Plaster molding, properties of the materials used, preparation for work and manufacturing technology. Plaster moldings are original interior details that can be used to give it a luxurious and noble look. This decor is perfect for decorating rooms made in a classic style, antique or baroque. Thanks to the advent of gypsum mixes, the possibility of implementing even the most intricate design solutions has become quite real. The correct selection of the form for the manufacture of plaster moldings is one of the main conditions for obtaining high-quality products.
Properties of materials for gypsum stucco molding on walls
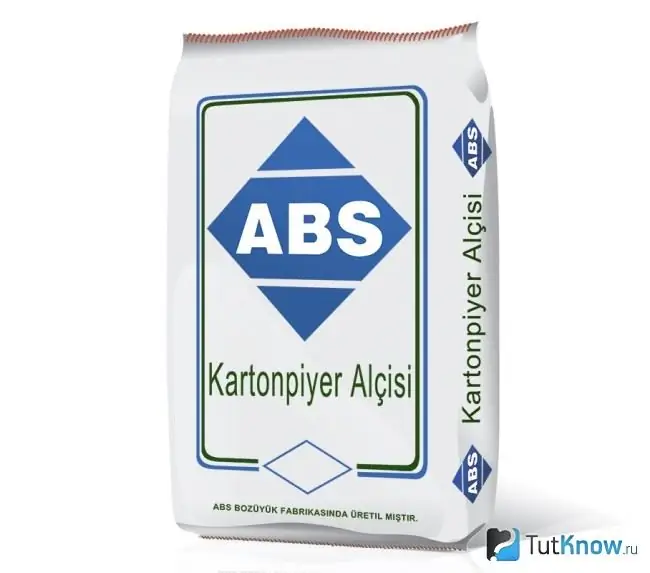
The popularity of gypsum stucco molding is due to the cheapness of the material, its wide distribution and ease of processing. Gypsum belongs to air binders, therefore, parts made on its basis are used mainly for interior decoration.
The base material is obtained by firing natural gypsum stone and then crushing it. For stucco work, dry and white gypsum is taken, which does not have any admixtures of sand and caked lumps.
After adding water, the gypsum solution begins to harden no earlier than six minutes, and finishes - no later than half an hour. To increase its setting time, additives are introduced into the solution: borax, lime, glue and surfactants. If skin glue is used as a retarder, the end of the gypsum hardening occurs in forty minutes. The retarder is added to the solution at the rate of 0.2-2% by weight of the gypsum.
To accelerate the hardening of gypsum, additives are used: alum, table salt, sodium sulfate or just hot water. Sometimes this property of gypsum is necessary when molding certain parts of the human body from nature or removing the mask.
The amount of water for mixing the solution depends directly on the quality of the gypsum. Its finer grinding will require less water. On average, the final hydration of gypsum requires 18.6% of the liquid by weight. For the manufacture of stucco molding on the walls, the composition of the solution is selected empirically. However, practice shows that to obtain a mixture of normal density for 1 liter of water, 1.5 kg of gypsum should fall, respectively, for a thick solution - 2 kg, and for a liquid solution - 1 kg.
When gypsum hardens, heat is generated in the solution, and the mixture increases its volume up to 1%. Expanding, it tightly fills the entire form with its small details that make up the ornament of the future stucco molding. The main disadvantage of the material is its low water resistance. To increase it, as well as prevent warping of stucco parts, do the following:
- The consistency of the plaster dough is made more rigid.
- Additives are added to the solution: water emulsions of synthetic resins, sulfite-alcoholic mash or mylonft.
- Used for mixing gypsum 1.5% solution of borax or zinc sulfate.
- Lime is added to gypsum up to 5% of its weight.
- The finished parts of the stucco molding are impregnated with special solutions: potassium alum, sulphate iron or zinc, barite water.
- High-strength or polymerized gypsum containing synthetic resins is used.
To separate the finished stucco model from the mold, a fatty lubricant is used, which is a solution of stearin in kerosene. For its preparation, stearin is melted in a water bath, and then kerosene is gradually poured into it. The process is accompanied by constant stirring of the mixture until the complete combination of its components.
After cooling, the grease thickens and becomes Vaseline-like. The ratio of stearin and kerosene is 1 kg per 2.5 liters. In addition to grease, in the manufacture of gypsum stucco molding, a decoction of birch wood ash, mineral oil emulsions, soap foam or technical petroleum jelly are used for the same purpose.
To protect the gypsum stucco elements from deformation and increase their strength, material reinforcement is used. Reinforcement can be galvanized copper wire, mesh fabrics, steel rods, tow, hemp or shit. The choice of one or another reinforcement depends on the type, size and purpose of the product. If possible, it is placed in places of tensile stresses and not closer than 15 mm from the outer surface of the stucco molding.
Preparatory work before the manufacture of gypsum stucco molding
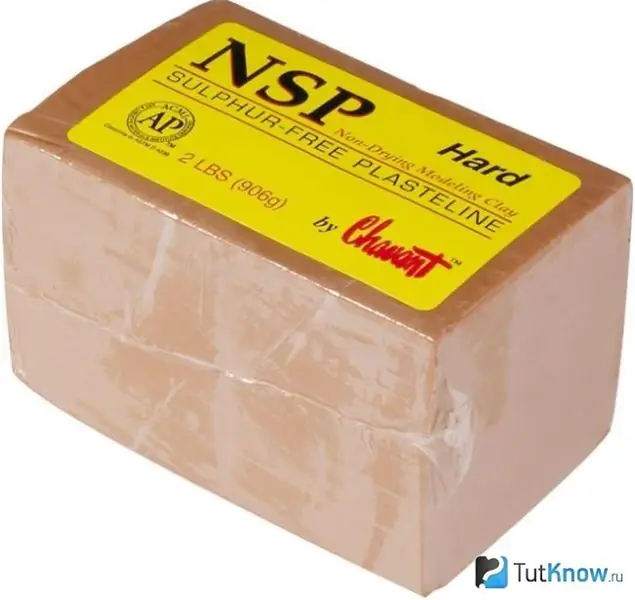
The stucco molding made by professional sculptors is incredibly beautiful, but the pleasure is quite expensive. However, if you have artistic taste, materials and the help of simple tools, you can make plaster moldings yourself.
All work will consist of several stages: creating a sketch or selection of a model, making a mold, casting a product and its surface treatment. Next, we will analyze them all in more detail. In the meantime, you need to stock up on the necessary equipment, consumables and tools. For work you will need:
- A flat table with a perfectly horizontal surface, since the molded stucco will freeze on it, and the slightest slope can cause a marriage.
- A dense film that will protect the table and surrounding objects from gypsum dust and adhesion of materials.
- A set of spatulas, a utility knife, a tape measure, a measuring cup, a ruler and a narrow brush.
- Building plasticine or clay.
- PVA glue, gypsum, cement for the manufacture of large elements.
- Silicone and release agent.
- Two guns for silicone and staple insertion.
- Stacks and knives as sculpting tools.
Before you make a plaster molding with your own hands, you need to decide on its size and design. The internet, history books, or design books can be used as a source of inspiration. It is important to know that gypsum stucco molding should correspond to the style of the room and harmoniously fit into its interior. When choosing the size of the parts, you need to make sure that the decor does not look too bulky and does not cover outlets and other details.
Plaster molding technology for walls
The technology for the manufacture of plaster jewelry provides for the sequential solution of several problems. It will require patience, attention, accuracy and some experience. If you do not have experience, you can practice creating small stucco elements: rosettes, flowers or monograms.
How to make a mold for stucco
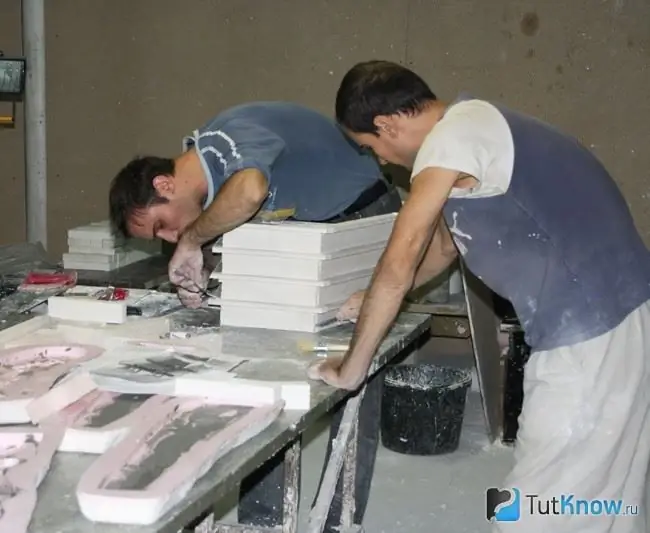
You should start by creating a model of a decorative element from plasticine. It is required for the future casting of the product. The model needs to be made slightly larger than the intended part. The use of plasticine makes it possible to change the shape of the casting any number of times until you get what you really need. The model can be manufactured according to the selected sketch. To do this, you need to print it on a 1: 1 scale and use it to sculpt a sample from clay or plasticine. If experience is not enough to make a stucco sketch, you can use a suitable finished polyurethane part, a wide selection of them is available in hardware stores. With just one element, you can make many of your own plaster parts. Moreover, the polyurethane model is easy to modify by adding plasticine elements to it or cutting off excess ones. Before use, the model must be treated with a release agent for easy separation of the future shape from it. After preparing the model, you can start the main process. First, it is necessary to mix silicone oil and silicone in order to increase the elasticity of the solution. It is required when the planned shape has complex details in the form of numerous curls and protrusions.
A simple form of using silicone oil for its manufacture does not require. A measuring cup should be used to maintain the proportions of the mass. The mixture must be thoroughly mixed until smooth.
Before making a mold for stucco molding, it is necessary to apply silicone to the model with a brush. It must penetrate into all pores and depressions and not leave air bubbles, which can further spoil the stucco molding. After applying the first layer of the mixture, the future form must be strengthened with reinforcement with gauze. It should be imprinted into the silicone layer, wrap tightly around the model, but not taut.
After the coating has dried, several more silicone layers must be applied to the sample, giving each of them 2-3 hours to dry. The total thickness of the coating should be about 3 mm. In places where the largest mass of plaster casting is planned, the silicone layer should be thicker. Here it is more convenient to apply it with a pistol.
If the form has a complex configuration and large dimensions, it will be necessary to make a plaster base for it. In the process of making stucco molding, this will help protect the shape from deformation. To make such a base, you will need any frame of suitable size, made of plywood or boards. The mold should be installed in it without removing from the model and secured with the same silicone.
Then you need to prepare a solution of cement, gypsum and PVA glue, and then pour it over the frame and level the surface. After the mixture has set, the frame should be carefully turned over, the copied sample should be removed from the silicone mold, and then the mold itself should be separated from the plaster. In this case, both parts will dry out faster. Final drying of the base and mold will take a couple of days. After its completion, you can start casting the stucco.
Features of gypsum mortar casting
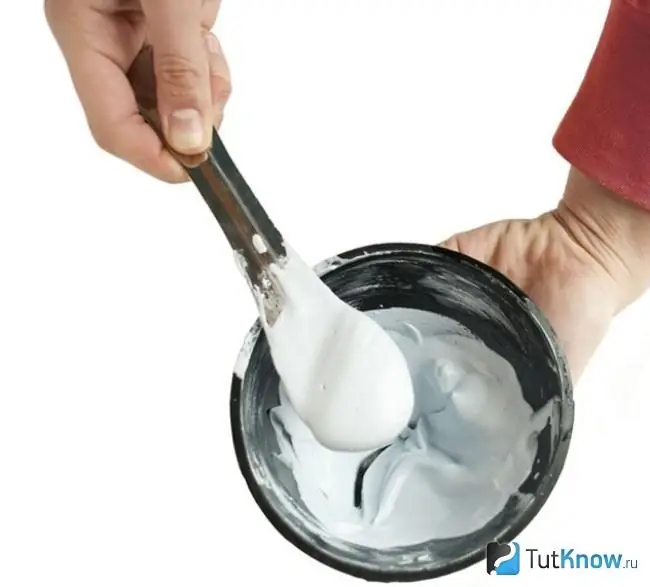
Before making plaster moldings, the finished form should be carefully treated with a release agent. In dry areas, the adhesion of the gypsum to the silicone may damage the mold.
Then you need to prepare a plaster solution. In order to avoid getting lumps, plaster should be poured into the water, but not vice versa. The material is scattered over the water surface until areas that are not absorbed by the liquid are formed on it; 10 parts of the powder should account for 7 parts of water.
After that, within a minute, you need to give the plaster the opportunity to calmly settle. This removes excess air from the solution. Then the mixture must be thoroughly and vigorously mixed using a drill with a mixer attachment. The consistency of the mixture should be semi-liquid. The addition of PVA glue, taken in a small amount and previously dissolved in water, will make the solution more plastic and prevent cracking of the finished product. Too long stirring is undesirable, since it can change the hardening process of the solution and further reduce the strength of the castings.
The next step in the stucco molding technology is filling the prepared form with gypsum mortar. When filling, the material should be distributed over it with vibrating movements. This removes unnecessary air bubbles, which can cause shells to appear on the finished stucco. After filling the mold, its top should be carefully leveled with a wide spatula. A standard stucco molding element dries for 15-20 minutes, after which it can be easily removed from the mold if it was previously well treated with a release agent. The final drying of the product must be done within 24 hours at room temperature.
Processing of finished stucco for walls
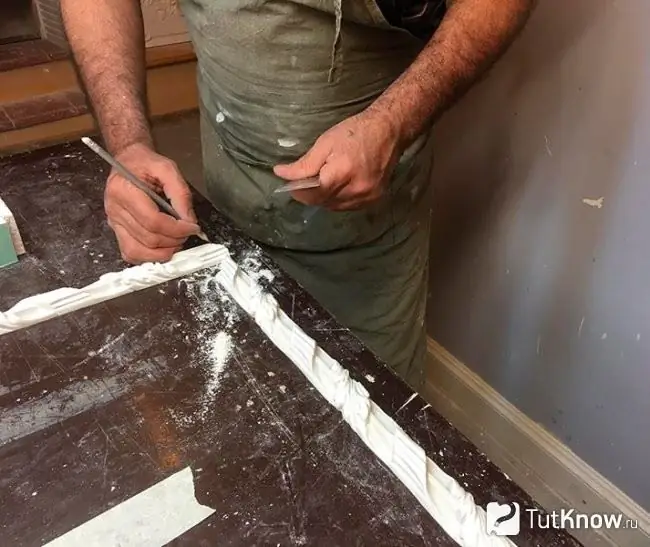
When the plaster molding begins to whiten, you can begin to correct and fine-tune it. In this case, small cavities should be eliminated, if any, and the surface roughness of the product should be sanded with fine emery paper.
On the side of the part mating with the wall, you need to make a notch for better adhesion to the structure. After that, the product must be primed, and when the composition is dry, painted in 2-4 layers with water-based paint.
Watch a video about making gypsum stucco moldings:
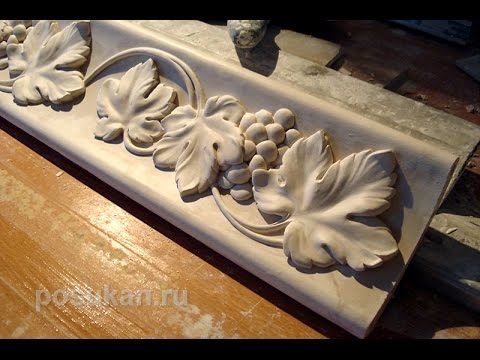
Understanding how to make stucco molding on the wall, you can not only decorate your home, but also prove yourself as a creative person. Good luck with your work!