The use of liquid glass for waterproofing floors, its features, advantages and disadvantages, surface preparation and the technology of applying a silicate solution to it. In addition to an impressive list of advantages, waterproofing the floor with liquid glass has some disadvantages:
- The alkaline environment of liquid glass requires protective equipment when working with it: special glasses and rubber gloves.
- Due to the short setting period of the material in the mixture, the skill of the work performer must be sufficiently high.
- Liquid glass is not recommended for processing a brick base, it can contribute to its destruction.
- When liquid glass is applied in its pure form on the floor, it forms a completely smooth surface on which some finishing materials, for example, may not adhere well. Therefore, silicate mortar is more often used as an additive for cement mixtures or concrete.
Surface preparation for insulation
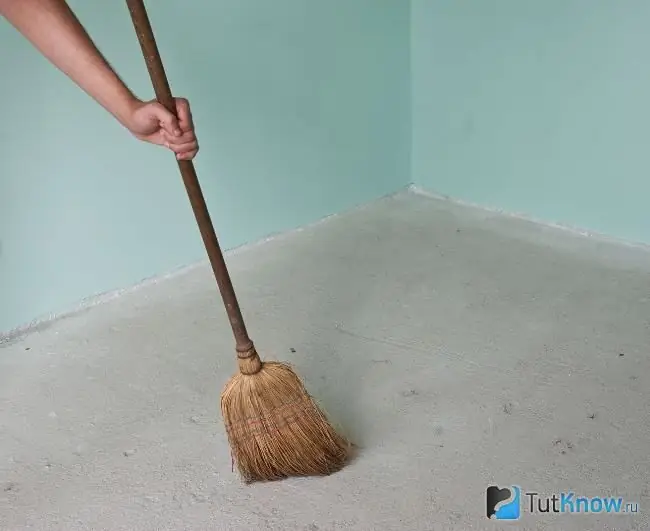
In order for the floor surface to be ready for impregnation with an insulating compound, it must be cleaned of dirt, grease stains, rust, exfoliated old screed, paint or glue. This can be done with a stiff brush, a sander with attachments and chemicals.
After cleaning, debris and dust should be removed from the floor surface. For the last operation, you can use a household or industrial vacuum cleaner. Cleaning the floor makes it possible to reveal all its hidden defects. These include cracks, chips, expanded expansion joints, and the like. In addition, thorough cleaning of the base cleans its pores, which further ensures deeper impregnation of the floor surface with a waterproofing solution of liquid glass.
Found cracks and similar damage to the base must be carefully repaired with construction cement mortar. This will reduce heat losses in the room and protect the floors below from leaks.
Further processing of the floor surface should be carried out taking into account the method of its finishing. For example, putty is applied to maximize the leveling of the surface of the structure for painting, and priming is used to ensure adhesion of the base to the material to be glued.
Instructions for applying liquid glass to the floor
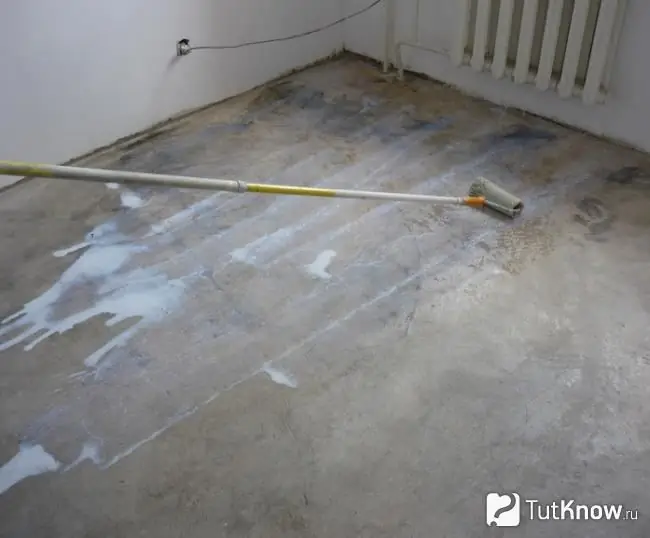
Before filling the floor with liquid glass, you need to prepare the tools and necessary materials. For a minor front of work in a domestic environment, you will need: a bucket, a drill with a mixer nozzle, a brush or paint sprayer, Portland cement, sand, water, a spatula and overalls.
The process of waterproofing a floor consists of two main stages: preparation of a silicate solution and its application to the surface.
Dilute liquid glass in water and mix it with other components in proportions that are recommended for a certain type of work. With reduced adhesion of the silicate solution to the floor surface, you can reduce the amount of water in the mixture or increase the cement content in it. Only cold water can be added to liquid glass. For its dosage, you should use measuring containers of the required volume.
To obtain a waterproof layer, it is necessary to use a mixture of components in a ratio of 1:10, that is, 10 liters of concrete or mortar should be added to one liter of liquid glass. First, cement and sand must be mixed with water, and then add liquid glass to the resulting mixture. To mix materials in a container, a drill with a mixer attachment is used.
The prepared silicate solution must be poured onto the screed in the form of equal portions in strips oriented parallel to the wall. After that, using a wide spatula, the composition should be evenly distributed over the floor plane. After leveling the mixture, the surface must be processed with a needle roller, using it to remove bubbles and small irregularities in the coating.
One layer of insulation must be done in one pass. Its thickness should be 3-5 mm. In the process of work, you need to ensure that there are no areas untreated with mortar on the floor surface. It takes a certain time for the liquid glass to penetrate into the pores and microcracks of the surface. Therefore, the second and subsequent layers of insulation should be applied at intervals of 0.5 hours.
Sometimes liquid glass is used for flooring when mixing a screed solution. In this case, the work must be done quickly, since such a mixture hardens very quickly.
Once the waterproofing coating has completely dried, it can be treated with epoxy or polyurethane varnish. At the same time, the surface will receive shine, transparency and additional strength. One day after the end of the work, it will be possible to walk on the floor.
How to cover the floor with liquid glass - watch the video:

Despite the fact that today the construction market offers more modern insulating mixtures, liquid glass is still a very popular material due to its versatility. Indeed, in addition to protecting floors, it is actively used to insulate tanks, masonry fireplaces and in many other areas of construction. The technology of using this material is not particularly complicated. The main thing in it is to adhere to the recommendations related to the safety of using liquid glass and the observance of proportions in the manufacture of silicate mixtures.