Coarse leveling agent, its characteristics, ready-mix laying technology and main manufacturers. A rough leveling compound is a multi-component dry mortar designed for leveling a sub-floor, which consists in eliminating significant differences in its surface and correcting other serious defects. You will learn about the technique of working with this material in this article.
Coarse Leveling Specifications
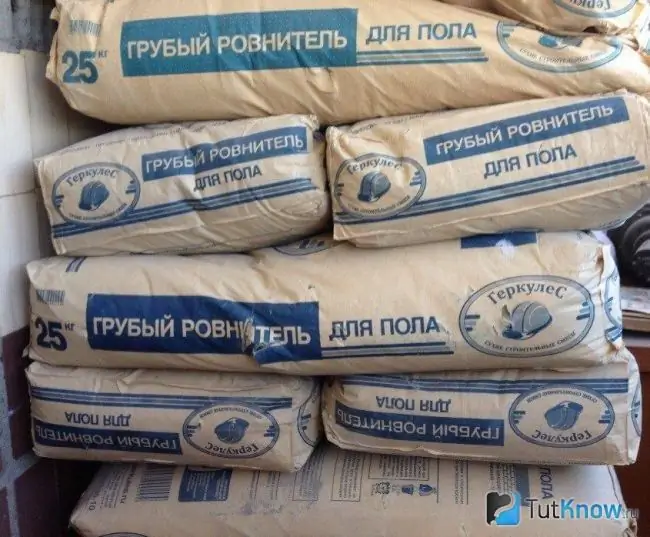
The coarse floor leveler contains coarse particles, thanks to which, after mixing, the mortar can be applied in a thick layer in one pass. After polymerization, the finished screed is very strong and crack-resistant. All mixtures can differ in structure and filler fraction, their composition and properties. The main technical parameters of coarse dopants are presented below:
- Composition … It includes cement M200-M400, sand, mineral fillers and polymers. Some leveling agents can be supplemented with reinforcing fibers and lime.
- Colour … Depending on the components included in the composition, the leveling agent can have light gray and dark gray shades.
- Filler fraction size … As a rule, the particles present in the substance have a size that is 0.5-1.2 mm.
- Layer thickness … All coarse leveling materials can be applied in one go and have a screed thickness of 5 mm to 7 cm. Special products offer a reduced layer thickness of up to 2 mm or an increase of up to 10 mm.
- Viability of the composition … All cement mixtures harden quickly outdoors. Therefore, it is recommended to use up the coarse leveling agent after mixing within 0.5-1.5 hours. The hardening time depends on the amount of additional additives in the solution: the fewer there are, the faster its polymerization.
- Mixture consumption … 1 m2 floor area with a layer thickness of 1 mm is required for leveling 15-17 kg of dry mix. On the packaging with the material, the manufacturer always indicates the consumption of the coarse leveling agent, that is, for what surface area one bag of the mixture is designed. For example, "PROFIT Monolith packaging" 25 kg when laying a screed with a thickness of 3 cm is designed for a floor area of 0.5 m2, then with the same screed thickness by 16 m2 the surface will need 800 kg of dry mix, packaged in 32 bags.
- Water consumption … In order to make a working mixture, it is necessary to observe the following powder / water ratio: 1 kg / 130-200 ml. These proportions are also specified by the leveling agent manufacturer for each grade of mix. The water consumption when mixing the components of the solution cannot be exceeded, as this can lead to a decrease in the strength of the finished screed.
- Frost resistance … Dry mix without loss of its properties can withstand up to fifty cycles of alternate freezing and thawing.
- Temperature … High-quality drying of the screed from the leveling agent is possible at an air and base temperature from +5 to +25 degrees.
- Polymerization time … Walking is allowed on the hardened screed after 7 hours, the next layer can be poured in a day, the finishing coating device - after 1-2 weeks, and the complete drying of the roving with a set of its maximum strength occurs after 28-35 days. All these periods are valid at an optimum positive temperature of 20-25 degrees. If it is lower, the curing time of the applied coating will increase.
- Storage … Before use, the material is stored from the date of production up to a year in its original undamaged packaging and in a dry place. For its guaranteed safety, it is recommended to pack paper bags with leveler in a sealed plastic wrap and put them in several rows on pallets.
- Packaging … The roving material is packed in paper bags. In them, the material is packaged in 20 and 25 kg.
- Appointment … The material can be used for leveling hard foundations of concrete, stone and brick floors, followed by the installation of a topcoat. In addition, the leveler is suitable for underfloor heating when installing a base layer, creating a sloped base and pouring a "floating floor".
The positive qualities of a rough floor leveler include its frost resistance, plasticity, a high degree of adhesion to the substrate and environmental friendliness. The screed, made on its basis, is distinguished by moisture resistance, heat and sound insulation properties, wear resistance and a low probability of cracking.
Major manufacturers of floor levelers
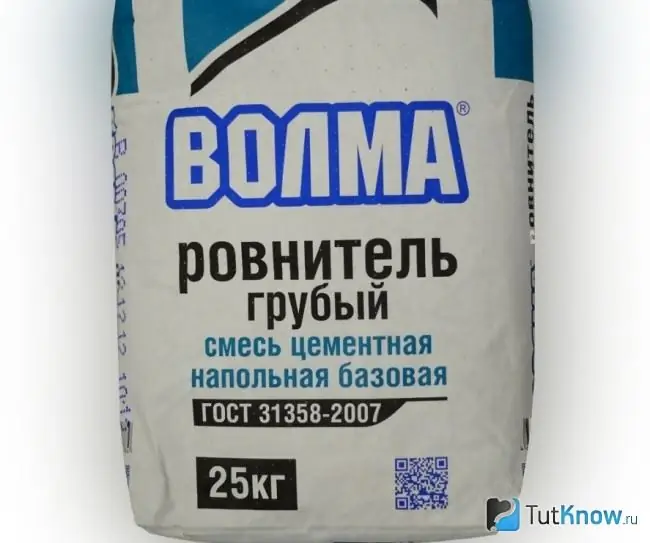
Several companies successfully operate in the modern construction market that have dry floor mixes, including rough leveling agents, in their product range.
The most popular ones are:
- LLC "Mask" … Russian plant producing dry construction mixtures. Its products are distinguished by ease of use, affordable price, high quality and stable characteristics during storage and stacking of the finished solution. Rough leveler "Mask" is used for leveling and arranging horizontal floor surfaces in rooms with different functional purposes. The basic basis for its laying can be a reinforced concrete floor, compacted soil, gravel-sand base and many other hard surfaces. The main advantage of the "Mask" leveler is the increased strength of the screed made on its basis. The material is supplied in bags of 25 kg, the cost of one package is 150-200 rubles.
- Volma LLC … It is the largest Russian industrial group, which includes 6 factories, about a dozen sales centers and 150 dealers. The company started producing dry floor mixes in 2009 after the launch of additional production lines. The coarse Volma leveler is used both for repairing floors and for their initial filling on a cement-sand and concrete base. The permissible thickness of the screed layer made of this material is 10-100 mm. The mixture is suitable for use indoors and outdoors outside buildings. The leveler is laid by hand; a screed based on it can serve as a base surface for any self-leveling mixture. The material is packaged in 25 kg, the cost of one package is 180-230 rubles.
- PROFIT … This is a plant from the Russian company "Livna", which has been producing building dry mixes since 2003. Currently, he produces two types of floor levelers - "PROFIT Monolith" and "PROFIT Monolith MN", which differs from the first in the possibility of machine application to the base surface and a slightly higher price. The thickness of the screed layer made with these materials can be 5-75 mm. The solution is suitable for making a "warm floor", "floating" coating and creating a finishing layer. On the screed made with PROFIT Monolith leveler, you can lay laminate and ceramic tiles, carpet and linoleum and apply self-leveling mixtures. The material can be used for indoor and outdoor use. It contains environmentally friendly components: sand, cement and mineral additives. When special polymers are added, adhesion and plasticity are ensured to the solution, and frost resistance, strength and moisture resistance to the finished screed. Equalizers of both types are available in 25 kg bags. The price of PROFIT Monolith is 130-200 rubles. per package, and "PROFIT Monolith MN" - 160-220 rubles.
- Hercules-Siberia … This is a Russian plant located in Novosibirsk and produces high quality dry building mixes for floors. The products of this company are distinguished by easy installation and economical consumption. All mixtures of the Hercules brand have excellent performance characteristics. Due to the presence of modifiers and polymers in its composition, the ready-made mortar has increased elasticity and adhesion, and the screed is waterproof and resistant to wear. A working compound made on the basis of Hercules coarse leveling material is used for the manufacture of screed floors and requires a solid base. It is allowed to lay a screed layer 5-100 mm thick at a time. The mixture is intended for indoor work. It is composed of quartz sand, polymer additives and a composite binder. The finished screed is distinguished by increased moisture resistance. For implementation, the Hercules dry mixture is packed in 25 kg paper three-layer bags, the price of one package is 180-200 rubles.
- "MC-BAUCHEMIE" … This is a Russian-German company that produces dry floor mixes under the Plitonit brand. All of them comply with European standards and have quality certificates. The company manufactures four types of rovings. The composition "Plitonit P1 easy" is intended for rough leveling of floors and slopes, the thickness of the screed can be 10-50 mm. It can be installed both inside and outside the building. All mixtures of the Plitonit brand are packed in bags of 20-25 kg. The average price of Plitonit P1 easy is from 200 rubles. Rovnitel "Plitonit P1 PRO" differs from the previous mixture by the possibility of using a ready-made screed without its topcoat and a price of 260 rubles. The mixture "Plitonite P1 Light" is distinguished by a reduced material consumption and the ability to lay a layer of mortar 20-100 mm thick at a time. The cost of this material is 300-350 rubles. per package 20 kg. Rovnitel "Plitonit P200" is a professional team. It is used both for the initial pouring of the floor and for its leveling, it can be used in domestic and industrial premises, create surfaces with a slope, poured onto soil, sand and concrete base. A screed based on a mixture of Plitonite P200, thanks to the reinforcing fiber included in its composition, is highly resistant to wear. The cost of this material is 360-400 rubles. for 25 kg.
Coarse screed technology
A coarse leveling compound is used as a floor base mix. The work of making a screed from this material consists of several successive stages, each of which is very important for obtaining a high-quality final result.
Preparation of the floor surface for the installation of the screed
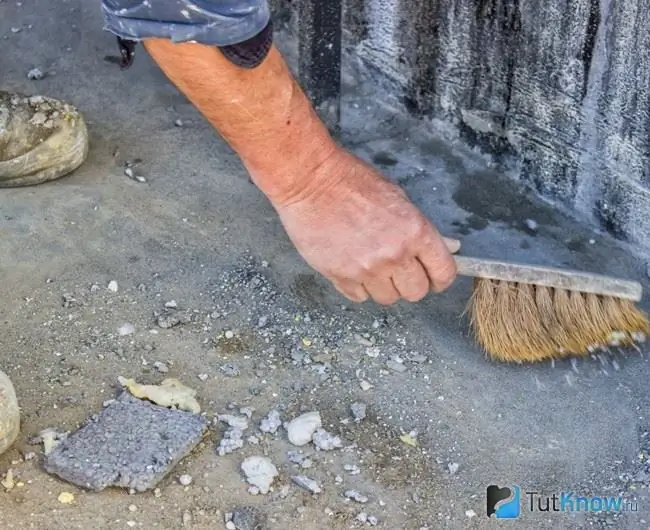
For the manufacture of a screed, three main conditions must be met regarding the preparation of the base: it must be clean, strong and firm.
If there are deep cracks or potholes on the surface, they can be repaired with a cement-sand mortar, the protrusions and sagging on it are knocked down with a perforator or chisel.
After removing cracks, gouges, sagging and protrusions, it is necessary to clean the base from dust, dirt and stains, which can further reduce the adhesion of the screed in some places. Rubbish from the floor is removed with hands and a brush, and dust - with an industrial vacuum cleaner. Stains of paint, oil, bitumen can be removed with the help of special removers, solvents and sandpaper.
The cleaned surface in front of the screed device must be treated with a fixing impregnation or primer. Their main purpose is to reduce the dusting and absorbency of a cement or concrete surface. Thanks to this treatment, the likelihood of shrinkage cracks on the screed in the future is significantly reduced. The surface should be primed at least 5 hours before starting the leveling.
Preparation of floor screed mortar
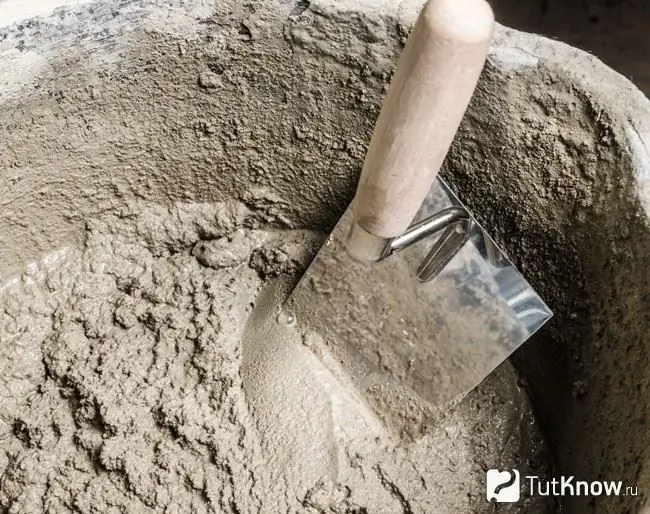
When preparing a solution from a dry mixture, one rule is the main thing: an equalizer should be poured into the water, but not vice versa. This sequence allows you to make a high-quality homogeneous working mixture for leveling the floor.
For 25 kg of dry mix, an average of 6 liters of water at room temperature are required. All necessary proportions are always indicated on the packaging with the material. Water must be poured into a plastic container, and then gradually add the dry roving mixture to it, stirring the solution for 5-8 minutes with a mixer or a special nozzle clamped in the chuck of an electric drill. After this procedure, the mixture must be left for 5 minutes, and then mixed again for 2-3 minutes.
It is important to know that the pot life of the finished roving mixture is 60-90 minutes. Therefore, it is necessary to prepare it in such a way that during this time it is possible to use a certain amount of solution without residue.
Laying the rough leveling material on the floor
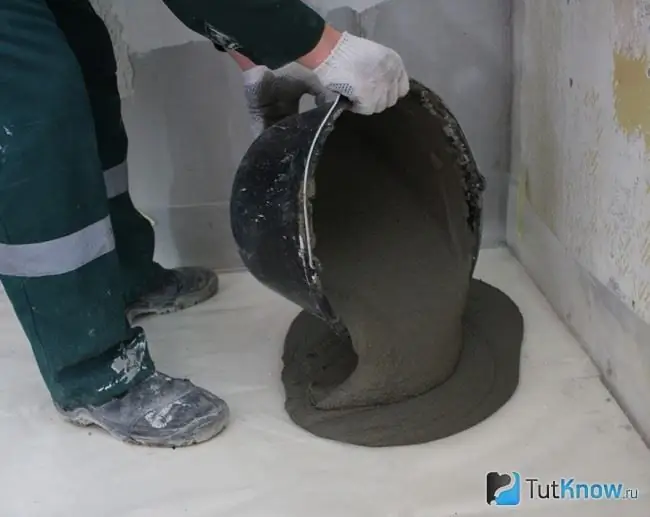
The leveling screed of the floor is made in strips that are located between the pre-installed beacons. The metal profiles that are used for their manufacture are placed on the entire floor area parallel to each other with a step of 0.5-1.5 m. The upper part of the beacons should be located in the same plane, providing the effect of its leveling during the laying of the screed.
To install the lighthouse profile along the line of its intended laying, small slides of cement or gypsum mortar are applied every 40 cm. Then the profile is slightly pressed into them while simultaneously leveling it in the horizontal plane, using the building level as a control tool. The upper plane of the lighthouse should be from the level of the base surface of the floor at a distance equal to the planned thickness of the screed.
Along the perimeter of the room, an edge strip, the so-called damper tape, is glued to the base of the walls. It is necessary to relieve stress and compensate for thermal deformations of the laid screed. In rooms with an area of more than 32 m2 its sticker is required.
The damper tape is made of foamed polyethylene, has a width of 15 cm and a thickness of 0.8 cm. One side of it is covered with an adhesive layer, making the installation of the product as simple as possible. The upper part is divided by perforation into strips 1 cm wide. They can be easily separated if the width of the strip is greater than the thickness of the screed.
The ready-made roving solution is poured into the strips between the beacons and the mixture is spread with a metal spatula over the floor area limited by the profiles. Then, using a rail or a rule, it is smoothed by moving the tool along the installed beacons, as if along rails. In this case, the voids appearing on the surface of the screed are closed by adding a working mixture of the leveling agent to these places, followed by smoothing it. If the solution is laid in several layers, each of them must dry for at least a day.
In addition, there is a technology, when using which beacons do not remain in the screed after it has hardened, but are removed in the process. To do this, after their installation in one level, the leveling device is laid through one strip. When the aligned screed in the cells hardens, the beacons are removed, and ready-made coating strips are used to fill empty cells instead of guide profiles.
A floor screed freshly laid with a rough leveling agent needs protection from sunlight, drafts and artificial heating for three days. These measures are necessary to prevent uneven drying of the finished screed and its drying out. Otherwise, the appearance of cracks on the floor surface cannot be avoided.
How to make a screed with a rough leveler - watch the video:
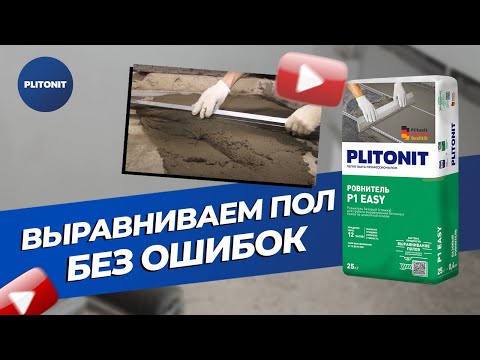
The rough leveling material is irreplaceable for the floor. Due to its qualities, it reduces the load on the base and makes it possible to carry out repairs in a short time.