Options for insulating the attic with foam or a coating based on it, the pros and cons of using the material on the upper floor, the choice of a quality product. Insulation of an attic with foam is the use of a modern sheet heat insulator to effectively protect a building from heat loss. Depending on the purpose of the technical floor, the slabs are laid on the floor or under the roof cladding. It is not recommended to carry out these works in parallel due to the cessation of the flow of warm air from the lower rooms. Below we will look at the techniques for creating insulation layers on all surfaces of the room.
Features of thermal insulation of the attic with foam
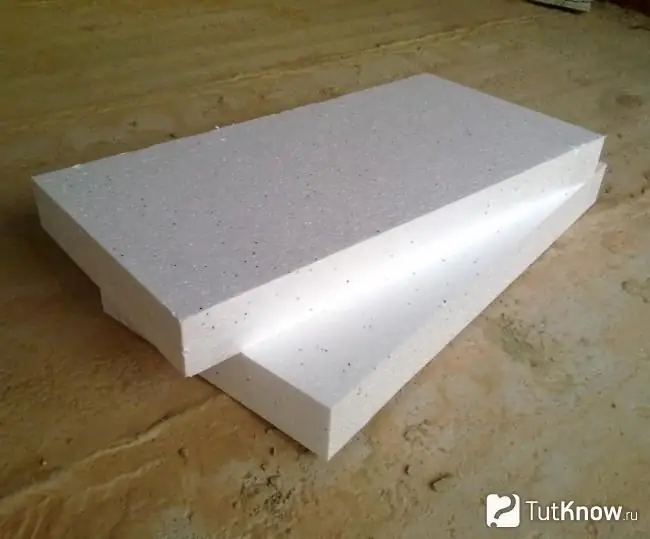
Through the roof, the house loses a large percentage of thermal energy, therefore, thermal insulation of the technical floor has always been taken seriously. Nowadays, foam plastic is often used for such purposes - plates made of expanded polystyrene granules treated with saturated steam. The fragments are filled with air, which is a natural insulator.
The product is available in various modifications, which allows it to be used in various situations. Rigid slabs are used for thermal insulation of the floors of the upper floor, less dense ones are laid under the roof. The method of insulation is chosen depending on the plans of the owner. His decision is influenced by such factors as the purpose of the room, the requirements for the temperature inside the attic, the composition of the insulating "pie".
Features of fixing foam:
- On wooden floors, samples are placed between the logs and are not fastened with anything.
- The material is glued to concrete floors and gables.
- To insulate the roof, it is laid between the rafters and fixed with slats or special corners.
The panels are distinguished by good water-repellent characteristics, therefore, the ceiling of the lower room must be covered with a vapor barrier film, and the room itself must be well ventilated. The membrane will not allow moisture to condense on the ceiling and exclude the appearance of dampness and mold. For the same reason, it is convenient to insulate attics with polystyrene during the construction phase of a building.
In stores, the product is sold under the PS or PSB brand with the addition of an alphanumeric designation. For example, PSB-S-25 means self-extinguishing foam with a density of 25 kg / m3.
Advantages and disadvantages of foam insulation of the attic
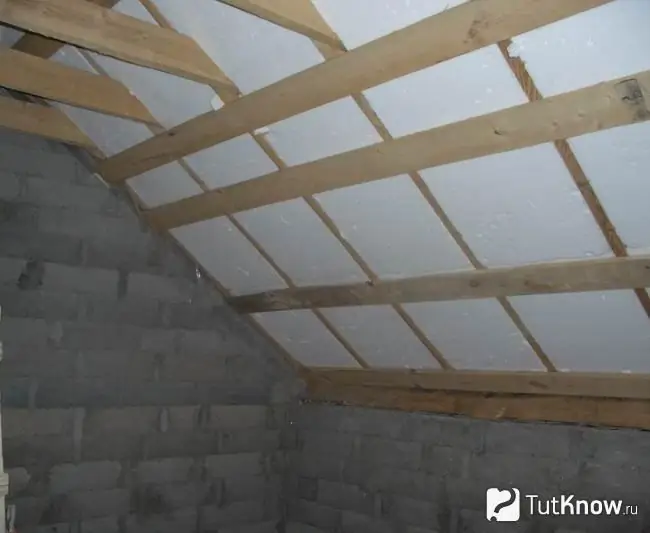
The use of foam for finalizing the roof and base of the technical room is profitable and has many advantages:
- It has excellent thermal insulation properties. The foam layer reduces noise in living rooms.
- The moisture absorption of the product is very low. It can be used to insulate the attics of buildings located in damp areas. Low hygroscopicity will allow you to lay the material without membranes.
- The insulator does not change its size with temperature fluctuations. This quality is especially appreciated on the technical floor, where the temperature in winter and summer is very different.
- During operation, shrinkage does not occur, cold bridges do not appear. No fungus or mildew forms on its surface.
- It is possible to install polystyrene in the attic at any stage of building a house and during its operation.
- The service life of the coating is tens of years.
- Sheets are easily cut to obtain custom shapes and sizes.
- The panels are manufactured with high precision, which facilitates installation work. The very low weight of the material also reduces the time required for finishing works.
- High-density foam can be installed on the floor of a maintenance loft without an outer covering.
For fairness, it is necessary to list the shortcomings that may appear when insulating the upper floors:
- Under the influence of open fire, the foam melts with the release of a large amount of poisonous smoke. It cannot be used for thermal insulation of fire hazardous buildings.
- When a warm attic is formed, the effect of a thermos is created, therefore, there must be forced ventilation in the room.
- Mice like to settle in the thickness of the coating.
- At high temperatures (for example, in summer), it emits volatile substances that are harmful to the body.
- Styrofoam quickly deteriorates in the sun. Therefore, when buying, check the storage location.
Attic insulation technology with foam
Installation of the product on the floor and roof of the upper floor includes compliance with all technological nuances: determining the required number of panels, performing operations in a specific sequence, checking the quality of materials. The technical room in the upper part of the house can be protected by cold or warm protection. The difference lies in the insulated surfaces. In a cold attic, polystyrene is placed only on the floor, in a warm attic - only between the rafters. In the latter case, a positive temperature is provided by warm air penetrating through the unprotected ceiling from the living rooms of the house.
Materials and tools for thermal insulation of the attic
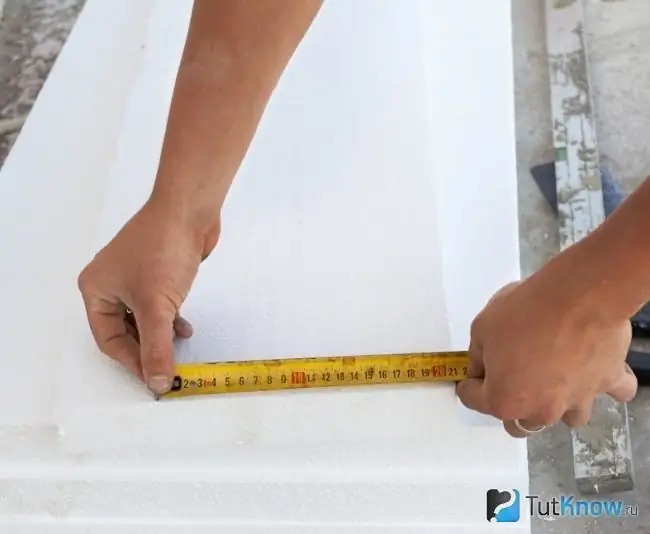
It is possible to insulate such a critical area of the house as the attic only with high-quality material. It is impossible to check in the store the compliance of the characteristics indicated on the foam plastic packaging with the actual ones, but it is not difficult to identify a fake.
Simple procedures will help to control the quality of the goods:
- Examine the foam panels. High-quality granules of the same size, evenly distributed in space, there are no voids between them. However, too large fragments indicate the presence of pores through which heat leakage occurs. In addition, such a product absorbs water well.
- The material should be perfectly white. It gets a different color when using low-quality raw materials.
- Styrofoam should be stored in plastic wrap packaging. There are options for selling products individually, but on their surface there must be appropriate brands and markings applied in the factory.
- The label contains basic information about the product - manufacturer, dimensions, characteristics, applicability.
- The panels have the same dimensions, deformations are not allowed. If you can agree with the deviations in length and width, then the different thickness should alert you.
- The sheets are odorless at all.
- Quality slabs are soft and plastic. After pressing, the surface quickly returns to its shape. Rigid products are obtained as a result of a violation of technology. They do not hold heat and moisture well.
- If you are allowed, break off a piece and inspect the fracture site. If the foam is of good quality, the granules of the material will be damaged when breaking. In a fake, a fault line will run between them. Do not judge the quality by the ends of whole sheets, the cuts at the factory are made very carefully with special devices and do not reflect the real structure of the product.
- Weigh a cubic meter of panels. Quality products weigh at least 16 kg.
- When determining the required thickness of the coating, be guided by the recommendations of SNiPs, but in any case, the sheets should be more than 100 mm. The size depends on the construction and material of the attic and the climatic zone in which the building is located.
Certain styrofoam modifications can be used on the top floor for indoor use. These include self-extinguishing products that do not support combustion, having the letter "C" in the designation.
Heat insulator, which is recommended for use in our case:
- PSB-S-15 50-100 mm thick - polystyrene with a density of 15 kg / m3, intended for insulation of roofs and unloaded floors.
- PSB-S-25 50-100 mm thick - foam plastic with a density of 25 kg / m3, for thermal insulation of gables.
- PSB-S-35 50-100 mm thick - foam plastic with a density of 35 kg / m3, for laying on the base of an attic with a medium load capacity. It is not necessary to make a decking to protect the covering.
Product adhesives are divided into 2 groups: universal and special. Regardless of their purpose, they must meet the following requirements:
- The product is intended for gluing the material indoors and emits a minimum amount of harmful vapors. The toxicity level is recorded in the certificate of conformity of the goods kept by the seller.
- The substance reliably holds the panels throughout the life of the insulator at any temperature that is possible in the attic.
- It contains additives that prevent the appearance of mold.
- The glue contains no gasoline, solvents, ethers that can destroy the structure of the insulation.
- Dry mixtures must be stored in closed warehouses. Buy goods in hermetically sealed bags.
When buying, use these recommendations:
- Check the availability of a sanitary-epidemiological conclusion and a quality certificate.
- Do not buy a product that sells for stocks. Often it has expired.
- Refuse offers from dubious manufacturers.
- It is advisable to purchase adhesives that have a long solidification period. You get additional time to adjust coverage.
- Buy funds with a margin. The packaging contains background information on its consumption on perfectly flat surfaces. In case of fixing on stepped substrates, more glue is needed.
- It is convenient to use foam glue for attaching to the gables. It is sold ready-to-use in cans, but a special device is required for application. It hardens very quickly - within 12 minutes.
To create an insulating layer on the roof and floor, you will need sheets of various sizes and geometries. To quickly cut workpieces, use tools such as knives - kitchen, wallpaper, or office supplies. The main thing is that it is sharp. You can warm up the tool before use.
An electric jigsaw will cut material of any thickness, but the ends of the workpieces will be uneven. Nichrome wire, heated to redness, is used to make curved workpieces. The ends of the sheets are very high quality.
Installation of foam on the floor
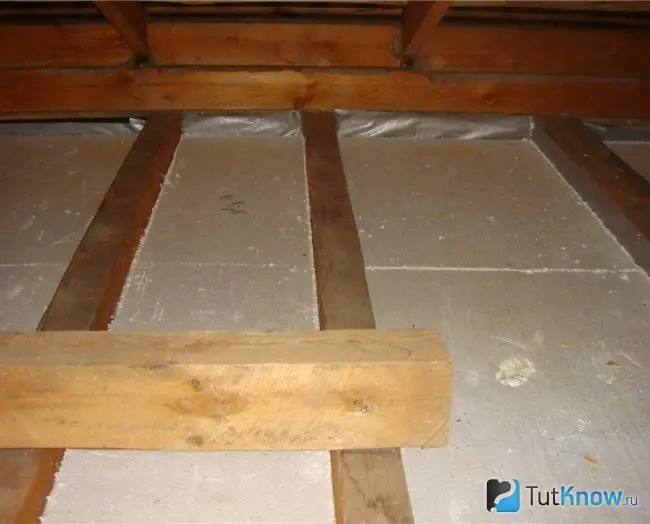
The main option for creating an insulating layer on a concrete surface is gluing foam.
The work is performed in the following sequence:
- Clear the attic of unnecessary things.
- Inspect the concrete floor for cracks, nicks, and other defects. Fill problem areas with cement mortar.
- Check the flatness of the surface with a long ruler. Cut down all protruding sections.
- Prime the base. Check the levelness of the floor and remove it with a self-leveling mixture. Perform further work after the base is completely dry.
- Apply glue to the foam. The coating method depends on the condition of the floor.
- For gluing to a flat surface, grease the sheet with glue first with a flat spatula, and then remove the excess with a notched trowel. If the base has differences in height, apply the glue to separate sections of the foam: along the edges, at a distance of 1-2 cm from the ends - in a strip 20 mm high and 3-4 cm wide; in the middle of the sheet - in 4-5 sections with a diameter of 10-12 cm. Leave the sides clean.
- Place the panel on the base and press down. After laying, press the following products against the neighboring ones. Remove glue that is squeezed out through the joints immediately.
- Periodically check the levelness of the surface with a ruler and level. You can move the slabs on the floor for 20 minutes, until the glue sets.
- Place small samples cut from the workpieces last.
- Check for gaps. Fill them up with scraps if found.
- Mount the second row of insulation with an offset so that there is no one joint line.
- After insulating the attic floor with foam, cover it with a vapor-permeable membrane with an overlap of 10-15 cm on adjacent areas and on the walls. Glue the joints with reinforced adhesive tape.
The need to create a protective layer for insulation depends on the purpose of the technical floor. In the case of intensive use, the coating is plastered with mixtures intended for foam plastic.
Follow these procedures:
- Stir the dry mixture with water in a concrete mixer in the proportion indicated by the manufacturer.
- Cover the base with fine construction mesh and fix it with a mortar.
- After the mixture has hardened, apply a layer of plaster 10-15 mm thick.
Wooden floors are supported by logs - load-bearing beams that can be used to attach walking decks to them. Therefore, in this case, the bases of the exploited attics can be insulated with foam of low density, which reduces financial costs.
The insulating shell is formed as follows:
- Remove the top row of planks if you have a finished and subfloor.
- Clean the cavity between the lags from dust and dirt.
- Bend or remove any fasteners that could damage the waterproofing membrane.
- Cover the base with foil with an overlap of 10-15 cm on adjacent pieces and on the walls. Polyfoam does not allow water to pass through, but in the event of a roof leak, moisture can get through the cracks between the sheets to the ceiling, and then to the lower room. Cover the joints with adhesive reinforced tape.
- Replace the removed finishing floor or reassemble the wooden walking deck.
Fixing the foam to the roof
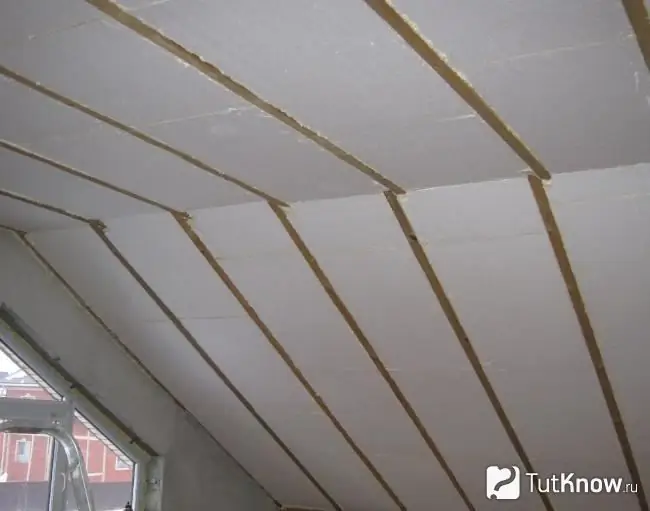
To insulate the roof, the sheets are placed between the rafters. This option is very popular, because there is no need to change the roof structure and load the frame with additional elements.
Before insulating the attic with foam, make sure that the roof meets the following requirements:
- The drainage takes into account the slope of the structure.
- The height of the attic allows you to attach a vapor barrier film to the rafters from the inside.
- There will be space for ventilation between the roof cladding and the insulation.
To prevent leakage of thermal energy through the roof, perform the following operations:
- Treat all wood structures with antiseptics.
- Cover the outside of the rafters with a tension-free waterproofing sheeting and staple them to the timber structures. Lay the cloth with an overlap of 10-15 cm on adjacent pieces. Seal the joints with special adhesive tape. If the cover has been installed long ago, install the membrane from the inside of the attic.
- Install the battens and lay the roofing material. After finishing work, a gap of 50-60 mm should remain between the cladding and the film. Free space is necessary to protect the rafters and slats inside the attic from possible roof leaks. Moisture trapped on the film will be removed by circulating air through the technological gaps of the cladding.
- Cut pieces of styrofoam and place them between the rafters. The dimensions of the panels should be slightly larger than the distance between the rafters, so that they hold on their own against friction. Plates are allowed to be mounted in 2 rows, but place the lower elements with overlapping the junction of the upper ones. Leave a gap of 20-30 mm between the foam and the vapor barrier for ventilation. Plates can be fixed with thin strips or special corners.
- Check that there are no gaps between the sheets and near the rafters. If found, seal them with scraps of material or polyurethane foam.
- Cover the panels from below with a second vapor barrier foil to keep moist air out of the timber structures. Do not stretch the membrane. Attach it to the rafters with a construction stapler.
- Glue the joints with adhesive tape.
- It is not necessary to cover the attic from the inside with boards or shields.
Fastening the foam to the gables
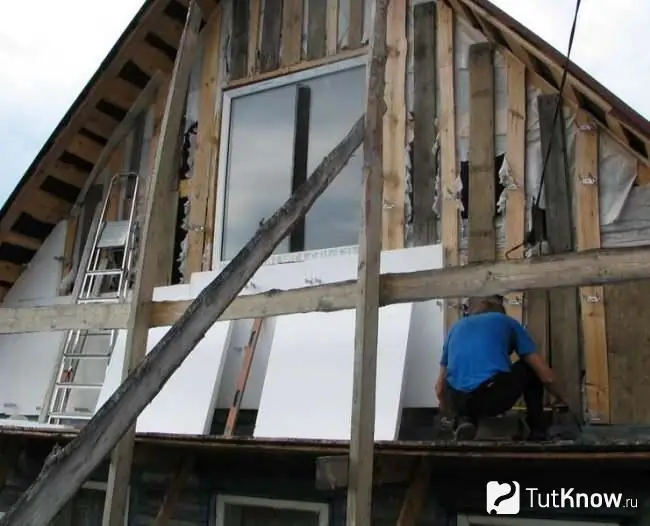
The method of attaching the product to the vertical wall of the attic depends on the design and material of the partition. The slabs are attached to the boards and shields in the same way as to the roof; they are glued to the concrete and brick wall. It is convenient to fix the foam with foam glue. The procedure is performed using a special pistol.
The order of work is as follows:
- Secure the substance container to the fixture.
- Apply foam around the perimeter of the sheet and diagonally.
- Place the insulator against the wall and press down.
- Repeat the operation for all sheets. After laying, press the new products against the already fixed ones.
- It is allowed to fasten the panels in a day for insurance with dowels with a wide head.
Using foam crumbs to insulate the attic
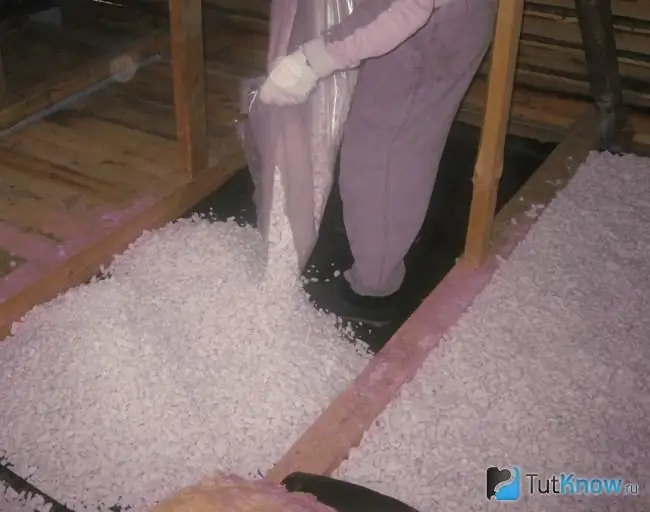
To reduce costs, the attic can be insulated with crushed foam plastic - rounded balls measuring 2-7 mm. Loose mass is obtained from waste and recycled products, which helps to reduce the cost of insulation. During crushing, the granules partially lose their shape, but the heat-insulating characteristics of the substance do not change. The crumb is sold in bags of 0, 5 or 1 m3.
Usually, wooden floors are insulated in this way. This is due to the presence of lags that help create pockets to fill. For work, you will need a special blowing machine or, if it is not available, a garden fan. Under the influence of a powerful air flow, the balls penetrate into hard-to-reach places, therefore, the insulation layer accepts all the irregularities of the enclosed space.
The work takes place in the following sequence:
- Prepare the base as in the previous insulation options. The presence of a waterproofing film is required.
- Lay a dense membrane on top of the logs with an overlap of 15-20 cm on adjacent cuts and on the walls. Seal the joints with strong adhesive tape.
- Fasten the film to the joists in a taut state using rails, which should be laid across the load-bearing beams. The distance between them is 40-50 cm.
- Prepare a powerful garden vacuum cleaner. Make a hole in the foil near one wall, install a hose in it and slide it towards the second wall parallel to the joists. Leave a 0.5 m gap between the edge of the hose and the wall.
- Place the suction hose in the foam bag and turn on the vacuum cleaner.
- When the mass fills all the space between the hose and the wall, move it another 0.5 m and repeat the operation.
- The density of the coating can be controlled through the film. When pressed, the insulation should bend only by a small amount. The hardness of the layer should be the same over the entire area.
- After filling the space between the lags, go to the next section.
- Cover the cut with adhesive tape.
- Similarly, you can insulate the space between the rafters under the roof.
The use of foam concrete for thermal insulation of the attic
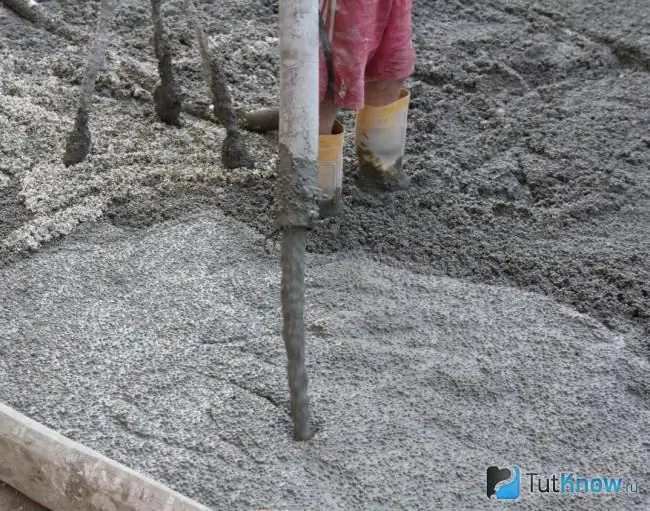
This type of insulation is used in attics with very uneven concrete floor slabs. In this case, you first have to level the surface with a thick layer of screed, and then lay the insulation. To avoid unnecessary costs, a special solution is used that simultaneously levels and seals the floors. The order of work is as follows:
- Prepare the base for insulation as in the previous sections. Don't forget the waterproofing film.
- Mount base surfaces on which it will be possible to control the horizontalness of the coating.
- Pour the sand-cement mixture (60 kg), plasticizer (0.5 kg), granular foam (60 l), water (8 l) into a concrete mixer and mix everything thoroughly.
- Check the quality of the foam concrete. All granules must be coated with cement. The finished solution should resemble a thick dough.
- Pour the mixture onto the floor and align with a long ruler supported by the beacons.
- After it dries, the insulation of the attic is completed.
How to insulate an attic with foam - look at the video:

Light weight and uncomplicated technical process allows one person to insulate the attic. Polyfoam reliably protects the house from heat loss if the installation technology is followed. To ensure an acceptable result, take the problem seriously.