The specificity of the basement insulation with polystyrene foam, the advantages and disadvantages of this technology, surface preparation, the algorithm of the main work, finishing. Warming the basement with foam is one of the most important measures that are aimed at creating an optimal operating mode in the building. The service life of the object depends on how reliably it is protected. If the structure is not insulated, up to 10-15% of heat can be lost. Due to freezing of the basement, the costs associated with the need to improve heating, eliminate dampness and fungus will inevitably increase.
Features of the use of foam when insulating a basement
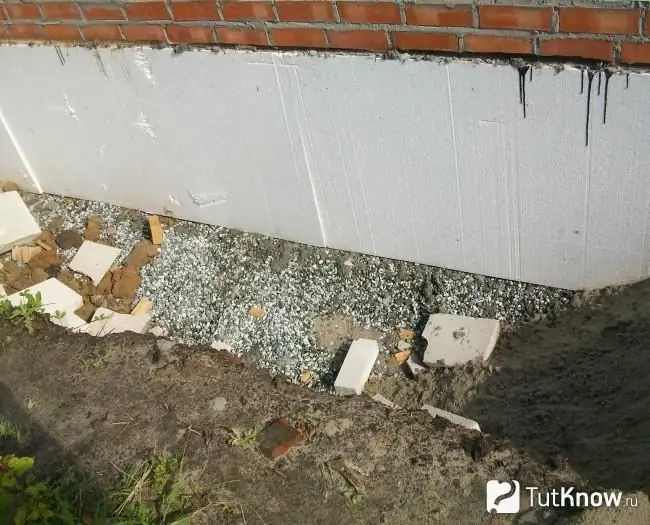
To reduce the influence of negative factors on the basement, there are a number of construction and finishing measures, including insulation of the basement with polystyrene foam. The inherent qualities of the material allow it to store heat and perform a good protective function, unlike other insulation materials. In addition, it is convenient to use, it cuts well, and the price of this insulator is much lower than others. This is how you can keep warm in the room when the temperature is below zero on the thermometer, and prevent cold air from entering the house.
Another primary factor in insulating the basement with foam is the aesthetic finished appearance of the building from the outside. Applying it, the surface becomes more convex and voluminous, which means that the architectural structure acquires its uniqueness and originality.
The technology of insulating the basement with foam plastic can be used both from the inside of the building and, if necessary, in external work. Any of these methods allows you to:
- Improve the temperature regime in the house;
- Protect the building from all kinds of moisture sources;
- Protect the bottom of the building from condensation penetration, preserving the material and extending its durability.
Insulation inside a building and outside has the same purpose. These methods differ only in the end result: when laying the foam outside, additional finishing is performed, which makes the structure even more attractive. It is also important to note that it is not worthwhile to carry out two types of insulation at the same time. But it is necessary to protect the basement even when not in use.
Advantages and disadvantages of thermal insulation of the basement with foam
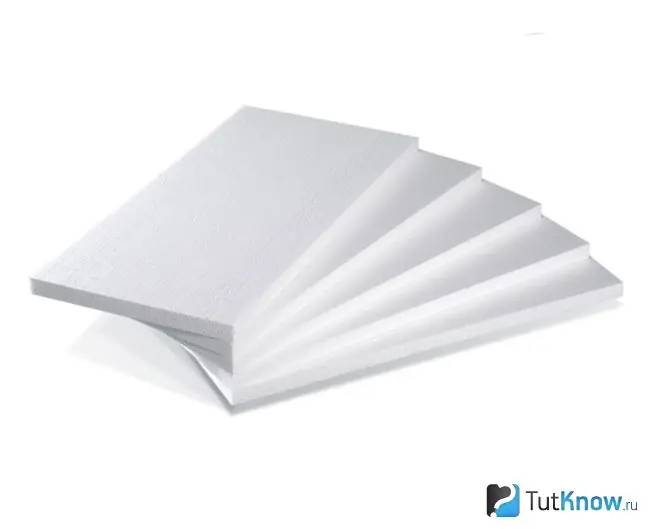
Like any other insulation material, when used for a basement, foam has strengths and weaknesses.
The advantages of such a heat insulator include:
- Low thermal conductivity;
- Ease of installation and trimming;
- Immunity of material for rodents, fungus, focus of decay and mold;
- Low cost, resulting in affordability for the consumer.
Insulation disadvantages:
- It is subject to moisture absorption. To avoid this, when laying the heat insulator, it is necessary to carry out waterproofing work using modern insulators. For these purposes, materials are used in rolls or on a bitumen-polymer basis.
- Low strength. In order to preserve the properties of the insulator for a long time, a brick wall is arranged to perform protective functions against soil pressure, or special profiled polyethylene membranes are used.
- Susceptible to mechanical damage. Therefore, the installation of a reinforced mesh is required.
Plinth insulation technology with foam
Observing the technology of using foam, all insulation work must be performed only at positive temperatures. This is one of the conditions for ensuring the high quality of the work performed. When purchasing assembly glue, you need to make sure that there are no solvents (gasoline, acetone) in its composition, which lead to the destruction of the inner surface of the material and, accordingly, the loss of its thermal insulation properties. Following these recommendations, it is possible, even without having a construction education, to insulate the basement with foam plastic with your own hands.
Preparatory work
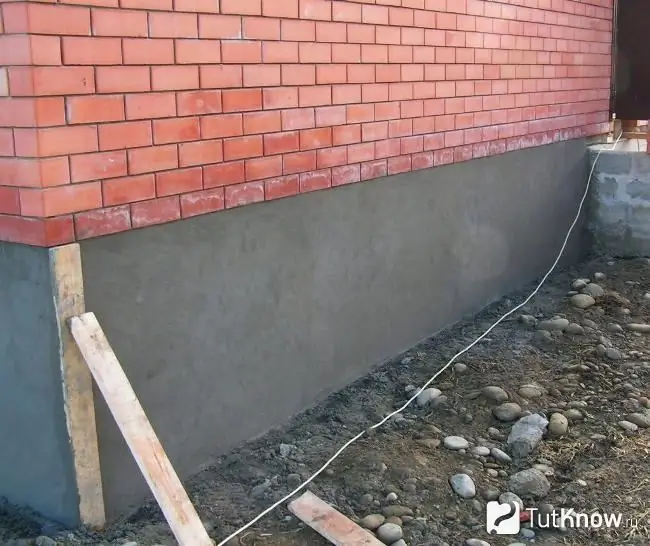
To begin with, mark the level of installation of foam plates. Usually, each house has a waterproofing layer (roofing material), which is covered with heat insulator plates 2-3 cm above the roofing material. The master applies markings on all sides of the house using a level, cord, marker. He will lay the heat insulator along this line. In addition to the indicated markings, a small groove breaks through around the house close to the wall, to a depth of 6-7 cm. The lower side of the insulator will enter into this groove.
The next stage of the process is the preparation of the base and cleaning from various contaminants. These works are performed using the simplest tools - an ordinary brush and a spatula.
Tools for mounting plates: cord, level, marker, corner for arranging slopes, knife, hammer, spatulas, puncher, brushes, rollers, working bucket.
Materials used to insulate the basement: polystyrene with a density of at least 25 kg / m3, putty, primer, assembly glue, reinforced mesh, facade paint, decorative bark beetle putty, brick, cement, sand, water.
Styrofoam installation instructions
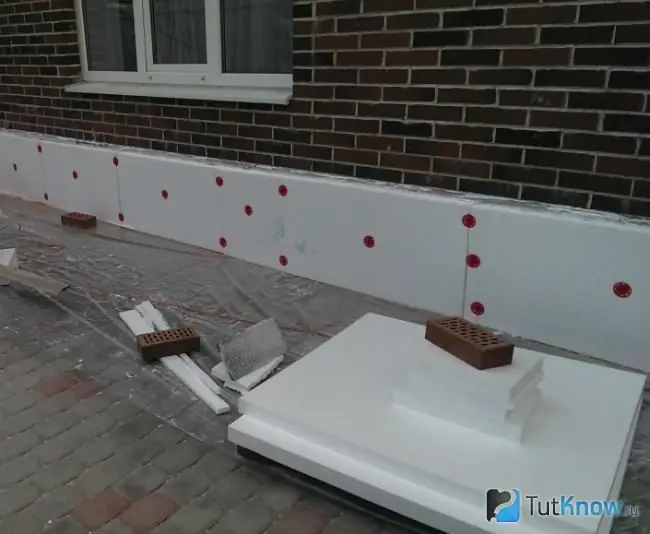
As soon as the surface is prepared, you can begin to perform thermal insulation work. To do this, follow the instructions below:
- When the debris is removed, all cracks and potholes are putty, in other words, the wall is leveled. In this case, use a special plaster for the walls. The solution is prepared according to the instructions. The prepared mixture is applied with a spatula. Next, you need to find out the curvature of the surface to be insulated. Take a level, which is set to the wall and determine the discrepancy between the upper and lower points of contact.
- It is not necessary to eliminate irregularities less than 1 cm; if large differences are detected, plaster is applied to the surface along the beacons. The next work can be done when the base is completely dry. In the event that it is not completely leveled, the procedure must be repeated when the first layer dries. In order to better bond the materials, a primer is applied to the surface with a brush.
- The next stage is attaching a reinforcing mesh to the base, it is fixed with staples using a construction stapler, or glue is applied to the surface of the mesh, and it is sunk into it. To begin with, the mesh is cut into pieces to fit the size of the base. It should be placed in such a way that about 10-12 cm remains under the insulation. After installing the insulator, it is wrapped and attached to the plate. When finishing, this fold is attached to the main reinforcement mesh.
- Next, you need to make a mixture of glue, it is best to use a special mixer or a drill with an appropriate attachment for these purposes, since it will not be possible to manually stir the solution evenly. Two spatulas are used to apply the glue: regular and notched. Conventional glue is applied to the surface of the insulation, serrated - it is leveled along the base. When the adhesive mixture is poured onto the board, the center and edges are covered with a large layer. If the surface was initially smooth, and it was not leveled, then glue can be leveled to a certain extent by filling cracks and small potholes with it.
- Along with the gluing of the plates, installation with the help of disc dowels-nails is also used. This method of fastening is used in the case of installation on a plinth of large slabs, for example, 125x60 cm or more. In this case, take dowels with thermal heads, with rods in a plastic sheath. Here the waterproofing layer can be broken when the holes are drilled for fixing the dowels. It is important to minimize these risks.
- The boards, cut to the required size, are fixed to the base with mounting glue. To ensure a high-quality connection, a wooden block is used, on which you can knock with a wooden hammer. If the layer of plates for insulation in height exceeds one row, then installation and fastening work begins from the bottom row, and in addition, from any corner of the house. In this case, they are fixed so that T-shaped joints are formed.
- After gluing every 2-3 boards, you need to seal the seams with the same glue. A similar operation should be performed on the ends. The bottom layer of the slabs must be rested on a solid base, for example, the foundation of a building, or sand and gravel backfill, which will allow the sheet not to slide off the base before the glue adheres securely.
- 1-2 days after the glue dries, each glued batch of boards is fixed with disc-shaped dowels-nails. Each sheet must be fixed with 5 dowels, in the central part and in the corners. It is recommended to make a hole in the foam sheets in advance, the dowels are buried into the material to a depth of 2 mm.
- Before reinforcing the wall, all potholes left after nailing are sealed. It is also necessary to remove all the slightest irregularities on them, using a paint float for this. A mesh fold of about 10 cm is attached to the foam with glue.
- After fixing the plates, it may be necessary to once again prime the insulated part of the structure in those places where separate small irregularities formed during the fastening of the insulation.
- After the completion of the primer, reinforcement is performed. For these purposes, you will need a special putty. The work must start from the corners of the base: the technology will be the same as when attaching the insulation. We cut the mesh to the required length. A reinforcing putty is applied to the heat insulator with a spatula, with a thickness not exceeding 2-3 mm. Press the mesh to the plate and smooth the entire surface with even up and down movements. The next sheet should overlap the previous one by about 10 cm. The mesh is covered with plaster from above. The use of fiberglass mesh allows you to make the surface even, prevents the appearance of cracks and various defects in the base. By this method, the entire base is insulated.
- After all these works, a new facing material is laid or the surface is plastered.
In order to protect the protrusions of the base from the ingress of atmospheric precipitation, it is necessary to install appropriate ebb tides. They protect the insulation from moisture penetration, protect the plates from getting wet and, accordingly, preserve the thermal insulation properties of the material.
Finish plinth
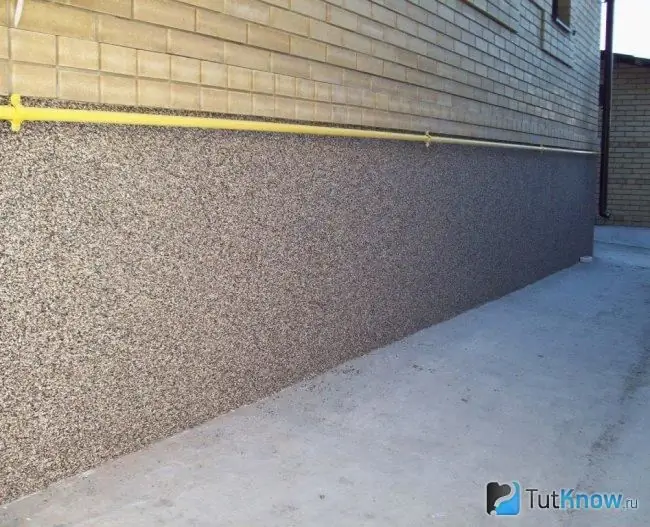
This type of treatment will give the surface a modern appearance, and will also perform protective functions, preventing the destruction of the heat-insulating layer. There are two types of finishes: decorative plaster and brick or natural stone.
Decorative plaster is used for work both inside the building and for outdoor work. The trading network offers a wide range of such materials, there are substances of various colors, as well as mixtures to be dyed. This finishing material is quite expensive, but its cost justifies itself, it serves for a long time, and the facade looks aesthetically beautiful.
The plaster is applied in the same way as the plaster for leveling the walls before strengthening the foam. Applying a level, you need to check whether the surface is flat or not. A suitable primer is applied to the foam board; a well-proven primer from the Contact-plus series can be used. When the primer is dry, decorative plaster is applied. It is applied with a metal spatula, then smoothed with a float, making circular movements or up and down movements. The final drawing on the surface depends on the actions taken. To facilitate the work, it is recommended to moisten the grater more often with water.
After the surface has dried, the float should be applied again, making great efforts. To avoid unwanted joints, it is worth plastering the entire surface at once, while trying to fill the space from corner to corner. The paint is applied to a completely dry surface, preferably it should be painted twice.
The next type of finish is brick cladding. It performs a very important function of protecting the thermal insulation layer and gives the plinth a beautiful appearance. Departing from the edge of the heat-insulating layer by 10-20 mm, a layer of brick is laid on a mortar, which consists of one part of cement, three parts of sand and water necessary to prepare a homogeneous thick mass.
After laying the first row of bricks, the next one is done with bandaging in half a brick. In addition, when they put 3-4 rows of material, nails with a diameter of 0.5 cm are attached to it directly into the heat-insulating plate. The nail is driven in so that it enters at least 2 cm, and its head with a diameter of 2-3 mm should lie on the brick. This will ensure the cohesion and solidity of the insulation and brick cladding.
How to insulate the base with foam - look at the video:

This method of insulating the basement, when foam is used as a heat insulator, is quite effective, relatively inexpensive and is currently widely popular.