Expansion joints of the floor, their need, types, cutting technologies and their subsequent sealing. Cutting seams is a technological technique that allows you to prevent the occurrence of cracks in the concrete screed, which are the cause of its gradual destruction. Such a procedure is considered the most important in the construction of cement-based coatings. The period of their safe operation depends on the quality of cutting seams in concrete floors. You will learn about its correct implementation from this material.
The need for expansion joints in a concrete floor
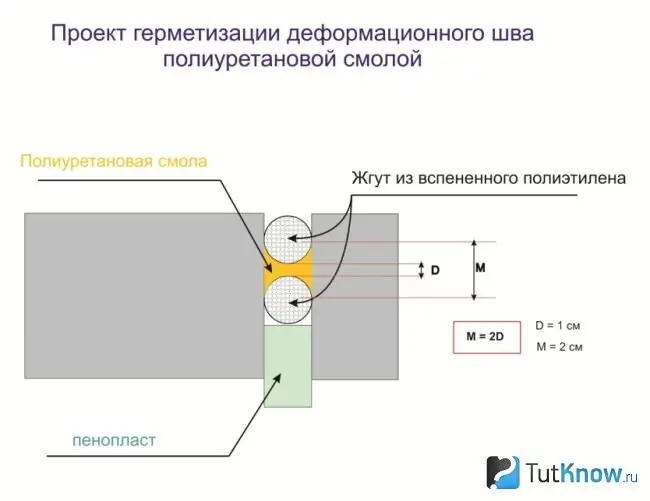
As a result of house shrinkage, temperature fluctuations in the air, insufficient floor thickness to accept industrial loads, cracks appear in the dried concrete screed. They have to be repaired with various mastics, after which the new floor looks as if it has been renovated. In addition, the strength characteristics of the coating deteriorate.
To reduce cracks, concrete surfaces are divided into maps using expansion joints. Maps are squares up to 36 m2… The seams are made immediately after the end of the leveling of the floor with a rail - the rule. The edges of the squares are cut exactly to the thickness of the screed, each adjacent section is adjacent to the previous one.
Due to the fact that there is no reinforcement between them, the cards separated from each other do not crack when the screed dries. During the time of its hydration, spontaneous cracking of the floor occurs strictly along the border of the squares, while the cracks do not move away from the expansion joint.
After their cutting, the obtained longitudinal depressions in the concrete are filled with a plastic sealing compound that protects the "body" of the screed and ensures the mobility of its cards during linear deformations arising from changes in the temperature of the medium.
The main types of expansion joints
There are three types of expansion joints in concrete floors, which limit the appearance of cracks in the screed during shrinkage, temperature changes and polymerization of its material. These are shrinkage, insulation and construction joints. Let's consider them in detail.
Insulation joints in concrete floors
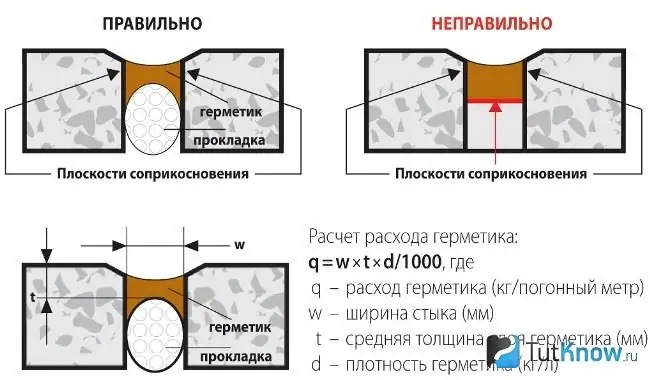
They serve to prevent the transfer of deformations to the screed through the foundation and walls in the places where the floor adjoins the columns, walls and other structures of the house. Insulation joints are made parallel to the walls, and in the presence of columns, around each of them. If the screed has a common border with the foundation, they are arranged along it.
Insulation joints can be round or square. Recesses of the second type must be rotated around the column 45 degrees so that the straight seam is opposite the corner of the column. If this is not done, the screed may crack.
An indispensable property of insulating joints is to provide the screed with the ability to work, that is, to make horizontal and vertical movements in relation to the foundation and walls. For this reason, the insulation that fits into the recess must be compressible and resist elastic deformations without breaking. The thickness of the insulation joint is calculated using the linear expansion value of the cement screed.
The average thickness of the insulating joint is 13 mm. Synthetic fiber or other similar material can be used as a filler. When laying it, it is impossible to make protrusions of the filler above the level of the screed. In addition, the contact of the screed material with the concrete of other building structures must not be allowed, since with such contact the insulating joint will not fulfill its function, which can lead to cracks in the floor. The insulation is laid before the start of concrete work.
Separately, attention should be paid to the technology of the device of joints in concrete floors near the columns. When pouring the screed in these places, the formwork must be installed along the lines of the recess. After the concrete has hardened, it is removed, and instead of it, joint insulation of the required thickness is placed in the cavity. In this case, the remaining space between the column and the seam is filled with mortar and leveled.
Insulation joints are also possible on solid concrete. In this case, the cavities are cut to the thickness of the screed, they are then filled with elastic insulation.
Shrinkage joints in a concrete floor
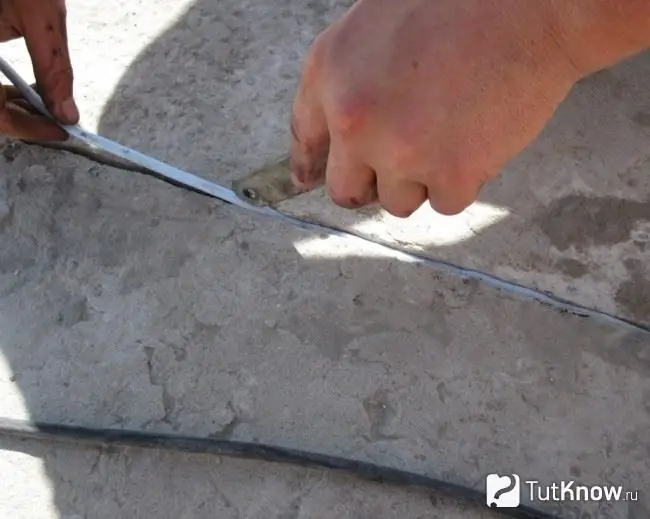
The shrinkage index for concrete is on average 0.32 cm by 0.3 m. Since the polymerization of the screed is uneven, shrinkage is greater in its upper part than in the lower one. Thus, the edges of the tie rise above its center and it "tends" to fold. This process causes internal stresses in it, leading to the formation of cracks. To exclude uncontrolled destruction of the floor, shrinkage expansion joints are designed. They create planes of weakness.
In the process of concrete hardening, shrinkage cavities allow insignificant opening of cracks in strictly designated places. For the manufacture of seams, special forming strips are used, which are inserted into the screed until its material loses its plasticity. Otherwise, they are cut after its finishing.
Shrinkage joints in concrete floors are cut along the column axes. They fit into the corners of the cavities that frame the columns around the perimeter. The seam running along the perimeter should be located from the column at a distance 2-3 times greater than the thickness of the screed. When cutting, you need to strive to make sure that the areas of the floor, bounded by the seams, have a square shape. Surfaces that are elongated along the length of the shape of the cards are unacceptable. It is also recommended to ensure that the shrinkage seam does not have branches and is located in a straight line. On sections of driveways and aisles, they must be positioned along the width of the screed. If the width of the track exceeds 3.6 m, a longitudinal seam must be made in its center. In front of buildings in the courtyard, the shrinkage cavities should be located in relation to each other at distances of no more than three meters, regardless of their direction.
Do not forget the general rule for placing seams: the risk of cracking decreases with a decrease in the floor map. In order to prevent cracking, it is recommended to cut the shrinkage cavities at the outer corners. Sharp corners should be avoided - if they are present, there is a high risk of cracking of the screed. Sometimes, to reliably close cracks in the corners of the floor, it is reinforced at these points with steel rods.
Construction joints in concrete floors
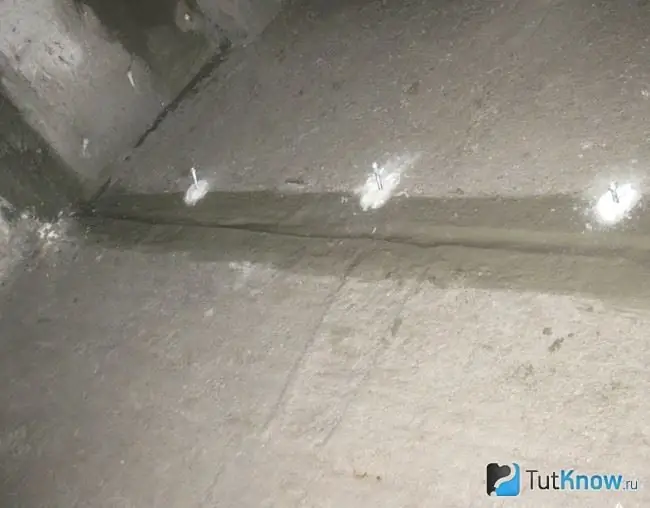
Usually, the device of a concrete screed is performed with technological breaks, which are necessary for a freshly laid mortar to gain a certain strength. In places of contact of the material, which differ in terms of laying, it is recommended to perform construction seams. An exception may be small rooms in which there was continuous work, and the concrete was supplied to the place of laying without interruption.
For the construction of structural cavities, sections of the floor are selected on which the installation of the screed was completed during the day's shift. In this case, a distance of at least 1.5 m from such recesses should be observed in relation to other parallel ones. The shape of the construction joints is a tongue-and-groove connection.
With side projections made of wood, a 30-degree cone is quite enough for a screed with a thickness of 12-20 cm. It is allowed to use metal products that are mounted taking into account the recommendations of their manufacturers. The work of the cones is similar to the process that takes place in the shrinkage joints. However, they provide the ability to move the screed not vertically, but horizontally.
It is not recommended to use metal cones of construction joints for floors with loads in the form of intensive wheel movement. For such cases, "hairpin" cavities are more suitable, which will be discussed below.
If there is a structural joint on a floor area where it is undesirable to perform insulating or shrinkage, it would be a good option to use strips installed across the cavity at? screed depth.
The studded structural joint is widely used on both wheel-loaded floors and areas with pedestrian traffic. The principle of operation of the stud is simple: it keeps the edges of the groove at the same level at the time the wheels pass over it. In order for the seam to work in the horizontal direction, its studs must be installed in the concrete on either side of the cavity or on both sides.
For the seam to work properly, you must follow these rules:
- The studs must be flush.
- They must be parallel relative to each other.
- The seam should run down the middle of the stud.
Seam cutting technology in concrete floor
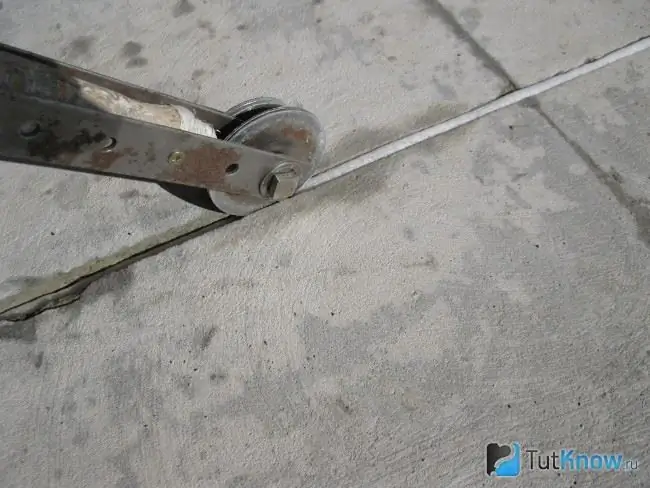
It requires certain knowledge and skills from the performer. First of all, when performing this work, you should maintain the straightness of the seams and cleanliness. The process should start immediately after the concrete has gained the necessary strength, and until the moment when the likelihood of the appearance of arbitrary cracks in the screed is high.
More specifically, the cutter should start work no earlier than a day and no later than three after finishing the screed finish. When using the wet cutting technique, the conditions for it appear 4-12 hours after the completion of the floor treatment. It is permissible to cut cavities after a day, but at the same time you need to wait for the moment when the filler will not fall out of the laid solution, and the cutter blade will cut it together with the concrete.
Before cutting the seams, they need to be marked on the floor surface using a stretched thread and chalk. For the same purpose, a ruler with a width of at least 4 cm is used.
The seams are cut in the same sequence in which the concrete was placed. The depth of the cavity should be one third of the thickness of the screed. Due to this, a section of weakness will appear in it, in which adjustable cracks can appear during concrete shrinkage.
The roughness of the edges of the cracks prevents them from displacing in the vertical direction until the crack widens. In order to comply with the described technology of cutting grooves, the freshly laid concrete mortar must be kept for at least 4 hours.
Not so long ago, the method of light dry construction of joints began to be used, in which their cutting is performed immediately after the completion of the laying of the concrete screed. Without walking on freshly poured concrete, it became possible to make cavities with an extended handle up to 10 m. If a longer seam is required, it is recommended to wear boots that allow movement along the tie and use the 2m saw handle. Dry seams are 2-3 cm deep.
Features of sealing joints in a concrete floor
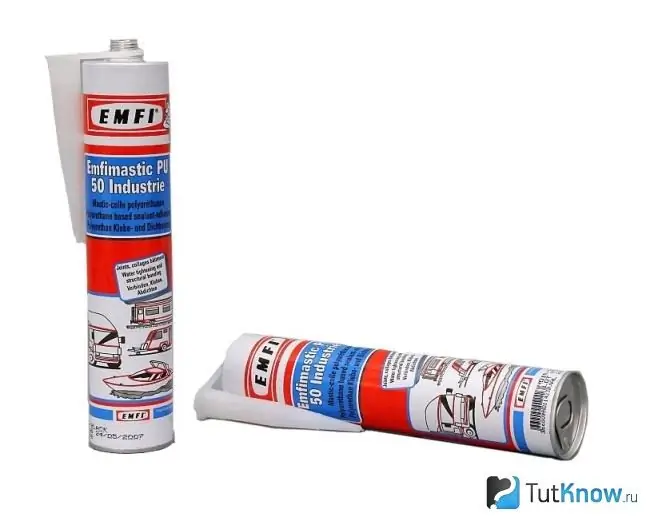
In order to strengthen the edges of the joints that are subject to traffic loads and to make cleaning the floor easier, they should be sealed. Thanks to this procedure, the deformation cavities will be protected from debris, the ingress of various aggressive liquids and water into them. The choice of material for grouting concrete floors depends on the loads and operating conditions.
For example, in a number of buildings, the floor must withstand the loads from the movement of heavy vehicles and be easy to clean. In this case, the selected sealant must have the hardness necessary to prevent chipping of the joint edges, and sufficient elasticity, which will protect the cavity from temperature changes and the effects of concrete shrinkage. Industrial floors, which are characterized by a high degree of traffic loads, must have expansion joints filled with Emfimastica PU-60, which is able to strengthen the cavity so that it can withstand heavy traffic. This sealant must be applied no earlier than 28 days after the screed is laid.
Flexible sealing compound is used for those floors where there is no wheel load on their seams. Such a sealant is applied quickly, it will be sufficiently resistant to screed movements when closing or opening a cavity.
Before grouting concrete floors, they should be cleaned by blowing out with compressed air or with a power brush. When working with the compressor, it is necessary to ensure that it does not contaminate the cavity with an oil film.
How to cut seams in a concrete floor - watch the video:

Expansion joints in floors are a necessity dictated by SNiP rules and associated with the invisible movement of concrete surfaces. In the absence of space for this process in the form of cavities, a slow destruction of the screed may occur.