Pros and cons of thermal insulation of an attic with ecowool, options for warming inclined and flat surfaces, quality control of raw materials, technology for creating a coating. Insulation of the attic with ecowool is an opportunity to make an exploited room out of an additional floor. The cellulose-based loose mass creates a reliable heat-insulating shell on the roof and floor. The substance is applied using a special device, which reduces the time of installation work. The article provides a sequence of operations for preparing raw materials for use and application to different types of surfaces.
Features of thermal insulation of the attic with ecowool
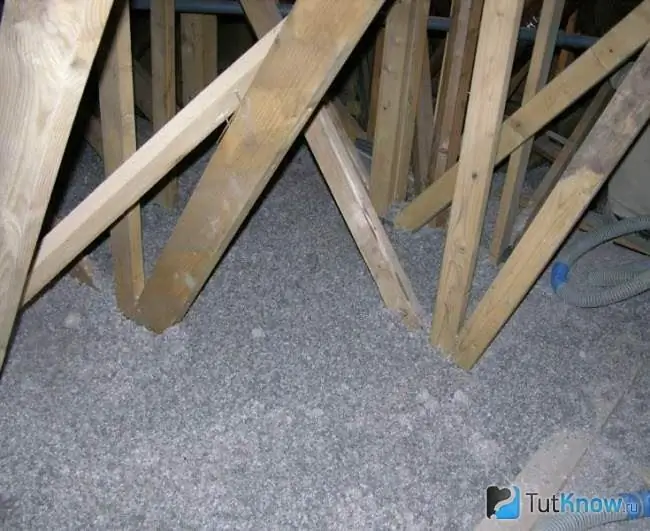
Thermal insulation of the upper floor involves the creation of a covering that allows you to save up to 40% of thermal energy in the rooms below it. Before insulating the attic with ecowool, decide on its purpose. If the upper floor is planned to be actively exploited, the roof must be insulated from the inside, but the floor is not, so that the heat of their living quarters heats the upper floor. If the attic serves as a technical floor, the substance is applied only to the ceiling.
Ecowool is considered one of the best options for insulating complex surfaces. It is a free-flowing heat insulator, consisting of cellulose fragments, small wood fibers and substances that improve performance properties. After manufacturing, the products are compacted and packaged in bags and briquettes, convenient for transportation. Before spraying, the material is fluffed with a special device. It can be transported to the surface to be insulated under pressure using a hose or manually.
There are two options for applying raw materials - dry and wet-glue. In the first case, "pockets" are created, which are filled with a dry substance. The packing density depends on the installation technology. If the insulation is supplied under pressure, this figure can reach 60-70 kg / m3, but usually 40-45 kg / m3… For comparison, the density of the coating after manual filling does not exceed 35 kg / m3… The cavity can be formed by plywood, film or kraft paper.
When installing according to the second option, the ecowool is moistened and a special glue is added to it, which ensures high-quality adhesion of the substance to the surface. In this case, it is not necessary to create closed cavities. The use of blow molding machines allows you to obtain a perfect coating on any structure, for example, this is how the most ulcerative areas are insulated - the joints of a sloped roof and floor.
Ecowool can be used to insulate the attic while in the room itself, if the distance between the ridge of the roof and the floor is at least 80 cm. If the height is less, a hole is made in the ceiling and a loose mass is fed through it from the side of the room.
Sometimes a combined method is used. First, the surface is covered with a wet mixture, which fills all voids and creates a monolithic shell. After drying, the area is fenced off, and the resulting "pocket" is covered with a dry mixture. This option is usually used when there is a need for high-quality insulation and soundproofing of the room.
Ecowool contains boric acid, which is a toxic substance. When ingested in large quantities, it can cause great harm to it. On contact with the skin, the component causes severe irritation, accompanied by itching and redness. Wear a respirator and gloves to avoid any nuisance while spraying.
Advantages and disadvantages of attic insulation with ecowool
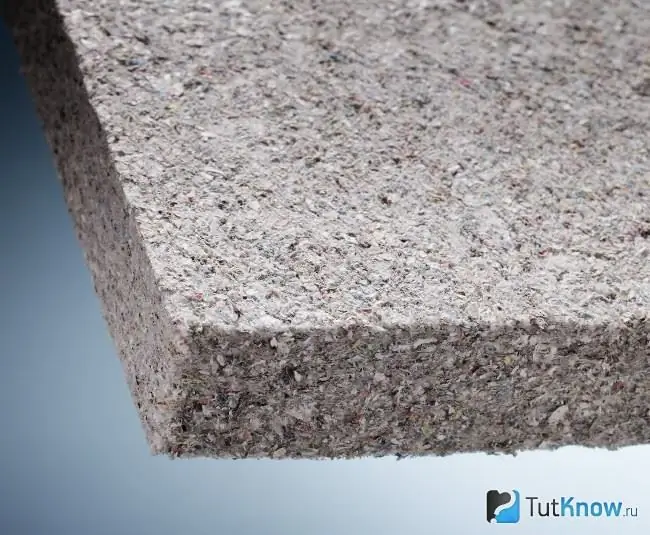
Experienced craftsmen are well aware of the advantages of a free-flowing mass. Users appreciate it for the following advantages:
- Ecowool has excellent sound insulating properties. After warming the floor, the house will become quieter.
- The elastic and resilient material does not shrink in a vertical position, which is important in the presence of a sloped roof.
- Does not react with metal roofing.
- The heat insulator retains its qualities for a long time due to the wood fibers, which have a capillary structure.
- After application, a monolithic layer without voids is formed, filling the surface of any shape. The cuttings can be reused - the production of ecowool is waste-free.
- The composition of raw materials includes antiseptics that do not allow mold and mildew to multiply. Mice do not live in its thickness.
- The coating performs its main functions at 20% humidity, which is ideal for use in cold attics. A vapor barrier membrane is not required to form an insulating layer.
- Ecowool reliably fills in hard-to-reach places between beams, battens and difficult floor surfaces. Subject to the technological process, the substance forms a monolithic coating without cold bridges.
- The process of creating an insulating layer can be mechanized. Special devices allow you to process large areas in the shortest possible time.
When insulating the attic, the shortcomings of ecowool appear, which the user should be aware of:
- In order to insulate inclined surfaces (roofs, slopes), it is necessary to create closed cavities where the mass is blown in. It takes a long time to make them.
- Raw materials for the production of insulation are cheap, but the processing technology requires special devices, so the finished product is quite expensive.
- The material smolders under the influence of high temperature, although there is no open flame. It must not be laid near chimneys.
- A lot of dust is generated during dry application.
Ecowool attic insulation technology
The biomass is lifted up manually or with the help of special devices. The first stage of preparing the mixture - fluffing - can be performed with any device, but only a machine designed for this purpose can create pressure in the hose.
Selection of equipment for working with ecowool
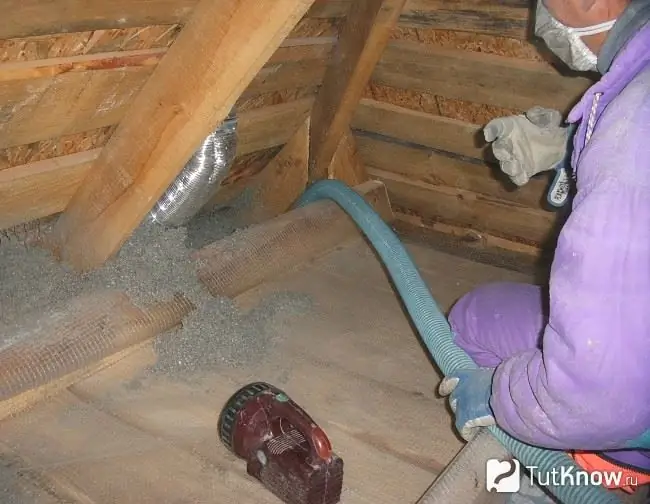
It is recommended to rent an apparatus for insulating the attic. In this way, you save money, and you will also receive a proven product for temporary use. The unit for applying biomass includes the following modules:
- The frame on which all units are mounted - power plant, gearbox, mixer, etc.;
- The electric motor is the source of energy for all moving parts;
- Reducer - changes the feed rate of the substance;
- Gateway through which raw materials are fed into the system;
- Baking powder - turns hard briquettes into a soft substance;
- Corrugated hose for transporting cotton wool to the attic;
- Replaceable nozzles for a hose, allow you to evenly apply the product with dry and wet styling;
- The control panel, with its help, the operating mode is configured.
The devices are divided into classes depending on the power of the electric motor. Professional machines process up to 700 kg of material per shift. They are equipped with many functions to make the process easier. Semi-professional pumps up to 80 bags, their capabilities are more modest. Small devices are designed for small amounts of work. In units of economy class, ecowool is poured into the bunker manually.
If you want to buy a device, choose products from reputable companies or firms with good reviews. These manufacturers include: Ekovilla Eggeh - a Finnish company that has been supplying quality goods to Russia for a long time; Isofloc is a world renowned German construction equipment company.
You can buy high quality domestically produced products manufactured at such enterprises as Ekovata in the Moscow region or the Don Industrial Company. They differ from competitors by the use of an automatic component dispenser in production, which increases the stability of the bulk mass.
Selection of ecowool for attic insulation
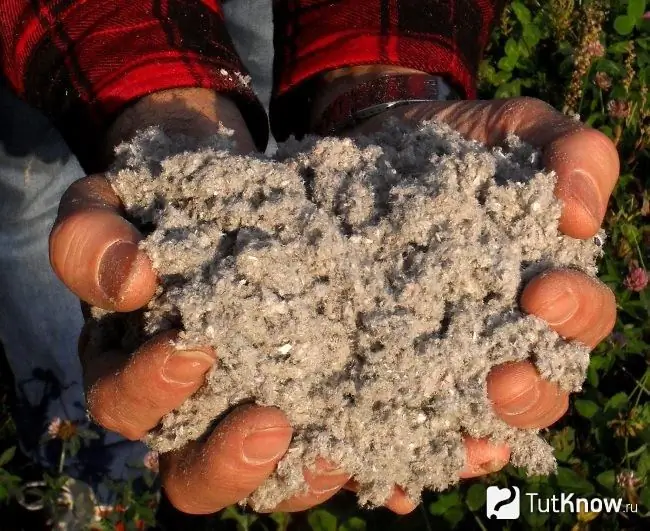
Cellulosic coating is not cheap and not worth buying. In order not to overpay, learn how to correctly determine its quantity.
To insulate the floor of a cold attic with ecowool, it is necessary to form a covering with a thickness of 30-40 cm. This is due to the fact that all the warm air collects in the upper part of the house and the losses through the ceiling are maximum. The roof is covered with a layer of 20-30 cm.
The number of bags of goods can be found by multiplying the volume of the space to be filled by its density, which depends on the technology of laying the cotton wool. With the manual method of installation, the density of raw materials is low - 30-35 kg / m3… If it is supplied under pressure, the density can reach 40-45 kg / m3.
An example of calculating the volume of insulation on the floor: coverage area - 40 m2, layer thickness - 0.4 m, density - 40 kg / m3… Multiply all the values and get the mass of the insulator. Divide the result by the weight of one bag and find out the number of packages of material.
The quality of the product can be assessed only indirectly - visually and by touch:
- Fluff a small piece of raw material with your hands. The material should feel like fluff, not shredded paper. When shaking, small elements should not spill out.
- Large fragments deteriorate the quality of cotton wool: they are poorly impregnated with antiseptics and fire retardants.
- Set fire to a handful of cotton wool, it will start to smolder and quickly go out.
- Make sure the substance is dry. In this state, it retains heat as much as possible.
- Pay attention to the color of the substance. High quality gray material. A different shade means that the composition is missing important components. For example, a lack of borate leads to yellowing.
- Ask the seller for the composition of the cotton wool. Ammonium sulfate becomes a source of an unpleasant odor, in the attic it will be acutely felt. Raw materials with the addition of borax do not smell.
Preparatory work
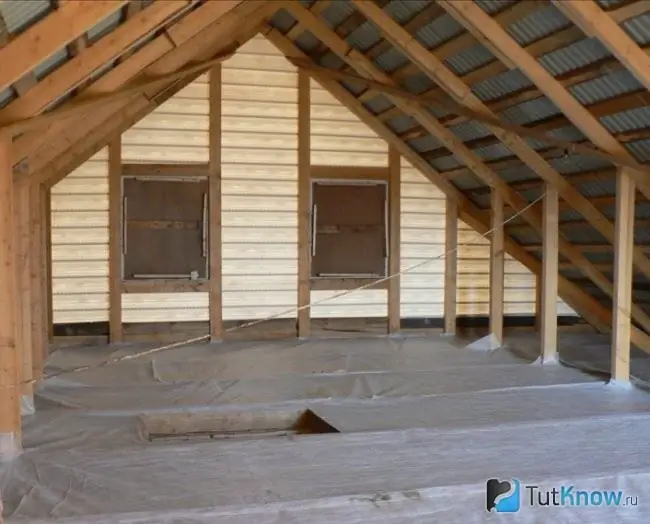
Before applying ecowool, perform the following operations:
- Check the condition of the rafter system. It must withstand the additional load from the insulation and the material from which the "pockets" are created for the bulk mass. Strengthen it if necessary.
- Free the floor from debris. For manual installation, remove the top floor covering. Remove dust with a vacuum cleaner.
- Install protective metal covers near the chimneys and in the places where electrical appliances and cables are placed.
- Cover the floor with foil to protect the insulation from household water vapor. If it is saturated with moisture, it will lose its qualities. In addition, shrinkage is possible. But vapor barrier has its drawbacks. The ceiling on the side of the living area can be damp, so install a ventilation system in the room.
- When insulating the attic with ecowool, avoid drafts, so seal all openings with foil.
Cold attic insulation
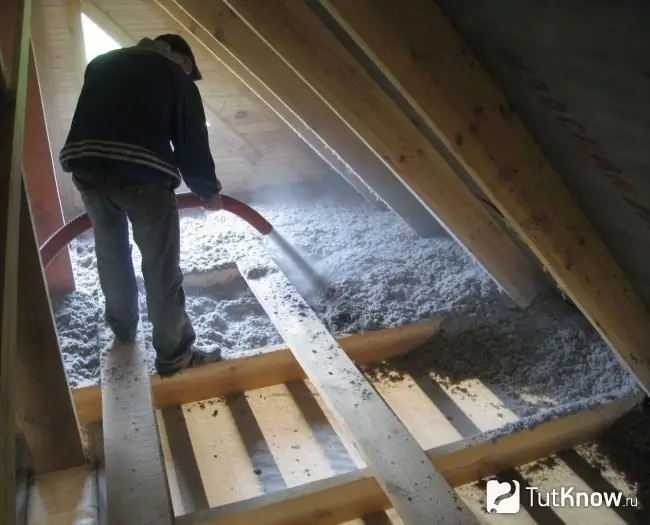
The floor of the room is insulated, if it is not necessary to maintain a positive temperature in it. The insulating layer is applied in two ways - hand or dry. The first option is used in small houses, when it is unprofitable to rent or purchase a blowing machine.
To the beams, from the side of the living space, fix a rigid base - plywood, boards, etc. It must withstand the weight of the coating. Keep in mind that there should be no slots in the surface through which cotton wool spills out, and the floor should be divided into cells, for which, fix the jumpers between the lags. The height of the cells should be equal to the insulation layer 20-30 cm.
Ecowool performs its functions, even when it is highly moistened, but for insurance cover the floor with a vapor barrier membrane and fix it to the beams with a stapler. Lay the canvas with an overlap on the walls and on adjacent pieces. Seal the joints with reinforced tape.
To create an insulating layer, perform the following operations:
- Lift a large container to the attic.
- Pour the compressed ecowool from the bag into it, filling it 1/3 full.
- Loosen the contents with a drill with a nozzle.
- Fill the slots on the floor with a loose mass and compact it. Make sure the cotton wool has filled in all the voids, otherwise the result will be poor.
- Spray the insulation with water. Under the influence of moisture, a crust forms on the surface, which has moisture-proof properties. It is not necessary to wet the biomass if there is no waterproofing film under it. The hardened crust will prevent excess moisture from evaporating.
- After the coating has dried, cover it with a vapor-permeable film with an overlap on the walls and adjacent parts.
- It is not necessary to make walking decks in a cold attic.
The process of thermal insulation can be automated using a dry method of applying raw materials.
Perform the operations in the following sequence:
- Cover the logs with a dense vapor permeable membrane and secure with a construction stapler. Lay the film with an overlap on the walls and adjacent panels, seal the joints. Cells must remain closed on all sides under captivity.
- Run a hose under the plastic from the ecowool maker to the far wall of the attic.
- Adjust the feed and turn on the machine.
- After filling the space, pull out the hose half a meter and repeat the operation.
- At the end of the work, seal the hole through which the hose was pulled with adhesive tape.
- If the cold attic is planned to be used for storage, the gap for blowing out the biomass can be obtained by nailing boards or shields to the logs from above. Make a hole in the deck for the unit's hose and fill the space in the same way as with plastic.
Attic roof protection with ecowool
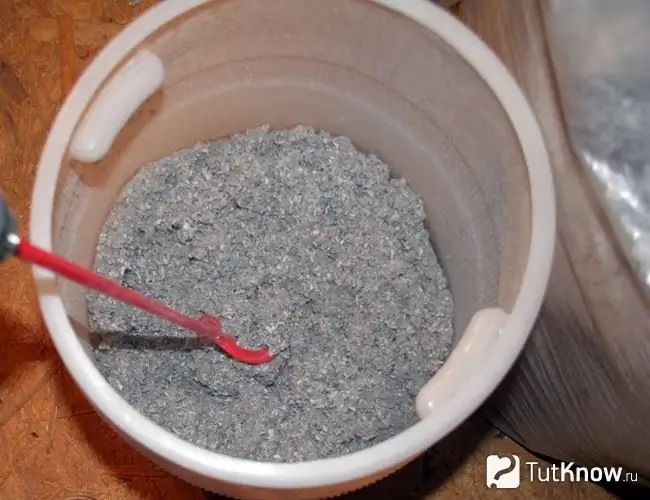
The sloped roof is thermally insulated using a dry or wet-glue method. In the first case, even at the construction stage, sew up the frame and form two cavities - the main one and the ventilated one. The main one is filled with ecowool, and the ventilated one, which is located between the roofing material and the main part, remains free.
To create a gap, do the following:
- On top of the rafters, stuff an edged board 5 cm thick. If the roof covering is metal, cover the board with a vapor-permeable film.
- Fasten thick construction paper to the rafters from below and fix with rails that will prevent the paper from breaking. The second purpose of the slats is that you can attach sheets of drywall to them for decorative cladding. Place the slats perpendicular to the rafters in increments of 30-50 cm.
- Install the corrugated hose between the rafters at the top of the attic. Fill the cavity from bottom to top. The last step is fixing drywall or other material.
- The sloped roof is also insulated with a wet-glue method. It is allowed to work with ecowool at an air temperature of at least +10 degrees and there are no drafts in the room. To keep the raw materials well, add lignin, water, or special glue.
The sequence of work is as follows:
- Nail boards or other sheet material onto the rafters from above. If the roof covering is metallic, cover the boards with a vapor permeable membrane.
- Put a special nozzle on the spray hose for supplying water to the loosened insulation.
- Add the adhesive to the water. It increases the plasticity of the ecowool after drying, reduces the risk of deformation of the coating and increases the adhesion of the base and raw materials. The glue should not be thick.
- Switch on the device, adjust the supply of components and check the quality of the mixture. To do this, squeeze some biomass in your fist. If water appears, the mixture cannot be used - it will fall from the roof. After obtaining the required consistency, direct the mixture stream to the area to be insulated.
- Cover the surface with an even layer. Further operations are performed after it dries, but it is not at all necessary to sheathe the attic from the inside. If it is decided to close the ecowool with plywood or drywall, cut off the parts protruding from the rafters with a sharp knife or a special roller device. After processing, a perfectly flat surface will be obtained. Waste can be re-loaded into the machine.
- Fasten the board material to the rafters.
How to insulate an attic with ecowool - watch the video:
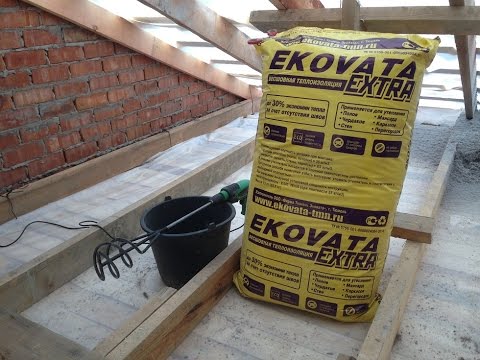
From the information provided, we can conclude that the crushed cellulose insulation is a high-tech material that is easy to install. It has no competition as an insulator for warm attics with a roof of any complexity.