What is wall insulation with expanded clay screening and its features, how to choose the right material, preparation for work, a step-by-step masonry algorithm, features of finishing. Insulation with expanded clay is an effective way to preserve heat in a building, the loss of which through its walls can reach 30%. This method not only makes it possible to create a comfortable atmosphere, but also saves on heating costs.
Features of thermal insulation of walls with expanded clay
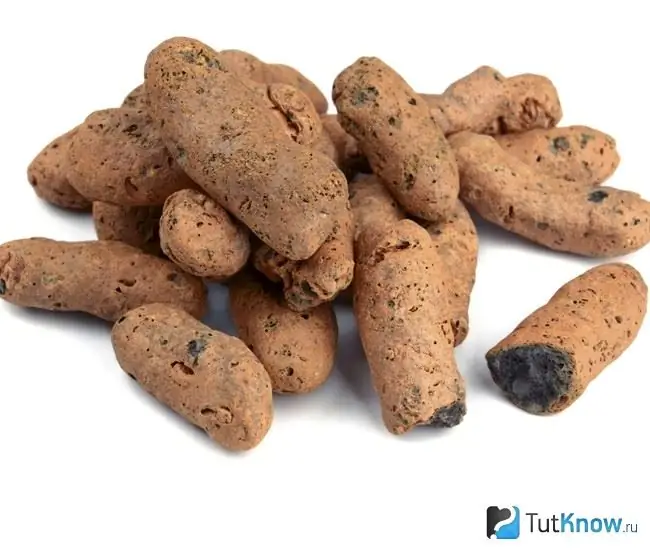
The owner may face a dilemma: do external insulation or give preference to internal thermal insulation with expanded clay. Experts recommend more often outdoor work, since it provides a higher level of heat preservation in the structure.
You can add to this savings of up to 60% of the cost of insulation. As a result of external thermal insulation, the building facade receives an additional margin of safety. Also, the level of moisture and condensation is reduced, and sound insulation characteristics are improved.
As for the internal insulation, it makes it possible to carry out work in any weather and in any season, since thermal insulation will occur within the premises. On the other hand, there is an obvious drawback - with this method, you can significantly reduce the useful internal area in the room. Often, the insulation of the walls of houses with expanded clay or other heat insulator leads to the problem of the appearance of fungus inside the insulation structure itself.
The most effective is the three-layer type structure with the use of expanded clay. The load-bearing wall of the building acts as the first outer layer; expanded clay with cement mortar is in the middle. After it is laid inside, the cement hardens, as a result of which the granules are firmly connected to each other. The last layer is a finishing (facing) brick, which will protect the insulator from the hostile environment.
The choice of expanded clay for wall insulation
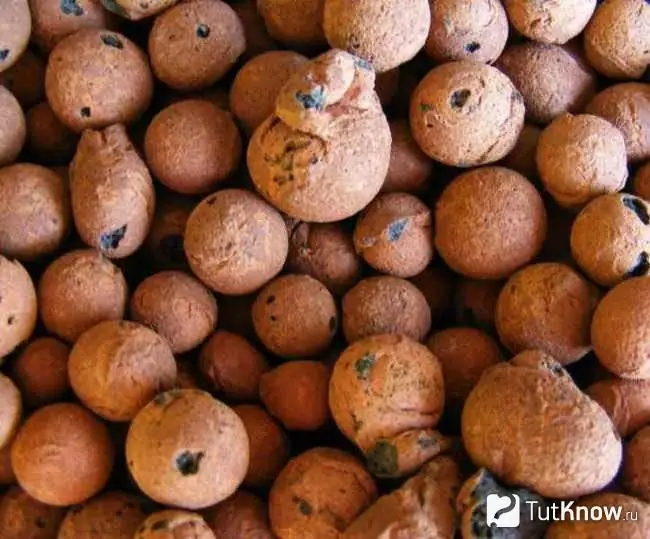
The material is classified depending on the weight and appearance of the granules, as well as the degree of strength. Fractions of this insulation can be of various sizes, namely 5x10 mm, 10x20 mm and 20x40 mm. There is another classification: expanded clay is divided into 10 grades, the smallest of which is 25, and the largest is 800. This number indicates how many kilograms of material were consumed per 1 cubic meter.
Its strength requirements are set for each grade, based on its bulk density. The area of application of the material depends on this indicator, while taking into account the load on the structure as a whole.
The main types of expanded clay in terms of structure and size:
- Granular gravel with dimensions 5-40 mm;
- Crushed stone obtained on the basis of coarse gravel by crushing it;
- Fine-grained sand is not larger than 0.5 cm.
It is expanded clay sand that is widely used in the production of dry mixes - walls, foundations, and ceilings are thermally insulated with it. Adding such material allows you to save up to 60-70% on heating costs. Gravel or crushed stone is most often used as thermal insulation for roofs, attics, floors, ceilings.
Expanded clay granules create a backfill for engineering communications, for example, pipelines. To fill the empty cavities, they are mixed with foam crumbs. The result is an effective version of insulation that protects communications from freezing and failure.
It is most convenient to use packaged expanded clay, which is scattered in packages. It is easy to store and deliver it to the facility where the walls are insulated with expanded clay. But bulk material is cheaper.
Wall insulation technology with expanded clay
For the construction of a strong heat-insulating structure, it is best to purchase expanded clay mixture, consisting of grains of different sizes - from small to medium and large. This mixing results in an insulation with good adhesive properties.
Preparatory work before insulating walls with expanded clay
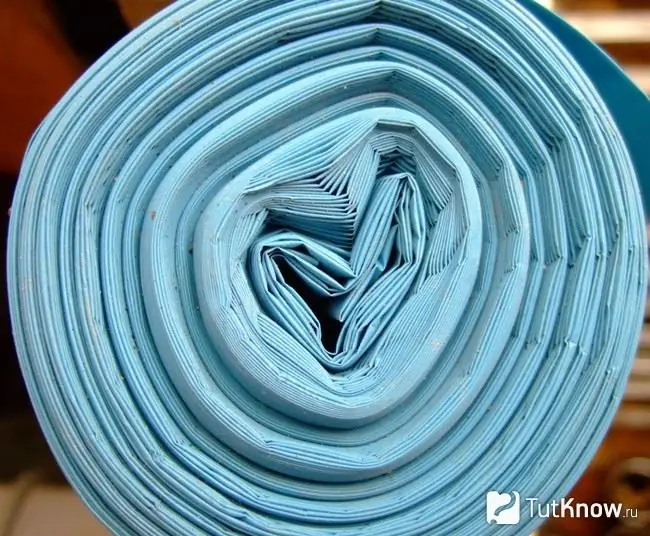
It should be borne in mind that before installing the insulation, it is mandatory to install waterproofing, which will protect expanded clay from moisture entering it. Even ordinary plastic wrap can be used as a waterproofing material. It should be laid so that a solid and sealed panel is formed. It is possible that at the edges it goes to the ceiling and floor, and the joints are glued with construction tape.
The easiest way is to equip the newly erected walls of the building with expanded clay. In this case, you can resort to the three-layer masonry method, in which each layer has its own purpose and characteristics. As part of the bearing layer there will be blocks of expanded clay concrete, the thickness of which is from 20 to 40 cm. A mixture of granulated expanded clay and cement milk can act as the main layer. The third layer is protection, which can be wood, brick or panel boards.
Before laying the heat insulator, it is advisable to pour over the expanded clay layer with cement milk. This will lead to a faster setting of individual fractions and, as a result, solidification of the entire layer. Of the tools we need: a bricklayer's trowel, a mortar spatula, a hammer, a jointing, a chisel, levels and plumb lines, a measuring tape, as a rule, containers for mixing solutions, a pickax or ledge. From materials: washed sand, cement, expanded clay screening, reinforcing mesh.
Installation instructions for expanded clay
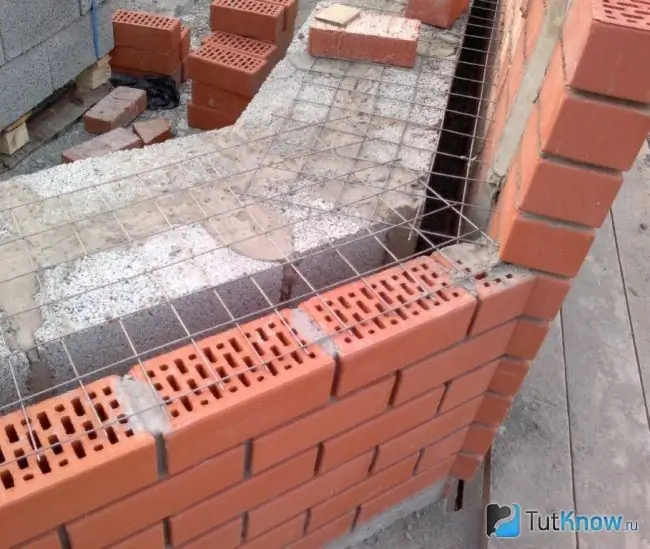
If you have decided on the method of laying the heat insulator, then you need to estimate the thickness of the future backfill. Experts recommend making a certain margin in order to increase the sound and heat insulation characteristics of the wall. It is advisable to make a layer of cement and expanded clay granules of at least 10 cm.
Most often, especially in private construction, well masonry is used with an insulating layer in the middle. It allows you to make the walls not so thick, but at the same time guarantees excellent thermal conductivity. This method leads to less consumption of building materials. However, it is necessary to make calculations and arrangement of vertical and horizontal diaphragms in advance. Since the inner surface of the finished well can become a place for the accumulation of condensate, it should be covered with a vapor barrier material. The width of the well itself can vary from? to a whole brick. Insulation of walls with expanded clay means that the thickness of the entire wall assembly is from 30 to 60 cm.
Anyone can master such a masonry, but it requires adherence to the procedure and correct calculations. Masonry is made with simultaneous insulation according to the following step-by-step algorithm:
- First, a base is made from the two lower rows of bricks. They are laid on the horizontal waterproofing, which is already on the plinth of the foundation.
- On the base, the installation of external parallel walls and partitions that connect them (called diaphragms) continues. The vertical distance between brick partitions depends on the selected size of the well.
- After laying 5-6 rows from the beginning of the base, the well can be covered with insulation. It is carefully tamped and poured over a cement-based solution. At the same time, expanded clay gravel must be unequivocally dry, and it must be poured into the well in layers.
- In order to provide protection for the expanded clay insulation from below, polystyrene sheets with any waterproofing are installed. So it will be possible to avoid the suction of moisture from the surface of the earth.
- As soon as the insulator is filled up, rammed and filled with mortar, a concrete screed is installed around the perimeter. Due to the adhesion of bricks from the outer and inner rows, it will provide the rigidity of the wall structure.
- The next step is the arrangement of horizontal diaphragms, the thickness of which directly affects the thermal insulation of the entire wall. A reinforcing mesh can be placed under them to ensure the reinforced strength of the entire wall structure. Horizontal diaphragms also protect expanded clay insulation from shrinkage, because they divide its mass into several levels.
- Then the laying continues in the specified sequence until the entire wall is made.
Finishing of insulated walls
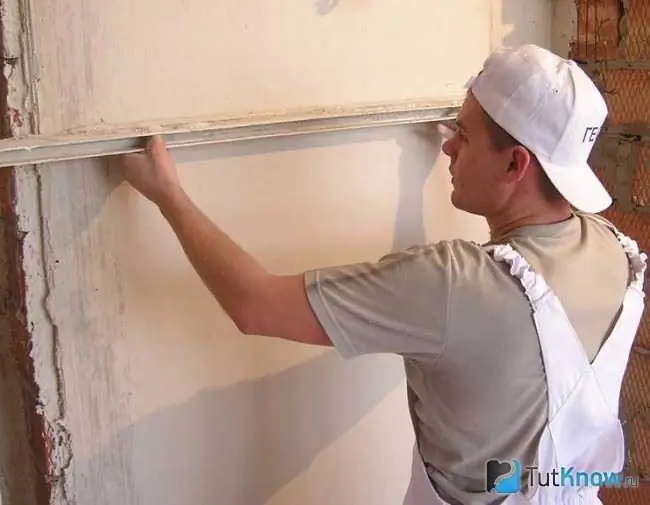
Drying of the wall insulated with expanded clay occurs in a few days. But the final strength will be reached in about a month. After the actual insulation of the walls of the house with expanded clay is completed, they begin finishing and facing work. Decorative brick or wood can act as the main material that will protect the insulation from adverse atmospheric phenomena.
But first it is necessary to plaster the wall, both from the outside and from the inside. This will provide additional vapor barrier for moisture that tends to escape from the room to the outside. As for the external plaster, it will protect not only the wall, but also the insulation behind it from precipitation. The plaster will give the whole structure even more rigidity. To prepare the solution, it is necessary to mix 4 parts of river sand and 1 part of cement, for example, M400.
Decorative stone is a good solution for finishing a heat-insulated wall. It can be applied not only outside the building, but also inside. It perfectly changes the interior without putting too much pressure on the structure. When choosing this material, you must pay attention to the fact that it does not contain traces of visible spots or build-ups. It is advisable, after drying, to cover such a surface with a water-repellent compound.
How to insulate walls with expanded clay - watch the video:

Despite the relatively low cost, the popular expanded clay insulation is able to make the walls in the house sound and warm. The main thing is to control the load on the foundation and the structural features of the foundation. For the rest, it can be unequivocally summarized that expanded clay warming is not for nothing considered a common and profitable option for thermal insulation.