For centuries, wood has served as the main building material for people. The development of technology has provided him with a worthy alternative - expanded clay concrete, which does not rot and is not afraid of insects. How to build a bathhouse from expanded clay concrete blocks with your own hands - this is our article. Content:
- Advantages of blocks
- Erection of the foundation
- Wall masonry
- Roofing device
- Warming and finishing
Expanded clay blocks are made from sintered granular clay, cement and sand by forming products with their subsequent vibration pressing. They are much larger than bricks in size, this speeds up the process of erecting walls and simplifies it. The fraction of expanded clay granules in a block affects its density and weight. The larger it is, the lighter the stone. Dense blocks are used for the construction of foundations, and light or hollow blocks are used for laying walls and partitions.
Advantages of expanded clay concrete blocks in the construction of a bath
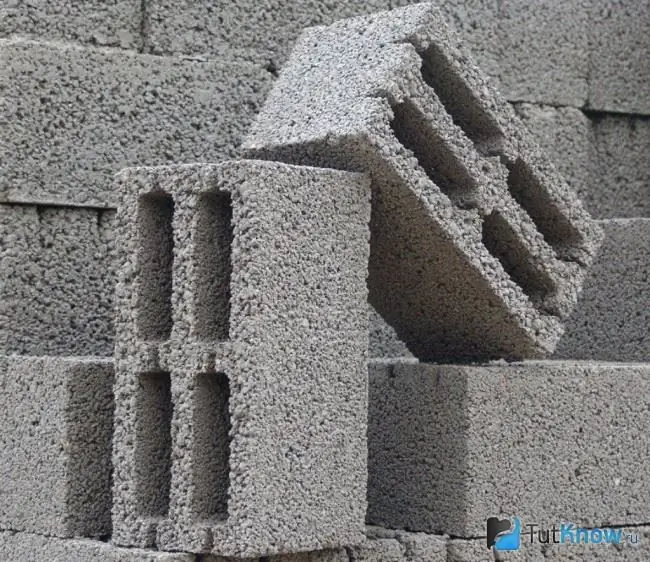
Expanded clay blocks have gained high popularity among developers due to their undoubted advantages, such as:
- Affordable price;
- Low consumption of binding materials for masonry;
- The strength of the material and its resistance to significant loads;
- Low thermal conductivity, which reduces the cost of wall insulation;
- Fire resistance, which is important when installing furnaces;
- Ecological cleanliness;
- Frost resistance even when wet;
- Easy finishing of their surfaces.
These qualities allow the products to be used in the construction of baths in any region, especially where wood materials are expensive or unavailable.
Construction of a foundation for a bath from expanded clay concrete blocks
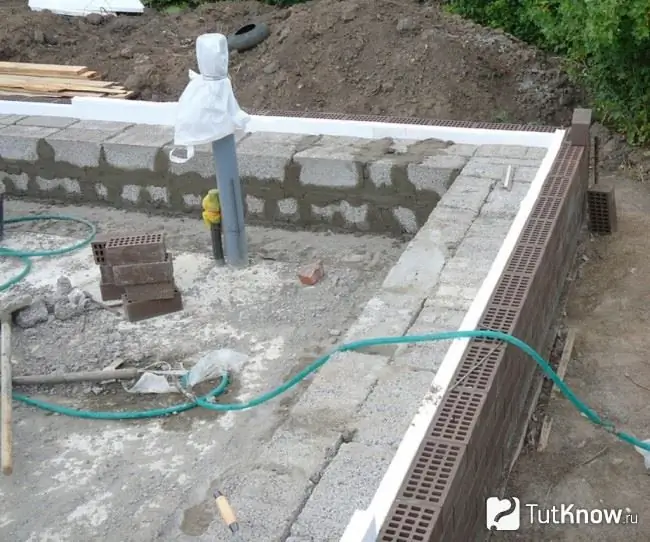
Strong baths made of expanded clay concrete blocks are erected on strip or columnar foundations. For a columnar structure, dense blocks are used that contain a fine fraction of expanded clay and have high strength. Foundation pillars are installed at the corners of the future bath and every 2 m under the walls. On top of the pillars, a metal strapping is made from a channel or corners, on which walls are erected. Such a foundation is suitable for small baths.
For more solid structures with recreation rooms, a bathroom and a pool, a strip foundation is being built:
- For its device, all unnecessary is removed from the site allocated for the construction of the bath and the fertile soil layer is cut off. With the help of a cord and pegs, the corners of the future building and the line of the walls are marked. The foundation is planned under load-bearing walls and capital partitions.
- A trench for the foundation is dug to a depth of 0.4 m. Crushed stone and sand are poured into its bottom layer by layer. The total thickness of the backfill is 0.3m. It must be tamped with periodic moistening with water.
- Then roll insulation is laid in the trench, consisting of two layers of roofing material. It is necessary to prevent the foundation from getting wet from the capillary rise of ground moisture.
- On the laid waterproofing, a foundation of solid blocks is arranged. For a small bath, 3-4 rows are enough. The masonry is carried out on a cement-sand mortar with a seam thickness of 0.8-1.0 cm and the dressing of stones between the rows. To increase the strength of the foundation, the masonry is reinforced with a metal mesh.
- During work, it is necessary to use the building level, since mistakes made during the installation of the foundation can affect the quality of the entire construction of a bath from expanded clay concrete blocks.
- In a couple of days, after the solution has completely hardened, the strip foundation is waterproofed from expanded clay concrete blocks. It is performed from all sides with a brush and bitumen mastic. On top of the foundation, 2 layers of roofing material are additionally laid.
Bath walls masonry made of expanded clay concrete blocks
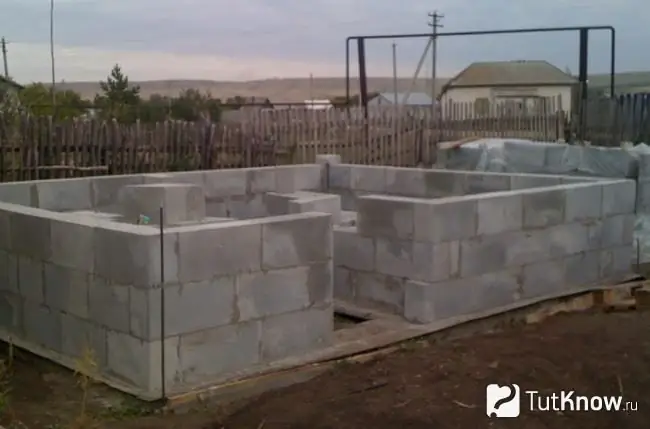
For masonry walls, in contrast to the foundation device, hollow expanded clay concrete stones are used. To start work, "beacons" are installed at the corners of the building, a cord is pulled between them and the usual laying of blocks is carried out with bandaging the rows. Using a trowel, the mortar is applied on top of the previous row and leveled in the plane. On top of the mortar, a block is laid along a cord and deposited with a trowel handle. This removes air and excess mortar from the seam.
Every 2-3 rows of masonry, the solution is reinforced with a metal mesh, pre-cut to the width of the block and rolled into a roll. As the stones are laid, it is rolled out and sunk in the solution by half.
Window and door openings are made from above with reinforced concrete lintels or channels.
In the upper and lower rows of masonry, "pockets" are arranged for supporting the ends of the ceiling and floor beams. The beams are made of 100x150 mm timber, their ends are treated with an antiseptic and, after drying, with a coating waterproofing. The fastening of the beams in the "pockets" is carried out using a metal corner. The free space is filled with mineral wool insulation.
The last upper row of wall masonry is made of solid blocks. Every 1, 5-2 m, anchor bolts are fixed in them for the future installation of a wooden Mauerlat on them - the base of the bath roof. Internal partitions are made from hollow blocks after the completion of the masonry.
Roofing over the bath made of expanded clay concrete blocks
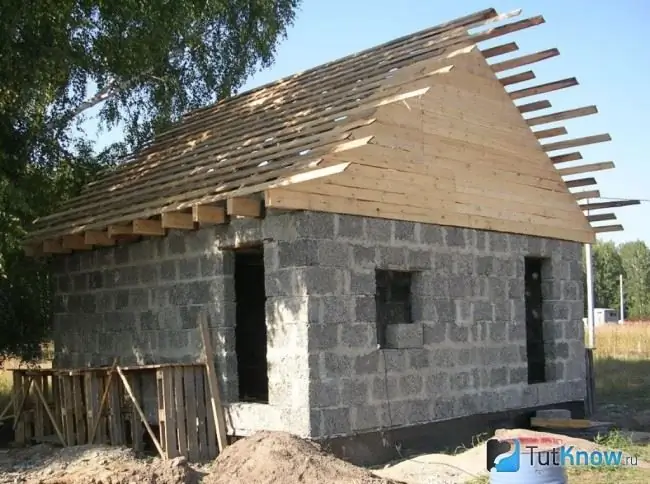
The roof for a bath is usually gable or pitched. There are projects of baths made of expanded clay blocks, which involve the construction of an attic floor. For regions with heavy snow load, gable roofs are preferable. Shed roof structures are more often used in saunas that serve as extensions to the main residential building.
Work begins with the installation of the Mauerlat on the anchor bolts of the upper row of wall blocks. The rafter system will be fixed on it. Due to the fact that the bathhouse from the blocks does not experience a significant draft, the rafter system of the gable roof is made on a layered basis. In this case, the beams of the rafter legs rest on the Mauerlat, the ridge beam, additional struts and wooden racks.
After the installation of the system, its rafters are covered with a waterproofing film, and the crate is stuffed over them. The roof covering is attached to it. For a bath roof, it is better to choose non-combustible materials - metal tiles or profiled flooring. If the attic is to be heated, the roof must be insulated.
Warming and finishing of a bath from expanded clay concrete blocks
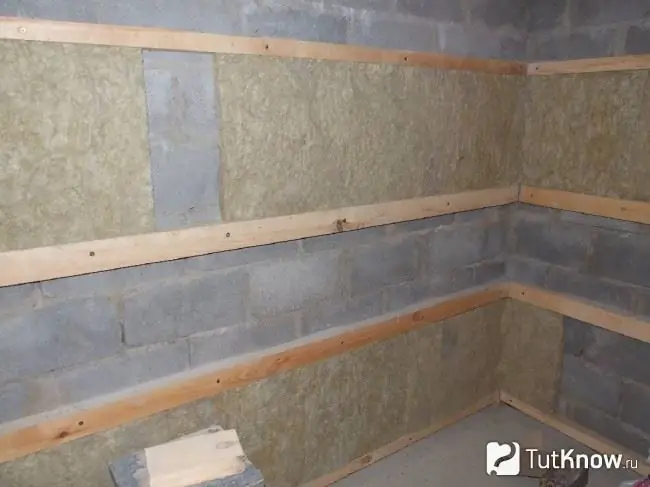
An excellent material for insulation is basalt and mineral wool in the form of pressed mats. The mats are non-toxic, do not generate dust and retain heat well.
Unlike a residential building, it is better to insulate a bath from the inside. It should warm up and keep warm. When performing external insulation, walls are included in the heating zone, which are usually frozen in winter. Heating them up can take a long time. Therefore, the insulation is carried out from the inside, and the outside is finished and the building is protected from moisture and wind.
The decoration of the steam room is carried out using natural wood. She is a natural healer who contributes to the creation of a healing microclimate in the steam room. When cladding its walls or making bath furniture, hardwood is used: alder, aspen or linden. The washing department will be more efficiently tiled, and rest rooms and changing rooms - with any safe materials of your choice.
How to build a bath from expanded clay concrete blocks - watch the video:

Based on the above, we can conclude that with proper insulation of such a bath, blocks are a worthy material. They can be used to build a durable, dry and warm bath. Numerous photos of baths made of expanded clay concrete blocks and typical projects can be found on the Internet. Good luck!