Advantages and disadvantages of attic insulation with expanded polystyrene, selection and quality control of the material used, methods of thermal insulation of the upper floor, technology of work. Insulating an attic with expanded polystyrene is a procedure for thermal insulation of a technical floor and creating a room suitable for use. The high-quality material is laid on the floor and under the roof to form a protective shell that prevents thermal energy leakage. During installation work, it is necessary to adhere to the technology of laying the coating, which will ensure comfortable living in the house for many years. Information about the isolator and how to handle it can be found in this article.
Features of thermal insulation of the attic with expanded polystyrene
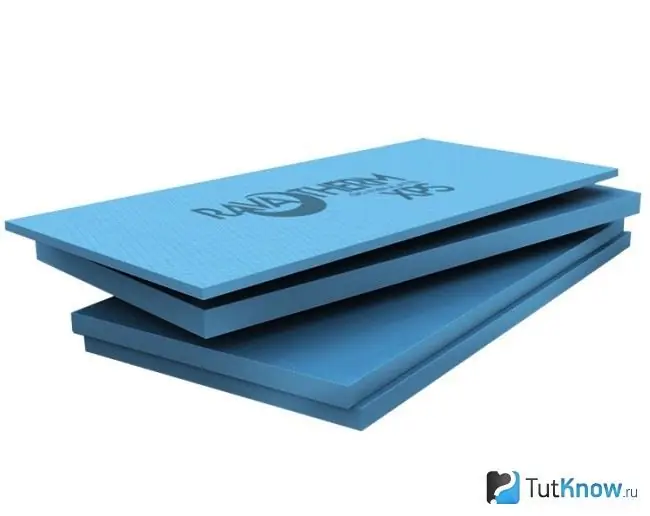
In winter, up to 40% of the heat leaves the house through the roof, so they try to insulate the technical floor as much as possible. For this purpose, extruded polystyrene foam is often used - a synthetic product that is considered a type of polystyrene. It is appreciated for its high thermal insulation characteristics and water-repellent properties.
The substance is obtained in an unusual way: in a liquid state, it is squeezed out through a special device - an extruder. The finished product was named the same as the fixture. Thanks to this technology, the samples have a porous structure, the basis of which is made up of very small cells correctly located in space.
The method of thermal insulation with expanded polystyrene depends on the purpose of the upper room:
- If the attic is very low or not intended for use, only the floor is insulated with the material, placing it on top of the structure or inside. The last option is used at the stage of building a house, when the sheets can be put between the logs without any problems, and then closed from above with a clean floor.
- The sloped roof is insulated with slabs, placing them between the rafters. The positive temperature will be maintained due to the incoming heat from below from the living quarters.
- The pediment is trimmed with sheets fixed to the vertical surface from the side of the room.
To quickly recognize the styrofoam, it is labeled with the letters XPS. An example of a full name is Styrofoam's designation: XPS 1B-AXPS-EN13164-Tl-C5 (10 / y) 250DS (TH) -TR100. The marking shows the main characteristics - thickness, size, density, color, etc. The designation of expanded polystyrene is not standardized, therefore each manufacturer has its own.
The material is sold in the form of plates of various sizes. The maximum sample thickness is 100 mm. There is a large selection of goods of different colors and textures on the market.
The installation technology depends on several factors: the structure of the roof and floor, the need to preserve heat in the attic, the components of the protective layer. When insulating the floor with expanded polystyrene, the contact of warm air from the lower room with a cold surface should not be allowed. Failure to comply with this condition leads to the appearance of condensation on the ceiling of the living room, which causes the formation of mold and mildew. Therefore, the bottom overlap is closed with a vapor barrier film and a decorative coating, and a gap is left between them for ventilation.
When installing expanded polystyrene in the attic, be sure to close the flues with non-combustible gaskets. Pull the electric cables through the metal tubes.
Advantages and disadvantages of attic insulation with expanded polystyrene
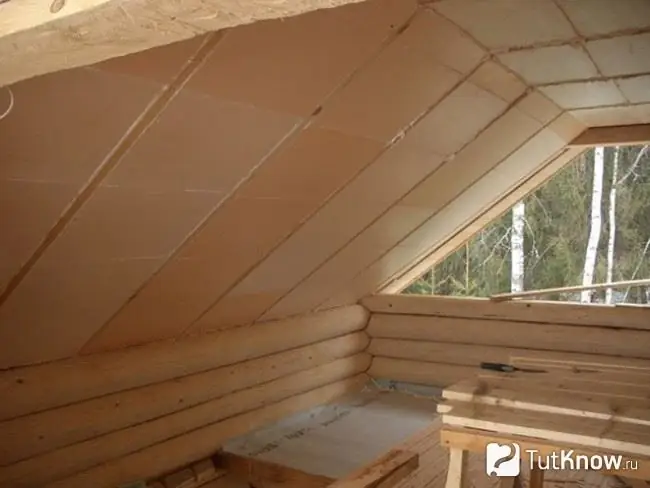
The use of expanded polystyrene for thermal insulation of a technical floor is beneficial and has many advantages.
Its dignity cannot be denied:
- The workpieces are easy to handle. Products of any shape and size are easily cut out of them. This property is especially appreciated when laying polystyrene foam between the interweaving of the rafters and the load-bearing roof beams.
- The slabs are very lightweight and therefore easy to work with when insulating the roof. No helpers are needed to perform operations.
- Specimens can withstand high bending loads, so the surface does not need to be carefully leveled, which makes it easier to place the material on an awkward roof.
- The material rejects fungus and mold, does not rot, which is important when insulating a cold attic in high humidity conditions.
- The presence of milling on the panels shortens the installation time and increases the reliability of the protective layer.
- After installation, a flat surface is formed, which can not be decorated.
- The coating has a long service life.
- The product is multifunctional. Heat-insulated extruded polystyrene foam protects living quarters from noise.
- Plates do not emit fumes harmful to humans. No dust is generated during installation.
- The insulation does not deform, does not crack and retains its qualities at large temperature drops. These characteristics are especially important in a technical floor, where roof elements function under completely different conditions in winter and summer.
While working with this material, unpleasant situations may arise that are easy to prevent:
- The high temperature causes the insulator to melt, producing toxic fumes. Therefore, chimneys, electrical wiring and other flammable areas and objects must be separated with a non-flammable gasket.
- The price of the insulation is higher than other products of a similar composition.
- The material does not allow moisture to pass through, therefore, the room below must be equipped with a ventilation system to avoid condensation on the ceiling.
Attic insulation technology with expanded polystyrene
The attic is usually thermally insulated in one of two ways - creating a protective layer on the floor or under the roof. They are not mounted at the same time, because the upper floor is heated from the lower rooms, and the floor insulation will block the flow of warm air.
Tools and materials for ceiling insulation
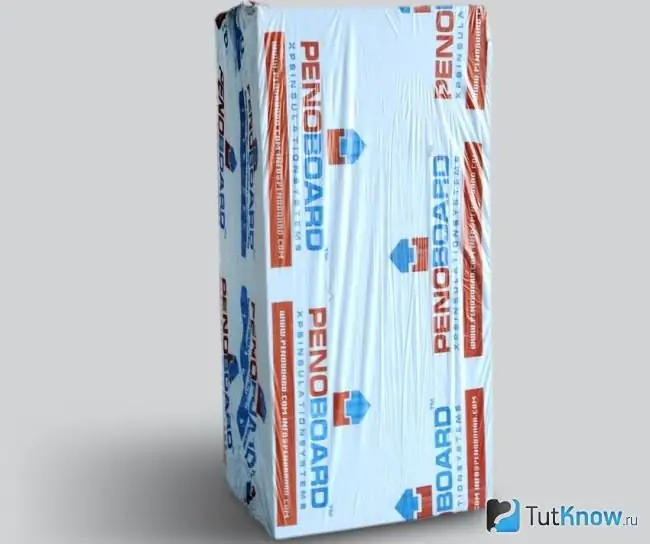
Only a quality product can prevent heat leakage. When buying, you cannot check all the declared characteristics of the insulation, but it is not difficult to identify a fake.
To do this, follow the simple procedures:
- Examine the product sheet. Cells of the material are visible on the surface; by their size and location, one can judge the structure of the product. In high-quality samples, they are small, barely distinguishable, and are evenly spaced. Particles that are clearly visible indicate the presence of large pores through which moisture seeps and heat escapes.
- Find the sample with the broken piece and press your finger on the damaged area. Defective goods can be recognized by the crackle that appears when the cells are destroyed, which indicates a thin-walled structure. Cracks appear on such material.
- High quality products give off a faint smell of alcohol. In the manufacture of a fake, cheap components are used that smell unpleasant.
- Before buying, find out the addresses of the branded stores of well-known companies. It is impossible to buy a fake in such stores.
- The product must be packed in a protective film. Make sure that the label contains information about the manufacturer, the date of manufacture, the main characteristics, and applicability.
When buying, also pay attention to the density of the material. This parameter is considered basic for insulation, the scope of its application depends on it. The higher the value, the more expensive the product is. Samples of various densities are placed on the floor and roof. the operational load on them is different.
In order not to overpay, study the following indicators:
- Sheets with a density of up to 15 kg / m3 can be laid on a surface that is not subject to stress. They are suitable for an unexploited loft or decked slab.
- Density from 25, 1 to 35 kg / m3 - the panels can withstand light loads.
- Density from 25, 1 to 35 kg / m3 - for floors of exploited attics. The coating is able to withstand heavy loads.
- Density from 36 to 50 kg / m3 - for especially loaded areas.
The required thickness of the insulating layer can be determined according to SNiPs. Its size is influenced by the climate of the area in which the house is located. Minimum slab thickness: for southern regions - at least 10 mm, for northern regions - at least 15 cm.
The choice of material also depends on the purpose of the room. To insulate a cold attic with expanded polystyrene, you can take panels that are thinner and cheaper if it is used as a warehouse. If things need to be stored in good conditions, buy a quality product.
There are many areas in the attic that require sheets of irregular sizes and shapes. To quickly solve the problem, you will need the following tools:
- A sharp knife, preferably a clerical or wallpaper knife.
- An electric jigsaw is used to cut thick slabs. However, it will not be possible to get straight ends.
- The heated knife is able to cut off excess without the formation of debris.
- Hot nichrome wire will cut workpieces of any thickness and shape, the ends are perfectly flat.
The glue is necessary to ensure a snug adhesion of the sheets to the surface, which increases the protective properties of the coating. Usually, in this way, the insulation is fixed to the concrete slabs.
There are two groups of funds - universal and special:
- Universal ones are capable of fixing polystyrene foam to the floor from any material. When buying, pay attention to the area of application of the substance - for outdoor use or indoor. The attic is insulated with products for interior work, they are cheaper. The popular cement-polymer composition ANSERGLOB ВСХ 30 is intended for external and internal use, the cheaper version of ECOMIX BS 106 is used only indoors.
- Bituminous substances can be used immediately after purchase, it is enough to mix the contents of the jar. They are waterproof, but for reliability, the entire surface should be thoroughly greased.
- For fixing the panels, liquid nails, tile glue, and silicone sealant are also used.
- The special tools include bulk materials of the CEREZIT brand - CT 83, CT 85, CT 190. They fix the products better, but the surface requires careful cleaning and leveling.
- It is convenient to fix the sheets to the plastered gables with CET 84 EXPRESS foam agent, which is sold in cylinders. It costs more than dry analogs, but replaces 25 kg of dry matter.
So that during installation work there are no problems with the adhesive composition, use our tips:
- Choose a product with a long hardening time in order to have time to correct the position of the sheets.
- Always buy the substance with a margin - on an uneven surface, consumption increases. The optimal amount of glue that is applied per 1 m2, indicated on the product label.
- The substance should not contain components capable of dissolving it: gasoline, solvents, ethers.
- Check the storage conditions of dry mixes in the store, because they absorb moisture well.
- Choose the glue for the intended purpose. Indoors, it is impractical to use a solution that is designed for severe frosts.
Methods for insulating the attic floor with expanded polystyrene
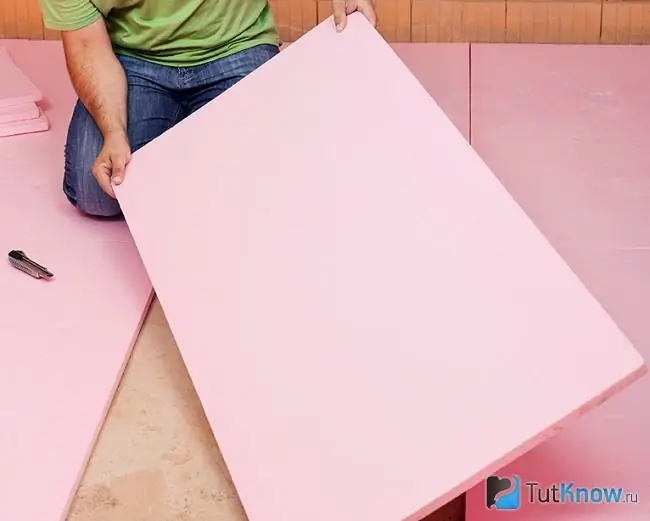
The main option for warming concrete floor slabs is gluing. The density of the sheets depends on how the technical floor will be used. The higher it is, the more the floor will withstand the load. Instructions for warming a concrete floor with expanded polystyrene:
- Free the attic of all things. Clean the surface of dust and rinse with water. Fill cracks and other defects with cement-sand mortar. Knock down the protruding parts.
- Cover the slabs with a primer.
- Check the levelness of the floor with a hydrostatic level. Fill it with self-leveling mixture if necessary.
- Make sure the concrete is free of oil or grease. Treat problem areas with solvent.
- Cover the floor with a primer. It is advisable to use a liquid from the same manufacturer as the glue. Further work can only be carried out on a dry surface.
- Prepare an adhesive solution.
- Apply the compound to the floor. Its amount depends on the height differences of the slab. Use a notched trowel to walk over the material on a level area. An uneven base with steps of 3-10 mm is processed differently. Lubricate the edges of the insulator with a 3-4 cm strip at a distance of 2-3 cm from the end, and inside the sheet, treat 5-8 areas with a diameter of 10-12 cm.
- The adhesive layer at the edges of the panel should be 20 mm high, leave space for air to escape. Do not lubricate the sides with a substance.
- Press the panel down to the floor immediately. Place subsequent products with a shift relative to the joints and press firmly against adjacent blocks. Place the cut pieces last. If glue has squeezed out, remove it immediately.
- Periodically check the levelness of the surface with a long ruler and level. Fill gaps larger than 2 mm with waste. You can move the slabs while the glue has not hardened (within 20 minutes).
- After drying, cover the insulation with a vapor barrier film with an overlap of 15-20 cm on the walls and on adjacent pieces.
- Seal the joints with adhesive tape.
If the attic is to be used for storage, the surface should be protected from damage. One of the options for solving the problem is the application of plaster.
The work is done like this:
- Prepare a slurry from a free-flowing mass specifically designed for styrofoam finishing.
- Place a 5x5 mm metal mesh on the insulation and fix it with mortar.
- After the mass has hardened, cover the mesh with a layer of plaster 5-10 mm thick.
- Smooth the surface with a trowel.
Thermal insulation of a floor with logs is usually used to insulate wooden floors. Perform the following operations:
- If a subfloor or finish floor is available, remove the top deck.
- Clean the surface from dirt.
- Remove all objects that could damage the membrane.
- Lay a waterproofing film on the boards and on the walls with an overlap of 15-20 cm. Glue the joints with adhesive tape. The canvas will protect the lower floor from moisture leaks through the roof.
- Cut the styrofoam pieces according to the size of the cells. The material should fit snugly between the lags.
- Fill the slots with scraps.
- Cover the slabs with a vapor barrier membrane overlapping the walls and adjacent parts. Seal the joints with construction tape.
- Install the finished floor.
Loose mass of expanded polystyrene is sold in hardware stores. On its basis, you can prepare a good heat insulator. For work, you need granules of material and cement in a ratio of 1: 3 or 1: 4. The more fragments in the mixture, the more effective the insulation, but the worse the strength. Think about how you will walk on the floor after finishing work. One of the options is to fill in the logs in advance, on which it will be possible to mount the flooring. The work is performed in the following sequence:
- Prepare the floor and cover with plastic in the same way as in the previous section.
- Pour cement and water in the specified proportions into the concrete mixer, mix everything to the state of liquid sour cream.
- Add styrofoam and turn on the machine.
- After obtaining a homogeneous composition, pour it onto the floor.
- Wait for the mixture to dry and cover it with steam wrap, overlapping the walls and adjacent pieces. Glue the joints with tape.
- Install the decks (if the places for their attachment were provided in advance).
Work to protect the roof of the attic with expanded polystyrene
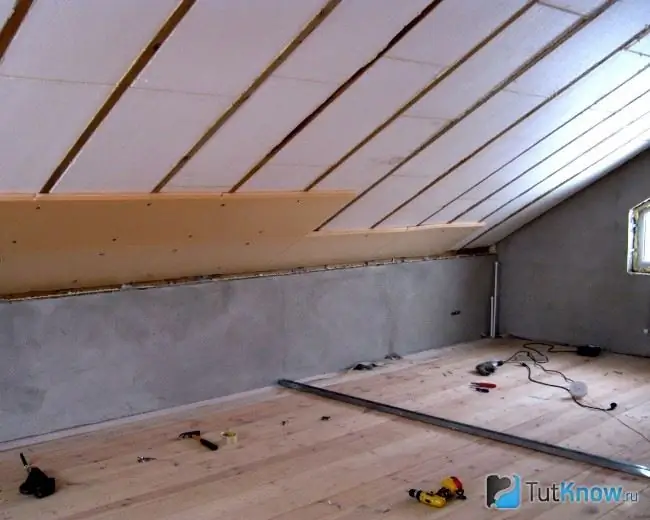
The most popular way to modify the roof is to lay the sheets between the rafters. This option does not affect the structure of the rafters, does not load the roof.
Operations are allowed under the following conditions:
- The roof drainage structure is designed taking into account the slope angle. This ensures that moisture does not get inside the cake and degrade its performance.
- The dimensions of the attic allow you to cover the roof with a vapor barrier film from the inside. It will prevent humid air from degrading the performance of the material.
- On the outside of the roof, the insulation is closed with a vapor-permeable membrane that allows moisture to evaporate from the "cake".
- There must be a ventilation gap between the film and the roof covering. Usually it is equal to the thickness of the slats on which the tiles, slate or other roofing material are attached.
Roof insulation is performed in the following sequence:
- Treat all wood elements with antiseptics to prevent decay. Let the lumber dry. Replace all damaged parts.
- Cover the outside of the rafters with a vapor permeation membrane. The film is stretched from the bottom up - from the eaves to the ridge. Do not stretch the canvas; it should sag slightly. Secure it with a construction stapler.
- Cut the styrofoam to fit the openings between the rafters. The sheets should fit snugly between the beams. You can fasten them with corners or brackets, which are sold in the store specifically for these purposes. You can also fix them with not thick slats from the inside of the room.
- Fill all the space between the rafters with panels. You can stack sheets in several layers, but the bottom row should overlap the joints of the top one. Fill the remaining voids with scraps. During installation, leave for ventilation gaps of 20-50 mm between the vapor-permeable film and the insulation.
- Cover the inside of the roof with a vapor barrier membrane with an overlap on the walls and adjacent cuts and secure to the rafters with a construction stapler. Seal the joints with adhesive tape. Do not tighten the canvas too much, a sagging of 1 cm is allowed in the middle.
- Installation of finishing materials in a warm attic is optional.
Features of thermal insulation of gables with expanded polystyrene
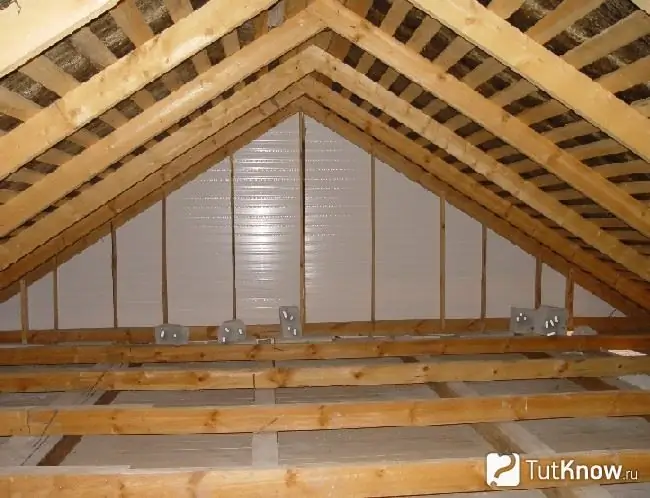
The choice of the method of thermal insulation of the pediment depends on the construction of the wall. Wooden partitions are processed in the same way as roofing. If the pediment is plastered, the insulation can be glued, as described above, or fixed with a foamy agent. For work, you will need a special device in the form of a pistol.
Perform the process in the following sequence:
- Secure the solution bottle to the fixture.
- Squeeze the mixture onto the panel around the perimeter at a distance of 2 cm from the edge and diagonally, and attach the panel to the surface.
- Place the subsequent sheets in such a way that the joints do not coincide.
- Clean the attachment with CEREZ1T PU solvent.
- After the glue has hardened, you can start decorating the pediment.
How to insulate an attic with polystyrene foam - look at the video:

The technology of insulating the attic with polystyrene foam is very simple, and the effect exceeds all expectations. House heating costs are reduced several times, all costs will pay off in 1-2 heating seasons. The main thing when working with this material is to fulfill the requirements of the technology, since amateur performance can lead to unpleasant consequences.