Substrate under the parquet board, its functions, types, laying technology. Parquet underlay is a special material that, at a relatively low cost and ease of installation, can extend the life of the floor covering. Let's consider how to choose and lay it correctly.
Functions of the underlay for parquet
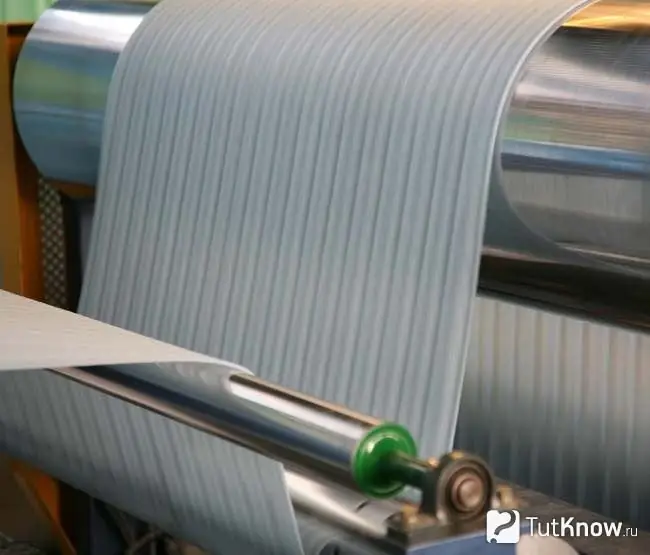
Parquet underlays serve several basic purposes. These are the correction of the subfloor, additional waterproofing, thermal insulation and soundproofing.
Due to the properties of the materials used for the manufacture of the lining, the thermal insulation characteristics of the parquet board change, as well as the heat transfer between the base of the floor and its final coating improves. This protects the parquet floor from temperature fluctuations and excess moisture.
Also, the material reduces noise and vibration. It prevents the penetration of sound vibrations from the room located below, and also dampens the sounds made by residents.
In addition to the properties described above, various types of parquet substrates may differ in such additional characteristics as durability, resistance to high loads, environmental friendliness, and also an affordable price. All these qualities make it possible to extend the life of the floor covering and make its operation as comfortable as possible.
When choosing a substrate for parquet, consider all the points, paying special attention to the parameters for adjusting the subfloor, waterproofing characteristics, durability, environmental friendliness and resistance to stress. Remember, quality material cannot be cheap!
Important! As a result of the high demand for this category of goods, manufacturing companies are trying to offer as many new types of substrates as possible. As a result, a wide variety of materials have appeared, but not all of them perform their functions effectively.
Criteria for selecting a substrate for parquet
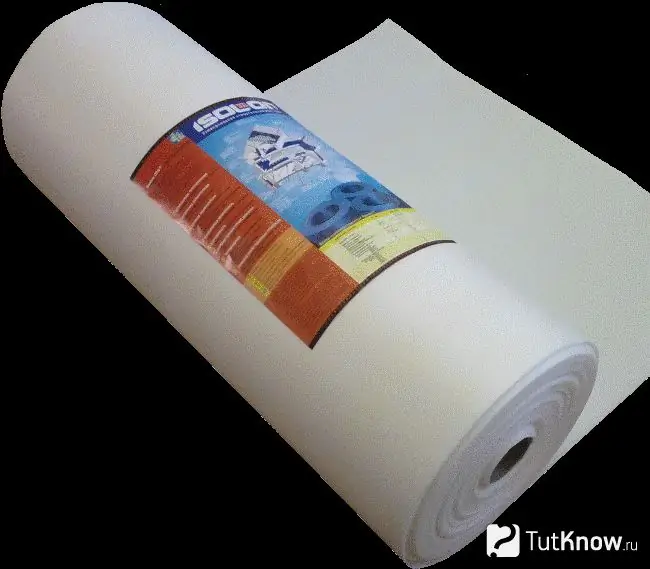
The choice of substrate for a parquet board is based on various parameters. It is very important to consider the following:
- Specificity of the premises … These include the maximum loads on the floor covering, humidity, temperature conditions.
- Security … In a room where children will spend a lot of time, it is recommended to use environmentally friendly finishing materials.
- Qualitative characteristics … A cheap backing will last less. When buying, also take into account the thickness, it will not work to reduce it if necessary.
- Value for money … We will also include a parquet board here. If it is of low quality (economy class), then it is impractical to buy an expensive substrate.
- Dimensions (edit) … The optimum thickness of the parquet subfloor is 2 mm. This is sufficient to compensate for slight irregularities in the base surface.
Advice! When choosing a substrate for a parquet board, be guided by the manufacturer. Do not buy goods of unknown brands in the construction markets. Go to specialized stores and always consult with a specialist.
The main types of substrates for parquet
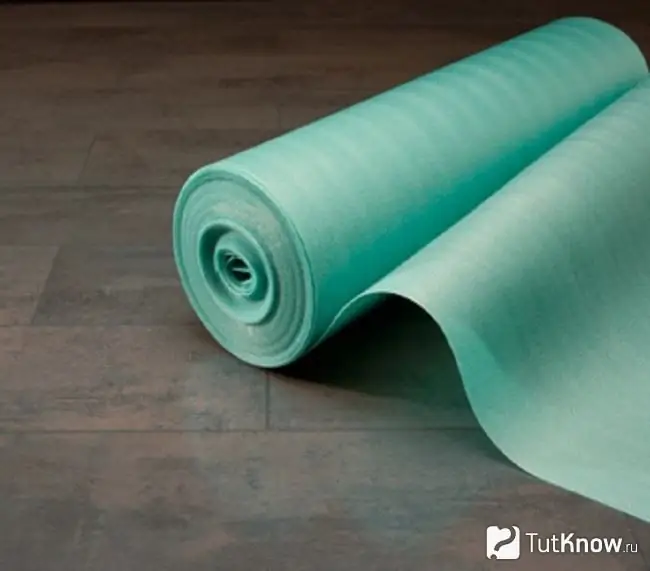
Installation of a parquet board is a rather laborious process that requires a lot of time. Therefore, it is important to take seriously the issue of choosing a substrate, because the replacement of this material will be complicated by the need to completely dismantle the top layer, and then restore it.
Let's consider the main types of substrates for parquet:
- Cork lining … Elastic, durable, environmentally friendly material, resistant to decay processes. The cork substrate is susceptible to moisture and therefore requires additional waterproofing. Differs in a long service life and high cost.
- Expanded polystyrene as a substrate for parquet … Long-lasting synthetic coating that does not shrink. It is characterized by a low cost. One of the main advantages of this material is considered a favorable interaction with a parquet board, in which there is no development of fungus and putrefactive processes on the inner parts of the top coating.
- Expanded polypropylene backing … The cheapest type of interlayer between parquet and subfloor. Among the advantages of the material are excellent steam, heat and sound insulation, as well as ease of installation. The main disadvantage is the short service life. Full wear of polypropylene occurs within 10 years from the date of manufacture. A substrate of this type is distinguished by high rates of fire hazard and release of toxic substances during combustion.
- Polyethylene foam as a lining for parquet … Another type of synthetic backing for parquet boards. The material is safe for humans, resistant to chemicals, as well as bacteria and fungi. It is moisture-proof and has excellent thermal insulation properties. Installation directly on a sub-floor is permissible. The big advantage of this material is its affordable price. Disadvantages include the loss of elasticity of the polyethylene foam backing over time.
- Bituminous cork substrate … It is made from natural bitumen and cork chips. This lining has excellent noise absorption and waterproofing performance. The composition of the material provides excellent micro-ventilation of the floor and the free elimination of moisture from under the floor covering due to the use of a special skirting board. A serious disadvantage of bitumen-cork material is its ability to release toxic substances when heated.
Among the large number of varieties of substrates for parquet, it is not difficult to find the most suitable option that satisfies any request. This will create a high-quality floor covering that will perform its functions for a long time and reliably.
Parquet underlay manufacturers

The quality of the workmanship of the material that is used to cover the subfloor before laying the floor covering plays an important role. Therefore, experts recommend, when choosing a suitable substrate for parquet, to focus on well-known manufacturers with a good reputation.
Among the brands that make cork coverings, representatives of the Portuguese Republic enjoy well-deserved success. Without any doubt, you can purchase products from such famous brands as Amorim, Ipocork and Aberhof. Among the producers of expanded polystyrene, the Izoshum company is often distinguished. According to consumer surveys, the parquet substrate of this Russian brand is the best in terms of price and quality characteristics. Also, you can often hear good reviews about the products of the Polish company Izopolin.
Based on information from leading manufacturers of parquet and laminate flooring, the brands Tuplex and Izolon were recognized as the best brands for the production of polyethylene foam substrates. And from a wide variety of manufacturers of bitumen-cork coatings, most often good recommendations sound to the Russian brand Parkolag.
Important! When purchasing a substrate for parquet boards of a particular manufacturer, be sure to ask the seller for product quality certificates and check all purchased goods for defects.
The technology of installing the substrate under the parquet
After you have decided which substrate is better for the parquet board, and have prepared the base, you can proceed to the installation work. Installation methods differ depending on the selected material, but in any case, to install the coating, it is necessary to prepare the surface of the base - clean it of debris, dirt and dust, and also dry it.
Materials and tools for laying the underlayment under parquet
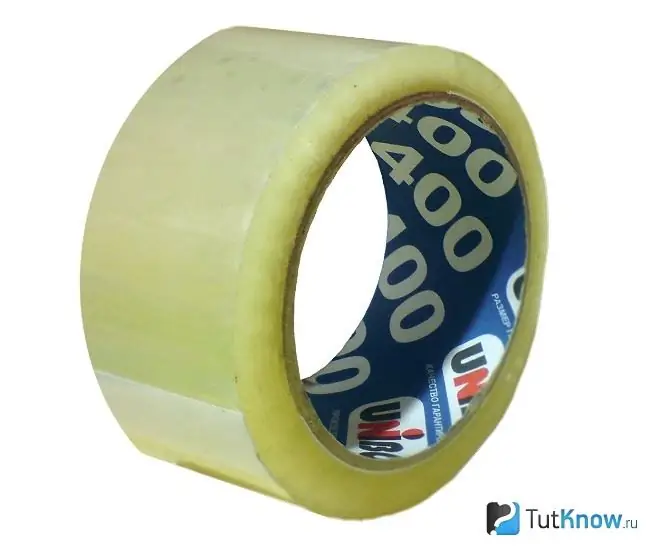
There are not many tools needed to work with the underlay. However, bearing in mind the rather extensive preparatory work for leveling the rough base, you will need:
- The substrate itself;
- Construction tape;
- Waterproofing film, if required by the substrate;
- Concrete mix to create a leveling screed;
- Mix for self-leveling floor with slight irregularities;
- A drill with a mixer nozzle for mixing concrete or self-leveling flooring;
- Spatula, rule, trowel for leveling concrete screed;
- Needle roller for removing air bubbles from the self-leveling floor;
- Tools for cutting waterproofing and cutting out the substrate;
- Tools for removing old finishing coat (as appropriate, depending on the type of flooring).
Dismantling the old subfloor before laying the subfloor
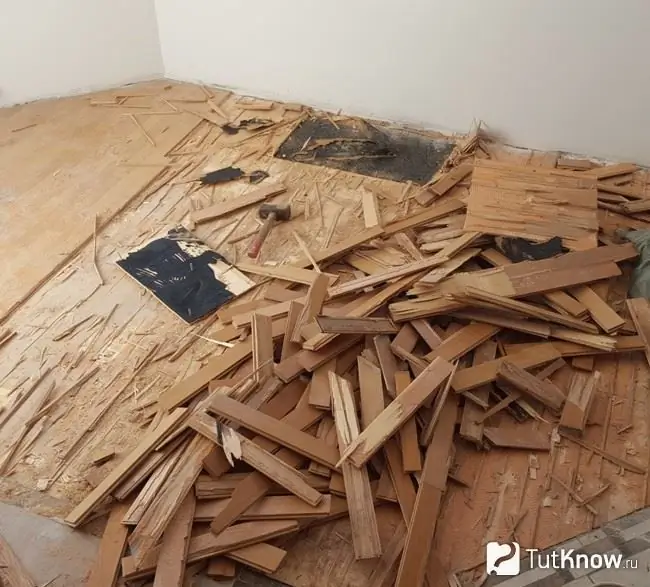
The old coating is removed. In this case, it is necessary to act as carefully as possible so as not to damage the screed. If the condition of the floor is not satisfactory or the height differences in the base are more than 2 cm for every 2 meters of area, it will be necessary to replace it. Smaller differences can be leveled with a self-leveling floor.
Before starting installation, you must carefully inspect the work surface. It must be completely dry and free from damage. If there are defects on the base, they must be eliminated with a putty or concrete mortar. Large fractures and cracks can be repaired with polyurethane foam.
After that, the surface is cleaned of debris and dust, and then impregnated with a special penetrating primer. An elastic damper tape is glued along the perimeter of the walls. After completing all these steps, you can proceed to the next stage of preparatory work before laying the substrate for the parquet board.
Floor surface preparation for laminate underlayment
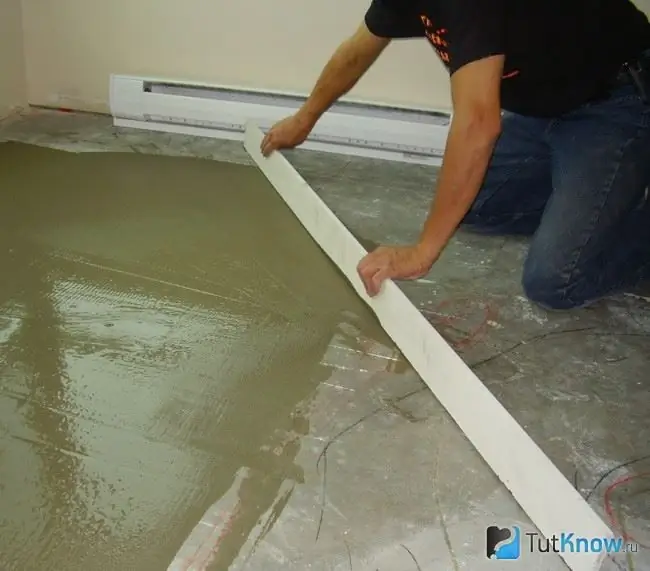
Contrary to the widespread misconception, the underlayment for parquet in any form is not able to smooth out absolutely all defects of the subfloor. In some cases, it can exacerbate the problem of an uneven base. Therefore, it is so important to thoroughly prepare the surface before laying the package board.
Installation of the substrate under the parquet board should be carried out on the most even base, otherwise all defects will be reflected on the top layer of the floor covering. The procedure should be started only after all communications have been laid in the room and the rest of the repair work has been completed.
If the rough base is completely uneven, it is customary to pour a concrete screed. To make it as flat as possible and reach the required height, a system of beacons is set up. They are guided by them when leveling the base of the floor.
Concrete screed installation technology:
- Make lighthouses out of a metal corner and secure them with thick cement mortar.
- Set them at equal lengths along the lobe and cross lines that intersect the room. The distance from the wall to the first level beacons should be no more than 25 cm, and between the rows no more than 110 cm.
- Spread out the concrete mortar in small portions every 40 cm.
- Lay the slats on it and press them down a little.
- Use a level to check the height difference between the points and correct it if necessary.
- Proceed to the installation of the screed after the solution under the beacons is firmly seized.
- Start pouring the solution from the corner of the room, filling all the cracks with it.
- As a rule, level the top layer of the screed, pulling it towards you, while making wave-like movements from side to side. In this case, lean them on the top points of the lighthouses.
- After the overlap is completely covered with mortar, let it harden. This process usually takes 2 to 3 weeks.
- To avoid the appearance of cracks on the surface of the screed, wet it during the first week at least 2 times a day.
If the condition of the old concrete screed is generally satisfactory, but a little leveling is still required, self-leveling floor technology is used. In this case, it is very important to prepare a solution of the correct consistency - it should be evenly distributed over the floor surface. To do this, it is enough to follow the instructions in the manufacturer's instructions for the mixture and observe the proportions. The technology for preparing the solution is as follows: the required amount of water is poured into the container, the powder is poured, then the mixture is thoroughly mixed with an electric drill for at least 10 minutes.
Pouring of self-leveling floors is carried out at a temperature of 15 to 25 degrees above zero. The distribution of the solution starts from the far wall and is carried out without long interruptions. The time interval between laying each next portion should be no more than 10 minutes.
The process of leveling the floor is as follows:
- A portion of the finished mixture is carefully poured onto the floor surface.
- The solution is smoothed with a wide spatula and rolled with a needle roller, expelling air bubbles.
- Thus, the entire base is poured.
After completion of the work, the floor is covered with polyethylene. A week later, when the surface has solidified, you can proceed to further work.
How to attach a subfloor under parquet
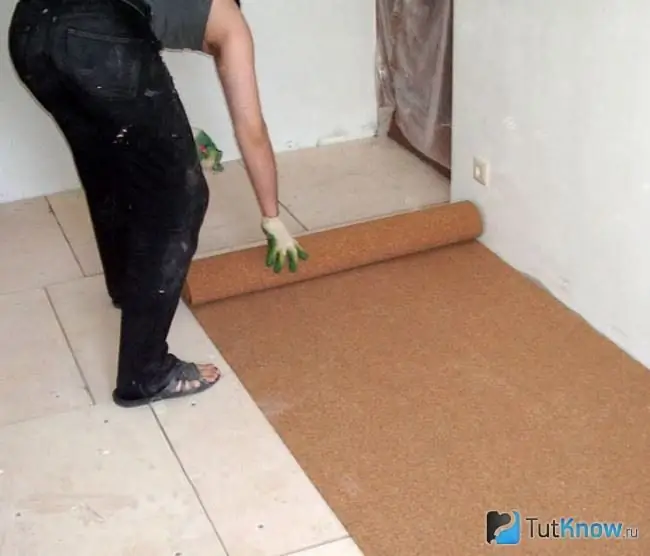
It is not recommended to lay the underlay all over the floor at once. This is due to the fact that under the influence of the weight of the topcoat, the material may change its dimensions slightly. For this reason, each next segment should be laid only after the previous one has been closed.
The cork backing does not tolerate interaction with moisture, therefore it is not advisable to install it in rooms with a floor humidity of more than 5%. For the same reason, care should be taken when laying on fresh concrete screed. A cork backing is not placed in rooms located above bathrooms, unheated basements.
If there is still a risk of increased humidity during the operation of the floor, a layer of waterproofing coating should be laid under the material. It is laid with an overlap and fixed with tape not only between the strips, but also along the perimeter of the room. The process of laying a cork backing is as follows:
- Leave a gap of about 10 mm between the wall and the backing sheet.
- Fasten the pieces of material together with tape, forming an overlap.
- The direction of stacking does not play a big role, unless otherwise indicated on the manufacturer's packaging. In this case, you must strictly follow the instructions.
- When installing the plug, make sure that the joints of the material do not coincide with the joints of the top cover.
- When placing each new sheet, clean the surface of the base from dust with a vacuum cleaner. In the process of work, you have to walk on the screed, which contributes to its abrasion.
Installation of polystyrene foam backing is made with an overlap not only between the sheets, but also with the surface of the walls. After laying the parquet board, the protruding parts of the substrate are cut off with a sharp knife. This is necessary so that the internal channels of the material have access to the external environment. Thus, the circulation of moisture and air is maintained.
When installing a bitumen-cork substrate under parquet, it is necessary to ensure that the cork layer is always facing the concrete screed. The sheets of material are fastened together using adhesive tape at least 5 cm wide. After laying the parquet board, it is necessary to leave ventilation holes in the plinth so that the moisture accumulating under the covering has the ability to freely escape.
How to fix the substrate under the parquet - watch the video:

A correctly selected and correctly laid floorboard substrate will allow you to create comfortable conditions in the room and extend the life of the floor covering.