Thermal insulation of a concrete floor with expanded polystyrene, mineral wool, expanded clay, insulation installation technology. Insulation of a concrete floor is a great opportunity to make your home comfortable. Thermal insulation is essential for all surfaces in a living space. However, about 20% of the heat escapes through the floors, especially in the house. By protecting them from warm air leaks, you will save on heating and will be able to walk barefoot instead of wearing woolen socks.
The choice of insulation for a concrete floor
The market for modern thermal insulation is large. These are both natural and artificial insulation made using the latest technologies. Among the heat-insulating materials suitable for a concrete floor, it is worth noting expanded polystyrene, expanded clay, mineral (basalt) wool, ecowool, polyurethane foam (PPU).
Expanded polystyrene for thermal insulation of concrete floors
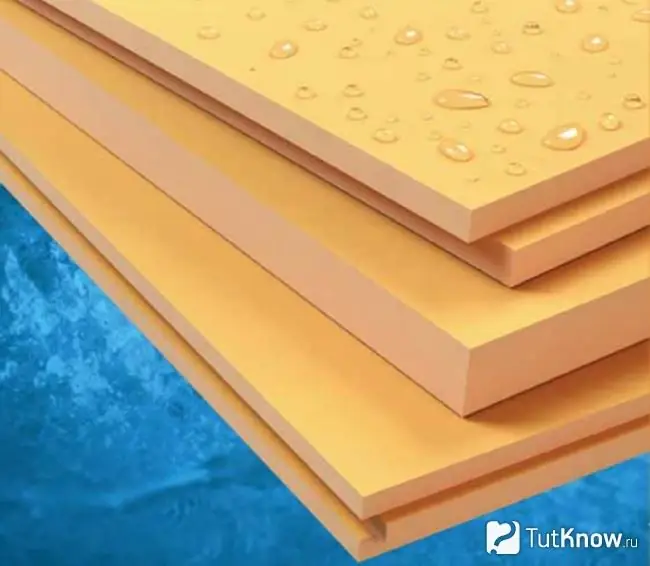
In construction, two types of this material are used - polystyrene and polystyrene foam. Without going into too much, you can equate them. But this is not true, since heaters, despite the external similarity (ease of installation, low weight, to the touch), are different.
Penoplex (extruded polystyrene foam) has closed pores. The insulation itself has a dense homogeneous structure, does not crumble, has a good density to bending (the foam cannot be bent at all, it will burst and crumble into small pieces). It is more convenient to work with penoplex, because it is cut with a hacksaw and does not fall apart.
Both penoplex and polystyrene are derived from polystyrene. And if the first passes through a special form (extruder), acquiring the final appearance by forcing through it, then the foam is just inflated polystyrene balls, sintered together at high temperatures. In the process of foam production, polystyrene undergoes significant changes, turning into a single viscous mass (hence the properties inherent in a solid substance), while the foam remains separate balls.
According to technical characteristics, extruded polystyrene foam is better:
- Strength - 0.18 (MPa);
- Thermal conductivity - 0.032 (W / m * K);
- Water absorption - 0.4%;
- Flammability class - G3, G4;
- Working temperatures - -50 + 75 ° С.
However, to insulate a concrete floor with expanded polystyrene, the correct solution would be to choose its usual type - polystyrene foam. It is much cheaper, and under a finished floor or under a leveling concrete screed, its characteristics such as weak strength, rather high water absorption and flammability will not make any difference. Do-it-yourself styling is not difficult.
Expanded clay for concrete floor insulation
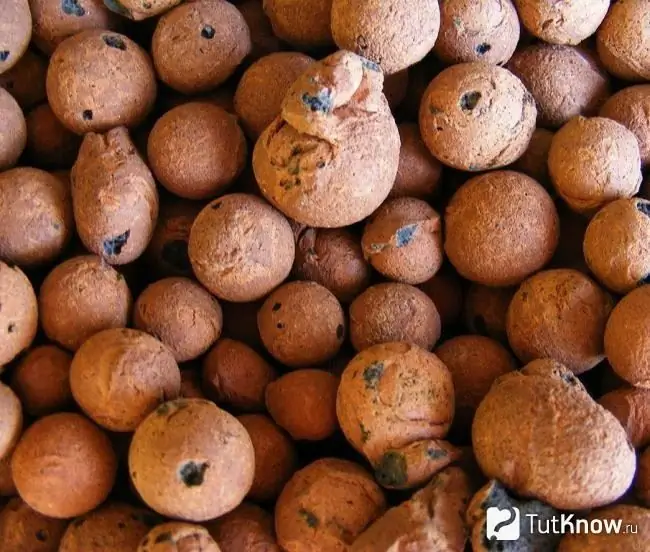
Natural baked clay insulation. There are different fractions - gravel, crushed stone, sand. Warming of a concrete floor with expanded clay is carried out with gravel of various sizes. To achieve the required level of thermal insulation, a layer with a thickness of at least 15 centimeters is required.
Technical characteristics of expanded clay:
- Density - 250, 30, 350, 400, 450, 500, 600 (kg / m3);
- Strength - 1, 2 - 2, 5 (MPa);
- Thermal conductivity - 0.1-0.18 (W / m * K);
- Water absorption - 8-20%;
- Flammability class - NG;
- Working temperatures - up to + 1300 ° С;
- Frost resistance - at least 25 cycles.
Expanded clay requires mandatory double-sided protection against moisture penetration!
Mineral wool and ecowool for thermal insulation of concrete floors
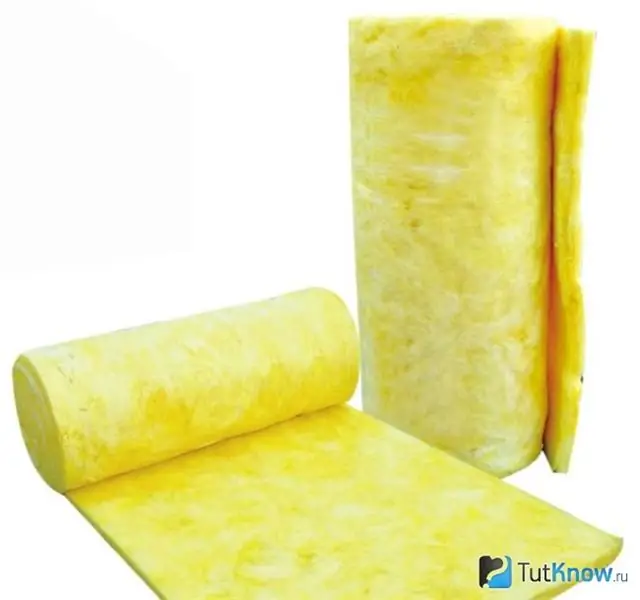
These are two different insulation materials, both in composition and in properties. Mineral wool is produced from waste rock (stone, basalt), slag (slag wool), quartz (glass wool). Ecowool is the smallest fraction of waste paper, supplemented with fire retardants and water-repellent agents (borax and boric acid).
Basalt wool refers to non-combustible insulation, but it is expensive. Therefore, concrete floors are usually insulated with the cheapest type of mineral wool - slag or glass wool. Not used under a concrete screed. Do-it-yourself styling is not difficult. On top of the insulation, wooden floors are laid.
Ecowool has excellent technical characteristics and is inexpensive. Flammability class - G2, G3. Has a fairly high water absorption, is not used in concrete screed. It can be used to insulate the floor on a concrete slab by backfilling or spraying (for wetting, an adhesive composition or ordinary water is used) under a finished wooden floor. Self-styling by dry method is possible.
Tools and materials for concrete floor insulation
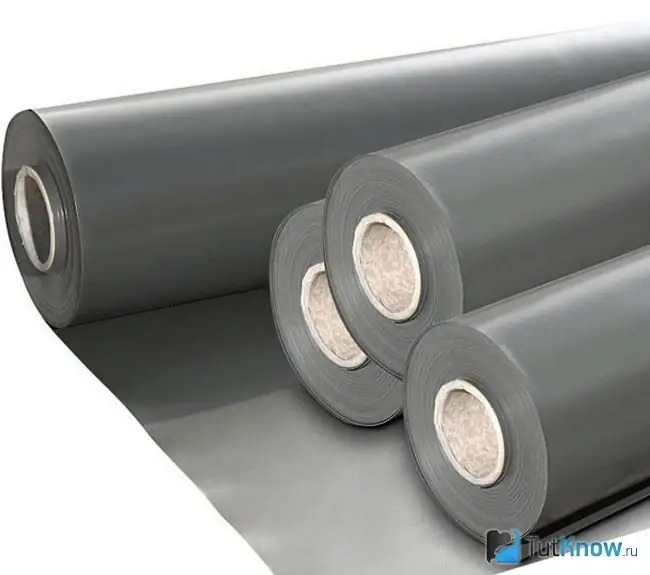
For thermal insulation work, a variety of materials and tools will be required:
- Insulation.
- Waterproofing film.
- Construction stapler for fixing waterproofing films.
- Metallic tape for connecting waterproofing or expanded polystyrene boards.
- Dry self-leveling concrete mix. It will be required if insulation with expanded polystyrene or basalt wool slabs is chosen.
- Dry adhesive mixture for rigid styrofoam laying.
- A hacksaw with a fine tooth for cutting styrofoam or basalt wool slabs.
- Trowel for leveling rough and fine concrete screed.
- Needle roller for rolling the expanded polystyrene sheet and for removing air bubbles from the self-leveling concrete mixture.
- A drill with a mixer attachment for fluffing ecowool and mixing self-leveling concrete mixture.
- Bucket.
- Level.
- Chisel, hammer, trowel - for leveling work.
Preparatory work before the insulation of the concrete floor
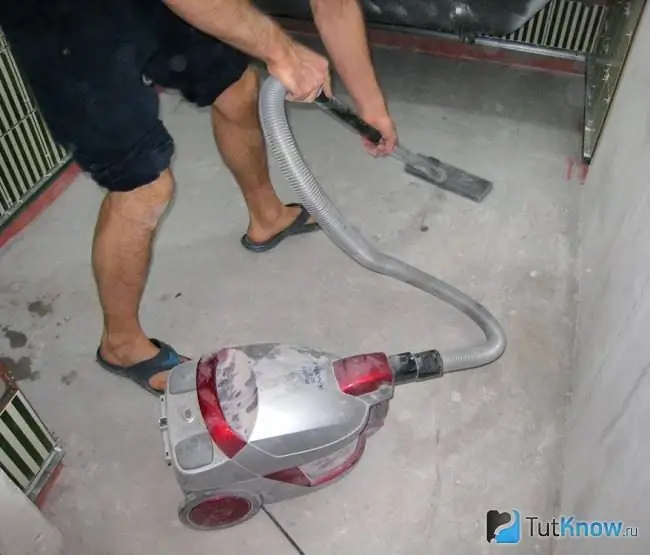
Remove the finished floors, if tiles are installed, they also need to be dismantled after reaching the main concrete slab. Examine it and check it with a level. If there are no humps and depressions, and the difference in height is about 2 cm per meter, you are in luck. All that remains is to remove debris and dust.
If the concrete slab is poured poorly, follow these recommendations:
- Remove debris and dust.
- Remove the bumps, fill the holes with cement mortar.
- Let the solution dry (a couple of days).
- Level with a self-leveling compound.
- Let the floor dry thoroughly.
Leveling works are necessary to insulate the concrete floor with any kind of expanded polystyrene and mineral (basalt) wool in slabs. For expanded clay, ecowool and mineral wool in rolls, you just need to remove debris, dust, knock down obvious bulges and cover up pits.
Concrete floor insulation technology
Works with expanded polystyrene, expanded clay, mineral wool and ecowool are available for independent execution. Detailed instructions for laying each insulation will help prevent mistakes and complete everything in the shortest possible time.
Insulation of a concrete floor with foam
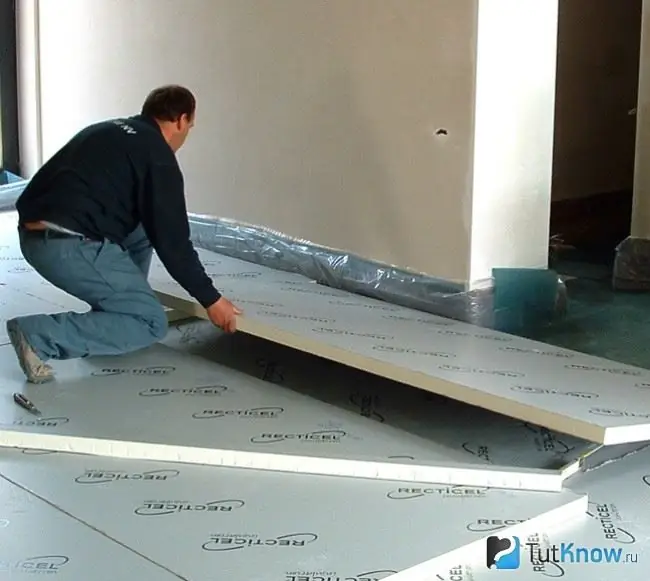
This is the most economical option. Styrofoam is suitable for insulation both under a concrete screed and along logs. In the second case, it should be borne in mind that the thermal conductivity of the tree is much higher. Therefore, the lags will become cold bridges.
The procedure for insulation under a concrete screed (floating installation):
- Cover the concrete slab with plastic wrap. Secure the joints with metallized tape. Bring the film on the walls by 15 centimeters. Then cut it off when you install the skirting boards.
- Apply the first layer of foam, observing the bandaging technique - the vertical seams in the adjacent rows should not overlap.
- Install a second layer of foam. Above each seam of the first level, there should be a whole plate of insulation in the second.
- Cover the seams in the second layer of foam with metallized tape.
- Install a second layer of waterproofing if you plan to pour a thin concrete screed on top. If a wooden floor is to be laid, a second layer of waterproofing is not needed.
- Prepare a self-leveling mixture: pour water into a bucket and pour the dry mixture into it in accordance with the instructions.
- Divide the floor into equal squares. Pour the concrete screed over them, carefully leveling the surface with a trowel.
- Allow the surface to gain working strength.
- Apply any topcoat.
The insulation of the concrete floor has been completed. The complexity of the process can only be caused by pouring a concrete screed. Its thickness in case of laying on top of ceramic tiles or porcelain stoneware must be at least 5 centimeters. In the same way, the insulation of concrete floors on the ground is carried out, only the foam is placed not on the rough slab, but on the sand-crushed stone pillow, covered with a waterproofing film.
Important! Having insulated the concrete base with expanded polystyrene, you can additionally lay a warm floor (water or electric). To do this, instead of the second layer of polyethylene, use foil insulation - foil insulation or foil penofol. A "warm floor" system is installed on top of it.
Thermal insulation of a concrete floor with penoplex
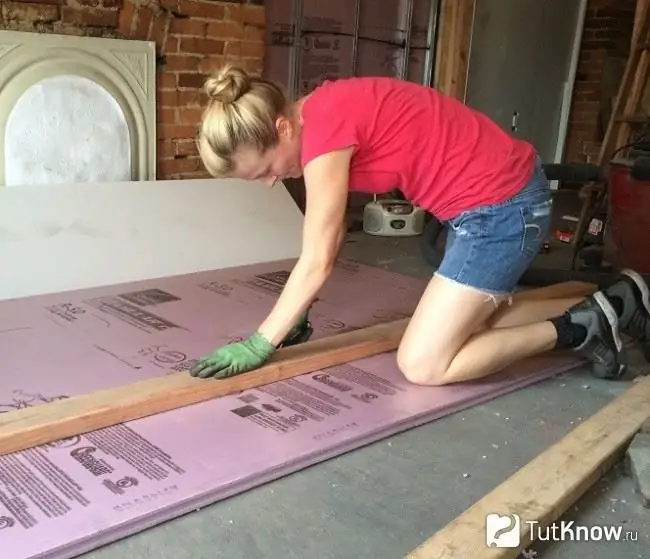
Insulation of a concrete floor with penoplex is carried out in the same way. This material does not require double-sided waterproofing and can be glued directly onto the concrete base (hard method):
- Apply a penetrating antiseptic to the subfloor and let it dry.
- Close the glue mixture according to the instructions with water, mix with a drill with a mixer attachment. Let stand for 5-7 minutes and stir again.
- Roll the insulation board with a needle roller to increase adhesion to the adhesive.
- Apply the adhesive to the penoplex in a continuous layer using a wide spatula.
- Remove excess with a notched trowel.
- Lay the insulation in the corner, press it to the surface.
- Continue with the rest of the plates. Follow the dressing technique when laying.
- At the end of the installation, seal the joints with silicone sealant.
- Install a reinforcing mesh on the penoplex.
- Divide the floor area into equal compartments.
- Carry out a fine concreting by carefully smoothing the mortar in each of the compartments with a trowel.
- Wait until the surface gains working strength.
- Finish off.
Insulation of a concrete floor with expanded clay backfill
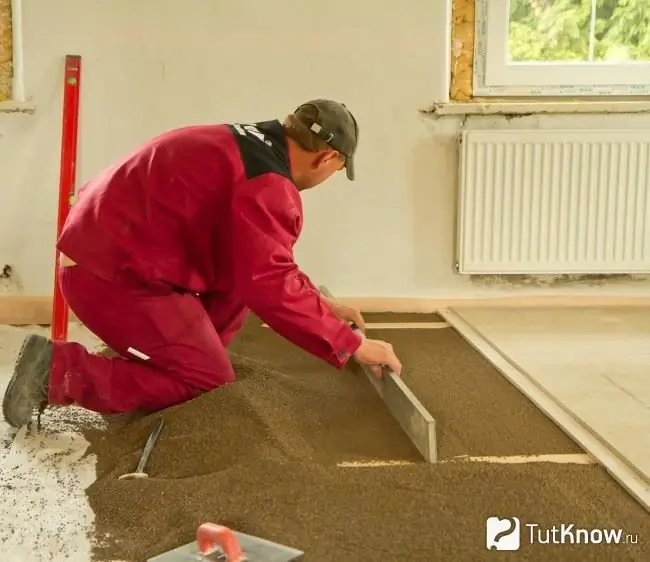
Insulate concrete floors with this material in a private or multi-storey building on the ground floor. This option of thermal insulation is not acceptable for small apartments with a standard ceiling height, as it “eats up” up to 25 cm of space (ask a specialist to calculate the thickness of the insulation for your region).
The procedure for working with expanded clay:
- Carry out waterproofing, gripping the walls to the height of the insulation to be laid. Use dense polyethylene or special mastic for this.
- Fill with expanded clay, level it with a rake.
- Install a reinforcing mesh.
- Prepare the rough screed cement mixture. Use ready-made dry compositions in bags, mixing them with water according to the instructions. The finished solution must not flow!
- Divide the floor into squares of approximately equal size.
- Fill in squares, leveling each with a trowel. Then move on to the next one.
- Let the finished floor work hard.
- Pour in a thin finishing screed (up to 5 cm thick).
- Lay the finishing coat - tiles, parquet, laminate, classic wood or linoleum, carpet.
Thermal insulation of a concrete floor with basalt wool
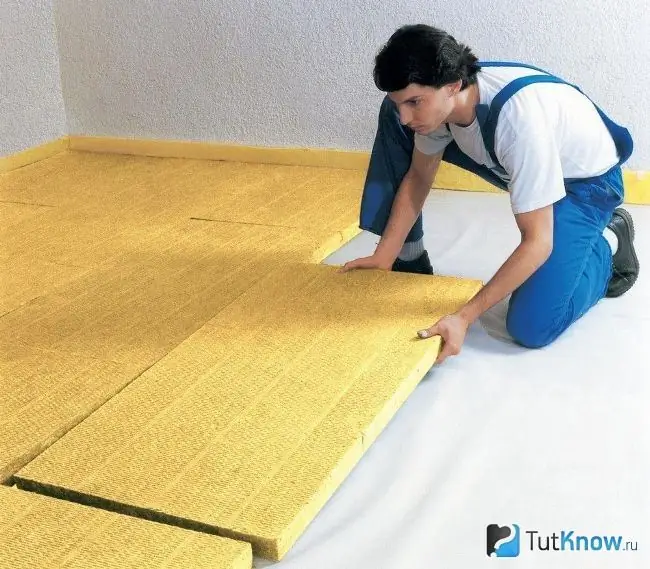
Mineral wool is not the cheapest material for thermal insulation. However, his choice is justified if it is necessary to insulate concrete floors. An electric floor heating can be laid on top of the basalt wool.
For insulation of a concrete floor, you can use basalt slabs and cotton wool in rolls. Plates are laid identically to expanded polystyrene (floating laying), and logs must be laid for rolls. On them, at the end of the insulation work, a fine wooden floor will be laid. An electric warm floor is laid on top of the matt insulation. With a lot of help from the room: the base is divided in half, if the room is narrow and long, or into equal 4 parts.
Laying of basalt slabs:
- Carry out waterproofing, gripping the walls to the height of the insulation to be laid. Use dense polyethylene or special mastic for this.
- When laying, observe the sequence - the vertical joints between the boards must not coincide.
- Insulate the joints with metal tape.
- Instead of a second layer of waterproofing film, lay a thin foil insulation with the foil facing up. It will repel heat back, and cotton wool will not let the cold through.
- Install the "warm floor" system. Follow the instructions strictly, do not bend in the wrong places and do not overlap underfloor heating elements. Place the switch just above the level of the future plinth. If the floor area has been divided into parts due to its large size, a "warm system" is installed in each of them and a switch is displayed for each.
For laying rolls of mineral wool, a lag system is installed - along the perimeter of the room and across, along the width of each roll. The insulation should enter the cavities intended for it with some effort. The procedure for laying rolled basalt wool:
- Lay in plastic wrap. Insulate the joints with construction tape.
- Fix the waterproofing with a stapler to the joists.
- Place insulation between the logs.
- Cover it with a vapor barrier.
- Install a rough and then a fine wood floor.
Warming a concrete floor with your own hands with basalt wool is a time consuming, but quite feasible process. This type of insulation is suitable not only for interfloor ceilings in a high-rise building, but also for floor insulation in a private house on any floor.
The distance between the "warm floor", laid on foil insulation, and the final finish should be at least 3 cm. This is the only way the foil can fulfill its function - to push heat back into the room.
Thermal insulation of a concrete floor with ecowool
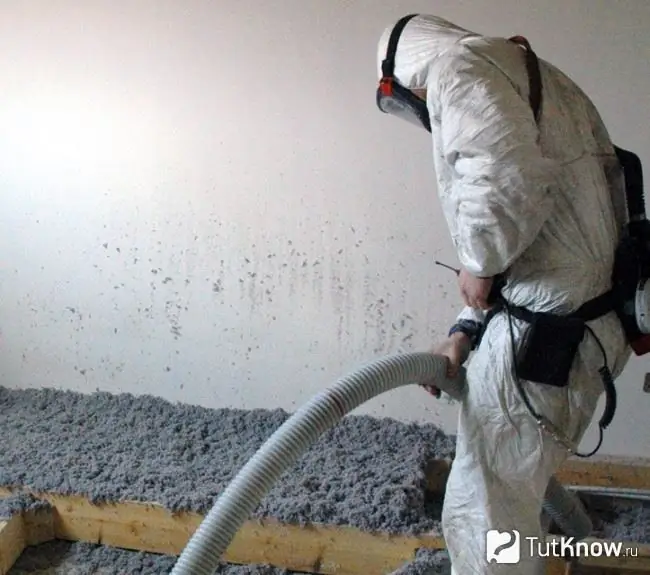
Waste paper is an excellent heat insulator. Therefore, use ecowool for insulating interfloor ceilings in a private and multi-storey building. It is recommended to always call the craftsmen to work with this insulation. However, in order to save money, try backfilling the material yourself.
For insulation with ecowool, no special preparation is required. The material “doesn’t care” whether the base is flat or curved; it crumbles and fills even the smallest gaps. Ecowool concrete floor insulation technology:
- Remove the finished floor. If the boards are normal, sand them, open them with linseed oil or any other antiseptic.
- Examine the lags. If they are quite strong, go over them with linseed oil.
- Clean out the concrete slab.
- Lay a thick plastic wrap on the joists.
- Unpack the bag of ecowool, pour the contents into a deep tank and fluff using a drill with a mixer attachment. The insulation will approximately triple in volume.
- Pour ecowool into one of the cavities. Start tamping with your hands or with the widest trowel. Perform the action until you feel a significant return force.
- Backfill the remaining cavities and tamp the insulation carefully.
- Lay plywood along the logs.
- Install the finishing floor on top.
Ecowool does not require double-sided waterproofing. When moisture gets in, the top layer of insulation is taken by a fairly strong crust. Inside such a "shell", the insulation remains in the same state, its thermal insulation characteristics do not change. Watch a video about concrete floor insulation:
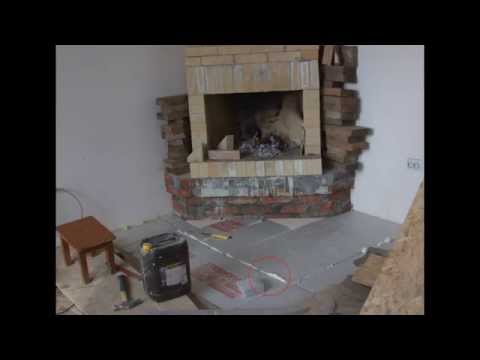
Can't decide how to insulate your concrete floor? Analyze the technical characteristics of thermal insulation materials. Calculate how many of them will be needed to insulate the floor in an apartment or house. Check the cost in hardware stores. And make a decision. Remember, underfloor heating is a coziness in the room and a good saving on heating.