Advantages and disadvantages of waterproofing surfaces by spraying polyurea, the choice of installations for applying the material, the technology of work. Waterproofing by spraying polyurea is the formation of a monolithic thick-walled film coating on the surface, characterized by high strength and elasticity. The protective shell is formed by the reaction of two components - isocyanate and resin. In our article, we will consider the intricacies of handling these components and the technology of spraying the composition onto the base in order to protect it from moisture.
Features of the use of polyurea for waterproofing

The polyurea coating is formed by the reaction of two components, which are applied to the surface under high pressure. After application, the substance quickly hardens to form a seamless web.
Two types of polyurea are used for waterproofing - pure and hybrid. The first option is used in harsh operating conditions, for example, at low temperatures, but its price is very high. In most cases, a hybrid version is used.
Manufacturers introduce additives into the substance, thanks to which the product, in addition to waterproofing, acquires other properties. A wide range of products allows you to choose a product for each specific case. For example:
- The reflective cover is mounted on the roof, which saves on insulation costs.
- Compositions intended for floors and foundations are flexible and withstand mechanical stress well.
- For floors, you can choose polyurea for smooth and rough surfaces.
- The product has proven itself well for waterproofing steel pipes.
- The application of polyurea to the facade not only increases its moisture resistance, but also increases its service life.
- Samples of any color can be purchased and the interior surfaces of swimming pools or aquariums are available.
Additives slightly impair the properties of the material, but hybrid formulations cost less than pure polyurea. The insulator application technology depends on its components, so check the requirements of the substance manufacturer in advance.
A feature of the insulator is a high curing rate, which eliminates the influence of various negative factors on the quality of the coating. Thus, the surface can be processed at low temperatures. The substance is capable of waterproofing the base under conditions in which other protection options do not work.
It is necessary to work with the product in special suits that cover the skin, eyes and respiratory organs.
Advantages and disadvantages of polyurea waterproofing
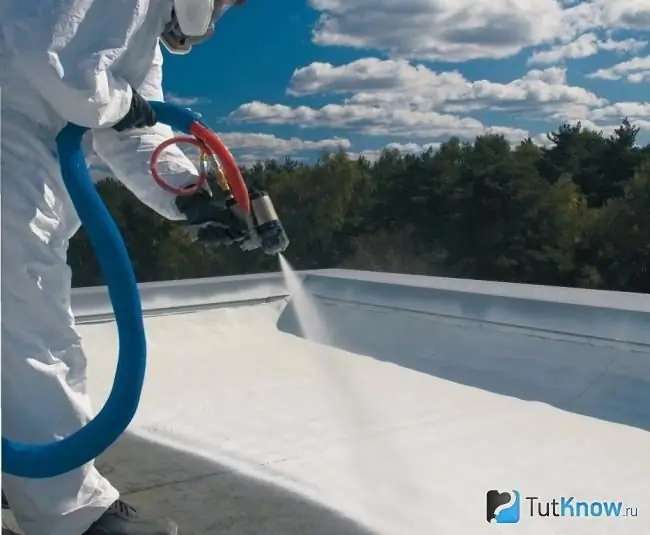
The coating of this material has many positive qualities that distinguish it from other water repellents.
Polyurea Benefits:
- Polyurea does not require repair or replacement for 50 years. After long-term use, it does not deform from mechanical, thermal and chemical influences, does not lose its performance characteristics, does not shrink or crack. The wear resistance even surpasses the standards for ceramic tiles. If necessary, the surface of the film can be easily repaired.
- Spraying technology creates a seamless waterproof shell of high reliability.
- The product is safe for humans, because it contains no toxic components.
- The process of forming a polyurea-based coating is very simple. During work, there is no need to adjust the materials, fix them, seal the joints.
- Spraying is carried out using special devices that allow you to process an area of 300-400 m in a short time2.
- The urea-based casing does not burn and can be used in fire-hazardous premises.
- The solidification rate of the substance is very high - no more than 20 seconds. It is possible to start operation one hour after application, but the coating acquires maximum strength later.
- Polyurea seals surfaces of any shape. It has good adhesion to almost all materials used in construction.
Even such a modern waterproofing agent has disadvantages that limit its use:
- Some varieties of polyurea are not sufficiently resistant to ultraviolet light, so carefully study the composition and properties of the components before buying.
- The raw materials for spraying a substance are expensive.
- For work, you will need expensive equipment, without which it is impossible to apply the substance. Only specialists with special training can work on professional devices.
- The tool will reliably protect any surface from water, but it cannot hide its imperfections.
Polyurea surface waterproofing technology
Waterproofing is carried out in several stages. First, you need to carefully prepare the base for processing, decide on the type of equipment for polyurea, and only then start the spraying process. Information about each step is given below.
Selection of equipment for spraying polyurea
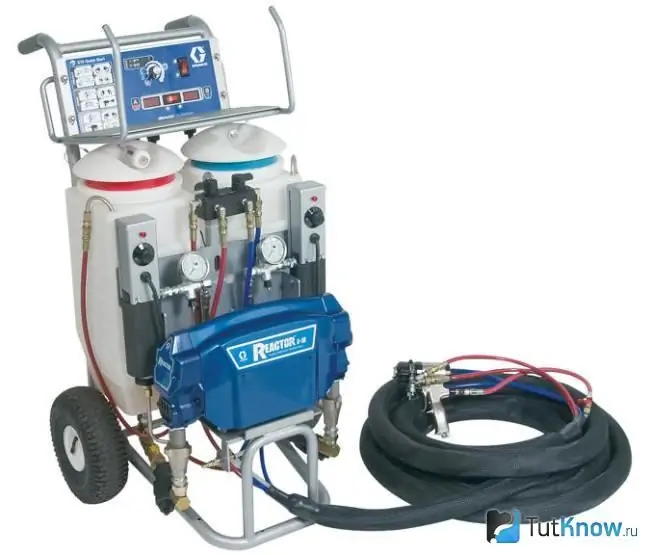
The insulator is applied to the walls by spraying using special devices that are selected depending on the area of the surface to be treated, the desired quality of the coating, the operating conditions of the protective shell and other factors. To obtain a working composition, the components are mixed at a temperature of 60-80 degrees in a 1: 1 ratio, under a pressure of 150-200 atmospheres. Therefore, the device must include such units as containers with chemicals, pumps, a dispenser, a mixture heater, special hoses for supplying a substance that maintain a given temperature, and a sprayer.
Light to medium duty multipurpose attachments are not suitable for the application of polyurea. They are not designed for high system pressures. Each modification of the substance requires a certain type of gun, its own mixing chamber size, pressure, temperature. All recommendations for the selection of equipment are given in the instructions for the composition developed by the manufacturer of the substance.
With a small amount of work, mobile one-time installations are used, usually pneumatic. With their help, small areas are processed - balconies, basements. The simplest setup includes two cylinders of polyol and isocyanate, a long flexible twin hose, and a gun with nozzles. The devices do not always have a device for adjusting the proportion of components, there is no function for heating the contents. In such systems, the permissible temperature is maintained using barrels of warm water. With some skills, disposable devices can handle even complex surfaces with high quality.
The electrical devices are of medium performance and are designed to handle large areas.
Hydraulic devices are classified as professional devices. They provide excellent quality waterproofing, are designed for a long service life, and have increased reliability. Dosing of reagents is carried out using piston pumps.
For spraying polyurea, it is necessary to use a spray gun with a flat torch, while for pneumatic and hydraulic devices, sprayers of different designs.
Preparatory work
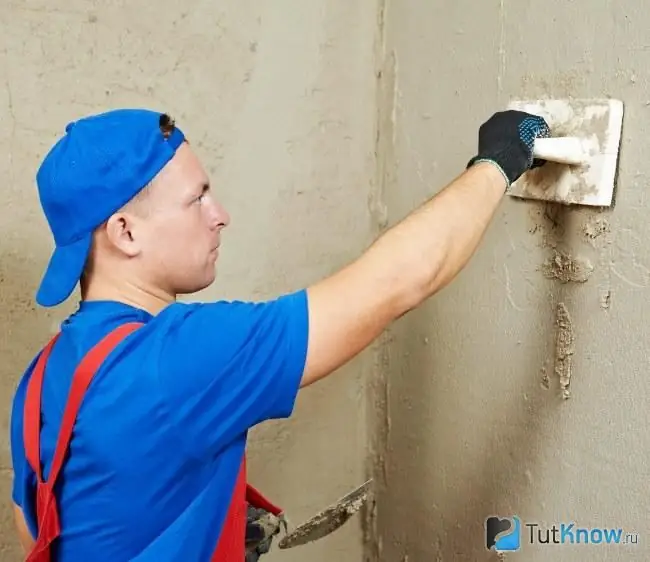
The surface should be thoroughly treated before spraying. To do this, follow these steps:
- Remove dirt using various methods - strong water jet, hard brush, grinder, etc.
- Check the flatness of the base. Irregularities do not affect the quality of waterproofing, but after the end of the work, the shell will look unaesthetic. Make sure that there are no oil stains and paint on the wall, the composition does not adhere well to them.
- To increase adhesion, the surface to be treated must be roughened. If necessary, brush over it with a stiff brush.
- Prime cementitious screeds to reduce the consumption of polyurea and increase the strength of the substrate.
- Additional treatment will prevent the plaster from peeling off. If porous materials are not primed, craters and other defects will form on the surface. It will not be possible to disguise them even by repeated spraying.
- Check concrete walls for weak spots. If found, cut them out, and fill the resulting voids with repair compounds. Fill the holes from the fasteners with expanding compounds to a depth of 4-6 cm.
- Round off sharp corners, knock down the concretions of concrete. Fill sinks with a diameter of more than 10 mm. In the places where the horizontal and vertical sections meet, make fillets.
- If polyurea, in addition to waterproofing, is planned to be used for decoration, the surface requirements increase. It is necessary to ensure that the walls to be treated are horizontal or vertical with a tolerance of 1 mm per 1 m. The number of nicks with a diameter of 1-2 mm per 1 m2 should not exceed two.
- Brick partitions must be plastered with a cement-sand mixture. Polyurea can be applied after a month so that the cladding acquires maximum strength.
- After leveling the surface, it must be primed with a special compound designed for working with polyurea. It is advisable to use the formulations recommended by the manufacturer of the waterproofer.
- On metal products, sand the welds and sandblast the rest. After the procedure, rinse and dry the surface. Metal surfaces are not primed, only covered with an anti-corrosion compound.
Polyurea is allowed to be sprayed if the following requirements are met:
- The moisture level of the surface does not exceed 4%. The value is determined by a special device - a moisture meter. In its absence, you can use the folk method. Place a large piece of plastic wrap on top of the base and tape. Check her condition in three days. If wet spots appear, the wall should still dry. It should be remembered that the polyurea coating forms even if the material is sprayed onto ice, but the casing will not stick to the surface.
- The admissible air humidity is less than 80%.
- The ambient temperature must correspond to the conditions specified by the raw material manufacturer.
Polyurea Application Instructions
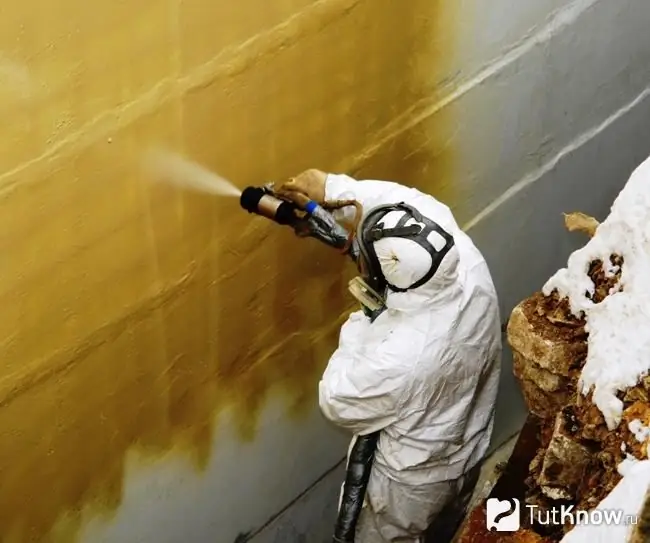
Surface waterproofing is carried out after the primer has completely dried. Assembling the product is very simple and takes only a few minutes.
Working with disposable installations does not require special skills, but before that it will not hurt to simulate spraying with the gun turned off. Practice grabbing the pistol and moving around with it. You cannot release the trigger, the composition will instantly solidify in the nozzle, and it will have to be changed. Professional installations have a complex design and before use, it is necessary to undergo special training in the maintenance of the device.
The classic spraying process of polyurea is as follows:
- Assemble the device according to the manufacturer's instructions.
- Connect the containers with hardener and resin to the heater using hoses.
- Turn on the pump to supply the compounds to the heater and vice versa. The process stops when the entire volume of reagents is not heated to a temperature of 60-80 degrees.
- After the components have been liquefied, the device redirects the materials for spraying. The same pumps pump the substance to the nozzles through special heated hoses. Each component exits from separate holes in the gun and mixes upon application. The polymerization process begins immediately, and after a short period of time the substance solidifies, forming a film coating.
- In some systems, mixing takes place in a special chamber built into the gun. To obtain a high-quality mixture, the pressure in it, as well as at the outlet from the nozzle, must be high enough.
- Spraying is carried out in strips 1, 5-2 m wide with an overlap of 15-20 cm on adjacent areas. Treat the surfaces twice: first in one direction, and then perpendicular to the first layer. The thickness of the applied layer is 1-3 mm, the standard value is 2 mm. After 10-12 hours, the strength of the polyurea will reach its maximum.
- In some cases, the coating is applied with two compounds, for example, when waterproofing swimming pools. The top ball with the addition of dye replaces the decorative layer.
Useful tips when working with polyurea:
- Keep the heated hose away from moisture to avoid electric shock.
- Do not allow water to enter the hardener. If this happens, the substance will instantly foam and solidify. Therefore, the spraying device must have a moisture filter.
- When waterproofing critical places, fiberglass is necessarily embedded in the protective shell. It protects surfaces from high mechanical and thermal stress.
- After work, wash the sprayer from the solution.
- It takes 3 people to work. One directly sprays, the second helps to move heavy hoses, the third controls the operation of the device.
How to apply polyurea - watch the video:

Waterproofing by spraying polyurea requires a serious investment and not all consumers can afford it. But the financial costs pay off over time due to the long service life and the unique properties of the protective shell.