Expanded clay blocks are an inexpensive and affordable building material. But its thermal insulation qualities are significantly inferior to the properties of natural wood, therefore, a bathhouse built from expanded clay concrete needs to be insulated. Content:
-
Bath insulation materials
- Basalt wool
- Glass wool
- Expanded clay
- Styrofoam
- Preparation for thermal insulation
-
External warming of a bath
- Facade
- Foundation
-
Internal insulation of the bath
- Floor
- Walls
- Ceiling and roof
Expanded clay blocks have a porous structure and consist of sintered granular clay, cement and sand. For the walls of the bath, hollow and lightweight products containing a large fraction of expanded clay are used. Thermal insulation of enclosing structures is divided into external and internal thermal insulation. All walls of the bathhouse made of expanded clay concrete blocks are subject to external insulation, and the steam room is to be insulated internally to create the effect of a "thermos" in it. In this case, various insulation materials are used, the properties of which we will consider below.
Materials for warming a bath from expanded clay concrete
Functionally, the bath is intended for taking healing procedures, so all materials used for its construction must be of high quality and environmentally friendly. This also applies to heaters, whose action is aimed at maintaining a comfortable temperature in the premises. The negative impact of samples that are not resistant to its changes and emit harmful substances is multiplied by the extreme "climatic" conditions of the bath. Such materials are prohibited for use in such structures. Today, several excellent "candidates" apply for the role of heaters for a bath made of expanded clay concrete, we will list the most popular of them.
Mineral basalt wool for thermal insulation of a bath
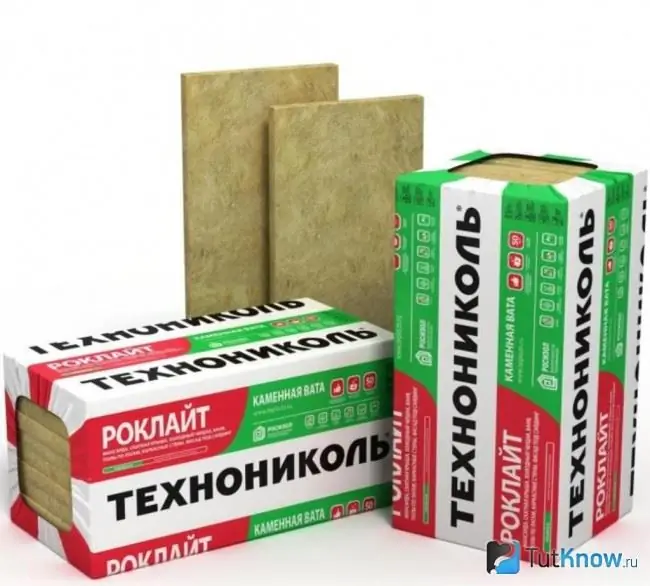
This fiber insulation is obtained by processing basalt rocks. The natural composition of the insulation guarantees its absolute harmlessness. Sometimes, some manufacturers spoil the reputation of basalt wool by adding slag impurities to it, trying to reduce the cost of their products. The insulation does not rot, it is not edible for insects and rodents. This guarantees a problem-free service of the material for at least half a century. Regardless of its fibrous structure, the material is quite strong and has a "force" index of 80 kPa. Basalt wool is a type of non-combustible material. It can easily withstand temperatures up to one thousand degrees Celsius.
This material is used for external and internal insulation of baths, as it is produced in the form of hard plates, semi-rigid mats and soft rolls with different density of their structure.
Glass wool for warming a bath from expanded clay concrete
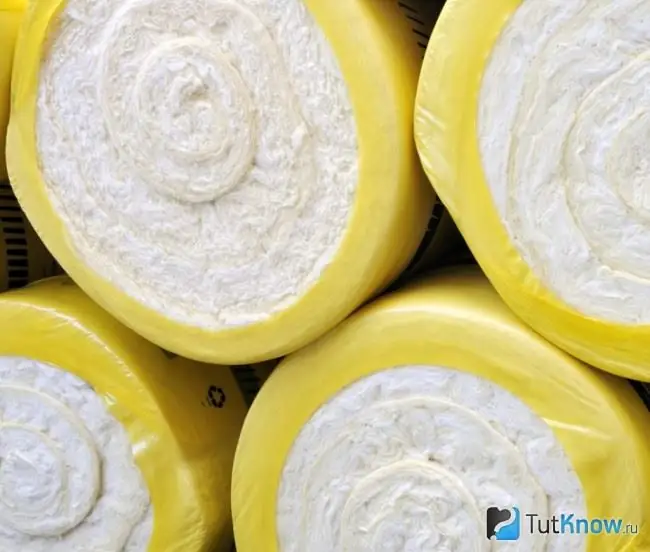
The insulation has a fibrous structure, but is inferior to basalt wool in terms of its technical characteristics. The material is made of broken glass with the addition of sand, dolomite, soda, etc. Having a coefficient of thermal conductivity of 0.052 W / K * m, it has good insulating properties, but it is completely unsuitable for internal insulation of the steam room of a bath for the only reason: glass wool does not withstand temperature conditions over +450 degrees. Therefore, it is not recommended to insulate the area that is in the immediate vicinity of the stove with it. Glass wool finds its use for thermal insulation of the attic and the roof of the bathhouse, reducing the cost of this process by 20-30% compared to the use of basalt insulation.
Expanded clay for thermal insulation of a bath
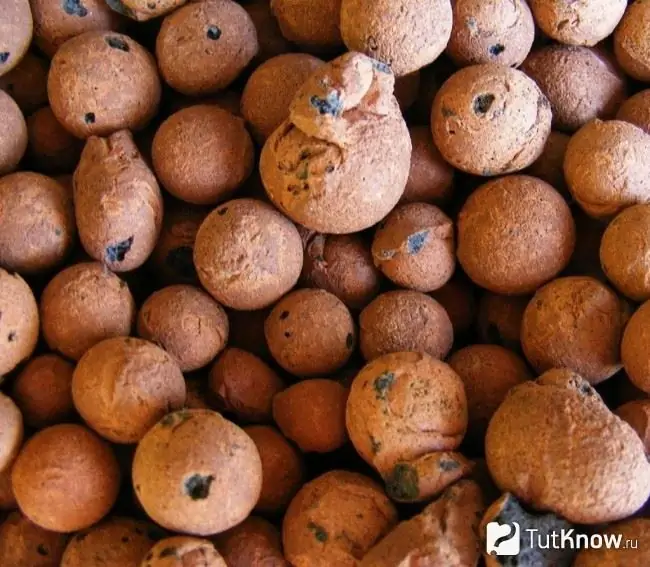
"Air" expanded clay granules are obtained by rapid firing of low-melting clay. This material is used in the form of filling the horizontal elements of the bath structure - the ceiling and floor. Various calibers of insulation in the form of gravel, crushed stone and sand are involved in the construction. The effect of warming is obtained from expanded clay when it is backfilled onto the surface with a layer of more than 25 cm.
Polyfoam for a bath from expanded clay concrete blocks
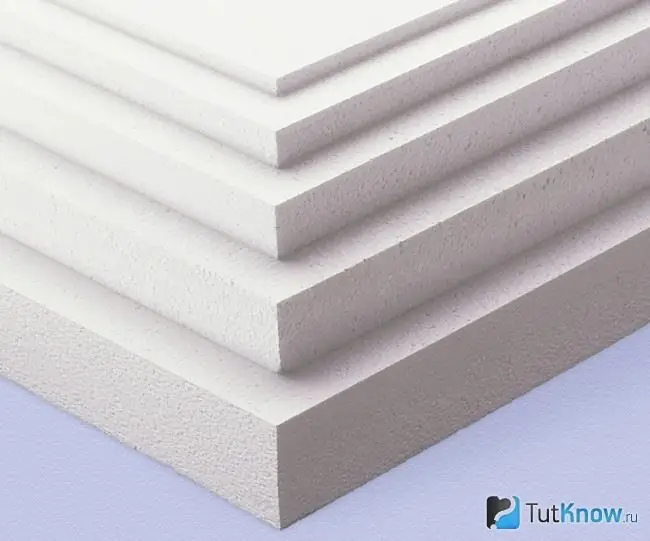
Bath insulation with this material is ideal for external wall surfaces. The facades of buildings are pasted over with foam, and then they are plastered or covered with decorative trim. It cannot be used inside the bath rooms due to the harmful fumes of phenol emitted by the foam and its flammability.
Preparation for thermal insulation of a bath from expanded clay concrete blocks
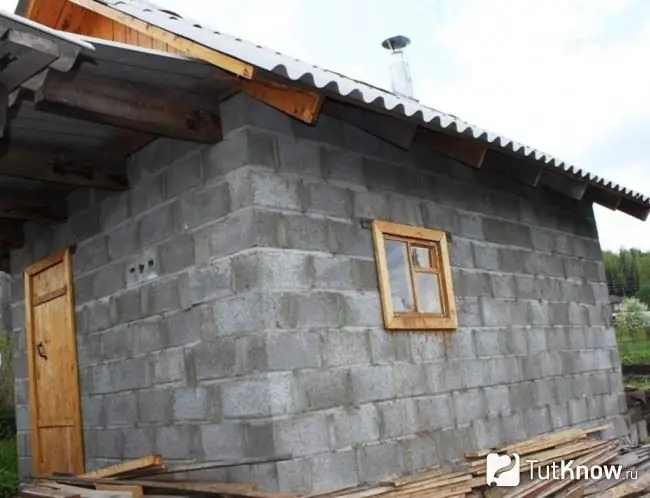
To insulate a bath from expanded clay concrete blocks, you will need tools and a set of materials: a building tape measure, a knife and scissors, a brush and brushes, gloves and protective goggles, buckets, a spatula, a primer, a reinforcing mesh, insulation, an adhesive composition, a vapor barrier membrane, a waterproofing film, fasteners.
Preparatory work on the bath's insulation consists in cleaning the insulated surfaces from extraneous influxes and bumps, oily liquids, dust and dirt. Walls made of expanded clay concrete blocks are plastered to seal all cracks and level the surfaces. On a flat surface, the insulation is fixed more reliably, especially since the process is carried out using glue. Dry the walls before installing the thermal insulation.
At this stage, the amount of materials required is calculated based on the total surface area, and the budget for their purchase.
External insulation of a bath from expanded clay concrete
External insulation of a bath building means options for thermal insulation of walls and foundations. Let's consider this issue in more detail.
Thermal insulation of the facade of the bath made of expanded clay concrete blocks
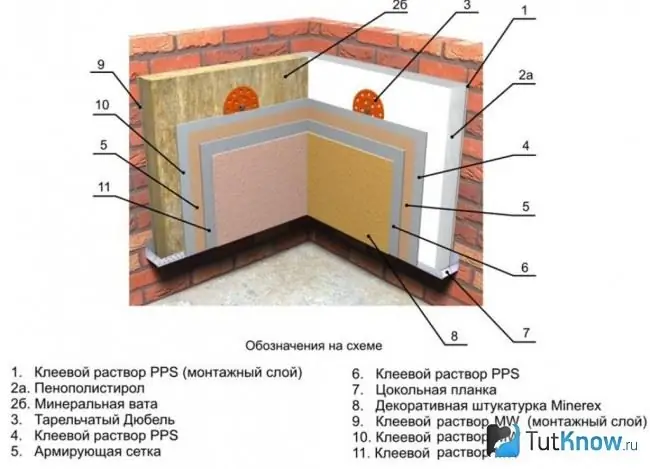
High-quality insulation of the bath from expanded clay concrete blocks from the outside is made by facing masonry with the placement of insulation between the bricks and the main wall. This is an expensive option for insulation and, despite its effectiveness, is not often used. The problem is the high price of facing bricks and the difficulty of laying them. Not everyone is able to perform it efficiently, and the work of bricklayers is expensive. Consider other options that are suitable for self-execution.
The second method involves external wall cladding made of expanded clay concrete blocks with PVC panels or siding, under which insulation is placed. As an acceptable option, as a heat insulator, foam sheets of 50 mm so can be attached to the walls in two rows in a checkerboard pattern with overlapping seams. The panels are fixed on pre-installed vertical guides. Instead of foam, you can use basalt insulation, covered with a vapor barrier material to protect it from moisture.
Another option for insulating the walls from the outside is the lining of the bath with plate heat-insulating material, for example, foam. It is attached to the wall with glue and plastic dowels. A reinforcing mesh is glued to the foam, which is covered with decorative plaster.
Insulation of the basement of a bath from expanded clay concrete
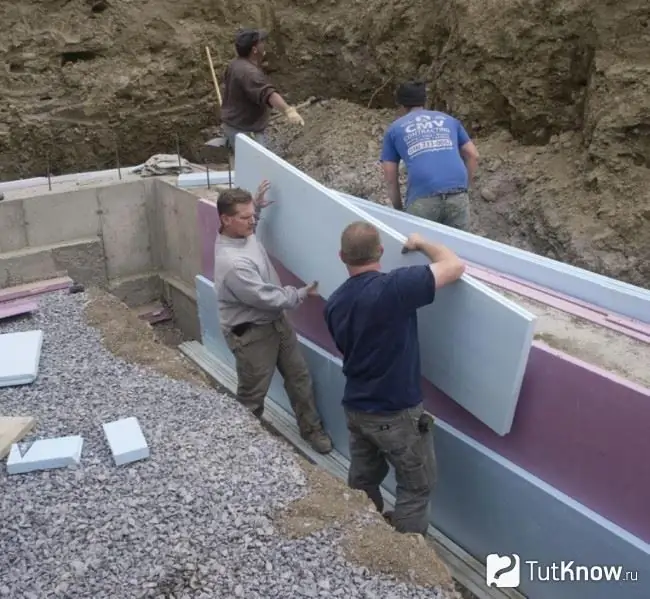
For thermal insulation of the basement of the bath, those materials are used that are moisture resistant, inedible for rodents and are not afraid of temperature fluctuations. The ideal and most popular option is foam. After the concrete has polymerized, the outer side of the foundation is covered with waterproofing and pasted over with heat insulator plates. They are staggered on the surface of the base in two layers of 50 mm each. Then the insulation can be covered with "warm" plaster.
Internal insulation of a bath from expanded clay concrete blocks
Thermal insulation of the floor, walls and ceilings belongs to the complex of works on warming a bath from expanded clay concrete blocks from the inside. Each of these designs deserves special attention.
Thermal insulation of the floor in the expanded clay concrete bath
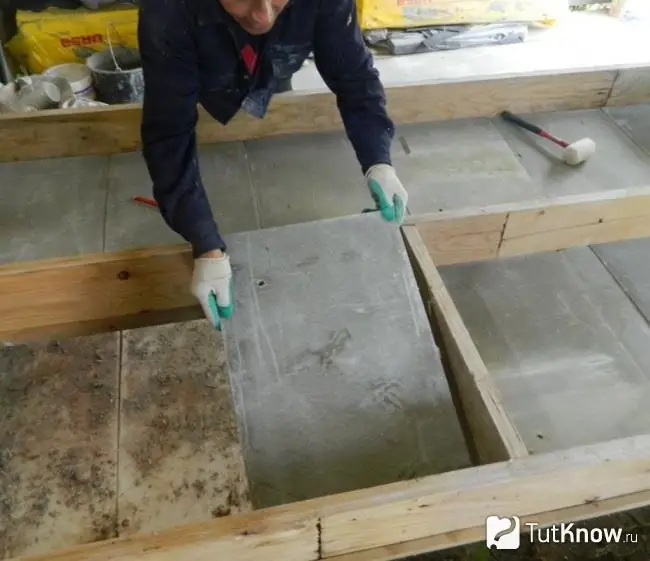
The principle of thermal insulation is the same - laying the insulation between rigid layers with its protection with insulating membranes. In a wooden structure, a heat insulator is located between the rough and clean floor, and in a concrete one - between the base and the outer layer of cement mortar.
The wooden floor is insulated in the following sequence:
- On both sides of the lower edge of the beams, cranial bars are stuffed along their entire length, which are necessary for the construction of the subfloor.
- Low grade boards, pre-cut to a size slightly smaller than the pitch of the beams, are placed on the cranial beam.
- The subfloor is ready. Then it is covered with waterproofing. For her, it is better to choose a membrane with vapor barrier properties. It is spread covering all beams and covering along the perimeter of the lower parts of the walls with a start of 20 cm. The material is fastened to the structural elements with a stapler, the joints of the sheets are glued with tape.
- Insulation is laid on the vapor barrier layer, which is covered with a layer of waterproofing material. An expensive membrane can be replaced with a layer of roofing material with neatly glued seams. The free space around the floor drain pipe is filled with polyurethane foam.
- At the end of the warming process, boards of a clean floor are laid, excess insulation is cut off, the baseboards are screwed on.
There should be a ventilation air gap of 3-4 cm under the finished floor to dry the structure. The concrete floor is insulated as follows:
- Waterproofing is laid on the lower floor slabs or the concrete cushion of the subfloor. It can be coated in 3 layers, rolled or combined from the first two options.
- It contains foam plates, expanded clay or mineral wool. The thickness of the layer is determined by the thermal properties of the selected insulation.
- A reinforcing mesh is placed over the insulation with a gap maintained using plastic supports. A concrete screed is poured over it. It can be tiled or used as a base for a wooden floor.
Thermal insulation of the walls of the bath from expanded clay concrete blocks
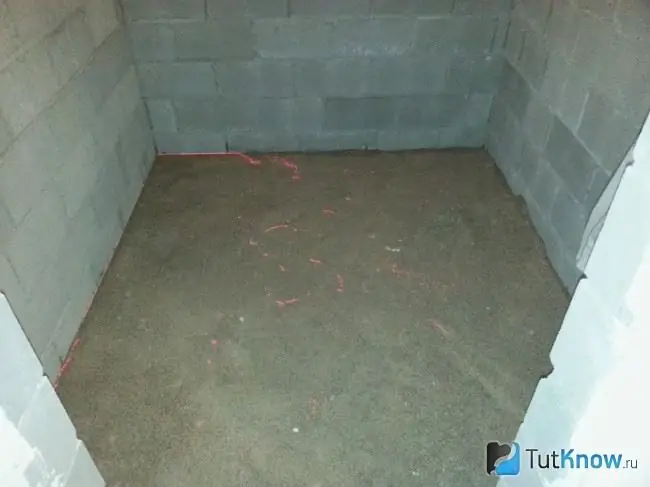
Before proceeding with the insulation of the walls of the bath from expanded clay concrete blocks, it is necessary to prepare their surface. For this, the enclosing structures are cleaned and plastered until smooth.
Further work goes in this order:
- Using the building level, a wooden lathing from a bar is installed on the walls on the pre-laid waterproofing.
- The distance between its vertical elements should be 2-3 cm less than the width of the insulation plates. This will allow the insulation to fit snugly against the batten and hold onto it by itself.
- The frame cells are filled with basalt wool slabs.
- A vapor barrier layer of a foil membrane made from kraft paper is laid on top of the insulation. Its reflective side should be directed towards the interior of the steam room. The membrane sheets are overlapped by 15 cm, the joints between them are glued with metallized tape. It is fastened to the crate with a stapler.
- Then, in the direction transverse from the timber, a counter-lattice is attached over the vapor barrier layer. It is necessary to install the outer wall cladding and create a ventilation air gap under it, which will provide the foil with a heat-reflecting effect and the removal of condensate from its surface.
- At the final stage of insulation, the outer cladding is performed. In the steam room, natural wood serves as the material for it.
Thermal insulation of the ceiling and roof of the bath made of expanded clay concrete
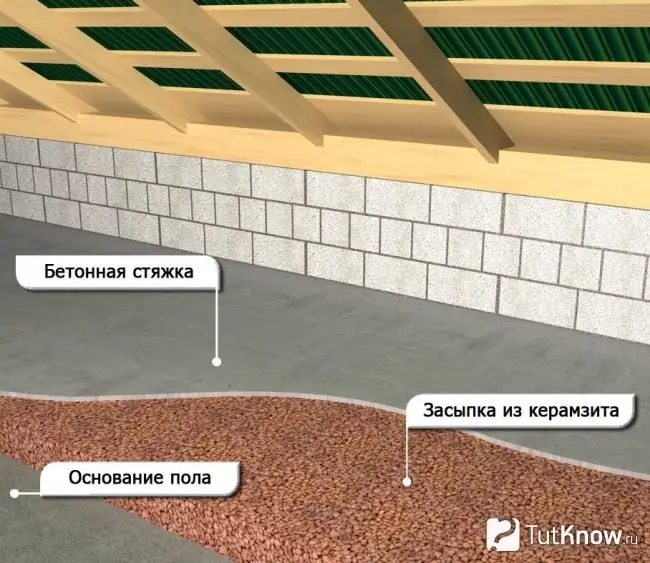
Compared with the thermal insulation of other structures of the building, the insulation of the ceiling of the bath made of expanded clay concrete blocks is of paramount importance. It operates under extreme conditions at the border of high and low temperatures. In order not to heat the air around the bath, but to keep the precious heat in the steam room, the ceiling is insulated in two ways - closed and open.
An open version of insulation is used for baths in which the attic space does not have a floor. The wooden ceiling sheathing is covered with a waterproofing foil membrane and covered with a granular heat insulator with a layer of more than 25 cm.
Another open method of waterproofing the ceiling has been used for a long time, but it is still relevant to this day. It consists in using a layer of oily clay 3-4 cm thick instead of a membrane with the addition of sawdust, after drying it is covered with oak leaves and dry soil. The method is very effective and has proven itself in work. Its only drawback is an increase in the weight of the floor - an additional calculation of the cross-section of the ceiling beams is required. However, expanded clay is more often used for backfilling. On top of the insulation, another waterproofing layer of roofing material or polyethylene film is covered, their attachment to the beams is performed using a stapler.
The closed method provides for a device on top of the thermal insulation of a flooring made of boards, which makes it possible to use the attic for household purposes. The flooring is nailed to the joists. The insulating cushion under it consists of three layers in series: a vapor barrier made of foil-clad material, an insulation made of mineral basalt wool and waterproofing made of roofing material.
The standard rules for constructing a warm roof for a residential building are also applicable to bath buildings. The choice of materials for its insulation depends on the functionality of the attic. Mineral wool as an absolutely clean environmentally friendly heat insulator is used to insulate recreation rooms or billiard rooms. Glass wool can be used to insulate storage facilities, saving 20-30%.
How to insulate a claydite concrete bath - watch the video:

Brick and stone are “cold” materials. Therefore, the better you insulate the bath from expanded clay concrete blocks, the lower heat losses can be expected in its premises. With proper organization of work and adherence to technology, you can build a durable, dry and warm "health resort" with your own hands.