Knauf screed device, its features, types, material consumption, selection of tools and installation technology.
The main types of dry screed Knauf
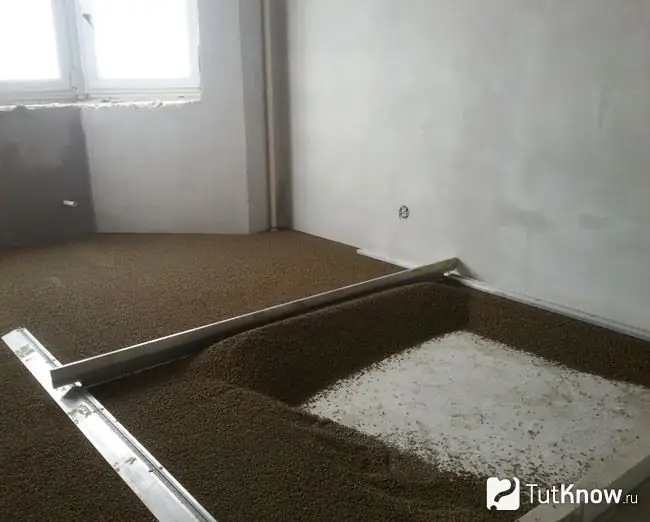
A dry screed involves the connection of its elements without the use of building binders. There are four main types of Knauf screed, which differ in filling material and price:
- Screed "Alpha" … It is carried out on a flat base with differences of no more than 30 mm without the use of expanded clay. It includes a damper tape, polyethylene film and panels made of gypsum fiber board. This is the most budgetary option for Paul Knauf.
- Screed "Beta" … Instead of expanded clay, foamed or porous materials are placed in it. Its advantage is increased sound insulation. However, such a screed has some disadvantages. If expanded clay is a frost-resistant, environmentally friendly and refractory material, then some of its substitutes are harmful to health. Therefore, before laying the dry screed Knauf "Beta", it is necessary to familiarize yourself with the characteristics of its filler. All other floor elements are similar to the previous version.
- Screed "Vega" … It consists of a layer of waterproofing, expanded clay, damping tape and gypsum fiber sheets. Floors leveled with expanded clay are distinguished by excellent heat and sound insulation and durability. After installation on the backfill layer of GVL panels, you can putty the subfloor and lay any topcoat on it.
- Screed "Gamma" … This is the most expensive kind of floor Knauf. It combines all three previous types. A layer of expanded clay, located on the waterproofing, is pressed by panels of gypsum fiber board, on which fibrous insulation or polystyrene is laid on top. The top layer of this "sandwich" is covered with more durable gypsum fiber sheets, providing the floor with special reliability and insulation.
Tools and materials for laying dry screed
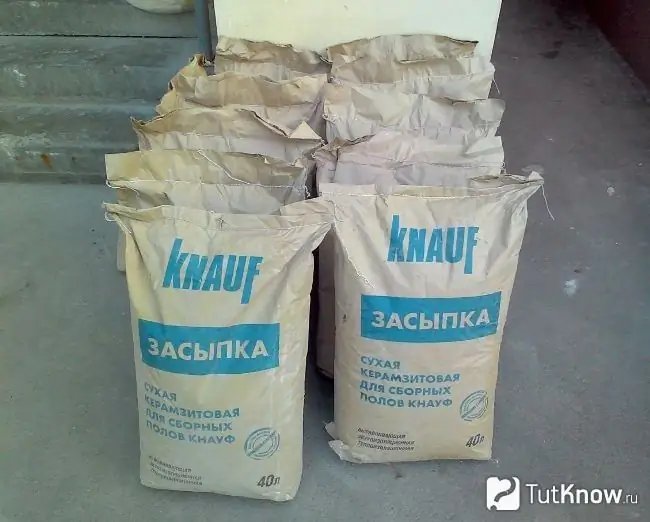
It is possible to perform an accurate calculation of Knauf dry screed, that is, to determine the volumes of materials for its manufacture of a given thickness in a room of a certain area, using a special online calculator, which is available on the sites of finishing materials of this topic.
We will list the required materials and indicate their approximate consumption:
- Gypsum fiber panels for Knauf screed - their number is taken based on the area of the room, taking into account the size of one product. At the same time, a small margin of 10% is required when purchasing material, taking into account the trimming of slabs at the abutments.
- Expanded clay in granules of fraction not more than 5 mm - its average consumption is 20 dm33/ m2, the exact volume can be determined using a construction calculator, knowing the thickness of the screed.
- Screws for fixing gypsum fiber boards - taken at the rate of 12 pcs / m2 floor.
- Damper tape - its width should exceed the thickness of the Knauf dry screed by 2 cm, the consumption depends on the perimeter of the room.
- Knauf adhesive mastic or PVA glue - consumption 50 g / m2.
- Putty - consumption 200 g / m2.
- Polyethylene film for waterproofing - the total area of its canvases should be 20% more than the area of the room.
- Knauf deep penetration primer - consumption about 200 g / m2.
In addition to materials, the following tools will be required for work:
- Drill and screwdriver - they are necessary for making holes and screwing in screws.
- A construction knife and an electric jigsaw - they are needed for cutting GVL.
- The metal rule is useful for leveling the backfill surface.
- U-shaped profile for working with gypsum board - here it can be used as beacons under the rule for leveling dry screed.
- A tape measure, a square, a level are always needed for any measurements and control of work.
Knowing the required thickness of the Knauf dry screed, the size of the room and the consumption of materials per unit of its area, it is easy to calculate how much this work will result in, given that the price of GVL is $ 3, 3 / m2, a bag of expanded clay weighing 24 kg - $ 14.5, polyethylene film - $ 0.2 / lm, a damper tape - $ 1.9 per 20 running meters and self-tapping screws - $ 1.95 / pack.
Knauf dry screed laying technology
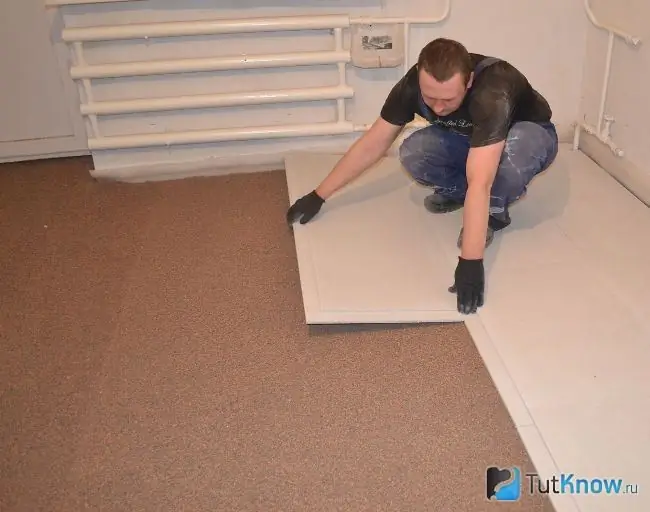
After performing the necessary calculations, preparing materials and tools, you can proceed with the installation of a dry screed. Detailed instructions on the rules of its device are available on each packaging with Knauf products. Compliance with the manufacturer's recommendations will allow you to make a durable floor and avoid problems during its subsequent operation.
The general scheme for laying a dry screed is simple. It involves the sequential implementation of a number of processes: preparation of the floor surface, selection of the backfill level, laying of expanded clay Knauf dry screed, installation and fixation of gypsum fiber board panels. So let's start:
- First of all, you should thoroughly clean the base of the floor from debris, cut off unnecessary metal parts protruding beyond its surface, knock down the protrusions and flows of concrete with a chisel, and remove its delamination.
- On the finished base, you need to spread a polyethylene insulating film. Its canvases are laid with an overlap of 10-15 cm, and their edges, in turn, are brought onto the wall at a height slightly greater than the thickness of the future bedding. The joints of the canvases must be glued with sealing tape.
- To protect the dry screed from temperature changes that can lead to its swelling, it is necessary to fix a damper tape around the perimeter of the room on the lower part of the walls.
- Along the supposed lines of lighthouses, several beds of expanded clay should be poured onto the insulating film with a step of 1 m, or corresponding to the length of the rule. The outermost beds should be located at a distance of 30 cm from the walls of the room.
- Using the level, you should determine the estimated thickness of the backfill and make the appropriate marks on the walls. The standard level of backfill when installing a Knauf dry screed is 100 mm.
- Guiding by the marks, it is necessary to lay guide beacons on the beds of expanded clay and correct their position by pressing the U-shaped profiles into the granular material. The height of the future dry screed should be in accordance with the floor level of adjacent rooms.
- After installing the beacons at the level between them, it is necessary to perform the rest of the expanded clay backfill and level its surface using the rule. To do this, the tool should rest its ends on adjacent beacons and pull loose material towards you. It is recommended to fill it up gradually in small areas in order not to walk on it later, installing GVL. After leveling a certain part of the floor, the lighthouses should be removed, and the recesses remaining from them should be covered with expanded clay.
- On all slabs that will adjoin the walls, the folds should be cut from the corresponding side.
- The first row of slabs should be laid along the wall farthest from the doorway. Before installing the next row, the joining folds of the previous one should be greased with glue. Sheets of adjacent rows should be spaced with an offset of at least 250 mm.
- After laying on expanded clay, all joints of Knauf dry screed sheets must be connected with screws with a pitch of 300 mm and sealed with putty.
For reliability, the subfloor is made in two layers. After the installation of the first layer, a proprietary system adhesive or F145 is applied to it, starting from half of the board. Installation of the second layer starts from the center of the first slab of the lower layer. After the end of the installation, both layers are connected with staples or screws 3, 5x25 mm. During the installation of the subfloor on a dry screed, the surface plane should be periodically monitored with a building level. The panels must be primed before flooring.
How to make a dry screed - watch the video:
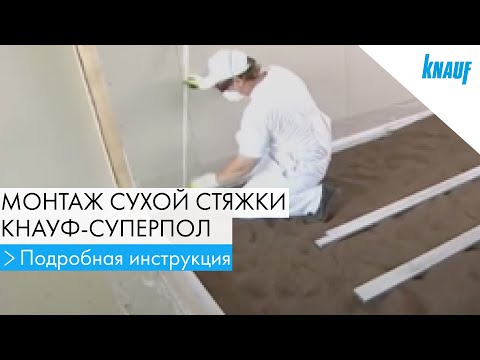
Unlike its traditional types, dry screed is much less of a hassle. And the use of floors based on it makes the home warm, comfortable and cozy.