The use of clay as a heater for the floor, the features of such thermal insulation, its advantages, disadvantages and work technology. Clay floor insulation is the oldest but effective way to eliminate heat loss in a stone or wooden house. Currently, it is quite popular due to the environmentally friendly materials that are used in the process of installing such thermal insulation. You will learn how to insulate the floor with clay from our article.
Features of thermal insulation of the floor with clay
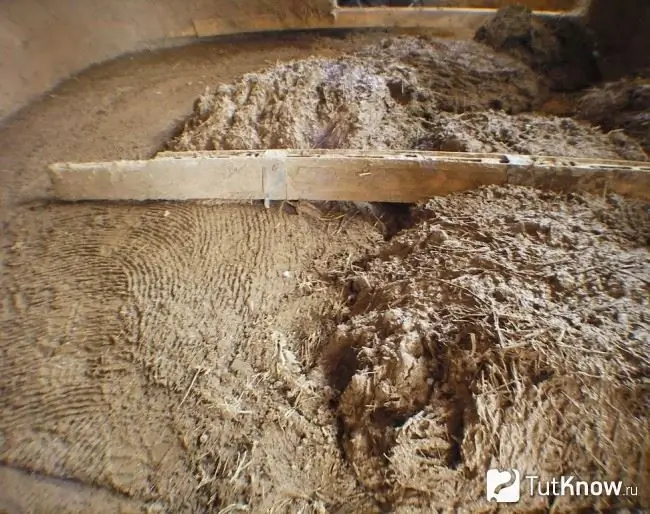
Red clay is suitable for floor insulation in this way. It is distinguished by high plasticity and the presence of small pores. White clay also has good performance properties. If necessary, it can also be used as a heat insulator. The color of the clay depends on the minerals it contains. Manganese and iron give the material a reddish color, organic impurities - a gray or black tint.
Clay, depending on the content of sand in its composition, is lean, bold and oily. The latter type of material is most suitable for thermal insulation of the floor. It is not difficult to distinguish such clay - it is soapy to the touch.
Often, to achieve the maximum effect when insulating the floor, a mixture of clay with sawdust or chopped straw is used. The choice of filler for such a mixture must be treated with care. The best option is considered to be oak or softwood shavings. The reason for this is essential oils, which are abundant in spruce, pine and larch. These substances have a well-pronounced antibacterial character, which reduces the risk of fungus formation in the pores and on the surface of the insulation. In addition, before use, the clay filler is additionally treated with a fire retardant and antiseptic. Oak shavings do not rot or swell from moisture.
Due to its unique properties, clay serves not only as a heater, but also as an excellent waterproofing. Supplemented with wood material, it can even be used to insulate the floor in a bath, without being damaged by contact with hot air. Not all materials used for heat and waterproofing have this property.
The process of thermal insulation of the floor with clay does not take much time. However, it should be borne in mind that the drying of the moistened insulation will last about a month, provided that the ambient temperature is positive.
Pros and cons of clay warming
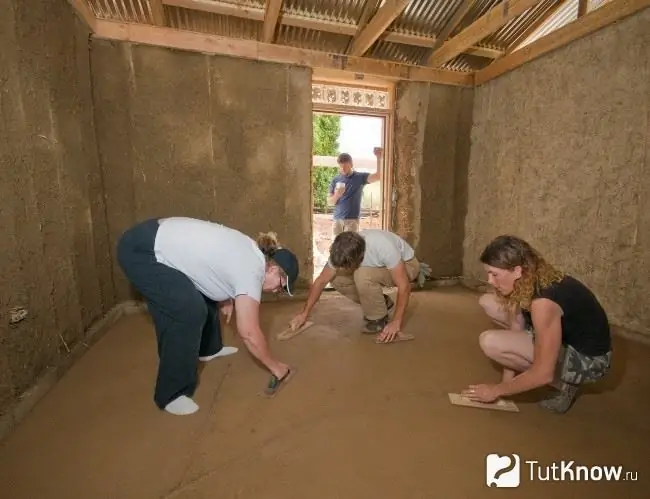
The ability of clay to keep warm is not its only advantage. In addition, the material has other positive qualities, which include:
- An elementary technology for applying a heat-insulating mixture to the base surface. Any home master can cope with its preparation and styling on its own.
- Low price of the material or the ability to get it for free in places of natural occurrence.
- Low thermal conductivity of clay allows you to insulate floors even on the ground.
- Clay insulation is inedible for insects and mice.
- Clay is environmentally friendly and therefore does not emit harmful substances into the air.
The disadvantages of this method of floor insulation include a significant duration of work and their high labor intensity.
Clay floor insulation technology
Clay for floor insulation can be used in the form of a liquid mixture with sawdust or ready-made panels. After the clay mixture has hardened, the surface of the insulating layer becomes so strong that you can move along it without fear of cracking the material. The work on thermal insulation of the floor consists of several stages: preparation of the base, laying of insulation and a protective layer of the film. Let's consider them separately.
Preparatory work
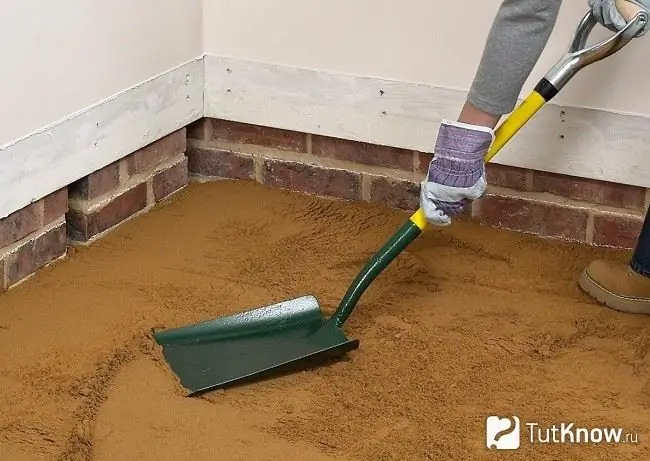
Before starting thermal insulation, the base should be cleaned of debris. If it is planned to lay ready-made clay blocks, it is recommended to first perform a cement screed 1-2 cm thick under them. If you plan to pour a wet mixture of clay with sawdust, you can use wooden floor beams as formwork under it. Before installing the insulation, the wooden surfaces of the floor structure must be treated with an antiseptic, for example, creosote.
As a substrate for a wet clay mixture, you can use a waterproof polyethylene film of 150-220 microns. It can be glued to a cement base or fixed to wooden floor joists. The underlayment should be overlapped. This will help prevent the clay mixture from leaking before it dries.
To work on the preparation and laying of the working mixture of insulation, it is necessary to prepare a trough for kneading it, a bucket, a construction mixer, water, sawdust and clay.
Installation instructions for clay insulation
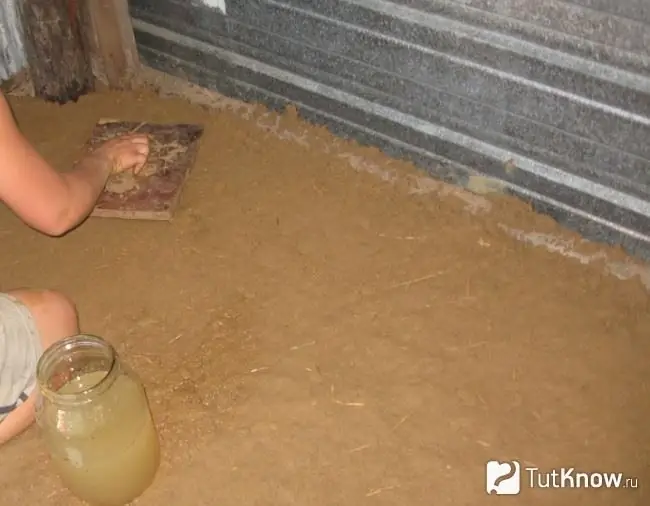
Clay can be used as floor insulation, as already mentioned, in two different ways. In this case, the method of manufacturing a heat insulator determines the technology for its further installation. In one case, a still wet mixture of clay with sawdust is poured onto the floor, in the other, panels are made from it, which, when dried, can be laid like mineral wool slabs.
In the process of preparing the mixture, an important point is to observe the correct ratio of its components, since in the future this will avoid the appearance of cracks on the finished surface of the clay insulation. If the working mixture is planned to be laid on the base in a wet form, then 2/3 of the same bucket of sawdust should be taken for one bucket of clay.
First, you need to block the clay with water to obtain a mushy consistency of the material. The amount of water in this case depends on the initial state of the clay. Clay is capable of absorbing moisture for a long time, especially when the raw material is dry and hard.
After a few days, the clay will acquire the necessary consistency, after which it needs to be diluted a little with water, add sawdust and mix well until a thick and homogeneous mixture. Use a garden hoe, blender or small concrete mixer for mixing. The finished composition can be laid on a prepared base.
Clay slab insulation is usually used in an already built house and is made in a slightly different way. For the manufacture of panels, the ratio of clay to sawdust should be 1: 1. The mixture is poured into special molds that must be made in advance. They represent the usual cells of a lattice made of bars with a thickness of 150-200 mm. The cells must be at least 500x500 mm in size. Before making the panels, the grille should be laid on a plywood sheet. This will allow you to conveniently pour the mixture into it and form the neat ends of the insulation plates.
Pouring the working mixture into the grid cells can be carried out using a bucket up to the upper edge of the bars. The resulting surface should be leveled with a spatula and leave the material to dry completely.
It is not recommended to dry the clay insulation panels in the sun, this can cause cracks on the surface of the products. Above the forms, you can make a canopy or simply throw grass on top of them, creating a sufficient degree of shade. Depending on the humidity of the air and its temperature, the clay mixture hardens in 7-15 days. If small cracks appear, they can be easily repaired with liquid clay.
To obtain an insulating layer, the finished slabs must be laid on the base with minimal gaps. Joints between products should be sealed with liquid clay to avoid heat loss through voids.
Features of insulation protection
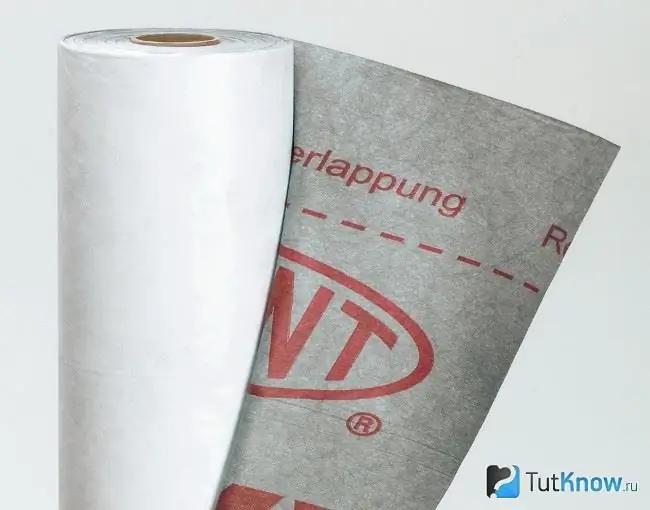
Any enclosing structures of the house, including floors, which come into contact with the outside cold and inside warm air, are exposed to condensation, which manifests itself in the form of drops of moisture on the surface. Therefore, in order to prevent the insulation from getting wet from condensation of steam coming to the floor from the side of a warm room, the clay coating is protected with a vapor barrier membrane.
When choosing it, you need to pay attention to the characteristics of this material. There are membranes that allow steam to pass through partially, while other films trap it completely. The versatility of the insulation, as well as its affordable price, will be the best solution for the purchase.
The canvases of the vapor barrier film should be laid on the insulation with an overlap of up to 150 mm, its surface should be completely covered. The seams between the strips of insulation should be taped to seal them.
After carrying out all the above measures, the flooring can be attached to the floor logs. If they are absent, perform a screed over the insulating layer of clay. In the first case, a ventilation gap must be left between the floorboards and the insulation. It will ensure the absence of dampness in the space under the floor and the safety of the wooden elements of its structure.
How to insulate the floor with clay - watch the video:

In recent years, many consciously choose natural materials for construction and decoration and are increasingly abandoning various polymers. If the environmental friendliness of materials is of paramount importance to you, clay floor insulation is what you need. Good luck and health!