Competent selection of tongue-and-groove boards, laying material on different substrates, advantages of coatings with side tongue-and-groove connection. Grooved boards are products from a single solid wood with milled grooves and ridges on opposite ends of the material, which, when joined, form a gapless connection. Used to create high-quality seamless coatings for floors and other surfaces. We will talk about the methods of laying grooved boards in this article.
Advantages and disadvantages of tongue-and-groove flooring
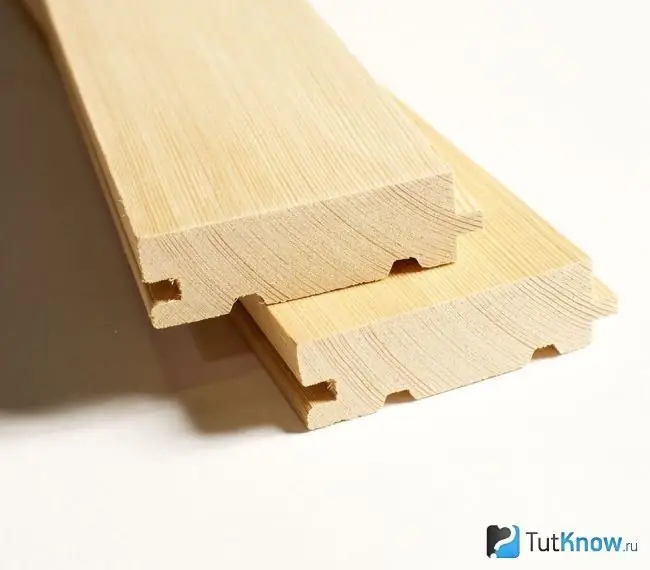
Due to their design features, tongue-and-groove boards have significant advantages over other sawn timber:
- The tongue-and-groove connection ensures an even distribution of the load on the boards and increases their service life.
- On the rear side of the board, special grooves are made for supplying air to the seamy side of the material, which excludes the appearance of fungus.
- The covering made of grooved boards has good sound and heat insulating properties.
- Thanks to the spikes and grooves, the assembly of the material is very quick.
- Grooved boards are produced in standard sizes, which also speeds up installation work.
- The board is made from a single solid wood, without the use of chemical components.
- The coating has a beautiful appearance.
- The boards, connected by means of a groove and a ridge, do not deform or warp.
- The tongue-and-groove boards form a durable, seamless finish.
- To restore attractiveness, it is enough to cycle or grind the front side and cover it with linseed oil or special varnishes.
- The boards meet European standards. The front part is smooth, does not require additional improvement, paint or varnish fits perfectly evenly on it.
- A healthy spirit is always present in rooms with natural wood floors.
- A tongue-and-groove floor looks good in any room decor.
- The connecting elements (groove and tenon) are manufactured on a high-precision milling machine, therefore the connection quality is very high.
Grooved coatings have weak points: to protect the surface from mechanical stress and insects, the boards must be periodically painted, varnished, treated with antiseptics, which requires considerable funds; such material is expensive.
How to choose tongue-and-groove floorboards
When buying grooved floorboards, pay attention to the main characteristics of lumber, on which the durability and visual appeal of the flooring depends.
Wood species of grooved board
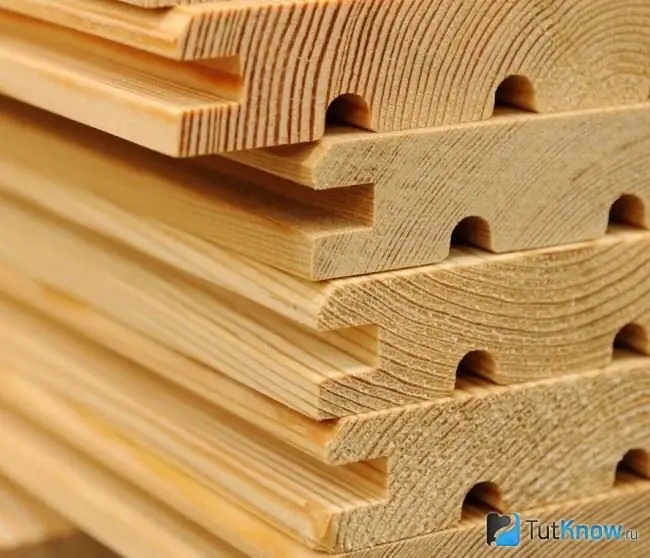
Extra class tongue-and-groove boards made of hardwoods (larch, oak or ash) are used to create a finished floor. This is the most expensive product, without knots, cracks and other defects, with a uniform structure and color shade. Extra class boards are distinguished by increased water resistance, but are expensive.
The subfloor is mounted from soft species (pine, spruce), as well as any boards of class C. Lumber of this class is distinguished by the presence of knots, cracks, single holes. In addition, pine and spruce boards are soft, quickly damaged by thin heels, and have a weak resistance to moisture. The positive aspects include the low cost of the material.
Dimensions of grooved board blank
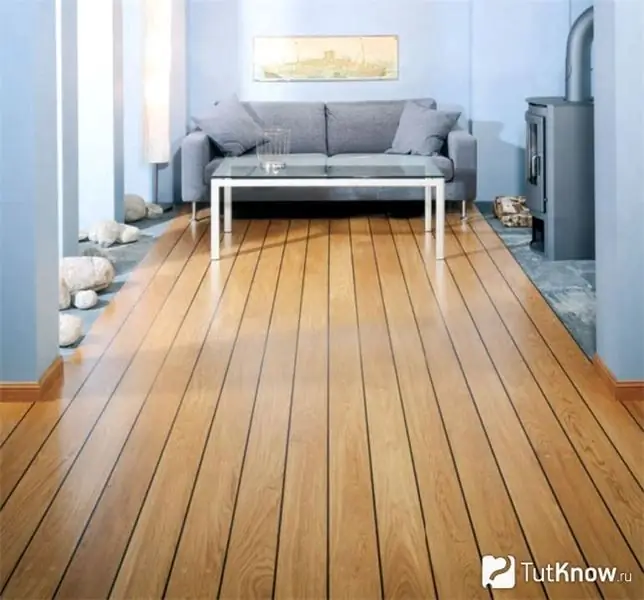
Measure the length of the walls of the room. Determine which wall the boards will be laid parallel to. Calculate roughly the total length of the boards for the entire room and decide how long you should buy the pieces.
The following information will help you make a decision:
- The length of the boards should be equal to the length of the room.
- You can buy short samples, but on the condition that they will not hang in the air.
- Planks from 1 to 6 m are sold on the market. For flooring, most often they buy lumber with a length of 3 to 6 m, which allows you to choose the optimal length of the workpiece and reduce the length of the trimmings.
- When buying, increase the estimated length of the material by 10%, which may be in the scraps.
- Recommended dimensions of grooved boards: width - 70-145 mm. Thickness - from 28 mm.
Moisture of grooved boards
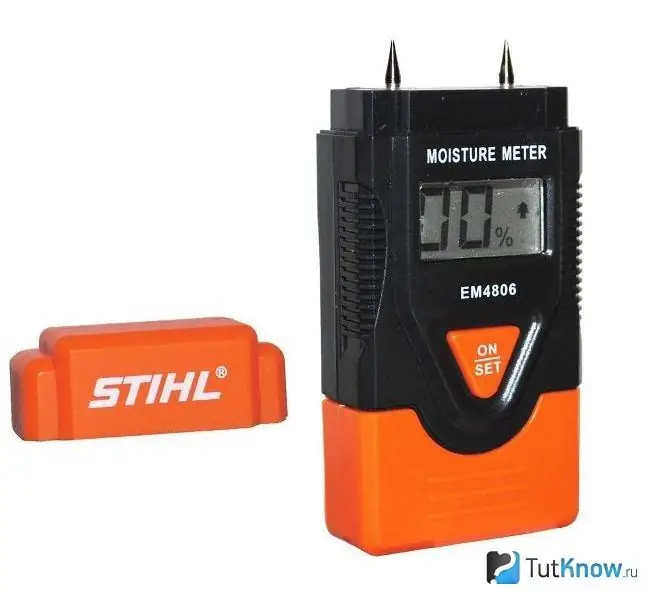
For work, grooved floorboards with a moisture content of 12-16% are suitable. If you have a choice, purchase products that have been dried in autoclaves - for them this figure does not exceed 10%. If the humidity is high, the floor will deform as it dries, cracks and warpage will appear.
Humidity is determined in several ways:
- The most reliable is to obtain this parameter using a moisture meter.
- It is not difficult to distinguish strongly damp boards - just put your palm to the surface.
- When tapping with the knuckles, wet material sounds dull, dry - loud and loud.
- Wet boards have a darker color than dry boards.
- A well-dried board has a noticeable shine, while a wet board has a matte shade.
- If the boards were wrapped in cellophane, inspect for condensation. The presence of moisture droplets indicates a high moisture content of the boards.
Checking the quality of grooved boards manufacturing
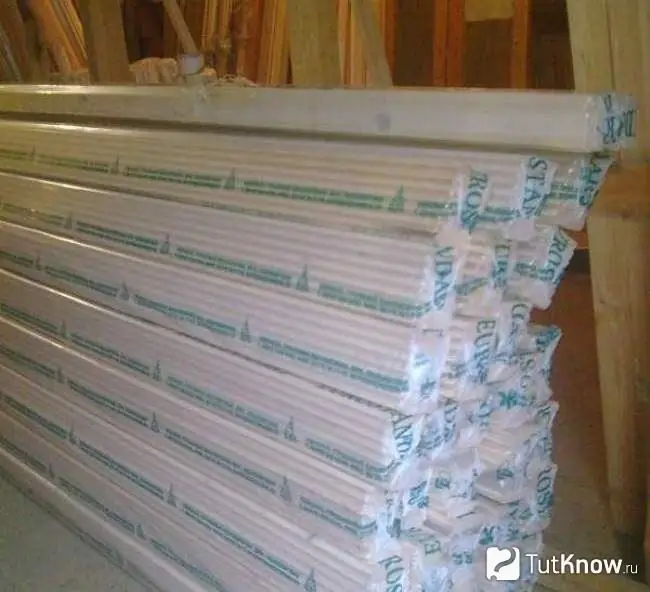
Check the accuracy of the grooves and tenons and the quality of the front side processing:
- The cleat should enter the groove with a slight load, with a slight click after connecting to the groove.
- The front side must be carefully sanded.
- The seamy side is usually roughly processed, but there must be grooves for ventilation of the flooring.
- Buy sawn timber only in its original packaging, which guarantees the safety of the goods for a long time.
Requirements for the base for laying grooved boards
The way the grooved boards are laid depends on the type of floor supporting structure. The classic option is considered to be logs or bearing supports, which raise the floor 70 mm above the base. In low rooms, boards are laid on plywood.
Lags for grooved boards
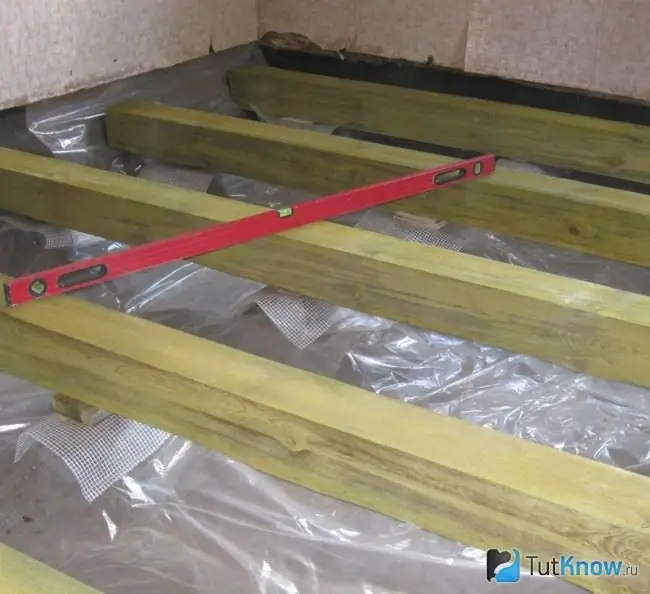
Lags are beams with a thickness of 50 to 70 mm, which are installed on a solid, even hard surface, for example, on a cement screed. If the base is uneven, instead of a lag, load-bearing beams are mounted, which are installed on point supports. Each beam of the supporting structure is leveled individually. For bearing supports, beams with a thickness of 100 mm or more are used.
When installing a lag, follow these recommendations:
- The distance between the lags depends on the method of fastening the material and the thickness of the grooved board. If the boards are laid perpendicular to the logs, the step of the supporting structures should be 60 cm. If the boards are laid at a different angle, the step is reduced. At a laying angle of 45 degrees, the distance between the support bars is 30 cm.
- The space between the lags and the ground cannot be filled. Ventilation of the floor takes place through it.
- So that walking is not accompanied by deaf sounds, soundproofing is laid on the beams - glassine, laminated substrate, synthetic winterizer.
- In the room, the beams are fixed in such a way that the boards lay parallel to the luminous flux coming from the window.
- In the corridor, the boards should be located along the main direction of travel.
Plywood underlay for tongue-and-groove boards
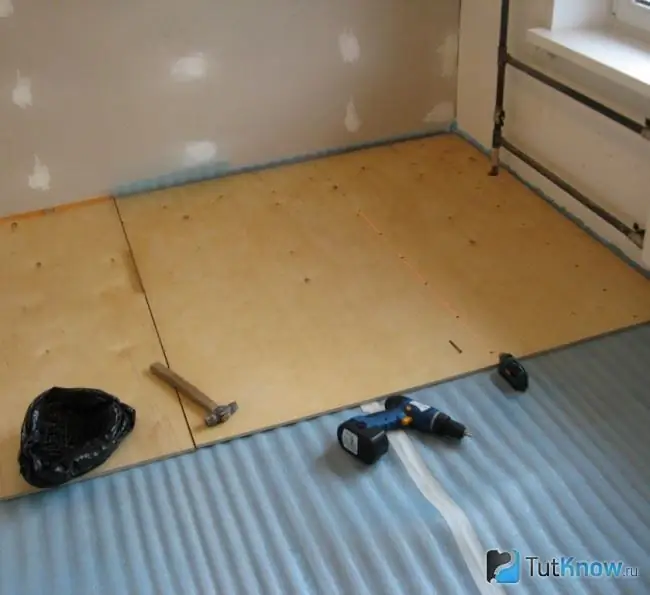
Plywood is used so as not to raise the floor level. For the substrate, moisture-resistant plywood with a thickness of at least 18 mm is suitable. Do not use thin plywood, as it reduces the rigidity of the base and can deform the boards.
Install plywood as follows:
- Check the non-planarity and horizontalness of the base on which the plywood will be laid, if necessary, rework it. Most often, plywood is laid on top of a concrete screed.
- Cut the sheet of material into several equal pieces. For example, a sheet of 1, 5x1, 5 m is cut into 4 parts to relieve internal stress.
- Place the workpieces on the floor diagonally to the floorboards and secure with 15 dowels. US2… Leave gaps of 2-3 mm between the parts, and 15 mm between the walls and plywood for thermal expansion.
- Sink the heads of the fasteners into the wood.
- Sand the surface with a grinder or drill with an abrasive head. For sanding, use a coarse grit sandpaper, P24 or P36. Vacuum up the dust after sanding.
- Make sure there are no greasy or other permanent stains on the surface. Clean with solvent if necessary.
Concrete floor for tongue-and-groove boards
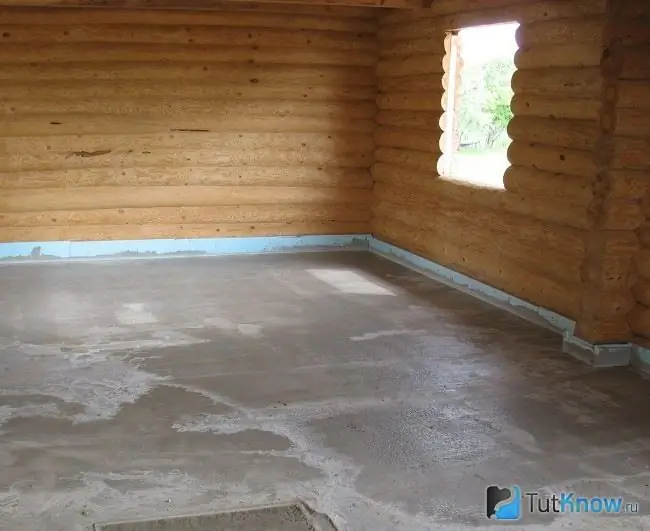
Boards are not placed directly on the concrete screed, only on logs or plywood. But the properties of concrete to absorb liquid lead to high humidity under the floor covering and rapid decay of the floor. Therefore, before installing the tongue-and-groove board, make sure that the concrete base meets the following requirements:
- Maximum concrete moisture content - 3%. The value is determined by a moisture meter. In the absence of a device, you can use the folk method. Place the plastic wrap on the concrete floor, tape it down. If after a day, water droplets appear on the bottom of the film or there is a damp spot on the floor, it means that the concrete is not dry enough.
- It is also necessary to check the condition of the screed surface, which must be even and flat. You will need a long ruler to check. Place the tool on the floor in arbitrary places and check that there are no gaps between it and the concrete. Surface deviations of more than 2 mm per 2 m of the ruler are not allowed. Unevenness causes the floor to squeak and sink.
- Use a hydrostatic level to measure the level of the floor. A slope of more than 0.2% of the maximum length of the room is not allowed.
- To level the floor, high areas should be sanded, low areas should be filled with self-leveling mixture.
- After leveling, saturate the concrete screed with several layers of polyurethane primer mixture.
- Foam film and ground mastic are used to create a moisture-proof barrier between the concrete and the wood floor. The mastic is applied to the floor with a roller, and a film is glued to it.
The technology of laying grooved boards on logs
There are several ways to install tongue-and-groove boards. The choice of option depends on the type of floor supporting structures. Installation of the cover on the logs consists of several stages: preliminary installation, final fastening, finishing.
Pre-assembly of tongue-and-groove boards
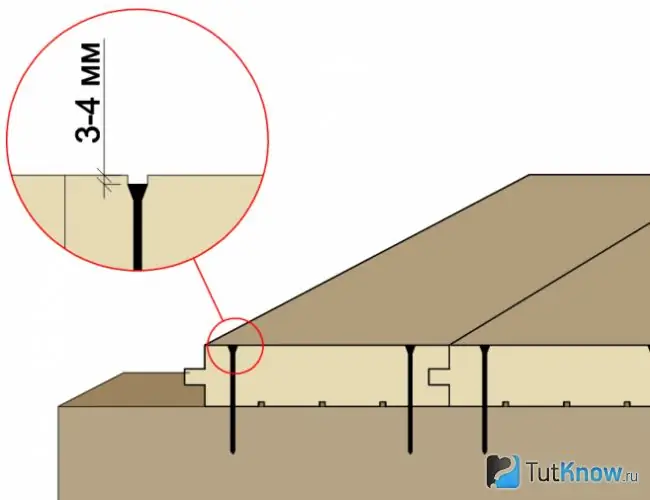
Preliminary work is carried out as follows:
- Bring the lumber into the room where you plan to lay it and leave it for 1 week. During this time, the humidity of the air and material will equalize.
- Choose a flat board that is wall-to-wall length.
- Lay the board on the joists with a comb against the wall, stepping back 10-15 mm from it. The gap allows the board to expand at high temperatures and changes in humidity. At the end of the work, it will be closed with a plinth. The size of the expansion gap depends on the length of the boards; more precisely, its value can be found in reference books on building materials.
- Fasten the first plank very securely. Screw the self-tapping screws into each lag to the full thickness. Instead of self-tapping screws, you can hammer in nails.
- Place the second board next to the first and align the comb with the groove. For a tight connection, hit the end of the second piece with a hammer through the block. Attach three more boards in the same way.
- At a distance of 10-15 cm from the last board, hammer the staples into the logs. Instead of staples, boards or bars can be nailed to the joists, which can also be used to tie products.
- Place a bar 50-70 mm long on the logs and slide it all the way into the board.
- Place two wedges between the bracket and the block, with the sharp ends facing each other.
- Using hammer blows on the wedges, pull the boards together, while the spikes will fit tightly into the grooves, choosing the gaps between the boards.
- Screw the self-tapping screws into the bottom groove strip of the last board at an angle of 45 degrees and fix the board to the logs. To prevent the bar from bursting, make holes for self-tapping screws in the board and logs.
- Instead of wedges, a screw jack can be used to tighten the boards. On the logs, nail bars or boards against which the jack will rest. Place the tool on the beam. Put a wooden block (spacer) between it and the board and slide it all the way into the board. Through the block, the jack will act on the boards.
- Cover the entire floor with boards, fixing every fourth floor to the logs with self-tapping screws.
- The middle rows are allowed to be assembled from short boards, the main thing is that the edges are located on the logs. Place the joints of the short ones in a checkerboard pattern. The installation of the boards in a run is made difficult by the large number of cuts, which must be strictly perpendicular to the ends of the boards. Cut the boards according to templates for reliability.
- Tighten the last boards with wedges, which are hammered into the gap between the wall and the board.
- If the outer board does not fit into the gap, trim off the excess parts with a circular saw.
- The assembled floor is left temporarily fixed for six months. The boards will sit and take their final shape.
Final fixing of tongue-and-groove boards
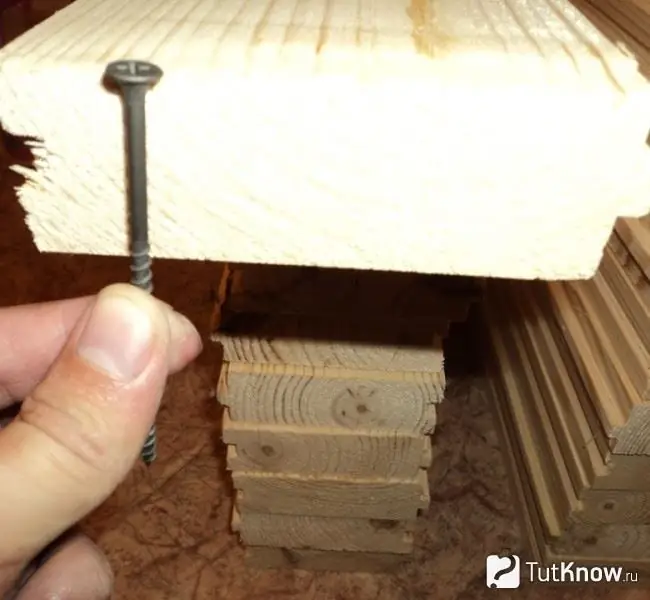
At this stage, the identified floor defects are eliminated and its restocking is performed:
- Examine the surface for cracks that can form due to shrinkage of the lumber.
- To eliminate the gaps, the floor is re-cut and each board is finally fixed.
- The cuts are fixed with self-tapping screws 3x35-40 mm (for boards with a thickness of 40 mm), which are screwed in at an angle of 50 degrees from the side of the spike. The hardware is installed every 30-40 cm. It is recommended to drill holes before screwing in the screws.
- During fastening, the boards should be tightened using one of the methods described above.
Finishing grooved boards
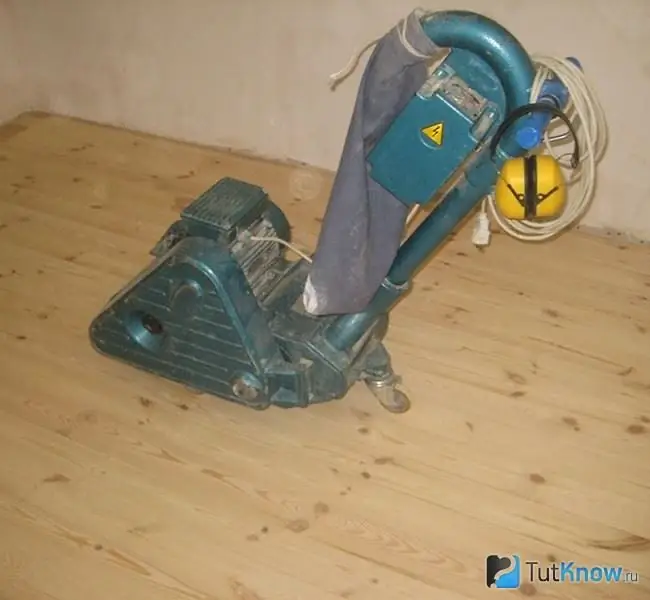
The front side of grooved boards is usually processed very high quality at the manufacturing stage and does not need additional grinding. But softwood products sometimes need to be reworked.
Surface grinding is carried out with grinding machines - surface grinding and angle grinding machines. The first device is used to treat the entire floor. Corner is necessary for grinding hard-to-reach places. In the absence of mechanisms, you can use a sanding block or a hand cycle.
Processing takes place in three stages - along, across and diagonally of the boards. After sanding the boards of their coniferous species, the pile rises. To eliminate it, use a triple primer and sanding of each layer.
Pine and spruce boards must be varnished after grinding to increase their strength, which compensates for their softness. The varnish is applied in several layers. Larch boards do not need to be covered with a protective layer.
Fixing grooved boards with glue
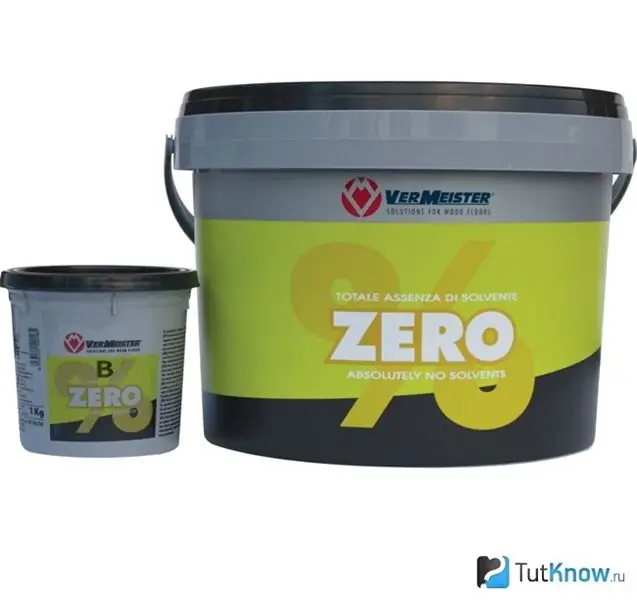
The boards are glued to the substrate in rooms with low ceilings. For work, you need glue that contains synthetic resins - polyurethane or epoxy-polyurethane. Such solutions are distinguished by their strength and ductility, which ensures the movement of the flooring during thermal expansion.
Fixing the boards in this way does not allow you to adjust their position, therefore, before laying the tongue-and-groove board on the glue, perform a model assembly of the floor dry. Only after satisfactory results are obtained can the boards be glued.
Planks are laid on glue as follows:
- Measure the length of the wall and cut a board 30 mm shorter than the result from the workpiece.
- Place the first piece next to a wall with a gap of 15 mm between the canvas and three walls. The spike of the board should be turned towards the wall.
- Draw the outline of the board with a pencil, which will allow you to glue on a section of plywood for only one board.
- On the other side, lay down the second plank and slide until the groove lines up with the tenon.
- Likewise, dial the entire floor of the room. Don't forget to trace the outlines of the boards. Hit them periodically with a hammer through a piece of wood.
- After installation, mark the position of the boards relative to each other and disassemble the floor.
- Apply a thin layer of glue to the plywood using two spatulas. The first one should be smooth, with its help the solution is spread on the floor. The second is notched, it evenly distributes the glue over the surface. Apply it to the area marked with a pencil.
- Place a plank on the mortar and press it well to the floor. For secure adhesion, fix it with studs, which are hammered into the thorn at an angle of 50 degrees.
- The rest of the boards are glued in a similar way, they are laid according to the marks of relative position.
- After installing all the boards, do not walk on them until the glue is completely dry.
How to fix a tongue-and-groove board to the floor - watch the video:

The tongue-and-groove boards allow you to obtain a practical and high-quality coating with minimal effort. The main condition for obtaining a good result is adherence to installation technology and a serious attitude to work.