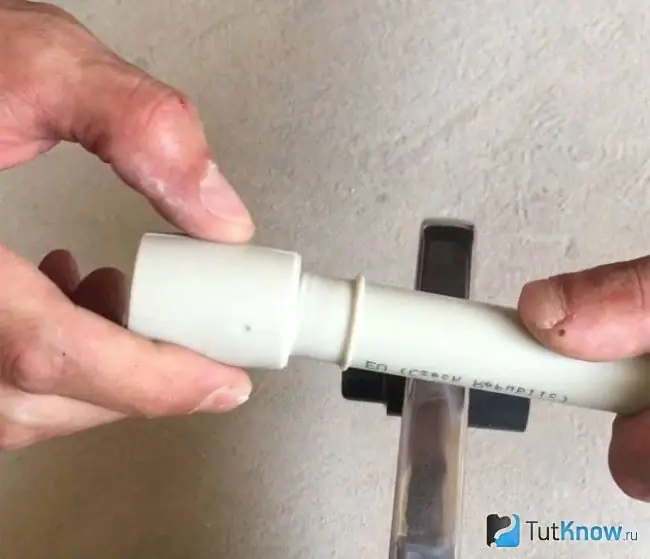
It is impossible to determine in advance the cost of a water supply system made of polyethylene pipes, which is mounted by welding. Each master has the right to set his own prices for the work performed. When evaluating his work, he takes into account the following:
- Distance from the place of residence of the specialist to the customer … If you have to work outside the city, prices will increase significantly.
- Professionalism of the master … Well-known companies value their employees highly.
- Tools for welding polypropylene pipes … High-quality soldering equipment allows you to get a reliable joint. However, it costs a lot of money, so the builder is forced to raise prices.
- Soldering method … Pipes can be fixed in two ways: end-to-end or with fittings. Butt joint is cheaper due to the use of cheaper fixtures. This method is used in low pressure water pipes. In most cases, pipes are brazed using couplings and fittings that require special equipment and work experience.
The price of soldering polypropylene pipes includes all the operations that make up the process of forming a water supply system:
- System project creation;
- Determination of the length of the workpieces, taking into account the dimensions of the fittings;
- Cutting blanks to size;
- Preparing the pipe surface for brazing;
- Soldering of elements;
- Checking the connections for leaks.
Also, the cost of expensive fixtures, such as soldering irons, is often taken into account. Round devices are more expensive than devices with a flat heating surface. But with frequent use, they quickly pay off. The budgetary instruments include domestic products, as well as products from China and Turkey. They are enough for welding pipes in 3-4 houses, but they justify themselves after working on the first object. The highest quality soldering irons are produced in Europe. Their main difference from cheap samples is their ability to provide a given temperature with a small tolerance for a long time. Czech Ditron devices are considered one of the best European soldering irons. From Turkish products, Candan and Kalde soldering irons can be distinguished.
The price of tools for soldering polypropylene pipes in Ukraine:
Tool | Price, UAH. |
Soldering iron | 200-2500 |
Pipe cutter | 52-1900 |
Scissors | 42-1200 |
Calibrator | 50-150 |
The price of tools for soldering polypropylene pipes in Russia:
Tool | price, rub. |
Soldering iron | 380-6480 |
Pipe cutter | 95-4300 |
Scissors | 100-2800 |
Calibrator | 90-420 |
How to solder polypropylene pipes - watch the video:

The technology of soldering polypropylene pipes is quite simple, and you can connect them in this way yourself. Before starting work, it is recommended to try to fix unnecessary pieces by welding, and then cut the joints and check their quality. You can proceed to the installation of the main line if the connection meets the requirements specified in our article.