Advantages and disadvantages of wall insulation with sawdust, compositions of solutions based on dust, rules for choosing components for forming an insulating layer, methods of laying the material. Insulation of walls with sawdust is the use of sawn timber waste to create an insulating layer for partitions. Loose mass belongs to environmentally friendly and economically beneficial substances. After special treatment, small fragments acquire good insulating properties and have long been used to retain heat in a room. Modern heat insulators have replaced dust, but this method is still popular in the private sector. In this article, we will consider common options for creating protective coatings based on this substance.
Features of using sawdust for wall insulation
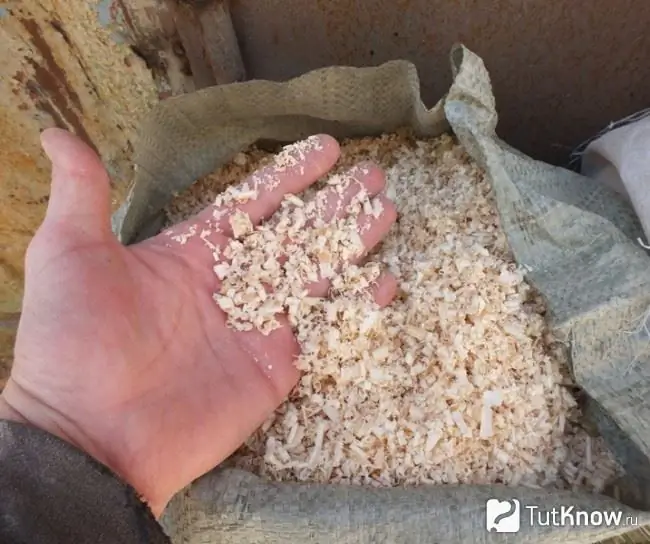
Sawdust is wood waste particles obtained after sawing. Loose mass is considered a universal insulation, but is most often used in one-story houses, saunas and houses with attics.
The most cost-effective options are to pour a thick layer of rubbish or a mixture based on it into the internal openings of the structure or cover the partitions from the outside. Wall insulation with sawdust can be performed at all stages of construction and operation of the building.
In some cases, clean sawdust increases the risk of fires, for example, if the partitions are very high and there are no fire bridges. When a fire source appears, an increased thrust arises, contributing to the rapid spread of fire. When laying electrical cables, arranging sockets and switches, the wires must be carefully insulated.
For wall insulation, use pure material or mixed with other components to change its properties and improve the result. For example, to extend the service life, the waste is impregnated with antiseptics, fire retardants and other means.
Some technologies involve the construction of a frame to hold the insulating "pie", which greatly complicates the work, but at the same time reduces the financial costs of repairs.
Advantages and disadvantages of wall insulation with sawdust
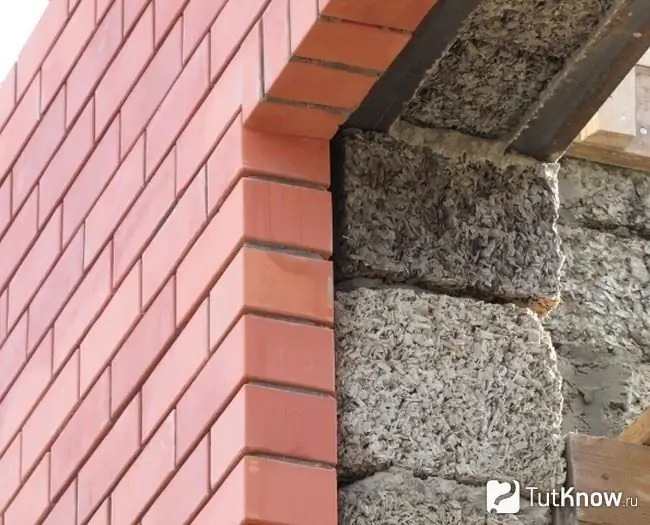
Dust has long been considered the best way to insulate a house. The advantages of this method of isolation include:
- The absence of components harmful to humans. For the preparation of the solution, natural materials are used, such as clay, sand, lime, sawn timber waste.
- Low cost of trash. The costs will only go towards the delivery of raw materials.
- Long-term operation of the sawdust coating.
- No need to have experience with these materials. No special equipment is required to perform operations.
- Very low thermal conductivity of the insulating "pie". Such properties are passed from the solid wood.
This isolation has a number of disadvantages. The following properties are considered the most unpleasant:
- Sawdust burns well and belongs to materials with increased fire hazard.
- They become a shelter for mice, and are quickly damaged by fungus and mold.
- The insulation layer shrinks, it is necessary to periodically check its condition and fill the voids.
- The dust quickly absorbs moisture. A waterproof, vapor-permeable film is required to protect the substance.
Wall insulation technology with sawdust
It is not easy to attach a covering made of bulk material to a vertical surface. The technology of work requires strict adherence to the sequence of operations, otherwise the effect of using the substance will be minimal. The quality of the components will also affect the result. Information on how to properly insulate walls with sawdust is given below.
Choice of materials
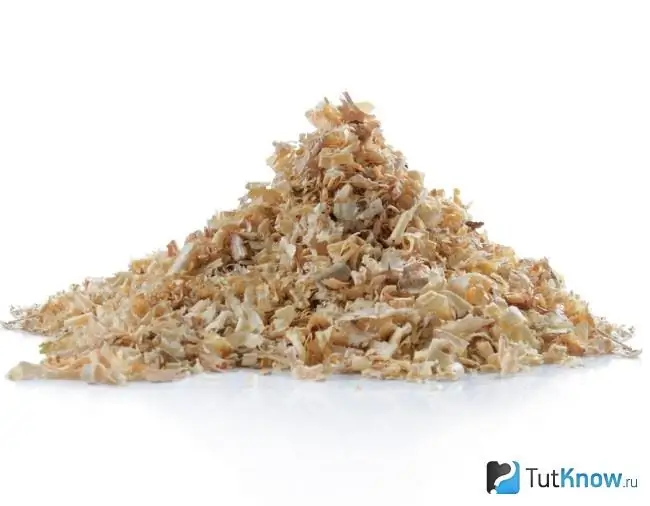
To keep the heat out of the wall, use only high-quality components to create a protective coating. When choosing ingredients, the following information may be helpful:
- One of the options for insulating the walls of the house with sawdust is dry backfill. In this case, waste from carpentry workshops is considered ideal, where they work only with high-quality dried wood, without rot and bugs.
- To prepare a solution of sawdust with cement, dust obtained a year ago is needed. During this time, special substances will leave the composition, which do not allow the cement to adhere to the fragments qualitatively.
- Discard raw bark. It contains a lot of insects that can damage wooden structures.
- Sawdust comes in different sizes. Fractions that are too small are heavy and dusty when stacked. Large particles do not retain heat well, and a lot of cement goes into the solution. For the same reason, don't buy shavings. Fragments of medium size, devoid of these disadvantages, are considered the best option.
- The lightest material is from coniferous trees. It contains a resin that keeps mold and mildew out. The heavier substance remains after the cutting of deciduous and fruit trees.
- To insulate a bath, waste of larch or oak mixed with ash is considered the best. This composition resists moisture well.
- Choose a greasy clay for mortar, it fills the voids well. It can be determined by stretching the lump in your hand. It is as slippery as soap and pliable to the touch.
- Waste obtained from sawing or processing natural wood is suitable for bookmarking. Do not use dust chipboard, MDF, OSB and other materials for furniture production, which include chemical additives. The reason is too small fractions, practically it is dust.
Preparatory work
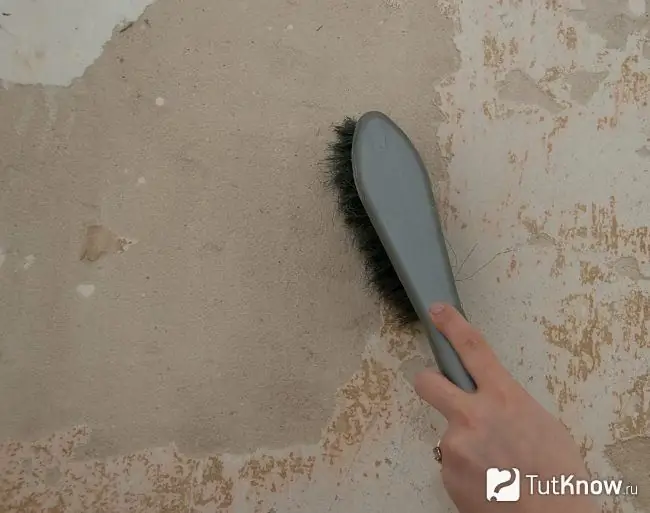
Before insulating the walls with sawdust, inspect the partition and determine the possibility of using this method of insulation. It is allowed to cover only those structures that are made of vapor-permeable material. They should not have products that block steam - polyethylene, roofing material, rubimast.
Perform the following work:
- Clean the surface from dirt. Make sure there are no sharp elements that could damage the vapor barrier membrane.
- Cover the wooden elements with special compounds to protect them from moisture, insects and fire.
- Fill up gaps and openings.
- If the insulation is planned to be laid using a crate, cover the wall with a waterproofing film with vapor-permeable properties.
It is not recommended to use sawn timber waste without preliminary preparation, they will quickly fail.
Treat the dust as follows:
- Saturate the substance with special agents to protect it from rot, fungus, insects, rodents and fire. To do this, cover with plastic wrap under the canopy. Put a layer of sawdust on it, add an antiseptic and stir. The most popular protective agents are copper sulfate and boric acid. They are added in the proportions indicated in the manufacturer's instructions. It is not recommended to use copper sulphate if the bath and sauna are insulated, because when heated, chemicals give off harmful vapors.
- Dry the raw materials, add a flame retardant and repeat the operation. Wait for the mass to dry and add slaked lime to protect it from insects and mice. Take the components in a proportion of 5 parts of sawdust to 1 part of lime. Mix the solution thoroughly.
- If dry laying is planned, the sawdust is thoroughly dried. The procedure is usually performed in the summer. Pour the loose mixture under the canopy so that the sun does not fall. You cannot cover it with foil. The substance should be stirred at short intervals. By the fall, a small percentage of sugar will remain in it, which reduces the likelihood of decay.
- Remove large fragments, it is recommended to pass the material through a sieve.
- Sawdust for wet solutions need not be dried.
Filling internal wall cavities with sawdust
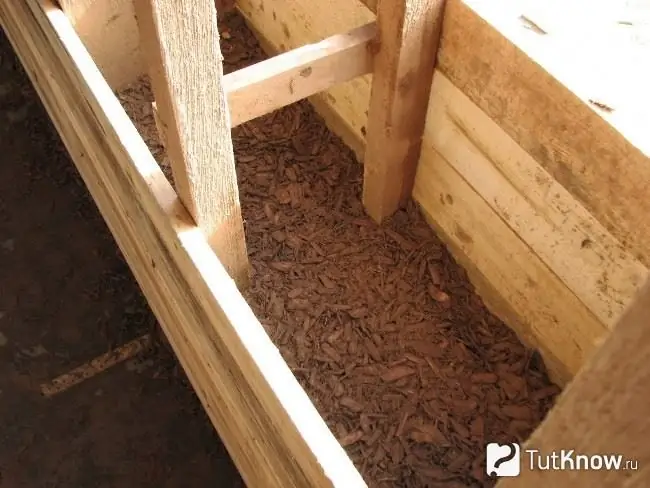
When erecting a frame house, partitions are often made of two layers of boards, and the resulting openings are filled with bulk material. To prevent dust from moistening from fumes from a warm room, glassine or other insulator is placed on the wall from the inside. The void filling mixture is prepared in several ways.
For dry backfill, it is necessary to prepare components in the following proportion: 90% dry sawdust and 10% lime-fluff to scare away rodents. Stir the ingredients until a homogeneous mixture is obtained. Backfill the walls with sawdust to the top with a small compaction. After a while, such a composition gives a large shrinkage, so raise the walls 200-300 mm above the planned level and fill it completely with the composition. After shrinkage, the additional mass will prevent voids from appearing. To seal the gaps under the windows, make the window sills retractable.
To avoid shrinkage, substances are added to the sawdust that harden over time. The solution is prepared from slightly damp dust and solid ingredients. A popular mixture of 85% sawdust, 10% lime-fluff and 5% gypsum. You can use other compositions: 1 part sawdust, 0, 3 parts gypsum or ground boiled and 2 parts water; 1 part sawdust, 0, 4 parts gypsum and 2 parts water.
Instead of fluffy lime, lime dough is sometimes added, but they take twice as much, reducing the percentage of water.
Prepare a wet backfill as follows: alternately pour sawdust and an astringent into a wide container and mix first dry, and then again after adding water. The mass must be quickly laid in a regular place and lightly tamped. After 3-5 weeks, the insulator will become completely rigid.
Laying sawdust on the frame
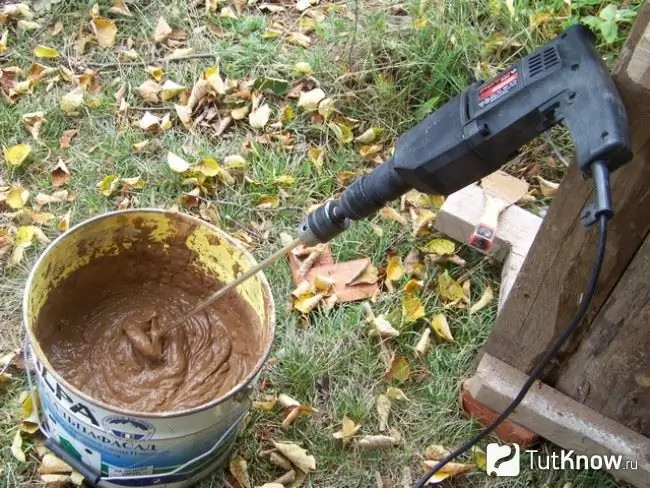
Fastening a thick layer of sawdust to the surface is problematic, so a frame is made. The dimension between the batten wall and the ceiling must be equal to the thickness of the insulating coating. The constructions are made from treated boards with a section of 100x50 mm. With internal insulation, the frame is made of aluminum profiles, to which drywall is fixed.
For houses with an area of 28-35 m2, designed for temporary residence in winter with a frost of 15-20 degrees, the insulation layer should be 15 cm. To live permanently, increase it to 25-30 cm. More precisely, the thickness can be determined by the formulas in GOST.
In the calculations, there is the size of the bearing wall, the thermal conductivity of the material from which it is built, the coefficient of the climatic conditions of the region. The result should be equal to the acceptable value for your area. The missing indicators are eliminated by increasing the insulation layer.
To fill the battens, it is recommended to use wet mixtures of prepared sawdust (10 parts), cement (1 part) and water (5-10 parts). The volume of the liquid depends on the moisture content of the sawdust.
The order of work is as follows:
- Handle sawdust and cement dry in a clean container. The process can be mechanized if there is a concrete mixer.
- Pour some water into the container and mix thoroughly. In the finished solution, the dust should be smeared with cement. It is considered to be of high quality when it does not crumble after being clenched in a fist. If water leaks out and the lump breaks apart, add shavings or leave for 24 hours to evaporate the liquid.
- Lay the mixture in layers of 20-30 cm with tamping. Perform sealing with high quality, otherwise there will be voids through which heat escapes.
- The hardening of the mass at a temperature of + 20 + 25 degrees will begin in 1-2 weeks and lasts a month. At this time, it is necessary to provide fresh air access to the wall and control the shrinkage of the mixture. If voids appear, fill them with the same solution. To shorten the drying time, it is best to do the work in the summer.
Instead of wet mixtures, the cells can be filled with dry prepared sawdust, periodically tamping them. Also, a glue based on carboxymethyl cellulose is added to dry dust for weighting. The result is non-flammable granules that do not shrink and retain heat well.
After filling the cells, sheets of plywood are attached to the racks of the crate (from the street side), and a windproof material is attached to it. Next, you need to build a ventilation system. To do this, fix the 40x40 mm thick slats to the plywood, to which the cladding is nailed - siding or block house.
Instead of a permanent frame, removable panels with a height of 1000 mm can be used. They are located between the drains of the frame, forming cavities of 200-250 mm along the main wall of the house. Fill the gap with a damp mixture and tamp it down. After drying, remove the boards, install them on the already frozen formwork and fix them. Then repeat the operations.
Thermal insulation of walls with plaster
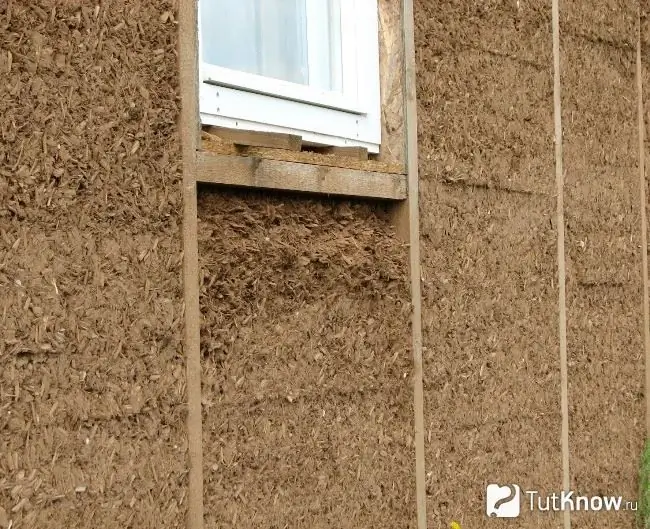
A mortar of dust and clay can be glued to the wall without a crate, if the components are selected correctly. To do this, prepare materials in the proportion: 2/3 buckets of sawdust to 1 bucket of clay.
Perform the work in the following sequence:
- Pour clay into a large container and cover with water in a 1: 1 ratio. Leave it to soak for a day.
- Stir the mixture until smooth. Add water if necessary and let sit again for 5-6 hours.
- To mix clay with sawdust, you need a 150-200 cm high rimmed trough. Pour the ingredients for one portion into it and mix. Work will go faster if you use a concrete mixer.
The method of applying the mixture depends on the design of the partition.
First install the insulator alignment beacons on the drop wall. Throw in the solution and level with a trowel. It will stick more reliably if the surface is covered with shingles. This design can hold a layer no more than 30 mm thick. After the sawdust has dried, cover with a sand-cement mortar, and then with plaster.
Installation of sawdust blocks
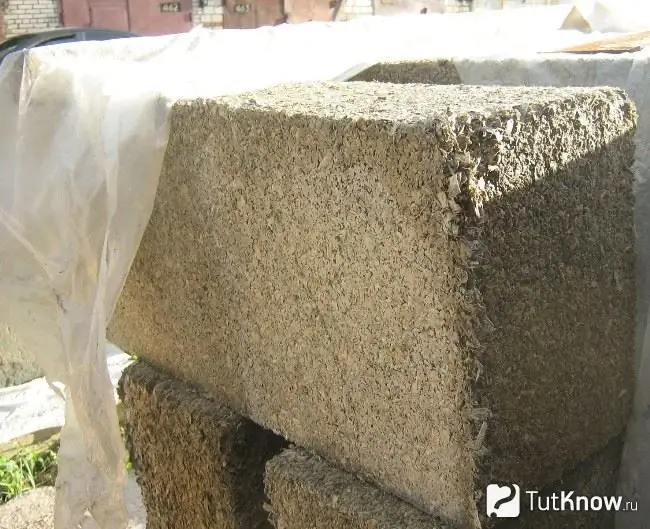
Sawdust and binder can be used to make rigid blocks for wall cladding. The most convenient for work slabs with dimensions of 50x50 or 70x70 cm with a thickness of 5-10 cm. In cold regions with a temperature of minus 30 degrees, the thickness is increased to 300-400 mm.
To prepare the bricks, you will need wooden molds of the required size.
The work is performed in the following sequence:
- Prepare a 1: 1 mixture of sawdust and clay. The process is described in the previous section.
- Place plywood on a flat surface and cover with plastic wrap.
- Set the shape on top.
- Fill the cells with the mixture and seal. Cut off the protruding mass with a rule flush with the walls of the form.
- Leave the blanks for a while until hardening, then remove the mold. Further cooling will take place without it.
- Replace the vacated forms in a new place and repeat the operations.
- Products cannot be dried in the sun, only under a canopy. If you leave the workpieces in the open, the clay will crack. Blocks dry for 4-5 weeks.
- To fix products with a thickness of 100 mm, fix a batten of the same thickness to the wall. Place the blocks between the frame rails and press them with bars that are nailed to the frame racks.
- If the thickness of the blocks is 300-400 mm, they are laid on the clay-sand mixture like brickwork, leaving a gap of 70-100 mm to the partition. After the insulation is erected to a height of 1000 mm, fill this opening with expanded clay. Raise the insulator another 1000 mm and repeat the operation. The process ends when the entire structure is covered.
- At the end of the process, plaster the surface with cement mortar.
How to insulate walls with sawdust - watch the video:

Insulation of walls with sawdust is more laborious compared to the use of prefabricated insulators. But the result will pleasantly surprise the owner, and the time spent on work will not be a pity.