Pros and cons of using ecowool for floor insulation, installation methods, the choice of equipment for applying insulation, calculating the required amount of material. Thermal insulation of floors with ecowool is the use of a cellulose-based material to create a seamless, uniform heat-insulating layer. Modern technologies make it possible to complete the work in the shortest possible time with high quality. The methods of applying the substance to the base will be discussed in our article.
Features of work on floor insulation with ecowool
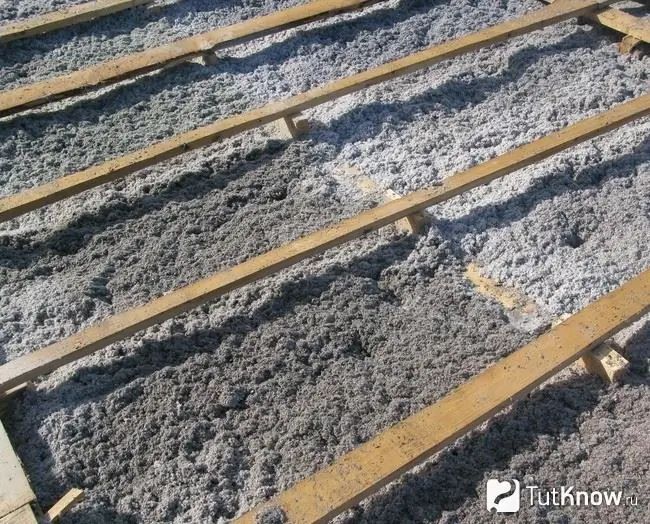
Ecowool is a soft heat-insulating material consisting of 80% fine wood fibers and special additives. Most often it is made from waste paper. During production, boric acid is introduced into the pulp, which does not allow the product to burn, and sodium tetraborate, which protects against microorganisms.
Ecowool is sold in dry form, pressed into briquettes or in bags, slightly compacted, therefore, it must be fluffed before the process. It is recommended to prepare it for use and feed it to the place of laying in a mechanized way. Manual mixing and installation is allowed for finishing small areas, which saves money on rent or purchase of expensive equipment.
The material has low rigidity, and it is not worth walking on it. Before insulation, a wooden frame is mounted on the base, which perceives the mechanical load. The support structure is often made in small, rigid-walled cells.
The substance retains its qualities at a humidity of 20%, therefore it is used in rooms with a sufficiently high moisture level, in which there is a risk of condensation.
Advantages and disadvantages of floor insulation with ecowool
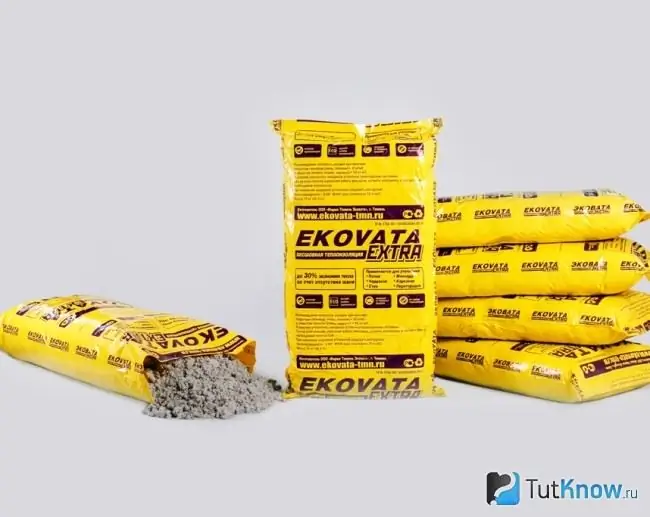
The material has numerous advantages, thanks to which it is very popular among users:
- The product is multifunctional. A layer of substance on the ceiling of a multi-storey building not only insulates it, but also insulates it.
- The fibrous structure adheres well to any surface. It forms a resilient mass that, when properly installed, does not sag.
- The material is impregnated with antiseptics, harmful to fungus and mold. Mice do not live in the insulating layer.
- It retains its qualities even at 20% humidity, and vapor barrier is not required when laying on the floor.
- Cold bridges never remain in cotton wool. The mixture is supplied in a hose under pressure and fills all voids.
- Working with the substance does not require personal protective equipment.
- Installation of the product is carried out as soon as possible.
- Insulation requires a small amount of wool - 28-65 kg / m3.
- After warming, there is no need to wait for the raw materials to dry. Finishing can be done immediately after application. In addition, it is allowed to work at any temperature and humidity.
- The use of special devices allows you to quickly cover large areas.
Thermal insulation of ceilings with cellulose has a number of disadvantages that the owner of the house should be aware of:
- Before insulating floors with ecowool, the installation site must be carefully prepared. The preliminary work is time consuming.
- The substance is made from waste paper, but the technology is quite complicated, so its final cost is much higher than products for a similar purpose. In addition, the process of warming requires special expensive equipment.
- Despite the presence of antipyrine in the composition, cotton wool begins to smolder under the influence of an open fire. To avoid troubles, it is not recommended to use it in fire-hazardous premises. Places near the stove should be protected with asbestos or basalt mats.
- Over time, the cotton wool shrinks, so they fall asleep with a margin.
Ecowool floor insulation technology
The insulator is laid in two ways - mechanized and manual. The first option involves the use of special machines, the second - only improvised means. Read more about blowing devices and the method of insulating the floor with ecowool below.
The choice of equipment for the installation of ecowool
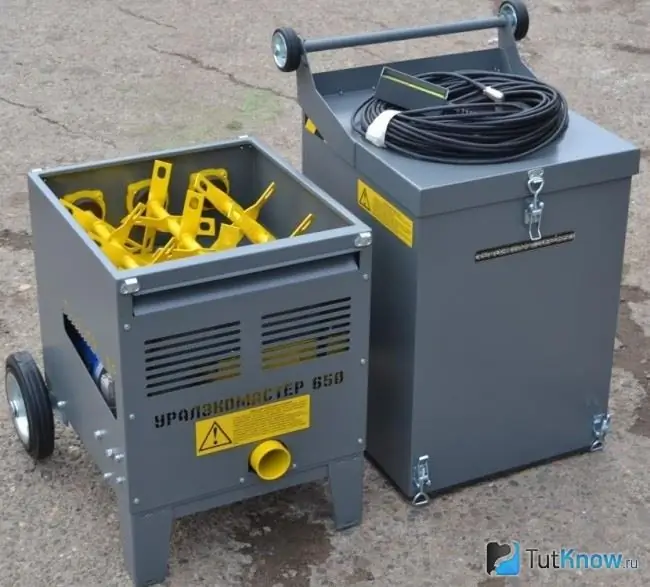
Raw materials must be fluffed to a homogeneous consistency before laying. Only in this state does it have the necessary insulating characteristics. Mechanization of the process involves the use of special devices that automatically loosen the material and supply it with air through the pipe to the ceiling.
A typical blow molding device looks like this:
- The platform on which the motor, gearbox, blower and other components are mounted.
- The electric motor with a gearbox can be of two or three stages. This scheme allows the buyer to choose products in terms of performance and power. Typically, the power plant operates on a low current, which ensures the quietness of the machine and its durability.
- Gateway - designed to grab cotton wool and fluff. From it, the working mass is fed into the hose.
- Funnel - for loading material into the device.
- Damper - allows you to regulate its supply to the sluice.
- Baking powder - fluffs up the compressed substance.
- Remote control - to control the installation. In many products, the biomass speed and feed can be changed remotely.
- Emergency stop switch - to quickly stop the machine.
There are several classes of blow molding machines that differ in performance. Professional devices include devices that pump at least 700 kg of substance per hour. They have the greatest degree of mechanization of the process. Semi-professional models allow to blow out about 80 bags of ecowool. Budget options are designed for a small amount of work. In these machines, the material is loosened and fed to the turbine manually.
Homemade appliances can be used in place of factory-made blowers. For example, a garden blower model Elitech BC 2000 is suitable for this purpose, but with a slight modification.
To prepare it for work, follow these steps:
- Move the terminals from one part of the product to another to amplify the power of the device.
- Remove the teeth on the dust collector tube. If left untouched, the cotton wool will cling and clog the hose.
- Connect the corrugation to the hole of the fixture and secure with tape. Buy a hose with a diameter of 63 mm and a length of 7 m.
- Put a thick cloth glove on the pipe and cut off the part with your fingers. It seals the gaps between the hose and the floor opening to prevent fiber spraying in the room.
Selection of materials for floor insulation
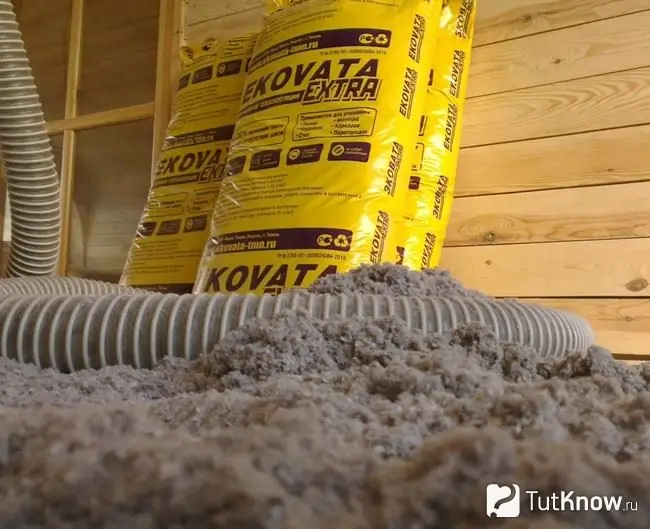
Before insulating the floors in the house with ecowool, decide on the thickness of the insulating layer. You can choose it according to our recommendations:
- The thickness of 10-15 cm is sufficient to prevent heat leakage on the floors. In the northern regions, it is increased to 20 cm.
- The floor of the non-residential attic and the attic is insulated with a layer of 30-40 cm. The increase in the heat-insulating layer on the upper floor is due to the fact that warm air rises and the greatest losses will be in the attic.
For manual filling, the permissible density of the material is 30-35 M3, for blowing in - 40-45 M3.
To calculate the exact amount of raw materials, multiply the floor area, the layer thickness and its density. Choose the last parameter 45 kg / m3.
Calculation example: if the area is 20 m2, the layer thickness is 0.2 m, then ecowool for the floor will need 10x0, 2x0, 45 = 90 kg. Having learned from the seller the weight of one bag, you can determine their quantity.
The material does not have a GOST for manufacturing, therefore the composition of the insulation differs from different manufacturers. It is not possible to check the compliance of the actual characteristics with those declared upon purchase; the quality of the goods can be assessed only visually.
Useful recommendations when choosing ecowool:
- Outwardly, it looks like fluff from small fragments. They shouldn't feel like cut paper or powder to the touch.
- When shaking, fine elements do not fall out of the workpiece.
- Do not buy a product with large parts, they are poorly impregnated with protective equipment.
- When trying to set fire to ecowool, it smolders for a short time and goes out.
- The material should be stored in its original protective packaging.
- Buy only dry fibers.
- The normal color of the insulation is gray. A yellow or light shade means that it contains low-quality raw materials. In most cases, the deterioration in performance is due to savings on the most important components - borates.
- Find out what kind of flame retardant was added to the product. Borax or borax is considered acceptable. If ammonium sulfate with boric acid is present, a strong unpleasant odor will appear in the room after installation. In addition, raw materials with such inclusions quickly lose their quality.
It is advisable to use the goods of trusted manufacturers. Before purchasing a product with an unknown logo, it is recommended that you collect as much information as possible about the manufacturer. Information of interest can be found on construction forums.
Reputable companies that deal with ecowool include:
- Ekovilla, Tertech are Finnish manufacturers who have been supplying products to the Russian market for over 30 years.
- Isofloc is a German company that sells the highest quality products all over the world.
- In Russia, one can distinguish the companies Ekovata (Moscow region), Ekovata (Chuvash Republic), Don Industrial. In these companies, products are manufactured on equipment with automatic dosing of components. This technology guarantees the stability of the heat insulator.
Manual laying of ecowool on the floor
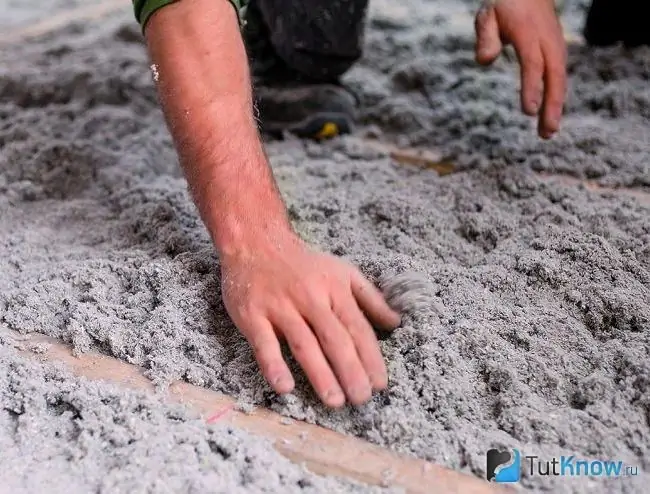
It is recommended to treat the floors of small rooms in this way when the use of blowers is not economically feasible. Lags should be fixed on the base, preferably with jumpers for better sealing. If the work is carried out in a residential building, remove the flooring boards, because ecowool is placed on the floor only from above.
The fibrous mass is not afraid of high humidity, but no one forbids covering the base with a waterproofing film.
The minimum cell depth for insulation can be determined based on the requirements for its thickness in the previous section. In order not to increase the consumption of the substance, mount the subfloor at a given depth.
Perform further work in this order:
- Transfer the required amount of cotton wool into any container with a volume of more than 50 liters and beat for 5 minutes with an electric drill with a mixer attachment. Can be mixed in the same bag in which it was purchased. Please note that when fluffing, the substance increases 2-3 times. The finished mass resembles ordinary cotton wool or shavings and is kept in a heap if squeezed into a handful.
- Pour the substance between the beams slightly above the level of the lags. Tamp material periodically to fill any voids. Otherwise, it will lose some of its insulating properties.
- Process the cotton wool between the joists again with a drill with a nozzle. Align the fragments into cells using the rule.
- Moisten the top layer of cotton with water from a spray bottle. It activates lignin, which is part of cellulose. Under its action, the fibers stick together and form a thin crust that increases moisture resistance and prevents moisture from penetrating inside.
- After a few days, when the coating is dry, cover it with a waterproofing film.
- Install the flooring and then the floor covering.
Mechanized installation of ecowool on the floor
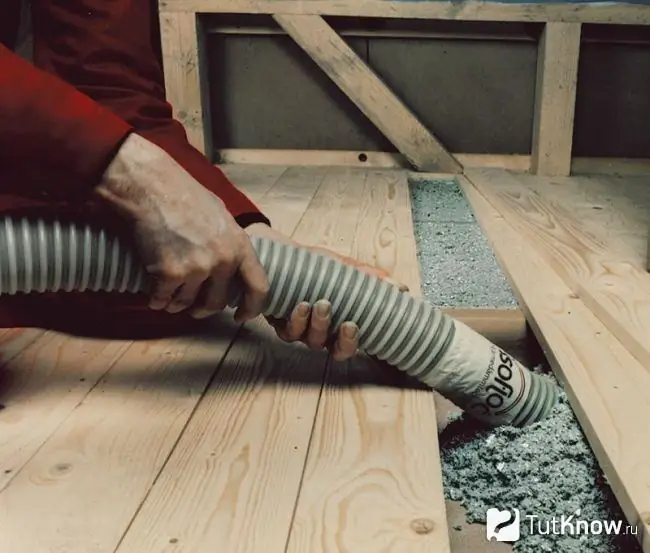
To cover the base in a mechanized way, it is necessary to have a flooring, which creates an enclosed space under the partition. In the board in an inconspicuous place, make a hole for the hose of the device.
The technology of floor insulation with ecowool is as follows:
- Insert the hose into the hole, move it all the way to the wall of the room, and then push it back half a meter.
- Seal the gap between the pipe and the floor using available means.
- Pour cellulose into the blower container.
- Set the operating mode of the product and turn it on.
- After the space between the pipe and the wall is filled (this is determined by the change in the blowing noise), pull out the hose half a meter and continue feeding the mass under the boards.
- At the last stage, the hose should enter the gap by 1 cm.
- Fill up the hole in the floor.
Air blowers can be used even with an open method of insulation. But it will not be possible to create the necessary density by feeding from a hose, so from time to time the material has to be pressed manually.
If using a homemade device, grab the fibers a little at a time, otherwise the machine will not have enough power to move the mass.
How to insulate the floor with ecowool - watch the video:
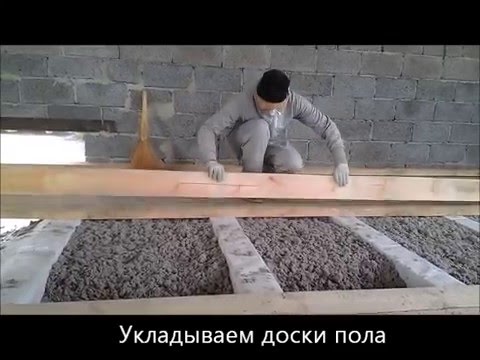
The above methods of stacking cellulose and its characteristics show that the material is no worse than traditional heat insulators, and in terms of environmental friendliness and wastelessness it has no equal. If you are insulating the floor with ecowool with your own hands, study the features of the process and determine which method of application is economically beneficial for you.