The main nuances of ceiling insulation with polystyrene foam, the advantages and disadvantages of this heat insulator, how to prepare the surface, perform basic work, plasterboard cladding and finishing the insulated ceiling. Ceiling insulation with foam is a reliable and effective technology that has been used for the past several decades to maintain a comfortable thermal regime in rooms. Due to the fact that this heat insulator is distinguished by its low weight and high heat-conducting characteristics, it has received such well-deserved recognition when insulating any type of building.
Features of thermal insulation of the ceiling with foam
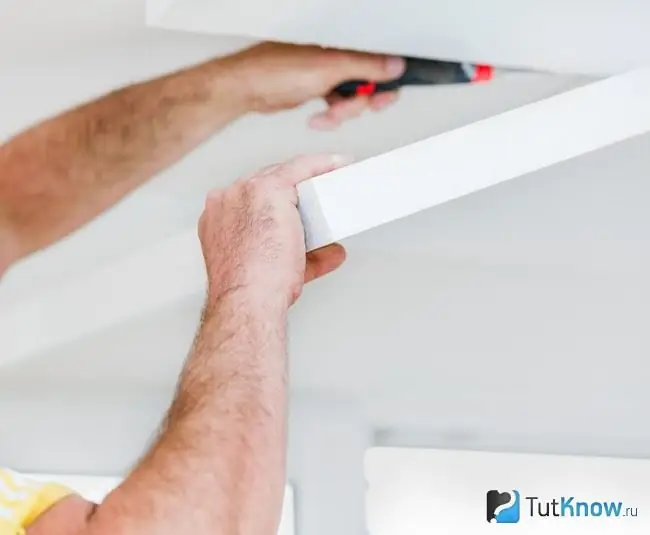
Polyfoam as a building material has been known since the middle of the last century thanks to the discovery of German scientists. He quickly gained confidence and began to be used in various areas of human life.
The raw material for it is polystyrene granules. A special airy structure of the foam is given by the process of foaming of these granules under the influence of high temperatures, pressure and water vapor.
During production, they increase in size 20 times or more. As soon as the required volume is reached, the granules are discharged from the tank. Then they dry out and are compressed. Thanks to the addition of adhesives, finished foam boards are formed.
This material has a high density, so there are no serious problems with laying. However, care must be taken not to cause severe deformation in any area - in this case, it will store heat worse.
Another important feature: the foam allows installation without a backing of a vapor and waterproof layer. But, if thermal insulation work is carried out in a wooden house, you cannot do without vapor barrier.
In addition, if you are interested in how to insulate the ceiling with foam, then you should remember that its sheets are stacked without any cracks and irregularities, that is, with maximum density to each other. In cases where it is technically impossible to achieve this, you can use special fillers for voids, and glue the seams with construction tape or assembly tape.
Polyfoam not only perfectly retains heat inside the house. It does not allow moisture to pass through itself, and therefore ventilation must be established in the room. Otherwise, the moist air will have nowhere to go, and it will remain in the insulation itself, causing the finish to get wet, and with it, the appearance of foci of mold and mildew.
It is believed that the foam is not safe for health. But if the operating conditions established by the manufacturer are observed, then it will not emit any substances harmful to the health of the inhabitants.
The only point that the owners of private houses need to pay attention to is the tendency of rodents to equip their holes in such a heat insulator. Therefore, the material must be additionally treated with agents against them and securely closed.
In the process of insulating the ceiling with foam, it is important to ensure a favorable temperature regime within + 5-30 ° C. This will serve as an additional guarantee of the reliability of the heat insulator fastening and the preservation of its operational characteristics in the future.
Advantages and disadvantages of ceiling insulation with foam
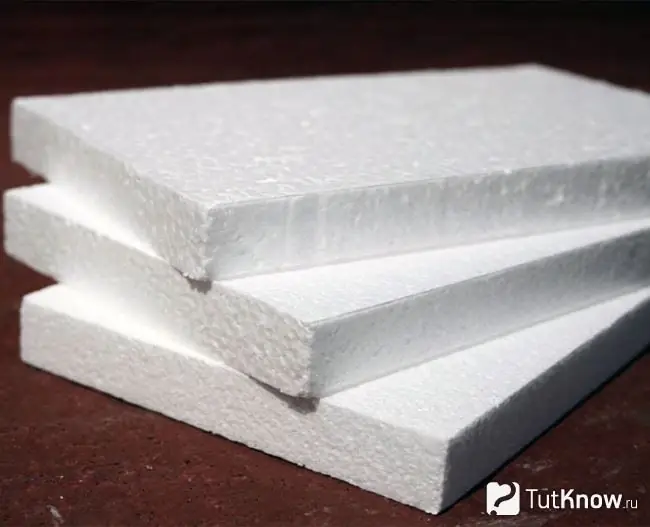
Polyfoam has been known for many decades for its unique qualities, such as:
- Low hygroscopicity, which in most cases allows you to do without laying steam and waterproofing;
- Excellent insulation characteristics along with low thermal conductivity;
- The invariability of the structure even under the influence of a wide temperature range;
- Absence of shrinkage processes over time, excluding the appearance of cold bridges;
- High resistance to the action of chemically unsafe and active substances;
- Good soundproofing qualities, to which the foam plastic owes its low dynamic stiffness;
- Resistant to the formation of areas of mold, dampness, decay and mildew;
- Light weight, easy to install together with ease of handling.
To be fair, it should be noted that the insulation of the ceiling of the house with foam plastic has a number of disadvantages:
- Everyone knows that during combustion, this heat insulator releases many toxic and corrosive particles that can pose a threat to human health. Despite the fact that the foam does not burn, in molten form it produces a poisonous gas that can cause respiratory paralysis.
- Low service life. Manufacturers give a guarantee only for 10-20 years of service, and if the technology of the work is observed properly.
- Insufficient natural ventilation. This fact is due to the fact that the foam itself does not differ in vapor permeability, which can inevitably lead to the formation of condensation in insufficiently ventilated rooms. We'll have to install forced ventilation of the supply type.
Ceiling insulation technology with foam
Thermal insulation of ceilings with foam includes adherence to all technological nuances, such as calculating the number of foam sheets, the correct sequence of stages and the quality of the material itself, without which it is difficult to create an effective heat-protective coating.
Preparatory work before installing the foam
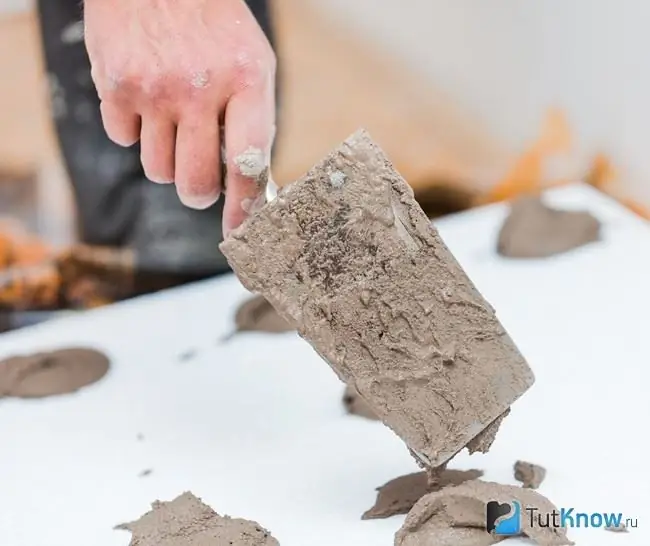
Before carrying out insulation and any types of repair work, it is important to make careful calculations of the required amount of material. For ceilings, the area is set by multiplying the width and length. The very insulation of the ceiling with foam plastic with your own hands can be done with material of different thicknesses: from 2 to 10 cm, however, sheets of 5 cm and with a density index "PSBS 15-35" will be optimal.
The heat insulator can be fixed in different ways: either on dowels equipped with wide hats, or using an adhesive mixture. On the building materials market, you can find a huge number of types of glue on sale. When choosing it, keep in mind that it should be designed specifically for expanded polystyrene plates.
The mixture can be used either for gluing the product, or for fixing an additional protective layer. In this case, it is possible to fix the reinforcement mesh and make a leveling layer on top of it.
As for the consumption of glue, it depends on the type of surface on which the thermal insulation is carried out. Average indicator - 10 kg / m2if fixation of the reinforcement and final alignment will be carried out.
When diluting the mixture, you need to pay attention to its consistency: it must be thick enough so that it retains its shape when placed on a spatula, and does not creep out of it. A more liquid solution is used to fix the mesh and create a leveling layer.
Immediately before carrying out the insulation work, the surface is prepared. The remnants of old paint and whitewash must be removed, the ceiling itself is washed from dirt and dust particles. After that, leveling is performed using soil and filler mixtures. It is very useful to treat ceilings with antiseptic substances.
From the tools you need to stock up on: a drill or a perforator, a small hacksaw or jigsaw, a level, a plane, a sharp knife, a tension cord, a scraper, a hammer.
Consumables and accessories will require the following: adhesive mixture for working with foam, ground paint, insulation sheets, drywall sheets, polyurethane foam, finishing putty, dowels, SD and UD profiles, wooden beams.
Note! Any kind of electrical work must be performed before the ceiling is insulated with foam.
Instructions for installing foam on the ceiling
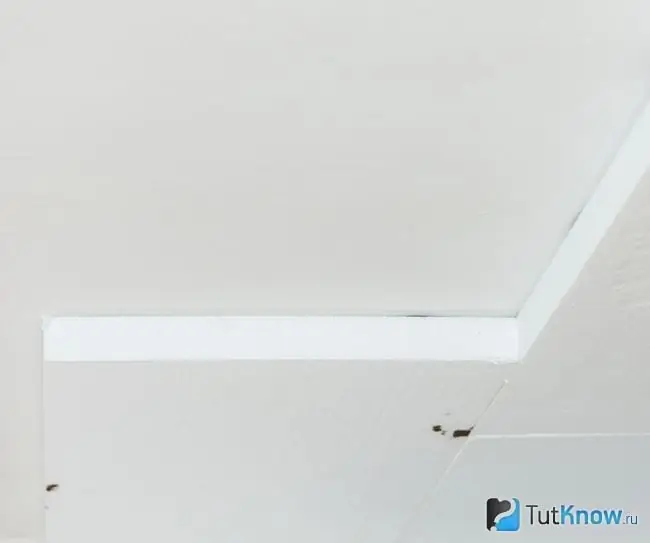
So, the available step-by-step algorithm for carrying out insulation can be reduced to the following stages:
- First, a frame is installed, which is selected based on the humidity in the room. It can be built from a metal profile or wooden beams. The frame components are drilled tightly to the ceiling.
- Styrofoam sheets must be trimmed to the exact size of the cells, since this material does not tend to change shape over time.
- As soon as the sheets have been cut, the construction of the metal cross-sections can be started. They are fastened with dowels at a distance of about 0.5 meters from each other. Experts recommend using a professional level for this. All profiles are attached to one another with metal screws.
- As for fixing the insulation, this can be done either with an adhesive mixture or with screws. In both cases, the joints and gaps must be treated with polyurethane foam, which will reduce heat loss.
- Then proceed to the installation of the lathing. If it is made of wooden beams, then a layer of a vapor barrier must be laid on top of the foam plastic, which will delimit it and the finish.
- You can use the option of fasteners without installing the lathing, exclusively with glue. This method is also quite effective, but, in addition to the glue itself, it is advisable to additionally nail the foam pieces with dowels with a "fungus" -type cap.
- Be sure to pay attention to the density of fixation of the heat insulator. Each sheet must be pressed down for approximately two minutes. As soon as the entire ceiling is pasted over, the insulation is nailed in with wide dowels.
- When they are hammered, a hole is first made to its length and even a little more. To do this, we add the thickness of the insulation, the vapor barrier layer, the finish and add a recess in the wall by about 5 cm. The dowels are driven in not only in the center, but also at the junction of individual sheets.
- The sheets should be fastened in a checkerboard pattern. When driving in the dowels, it is desirable that their cap is flush with the outer edge of the heat insulator. Even if it is deepened into it by 1-2 mm, this is also considered the norm. When the dowel cannot be completely driven in, the remainder of the length can be trimmed with metal pliers.
- Before the start of finishing work, a reinforcing layer is created. For this purpose, a special solution is applied to the heat insulator sheet in an even layer. A mesh for reinforcement is placed in it, recessed and remains in it until it dries completely.
- As soon as the solution, together with the mesh, is completely dry, a second layer is applied and left to dry.
Finishing the ceiling
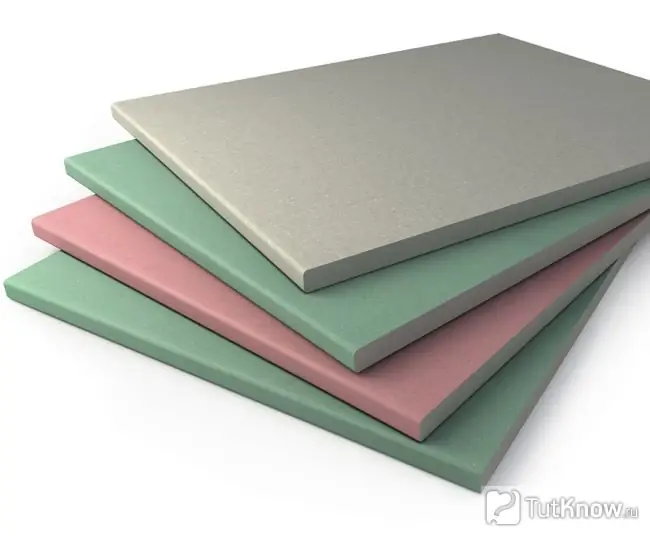
One of the most successful materials with which you can sew up an insulated ceiling and hide irregularities or differences in height is drywall. Measure and mark the surface before sewing. After the marking has been carried out, it must be checked using a level and a tension cord for this.
Installation of the frame for drywall begins with the fastening of UD-profiles. The guides are fixed with the lower edge along the marked line, which will remain under the profile. For fixing, you can use the same dowels with which the heat insulator was attached.
After that, the places where the CD-profile will be installed are marked. It is advisable to do this in the areas of connection of drywall sheets.
It is optimal to fix the transverse profiles at a distance of 40 cm from each other. After that, plumb lines are installed - a step of 1 meter is used for them.
You can start fixing the CD profiles after the plumb lines are fixed. By setting the required level of the horizon, they are fastened with self-tapping screws for metal. At the end, each CD-profile is inserted into the UD, and the individual parts of the battens are connected with self-tapping screws. If you plan to install fixtures on the ceiling, then you can start laying electrical wiring.
When insulating the ceiling with foam plastic, the plasterboard sheathing technology should imply the obligatory trimming of the corners of each sheet, which will allow high-quality puttying of the corners. If this condition is neglected, then the cardboard will get wet and peel off from the filler. For processing corners, an edge plane is used with which you can cut the corner at the same level along the entire length of the edge.
A hacksaw with sharp and fine teeth is required to properly cut drywall. A line is marked with a pencil at the site of the intended cut. A long and straight ruler is applied to the line, and along it should be drawn with a sharp knife, making strong pressure. After that, the sheet is placed on the table in such a way that the break point is along the edge of the table. It remains to bend the sheet, which will break off strictly according to the markings. On the reverse side, it remains to make a cut in the paper.
In exactly the same way, all plasterboard products are trimmed and mounted. After this stage is completed, you can begin the final decorative finishing. For this, there is a wide variety of materials and technologies, from painting with enamel to wallpapering with various textures and applying decorative plaster.
To improve the bonding properties, the final finishing must be preceded by a thorough priming of the surface. This stage is mandatory when processing the ceiling with paints and varnishes.
Painting is carried out only on a perfectly leveled surface with a roller, manually or using a spray gun. The enamel is selected based on the requirements for the final result and its purpose. During the staining process, it is imperative to maintain the time intervals for each of the layers to dry completely.
One of the simplest finishing methods is wallpapering, the variety of colors and textures of which will make the interior very attractive in a short time. They can be harmoniously combined with the overall style of the room to make it even more expressive. For those who want to get an individual color background, the best option would be to apply paintable wallpaper.
Another successful and modern option is decorative plastering. Today, manufacturers not only use various types of original textures, but also add coloring pigments, thanks to which the decorated surface is radically transformed. The finishing plaster may contain inclusions that will add their own flavor to the interior of the room.
In general, the gypsum plasterboard used to protect the foam insulation is a pliable material that allows you to create original ceiling structures. Among other things, both foam and drywall are distinguished by excellent soundproofing properties and serve as an obstacle to the penetration of extraneous sounds into the room.
How to insulate the ceiling with foam - watch the video:
[media = https://www.youtube.com/watch? v = nwCF-R5dhWA] Due to the affordable price, ease of installation and extremely low weight, all types of foam are widely used in thermal insulation works, including for ceilings. By following the instructions specified here, you can carry out the insulation on your own, without the involvement of professional construction crews.