Thermal insulation of the foundation using sawdust, its features, pros and cons, preparation of the material for work and the technology for its implementation.
Preparation for work
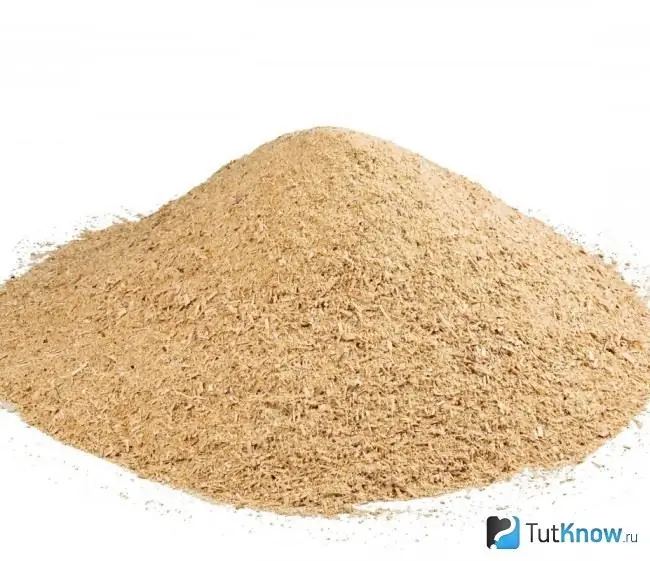
Before starting work on the insulation of the foundation, it is necessary to prepare the source material. To minimize the impact of organic elements on Portland cement, shredded wood is subjected to chemical or physical treatment. The simplest treatment is the oxidation of organic matter in air, preferably under the influence of sunlight. In this case, some organic elements are oxidized immediately, the rest ferment at first, then partially crystallize, forming insoluble forms. The disadvantage of this method is the duration of the process, which can be 2-3 months for coniferous sawdust and more than six months for deciduous.
Another way is water treatment of shredded wood. In this case, it is specially soaked or left in the rain for a long time. This method is similar in time to the previous one.
Most often, the method of impregnation of sawdust with liquid glass or CaCl is used. However, despite the rapid hardening, sawdust with water glass is less durable than the same material impregnated with calcium chloride. In the latter case, quality wood must be well seasoned.
The technology of warming the foundation with sawdust
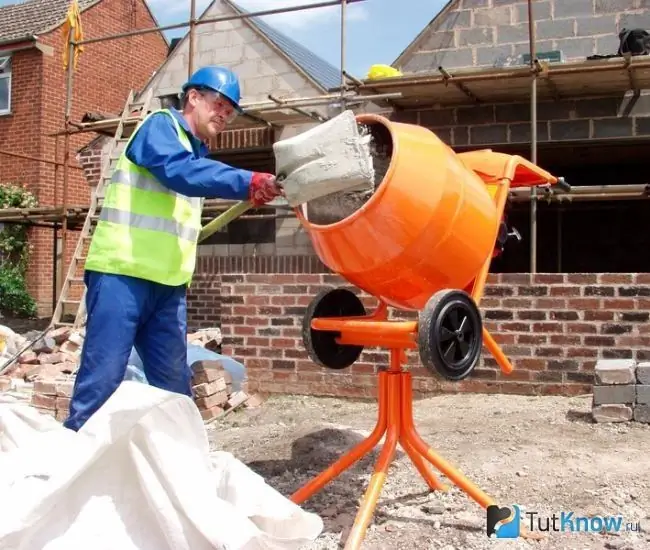
For the construction of a warm foundation, the most rational way is to manufacture it directly from a cement-sawdust mixture, which is placed in a prepared formwork similar to ordinary concrete.
To obtain sawdust concrete, you will need cement, sand, water, sawdust, a concrete mixer and a vibration rammer to compact the mixture in the formwork. The density of sawdust concrete is regulated by the ratio in the mixture of sawdust and sand. Moreover, the more sand is present in it, the stronger, but less warm, the foundation will turn out. To make the material stronger without losing its insulating properties, chopped straw is added to the mixture.
For a warm foundation, M5 sawdust concrete is used in the form of a mixture for laying in formwork or ready-made blocks. To save cement, a small part of it is replaced with lime.
You can get a high-quality mixture by adhering to the following recipe:
- Wood sawdust - 220 kg / m3;
- Slaked lime - 600 kg / m3;
- River sand - 1550 kg / m3;
- Cement m400 - 1200 kg / m3.
The volume of water required when mixing these components depends on the initial moisture content of the sawdust and should be on average 250-350 l / m3.
The process of preparing the working mixture is as follows:
- Lime, Portland cement and sand are thoroughly mixed in a concrete mixer until a homogeneous dry mixture is obtained;
- Add sawdust and mix again;
- Gradually add water without turning off the concrete mixer.
The finished mixture is easy to check for readiness. To do this, her taken lump must be squeezed in her hand. If, at the same time, water does not come out of it, and with unclenched fingers, it does not crumble, this indicates that the sawdust concrete is ready for use. In this case, it can be pressed into block molds or laid in formwork.
The mixture hardens within 3-4 days. The optimum temperature of this process should be at least +15 degrees, which is a prerequisite for achieving maximum density of sawdust concrete. Complete polymerization and drying of the warm foundation will end in 90 days. There should be no cracks on its surface.
How to insulate the foundation with sawdust - watch the video:
[media = https://www.youtube.com/watch? v = l9uRepr3s_g] When the foundation is insulated with sawdust, the material can absorb moisture from the soil. However, this problem is successfully solved by insulating the buried walls with moisture-resistant compounds or using roll products based on bitumen.