Thermal insulation of the floor with polyurethane foam, features of insulation work, its pros and cons, coating technology. Warming the floor with polyurethane foam is one of the ways to maintain a comfortable temperature in the house. This material is used with equal success for thermal insulation of foundations located on the ground, between floors and above basements. We will tell you how to insulate the floor with polyurethane foam in this article.
Features of floor insulation with polyurethane foam
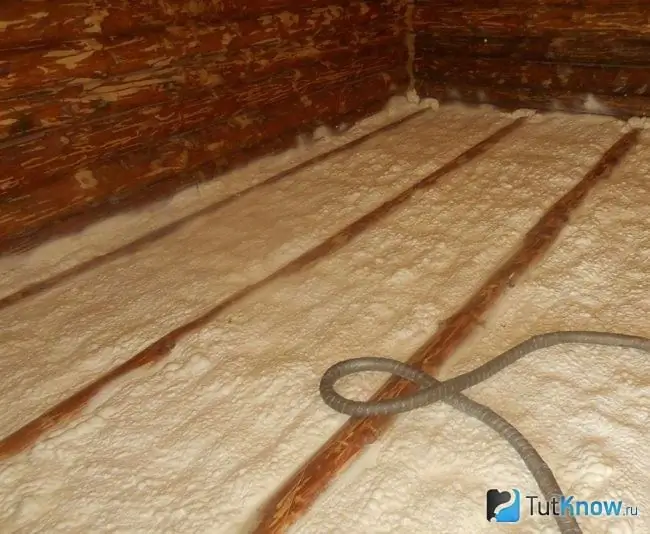
Two types of polyurethane foam are used to insulate the enclosing structures - an elastic product and a rigid one. Thermal insulation of the first type has a density of about 30 kg / m3 and in all technical respects it is similar to mineral wool. Installation of such insulation requires a protective waterproofing layer and an air gap for ventilation of the structure.
For thermal insulation of the floor, polyurethane foam of the second type is much more often used. Rigid insulation does not need vapor barrier protection, has better insulation characteristics and a density of more than 30 kg / m3… The material is especially recommended for use in difficult conditions of the North and in humid rooms.
Polyurethane foam is obtained from two components "A" and "B", which are in different metal containers and have a liquid consistency. Component "A" is called a polyol. It is an acidic solution containing polyesters, chemical emulsifiers and foaming agents. Polyol is usually yellowish in color, it is slightly toxic and almost non-explosive.
Component B is an isocyanate, a mixture of diphenylmethane diisocyanate with a polycyanate. The substance is a powerful reagent that easily comes into contact with water and air. The component is manufactured overseas in Japan, Spain, Germany and Hungary.
Polyurethane is formed by mixing these components in a 1: 1 ratio using a special apparatus. This proportion cannot be violated. An overabundance of component "A" in the mixture leads to an increase in the thermal conductivity of the finished material, and component "B" - to its fragility.
Compared to classical insulation materials, for example, mineral wool or ordinary foam, liquid polyurethane foam benefits primarily due to the duration of the installation of thermal insulation.
Thermal insulation of floors with classic materials requires compliance with certain stages of the process: leveling the surface, fixing the heat insulator on it and sealing the gaps between the elements of the coating after its installation. All this takes a lot of time. In addition, mineral wool and foam must be protected by waterproofing, since when moistened, they lose their insulating properties and durability. In addition, thermal insulation boards are a rather fragile material that requires careful handling.
In contrast, thermal insulation made with liquid polyurethane has higher strength and less moisture absorption.
The structure of the insulation hardened after pouring is such that air circulates in it easily, eliminating the possibility of water condensation under the insulating layer. Thus, in polyurethane foam, the possibilities of insulation and waterproofing are combined. Therefore, it can be applied directly to the base surface of the floor, shortening the production time.
Pros and cons of floor insulation with polyurethane foam
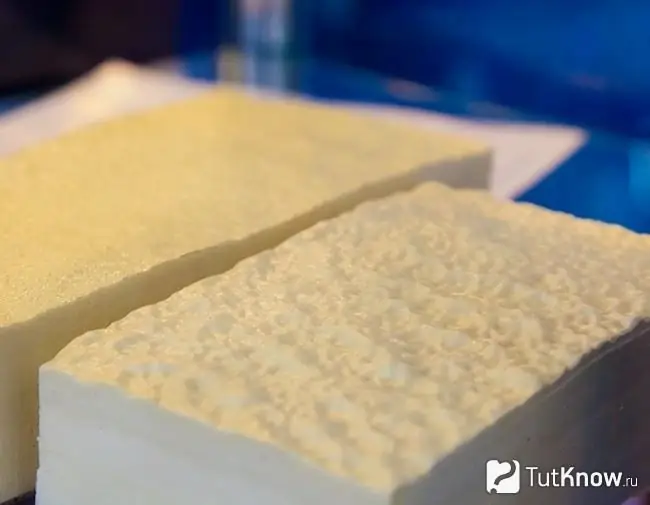
The method of insulation with polyurethane foam makes it possible to isolate floor surfaces of any area and geometric shape with high quality. In addition, thermal insulation with this material, due to its properties, has many more very significant advantages:
- Due to the fact that the liquid polyurethane foam for the floor is applied to the base surface by spraying, the finished coating has no seams. As a result of the work, a solid structure is formed without joints, which always accompany the installation of tile heaters and are conductors of cold from the ground to the interior of the room. In addition, due to the absolute tightness of the polyurethane spraying, the floor is vapor and water tight.
- Polyurethane foam has the lowest thermal conductivity among all known heaters. At a temperature of 10 ° C, its coefficient is 0.0235 W / (m • K). For specialists, this suggests that a ten-centimeter layer of polyurethane foam will be quite enough for high-quality thermal insulation of the floor in the house. To obtain the same effect when using sawdust, it is necessary to fill them with a layer of 300 mm or more.
- Spray coating is not a complicated process for an experienced technician. In the presence of a special apparatus, a team of two people will be able to perform thermal insulation of the floor with polyurethane foam on an area of 300 m2 in just 8 hours. When insulating with a tile material such as mineral wool, it is impossible to do this in such a time. After spraying the substance on the base, after 4 hours, the heat-insulating layer can be sheathed with a floorboard or applied with a cement screed.
- Polyurethane foam is quite inert. He does not care about moisture, ultraviolet light and wind, the frozen material is difficult to dissolve, there are no volatile substances in it. These factors give reason to consider this insulation in the ecological sense absolutely safe.
- Polyurethane foam flooring, due to its resistance to moisture and the appearance of condensation, does not require a vapor barrier protective layer.
- Floor insulation by spraying polyurethane foam can be performed from the inside and outside of the structure. This heat insulator has excellent adhesion to almost any building material. Therefore, fixing it does not require fasteners, which are sometimes expensive.
- The material is convenient for transportation to objects. Due to the fact that it is packaged in a liquid state in metal barrels, it can be delivered to a construction site with one car trip. The preparation of the working mixture for thermal insulation is carried out on site.
- The elasticity of the polyurethane foam coating and its resistance to external influences in the form of static, mechanical and dynamic loads makes it possible to do without reinforcing the material.
- The service life of the insulation is designed for 20-60 years, it is about five times higher than that of mineral wool and expanded polystyrene.
There are very few disadvantages of polyurethane foam insulation. The material does not adhere to polyethylene. In connection with the high-tech method of applying insulation to the base surface, a special apparatus and the participation of an experienced craftsman are required.
Floor insulation technology with polyurethane foam
Insulating the floor with polyurethane foam insulation solves two issues at once: it reduces the cost of heating the house and helps to create the optimal temperature for living in it. The work on warming the surface can be divided into two stages - its preparation and the spraying of a liquid heat insulator on it.
Floor preparation for ecowool installation
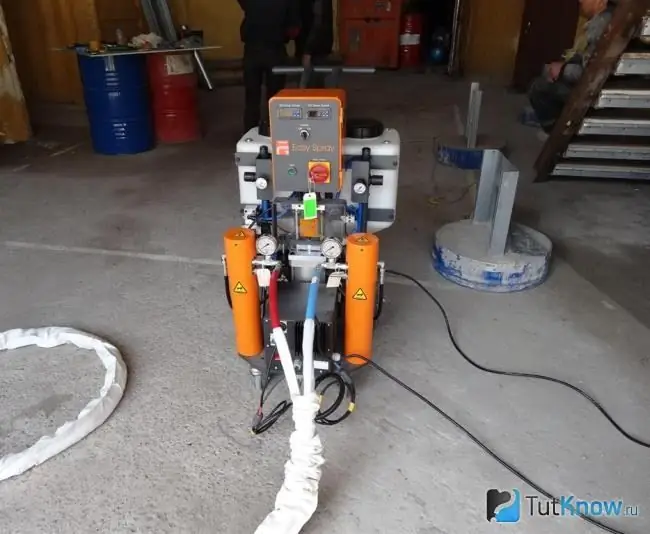
To ensure high-quality adhesion, the polyurethane foam insulation must be applied to a clean and dry substrate. Therefore, before starting thermal insulation work, debris should be removed from the surface, and then carefully inspected. The unevenness of the base with this method of insulation is not of particular importance.
Much more important is the absence of oily stains on the floor, for example, from oil products, grease and other things. If they are found, this defect should be eliminated using mechanical and chemical means: washes, solvents, scrapers, etc. Otherwise, there will be no reliable adhesion of the insulation to the base on problem areas.
The second point to pay attention to is the moisture content of the floor surface. Its value should not exceed 5%. To check, you can use quite affordable means: you need a glass and a paper napkin. It should be placed on the floor surface, covered with an inverted glass and left for a day. If, after this time, the napkin becomes moistened, the base should be dried naturally or using heaters.
Insulation with polyurethane foam should be performed at an air temperature of at least + 10 ° C. If this condition is neglected, the adhesion of the heat insulator to the base will be insufficient.
Applying polyurethane foam to the floor
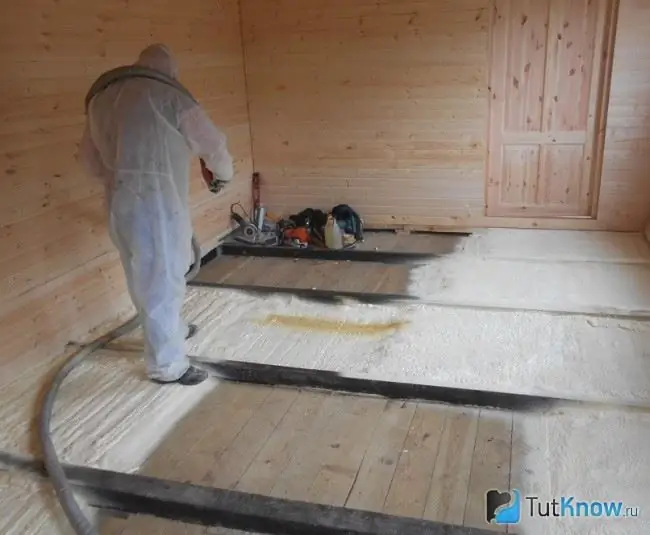
To mix the components of the insulation and apply it to the floor, you will need a special high-pressure installation, which costs more than $ 2,000. It is impractical to buy such a device for one-time work, but in the case of its independent implementation, the equipment can be rented.
Before starting insulation, the installation must be connected with hoses to barrels with components "A" and "B". In the vortex chamber of the apparatus, the substances will mix, and then the resulting finely dispersed suspension will be sprayed through a special nozzle.
In order to obtain high-quality polyurethane foam insulation, the device must constantly maintain a pressure of at least 140 atmospheres. Often, such equipment is not capable of operating from a conventional 220 V network. It needs a three-phase current and a power of more than 15 kW. For this reason, many companies that are engaged in such activities leave the facility with their own diesel generator, capable of ensuring the operability of the injection equipment, generating the current of the required power.
After turning on the unit, spraying polyurethane foam should be done, evenly distributing the material over the surface of the base. Thermal insulation of the floor of one room lasts on average from 40 minutes to an hour. The sprayer must adjust the required layer thickness himself.
Upon completion of the spraying of the insulation, the coating should be left to dry, which lasts an average of 24 to 48 hours and depends on its thickness.
Polyurethane foam insulation of a wooden floor has its own nuances. For its insulation, polyurethane foam is the ideal material. Due to its inertness, the ecology of the house is not disturbed, and the special structure of the coating protects the plank surface from putrefactive processes, thereby prolonging its service life.
When processing a rough base, the material should be sprayed onto the underground part of the structure or from both sides. In this case, both the floor logs and the space between them should be sprayed with insulation. Due to the excellent adhesion of wood to polyurethane foam and the tightness of the coating, waterproofing of the surface is not required.
Finishing the floor
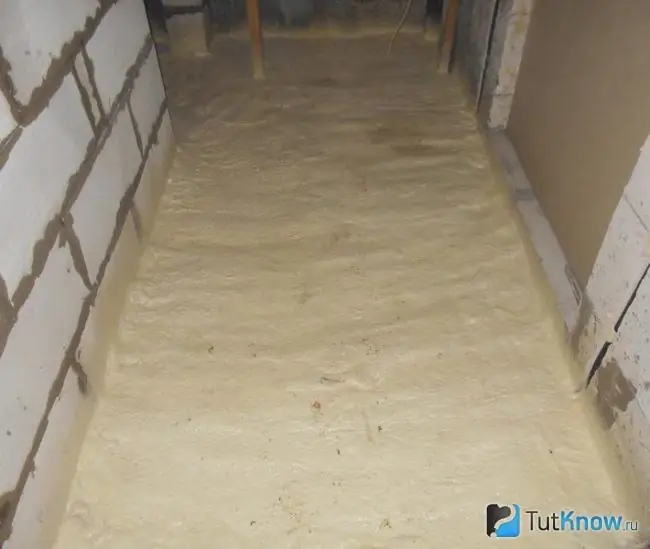
If the spraying of polyurethane foam was carried out between the wooden logs, then after polymerization of the insulation, you can immediately begin the installation of the plank flooring, carrying it with screws to the beams of the floor structure.
After applying insulation to a concrete base without the presence of a log, the thermal insulation layer should be protected with a cement-sand screed. To do this, in a suitable container, you need to knead the solution and distribute it evenly over the insulation. The levelness of the screed should be checked with a building level to avoid unevenness or unnecessary surface slopes. The thickness of the screed must be at least 40-50 mm, a thin layer may not withstand mechanical stress, and the floor will crack.
How to insulate the floor with polyurethane foam - watch the video:
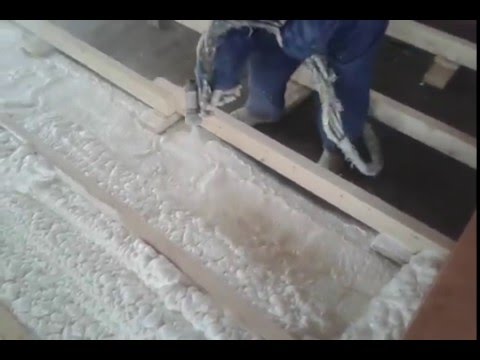
Polyurethane foam as a heater is currently at the top of its popularity. All of its effective qualities have long been tested in practice and therefore do not even need advertising. It is this method of floor insulation that is the most practical and reliable.