Sub-floor device, its design, installation technology on logs and dry screed. A subfloor is a structure that serves as the basis for outdoor decoration. The subsequent result of the installation of the topcoat depends on its condition. You will learn how to make a wooden sub-floor so that it is reliable, does not flake or crack, you will learn from our material.
Construction of a rough wood floor
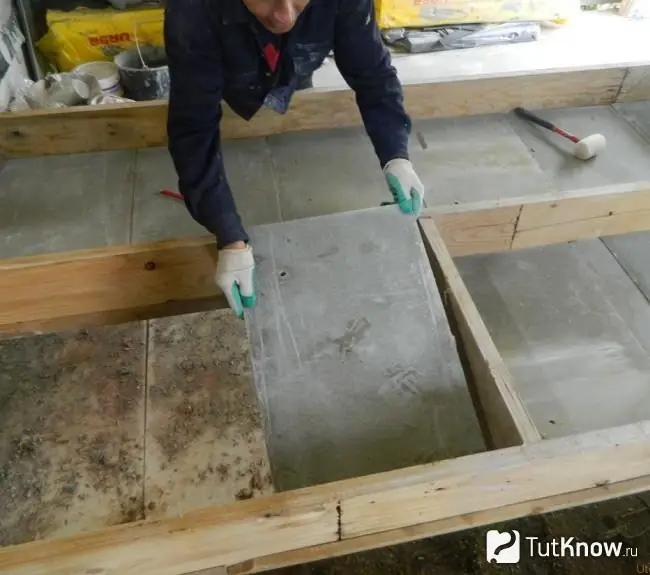
To begin with, the construction of any floor consists of a finishing and a rough coating and lies on a load-bearing base. For example, between floors, its function is performed by an overlap. The finishing coating can be tiled, parquet, concrete, plank, etc. The subfloor underneath the final subfloor is a multi-layer "cake". Its structure is determined by the type of finish coating, general requirements and the construction of the base.
The sub floor has the following components:
- Underlying layer. It serves to accept and evenly distribute the load from the coating along the base, as well as transfer it to the walls. The underlying layer can be a soil that has been trained according to the relevant requirements, or a floor slab.
- Leveling layer. It is needed to eliminate the irregularities of the previous layer and is quite dense. With its device, you can perform the slope of the surface using a screed, if one is planned.
- Intermediate layer. Acts as a bond between the outer covering and the underlying floor structure.
- Insulating layers. They provide protection against moisture and noise, and also serve as insulation. Their locations depend on the method of construction and the functional load of the floor system.
Rough flooring is usually made of a low-quality board: a picket fence, a slab, that is, something on which insulating materials can be laid. The main reason for this is the sensitivity of the material to fluctuations in temperature and humidity. In order to make the deformation of the finishing flooring as minimal as possible, lumber capable of it is chosen for the subfloor.
Rough wooden floor installation technology
For the installation of rough wooden floors, soil or concrete preparation can be used as a base. The flooring is laid on wooden joists or directly on the base. We will consider both of these cases below.
Subfloor on wooden logs
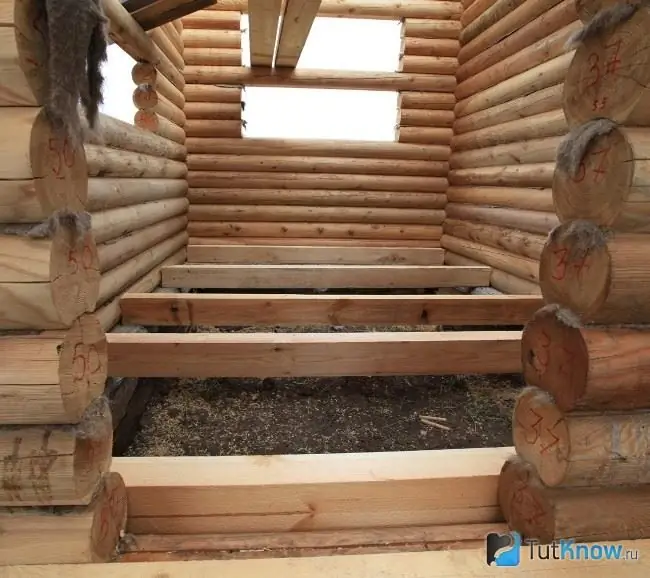
This floor has been used by many for a very long time and has become quite popular. Its production does not require any special skills. However, the subfloor on wooden logs has a significant drawback: since all its elements have rigid connections, the impact noise in this case is not sufficiently isolated. In addition, this option is not recommended for use in saunas, bathrooms, since the boards are sensitive to high humidity.
Logs are a beam that is a supporting part of the frame of a wooden floor. They can be made from solid wood or from boards of the second and third grade, connected in a special way to each other. As for a private house, it is better to use logs as a log, which are much stronger and more reliable.
Prepare them before laying. Since logs usually have an uneven surface, it is recommended to grind their upper part with an ax until a plane is obtained on which the elements of the finished floor will be attached.
The ends of the logs should be located in previously prepared grooves, which are cut in the crown of a log house or made in stone walls. The distance between the wall and the end of the log is taken equal to 2-3 mm. This will prevent the floor from squeaking underfoot. To preserve the edge of the lag, before installation, you need to treat it with an antiseptic or ordinary bitumen.
In addition to the grooves, the logs must have intermediate supports, which can be made of bricks in the form of posts. The distance between the supports should be 0.8-1 m. The breakdown of their location is performed using cords stretched over the entire area of the room.
For each column, you need to make a foundation. If the base is earthen, you should dig holes 40x40x40 cm in size, tamp their bottom, fill in 10 cm layers of sand and rubble, install a small formwork on top and pour concrete. The top of the resulting foundation should be 5-10 cm above the ground level. If the columns have a height of up to 25 cm, they are laid in one and a half bricks, if more, then in two. The top of the finished supports must be covered with roofing material in 2-3 layers.
Lags are installed on supports in increments of up to 1 m, depending on what material they are made of. After their installation, you can perform the next stage of work. It consists in installing a cranial bar on the logs, which will serve as a support for the rough flooring and insulation.
The bar should have a cross section of 50x50 mm. Its fastening is carried out using wood screws from each side of the log in their lower part. The bars must be fixed securely, otherwise the flooring may collapse along with the insulation. In order to save money, the timber can be made from a 150x40 mm board.
To do this, it is enough to dissolve it lengthwise into three equal parts. One board will make three beams 50x40 mm, which are quite suitable for laying rough flooring on them. The fastening of the timber must be carried out taking into account the thickness of the insulating material. If, for example, it is 10 cm, and the thickness of the rough flooring is 25 mm, then the distance from the cranial bar to the top of the log should be 12.5 cm. After installing the log and supporting bars, it is necessary to waterproof the rough wooden floor. For this, a polyethylene film with a thickness of 0.2 mm is used. It must be fixed with stapler staples to the lower surface of the log and brought to the walls of its edges. The film canvases are stretched overlapping, their joints are sealed with metallized tape.
The next step is to install the rough flooring on the cranial bars. This is a rather painstaking job, since you will have to cut a lot of boards with a length equal to the distance between the logs. If the logs are made of logs, the task is complicated by the fact that, due to their usual curvature, the rough floor boards will need to be harvested of different lengths.
For a bar, everything is simple: if the logs are installed at the same distances from each other, the preparation of rough flooring boards can be performed according to a template. The cut boards must be methodically laid on the cranial bars located on the sides of the logs, and fixed with nails or screws.
You can walk on the finished rough flooring, but it is undesirable - it has a different purpose. To move around the room during work, thick boards can be laid on the logs on top and all further operations can be performed from them.
After the installation of waterproofing and laying the rough flooring, you can start installing the insulation. The choice of heat-insulating materials is quite wide, so it is not difficult to buy the necessary products that are suitable in size and price. These can be slabs of mineral wool, foam or roll material.
All of them cut perfectly and are easily adjusted to the desired size. The insulation should be tightly laid between the logs on the rough flooring, avoiding gaps and "cold bridges" in the form of protruding parts. Its outer surface should be slightly below the level of the top of the log to provide a ventilation gap of 3-5 mm.
The installed heat insulator should be covered with a vapor barrier membrane, fixing it with brackets or wooden strips on the joists. This completes the installation of the sub-floor structure. In the future, on the logs, you can make a finishing coating from a grooved solid board or fix an intermediate layer of moisture-resistant plywood 12 mm thick on them for laying parquet, laminate, linoleum or tiles.
Rough wooden floor on a dry screed
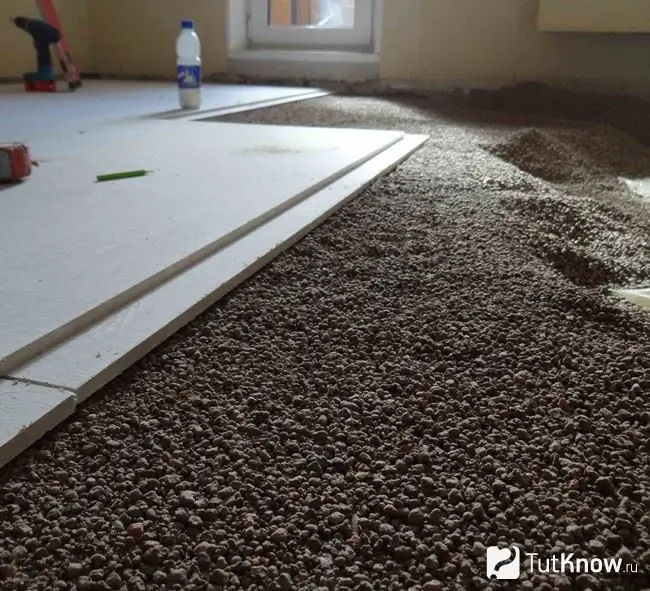
The above method for arranging a subfloor is convenient to use at the stage of building a house. When you buy it already in finished form, old floors can be made not on the basis of a wooden floor, but on a monolithic concrete. In this case, their alignment must be done in a different way. Of course, you can perform a simple screed on the lighthouses on top of such a floor, or use the "wet" method - pour the floor with a self-leveling mixture. However, a dry screed is much cheaper.
To lay a rough wooden floor on a dry screed, you first need to prepare the necessary tools and materials: chipboard or moisture-resistant plywood, electric jigsaw, PVA glue, expanded clay, damper tape, wood screws, tape measure, marker and ruler.
The work is carried out in stages:
- The concrete base must be covered with a waterproofing polyethylene film. Its canvases should be laid with an overlap of 20 cm, and their ends 10-15 cm long should be placed on the walls. So that the joints of the canvases do not diverge and are sealed, they should be glued with metallized tape.
- The next stage is pasting the bottom of the walls around the perimeter of the room with a damper tape. The height of the pasting should be greater than the thickness of the layer of loose insulation, which will serve as the basis for the subfloor.
- After gluing the tape, you need to install the beacons using a water level for this. Their height can be adjusted using small blocks: removing and placing them, you can get a flat horizontal plane of the future base.
- As a heater, you can choose expanded clay. It must be poured onto a concrete base and leveled with a rule, moving it along the lighthouses. It is not recommended to cover the entire area with expanded clay, it is better to lay it in the amount required for the installation of the first sheet of chipboard or plywood. This is more convenient, since it is much easier to walk on a flat floor than on a shifting layer of insulation. The minimum thickness of the expanded clay layer is assumed to be 20 mm. It should not be made thinner, since the subfloor in this case can "play" underfoot.
- After laying the first sheet of plywood on expanded clay, many immediately have doubts whether everything has been done correctly. After all, if you stand on it and walk a little, you can feel how the laid sheet begins to gradually sink into the layer of insulation. However, you should not be afraid of this: after layering the following sheets, you can make sure that the dry screed works normally, and all the sheets lie flat without any displacement. The installation of plywood must be done carefully, trying not to move the sheets too much, since the movement of 15 kg plates can deform the surface of an even layer of insulation.
- The connection of the sheets to each other is carried out with ordinary wood screws. The optimum mounting pitch is 100-120 mm. For greater reliability, the joints of the sheets can be greased with PVA glue before installation. It must be applied in a small layer "snake", since the structural elements will be additionally connected with screws.
- After the installation of the sheets of the rough flooring is completed, their joints must be sealed with wood putty, wait for it to dry and sanded with sandpaper or abrasive fine mesh No. 80-100.
- If the dry screed is performed in a bathroom or other wet room, the floor surface must be treated with any coating waterproofing, for example, bituminous mastic. After that, tiles or other suitable finishing material can be laid on it.
How to make a rough wooden floor - watch the video:

It's all. We hope our material will help you to make a high-quality subfloor made of wood, which is the basis for the smooth operation of the floor covering. Good luck!