What are self-leveling floors with quartz sand, what are their pros and cons, features of the choice of materials and the technology of pouring this coating in different ways. Quartz sand flooring is a self-leveling coating that can most often be found in public buildings, shopping centers, garages, and parking lots. Quartz sand is usually the main component and the bonding element is epoxy or polyurethane.
What is self-leveling floors with quartz sand
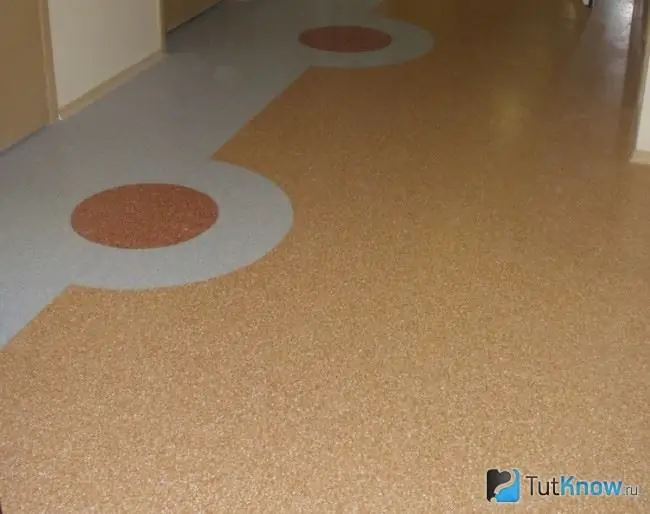
Self-leveling floor coverings are very popular these days. Especially in demand are polymer floors made of various synthetic materials.
They also include various modifiers. The latter are used in order to impart special physical properties to the surface. In addition, they help to create a unique aesthetic appearance for the flooring. Quartz sand is most often used as a modifier (filler), less often marble chips, crushed stone and other materials. The filler can have a different fraction diameter. Particle size largely determines the technical characteristics of the finished flooring.
Quartz sand is different in color. This allows you to create special markings and patterns over a large area. In addition, sand can be used to create polymer floors, not only as a filler, but also as a special material that roughens the surface. This is useful in cases where you need to improve grip. The installation technology of such floors differs only slightly from quartz-filled ones.
Self-leveling floors with quartz sand are installed in the premises of medical institutions, the food industry, in private garages, in warehouses. This coating is rarely used in living rooms. To create a bulk mixture with quartz sand, various resins are used:
- Polyurethane … They have good elasticity and high strength. Floors based on such a resin are usually laid in rooms where there is strong vibration and mechanical stress on the surface. Also, the polyurethane resin is resistant to abrasive detergents.
- Epoxy … They are used to create coatings in rooms where there is a high probability of shock loads. They are resistant to moisture and do not deteriorate under the influence of chemicals. Externally, the epoxy resin coating resembles glass. It should not be installed in rooms where high vibrations are present, since this composition is practically devoid of elasticity. But you can put such a floor on a damp base.
- Methyl methacrylate … These resins are used exclusively in residential areas, as they have low performance compared to other bulk materials. Methyl methacrylate dries quickly, which speeds up repair work.
In most cases, the binder for quartz sand is epoxy or polyurethane resin as the more practical materials.
Advantages and disadvantages of quartz sand floors
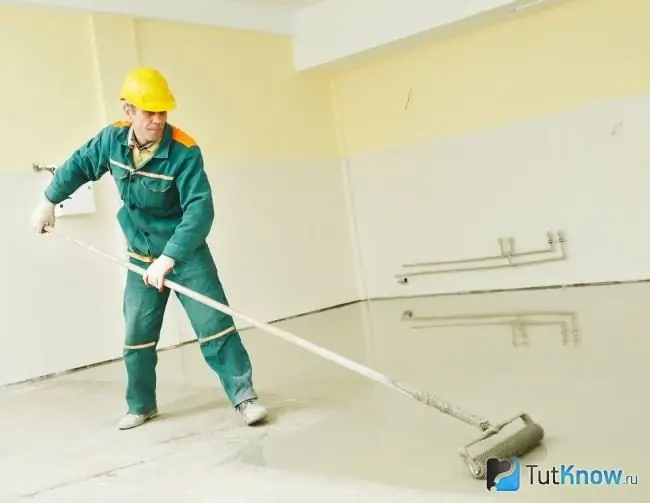
Quartz sand flooring has the following advantages:
- No seams in the floor … This guarantees absolute tightness if an additional top coat is applied.
- Dust free … Epoxy or polyurethane binds even the smallest dust particles so they do not rise into the air.
- High level of wear resistance … Quartz sand itself is a very durable material. In combination with polymers, the wear resistance of the coating increases.
- Resistant to most chemicals … Sand and polymer resins do not react with chemical-based detergents.
- Environmental friendliness … Neither external chemical, mechanical action, nor temperature changes provoke the release of toxic substances by such floors.
- No slip effect … Even the finest quartz sand fraction added to the working polymer mixture will create a rough surface that will prevent slipping and improve adhesion.
- Fire safety … The quartz resin floor does not burn and does not spread fire.
The presence of quartz sand in the bulk mixture significantly reduces its cost, since the consumption of polymer resins is reduced.
If you prepare the base with high quality and carry out the laying work in compliance with all the rules, then a polymer floor with quartz sand can last up to 20 years. The service life depends on the level of permeability in the room with such a coating and the mechanical effect exerted on it. As for the shortcomings, among them one can distinguish a rather meager color palette of such floors, the laboriousness of the installation process and the difficult dismantling of this coating. In most cases, instead of removing, a finishing layer is placed on top of such a floor, since this is much easier and faster than removing polymers.
Features of the choice of quartz sand for self-leveling floor
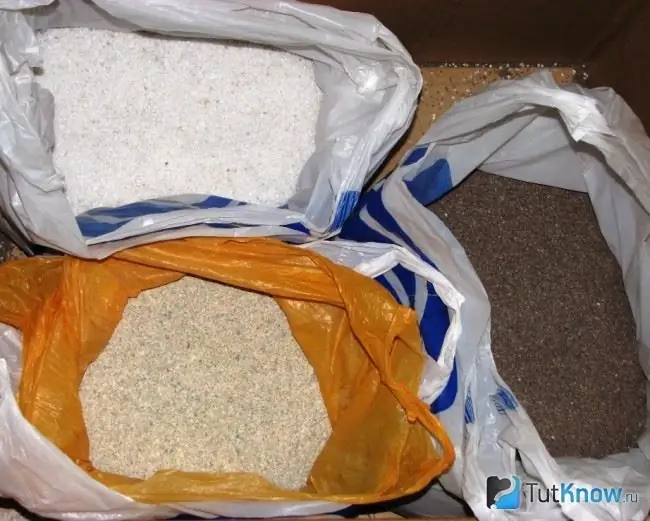
Natural quartz sand is a natural mineral that has a milky hue and is produced in the process of crushing and sifting rocks. Its composition is more homogeneous and does not contain impurities, in contrast to river and sea analogues. The strength of the polymer self-leveling floor will directly depend on the quality of the quartz sand, which acted as a filler. To create a reliable coating, you need to choose a high-quality material that is prepared using a special technology at mining and processing plants for the foundry and glass industry. The absence of impurities in such sand is an important point. It is imperative that the dust fraction is completely eliminated or reduced to minimum values. The permissible moisture level of quartz material for a self-leveling floor is 0.5%. To achieve these values, the sand is dewatered.
When choosing quartz sand for a polymer floor, pay attention to its fraction. Consider the size of the particles when planning to equip this or that type of coverage.
There are 3 main types of quartz-filled self-leveling floors in terms of thickness and composition:
- Thin-layer … Their thickness is up to 1 millimeter. The sand content is low. It is the cheapest way to equip such a floor, given the low consumption of materials. A prerequisite for the installation of thin-layer self-leveling floors is the presence of a perfectly flat, solid base surface, since a thin layer will not be able to hide defects. The used fraction of sand is 0.1-0.2 millimeters and 0.1-0.63 millimeters. This is a fairly small material that makes the coating more uniform and uniform.
- Self-leveling … Their thickness does not exceed 5 millimeters. The sand content is up to 50%. These floors are the most demanded because they have the optimal balance of durability and aesthetic characteristics. The recommended fraction of quartz sand is 0, 5-0, 8 millimeters, 0, 63-1, 2 millimeters.
- Highly filled … Coating thickness - from 5 to 8 millimeters. The quartz sand content reaches 85%. Their structure allows them to withstand large temperature fluctuations, strong mechanical stress. In addition, the thickness of the floor makes it possible to hide defects and problems of the roughing. Sufficiently coarse sand can be used - 0.8-2.0 millimeters.
Quartz sand floor installation technology
Quartz sand can be laid on the floor in two ways. In the first case, it is added to the polymer composition when kneading, and then the surface comes out rough. In the second, sand is poured into an even layer on the bulk mixture and covered with a finishing compound on top, and the surface is smooth. It does not matter which polymer mixture (epoxy or polyurethane) you use. The technology of their installation is practically the same.
Preparatory work before pouring the floor
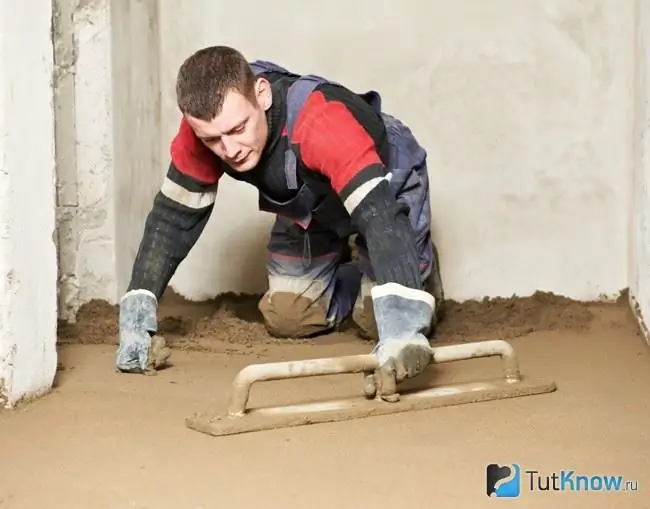
The recommended subcoat for casting epoxy or polyurethane floors with quartz sand is a concrete screed. It can be laid on both ceramic and wooden substrates, but it is more difficult to align and bring to perfect smoothness. To improve adhesion, remove oil stains, mildew and loose pieces from the floor. If there are chips, potholes, bumps on the coating, then they should be putty. If you can, it is best to shot blast the substrate. For this, a special machine is used, which will eliminate all visible defects in the coating and prepare a rough surface for better adhesion to the filling layer. Also, after such processing, it is recommended to carry out grinding. And the dust formed in the process must be removed with a vacuum cleaner. After that, you completely clean the surface, it must be primed with a special impregnation - impregnated. When it is dry, the subfloor is ready for further work. Please note that the temperature in the working room should be at least 5 degrees Celsius, and the humidity should be below 75-80%.
Preparation of a polymer mixture with quartz sand
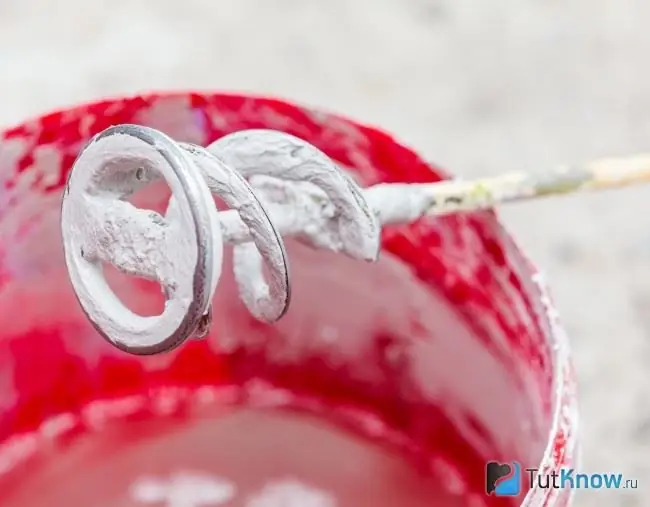
Bulk mixes (polyurethane and epoxy) are sold dry. To prepare them, it is enough to dilute the composition with water in the right proportion according to the instructions. If you plan to make a quartz-filled mixture, then quartz sand must also be added to it. In the process, follow these recommendations:
- Use a construction mixer or a drill with a nozzle for mixing.
- It is desirable that the instruments can rotate in forward and reverse directions.
- You need to stir the mixture twice: after the first mixing, we leave it for a couple of minutes so that the solution adheres a little. Before the second mixing, pour quartz sand into the mass and repeat the procedure.
- Do not prepare too much material in advance. The volumes should be sufficient for a maximum of one hour of work. Then a new portion of the solution is prepared.
The amount of quartz sand for a polymer floor depends on how thick the coating you plan to do and what its purpose is. For medium-thickness, high-strength flooring, use an approximate 1: 1 sand to resin ratio.
Instructions for pouring polymer floor with quartz sand
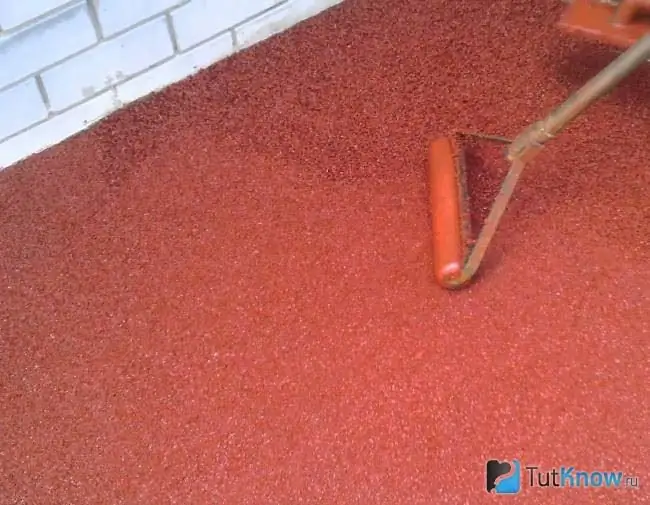
We start laying work only after the subfloor is completely dry. For uniform application of the polymer layer, we need a roller (regular and needle), a spatula, squeegees, as well as paint shoes for easy movement around the room.
We carry out work in the following sequence:
- Apply the mixture in stripes from the far wall from the entrance.
- We use squeegees to distribute the composition as evenly as possible over the surface.
- To make the polymer mixture lie evenly in the corners of the room, we use a spatula.
- We remove air bubbles from the thickness of the coating using a needle roller.
- We compare each new strip in height with the previous one.
Remember that you need to work quickly, since the epoxy and polyurethane mixture thickens very quickly, and it becomes impossible to work with it. It usually takes 24 hours for a self-leveling coating to harden. At this time, the floor should be protected from excessive moisture and direct sunlight. If you want to make a separate layer of quartz sand for a self-leveling floor, then, first of all, you need to fill in a clean polymer mixture. After that, without waiting for it to dry completely (after about 4-5 hours), sprinkle the sand over the surface in an even layer. In this form, we leave the surface to polymerize completely.
Topcoat application
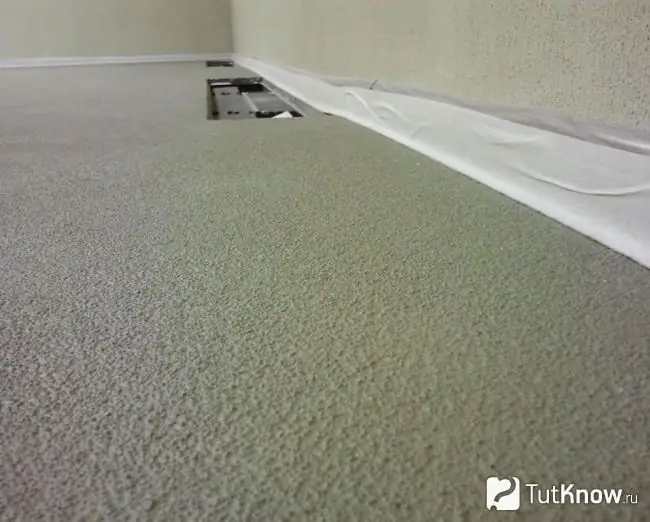
Regardless of whether you did the filling of a layer of quartz sand separately or introduced it into the composition of the bulk mixture, it is imperative to finish the surface with a special varnish. This layer will serve as additional protection for the floor.
The procedure for applying varnish is not much different from pouring the basic composition. This stage is carried out immediately after the polymer layer hardens. For these purposes, you can use a polyurethane topcoat (for all types of polymer coatings). We pour it over the floor surface and stretch it evenly using rollers and spatulas. It will take at least two days to completely dry.
How to make a self-leveling floor with quartz sand - watch the video:

Self-leveling floors with colored sand are in great demand these days due to their excellent performance. Before deciding on such a coating and choosing the right materials, consider the type of room where the floor will be set up and the loads that it will have to withstand.