The choice of mineral wool for floor insulation, pros and cons, as well as options for heat-insulating layers based on this material. Thermal insulation of the floor with mineral wool is the creation of a multi-layer structure for comprehensive protection of the floor from cold, overheating, moisture, insects and mold. The device of the heat-insulating layer depends on the operating conditions of the base. We will talk about how to mount the product in this article.
Features of work on floor insulation with mineral wool
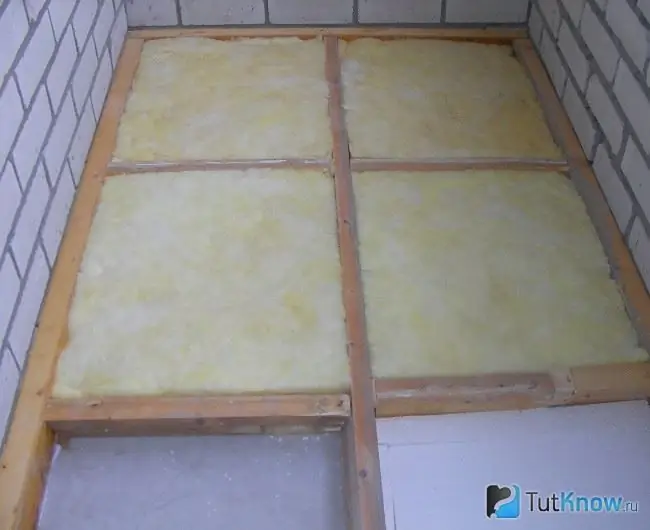
The insulator is a material of a fiber structure on a synthetic basis that is saturated with an inert gas that retains heat well. Mineral wool for floor insulation is sold in the form of rolls and slabs of various sizes and densities, which affect the choice of installation method.
The rolls have low rigidity, and a wooden crate is made for them in advance. They are ideal for large areas because the total length of the gaps between the individual parts is minimal. Products are produced in widths of 1, 2 and 0, 6 m and a maximum length of 10 m. Usually, two layers of roll insulation are laid to ensure the optimal thickness - 100 mm.
Plates are more often than rolls used for laying on the ground. They differ in the presence of hydrophobized components. They have two-sided rigidity: one side is harder, so their installation should be carried out taking into account the manufacturer's requirements. In order not to be mistaken, markings are applied to the surface in blue. They come on sale in a package that is enough to cover from 1 to 4 m2 in one layer. The dimensions of the panels are 50x100 cm. Plates of high density can be laid without lathing and filled with a screed.
In homes, mineral wool is used in such cases:
- For insulation of floors above a cold basement;
- For heat and sound insulation of interfloor ceilings;
- To protect the attic floor.
The thickness of the product depends on the climatic conditions and the purpose of the room. The floors of houses in the southern regions and summer cottages, which are used only in summer, are covered with samples of 50 mm thickness.
The same materials are used on the floors. This is due to the need to maintain the height of the room and the low temperature requirements in these places. In country houses, the thickness of mineral wool for floor insulation can be up to 200 mm.
The product has a harmful effect on humans due to the presence of fine fibers that irritate the skin. When working, you should adhere to the elementary safety rules:
- Avoid contact with the material when laying. Wear goggles, gloves, long sleeves, and a respirator. Change after work.
- Keep rolls and slabs out of the reach of children.
- Prevent fibers from spreading throughout the apartment. After warming, immediately clean the place of work.
Mineral wool absorbs moisture well, therefore, to protect it from getting wet, the composition of the insulation "cake" must necessarily include hydro and vapor barrier films.
Advantages and disadvantages of floor insulation with mineral wool
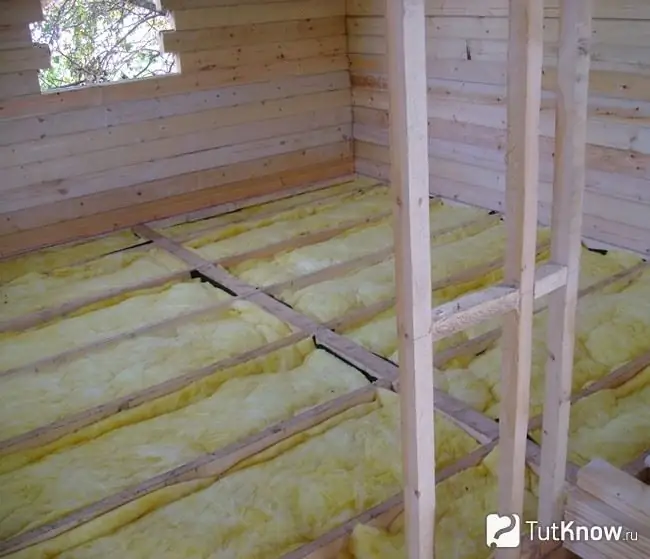
The heat insulator has the qualities that make it the most common material for floor insulation:
- It does not burn, does not emit dangerous vapors under the influence of fire. Often used in fire hazardous areas.
- Due to its low weight and ease of cutting to obtain fragments of the required sizes and shapes, installation time is reduced.
- When laying, no fixing to the base is required.
- The use of mineral wool increases the sound insulation of the floors.
- The cost of mineral wool is lower than the price of other heaters.
- Fungus and mold do not take root in the fibers. The material doesn't like mice.
- When dry, the product does not change its shape and size when the temperature fluctuates.
- The material does not require replacement during the entire life of the house.
When choosing a floor covering method, you should know the disadvantages of mineral wool:
- In most cases, the height of the ceilings will decrease due to a sufficiently thick heat-insulating layer, which includes the logs.
- The product absorbs water well, so the "cake" must contain hydro and vapor barrier, which increase the cost of work.
- Mineral wool should not be used in damp rooms.
Mineral wool floor insulation technology
Thermal insulation of the base is carried out in a specific sequence. Deviation from the technology of installation work will lead to constant heat leakage and may cause loss of properties of the heat insulator. Refinement of each type of overlap has its own characteristics.
The choice of mineral wool for floor insulation
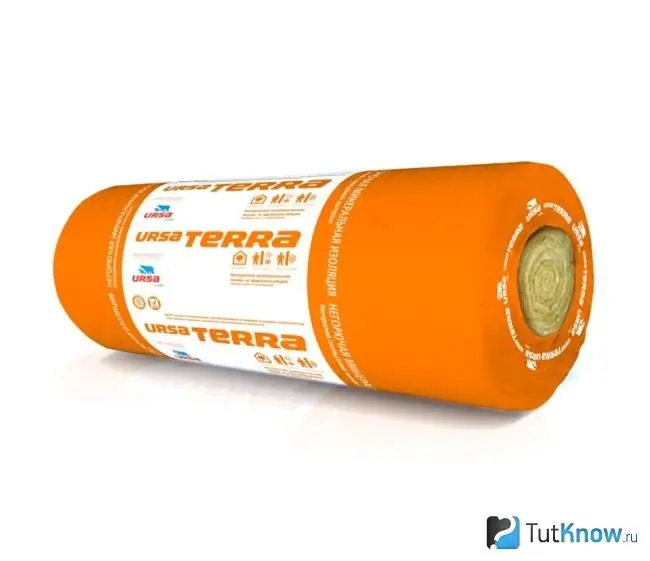
When buying a product, you need to familiarize yourself with its characteristics and check the quality of the product.
The main parameter of mineral wool is density. In residential premises, material is most often used in rolls with characteristics of 35-40 kg / m3 or slabs up to 90 kg / m3… Solid blocks are also used in industrial facilities.
For laying under the screed, especially dense slabs with a hardness of more than 150 kg / m are used3 with very low thermal conductivity. The panels are made in small sizes, which is convenient for work. In addition to heat-insulating properties, they have excellent sound-insulating and fire-fighting qualities. They are very expensive, therefore they are not popular among users. Moreover, such products are not produced in Russia. For example, Stroprock wool with a density of 161 kg / m2 supplied from Poland.
The declared characteristics of mineral wool at home cannot be checked, but according to some signs it is possible to determine its quality:
- Ask to show the storage conditions for products in the warehouse. If it lies outdoors, inspect the packaging. Polyethylene breaks are not allowed. Unprotected goods must be kept in a dry place.
- Do not purchase wet cotton wool, even if the price is very favorable. In a wet state, it does not retain heat, and after drying, it does not restore its qualities.
- Buy samples from the same manufacturer to ensure the same density.
- To avoid counterfeiting, choose products from well-known companies.
- Discard inexpensive products. The reason for the reduction in price is most likely a deviation from the manufacturing technology. The material will quickly shrink and lose its quality.
Installation of mineral wool on a wooden floor surface
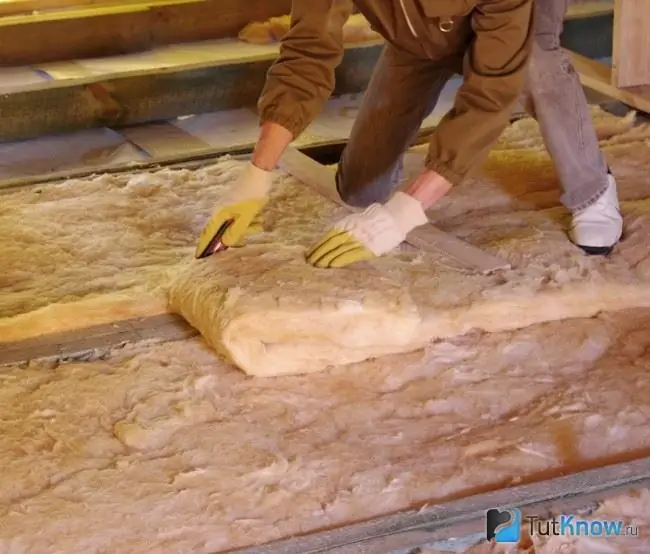
To insulate the floor along the logs with mineral wool, the flooring must be completely dismantled. Therefore, check the condition of the coating before use. If there are no defects, remove it carefully in order to return it to its place after repair.
Further work is performed as follows:
- Inspect the logs, install new ones to replace the rotten ones. Soak the items with antiseptic agents against mold and insects. Place shims or wedges under the movable battens.
- Check the location of the upper surfaces of the beams in the horizontal plane.
- Attach the subfloor planks to the bottom of the battens. If the distance between the logs and the ground is small, nail the cranial bars, and then mount the support structures on them.
- Place a vapor barrier membrane on a wooden base with an overlap on the beams and on the wall by at least 10-15 cm. The film will protect the insulation from moisture, which impairs its thermal insulation properties. As a vapor barrier, you can use a polyethylene or vapor barrier film coated with aluminum. Its cost is low, but its efficiency is low due to the possible appearance of condensation. The sheets are laid with the metallized surface up. The best option for vapor barrier is a special membrane. This is a thick canvas consisting of several layers of waterproofing materials. Align the foil thoroughly after installation and press firmly to the base. Ventilation gaps are not allowed.
- Secure the canvas to the walls with metallized reinforced tape, which is designed for sealing and thermal insulation. The tape must have a high degree of adhesion, the ability to resist bacteria and moisture, and maintain its qualities in the range of -20 + 120 degrees. Seal the joints of the fragments with each other in the same way.
- Place the mineral wool on the foil. If using a roll, unwind it and press firmly against the logs and base. The presence of gaps is not allowed, they lead to the insulation getting wet and the appearance of cold bridges. When laying the second layer, make sure that the upper products overlap the joints of the lower row. Mineral wool should be handled carefully so as not to crease the fibers. This can negatively affect its performance.
- Cover the sheets with waterproofing to keep out water. Lay the film with an overlap on the walls and adjacent fragments. Glue the joints with reinforced tape.
- Install the finished floor, leaving a clearance of at least 5 mm for ventilation between the lumber and the membrane. The deck can be a durable material such as fiberboard, chipboard, plywood or planks. It can be used for flooring.
When insulating wooden floors at the stage of building a house, mineral wool can be laid on a prepared base. The volume and order of work when insulating the floor with mineral wool will depend on its design.
Mineral wool insulation instructions:
- Clean the concrete floor from dust and dirt. Seal the gaps with cement or other mortar. Remove irregularities with a cement-sand screed. If the alignment is not carried out, then uneven loads will act on different areas, which can cause the destruction of the slab.
- Use crushed stone to level the subgrade. Cover it with a layer of 10 cm and compact. Add sand on top. Instead of crushed stone, expanded clay can be poured, it will become additional thermal insulation.
- Lay the vapor barrier with an overlap on the wall at the same height as the floor.
- Mount the logs in increments of no more than 90 cm (the optimal width is 50-60 cm). The distance between them should be 10 cm less than the width of the roll (or slab). The spacing of the supports is also influenced by the size of the room.
- The thickness of the beam should be 5-10 mm more than the thickness of the insulation. If you plan to lay the insulator in two layers, also increase the height of the battens. Align the surfaces of the supports in a horizontal plane and secure in this position.
- Further work is being carried out as described above.
Laying mineral wool on the floor under the screed
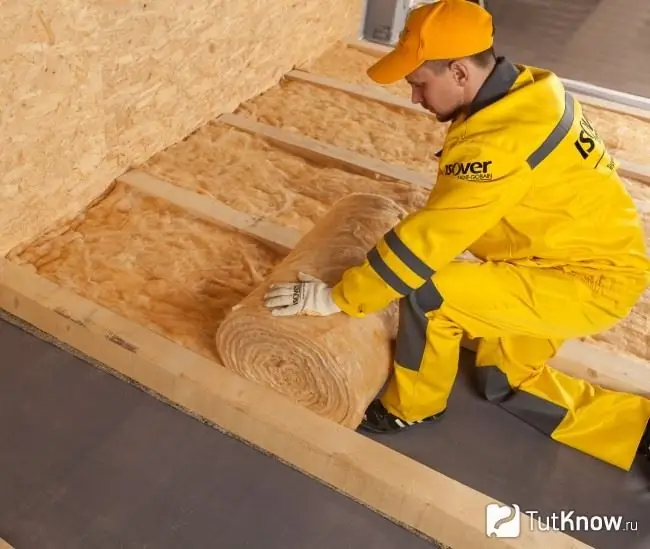
If the base is made of soil, insulation can be performed without rigid connections.
Floor insulation works with mineral wool:
- Compact and level the ground. Fill the area with a 150-200 mm thick sand-soil cushion and compact it carefully. Align the surface horizontally. If the ceiling is being finalized over a warm basement, the layer may be thinner.
- Place cellophane on the sand to protect it from moisture.
- Perform the installation of mineral wool. For this, it is necessary to use rigid boards with a density of at least 150 kg / m3 with increased resistance to moisture. The insulation thickness can be up to 20 cm, depending on the climatic zone in which the house is located.
- Cover the material with roofing material on top in one layer with an overlap on the wall and between each other. Glue the joints with reinforced tape.
- Make a reinforcing mesh for reinforcement and install on the slabs.
- Pour the "cake" with concrete of class B12, 5 or higher. Level the screed surface horizontally.
- Install the floor covering.
Thermal insulation with mineral wool for the floors of attics and attics
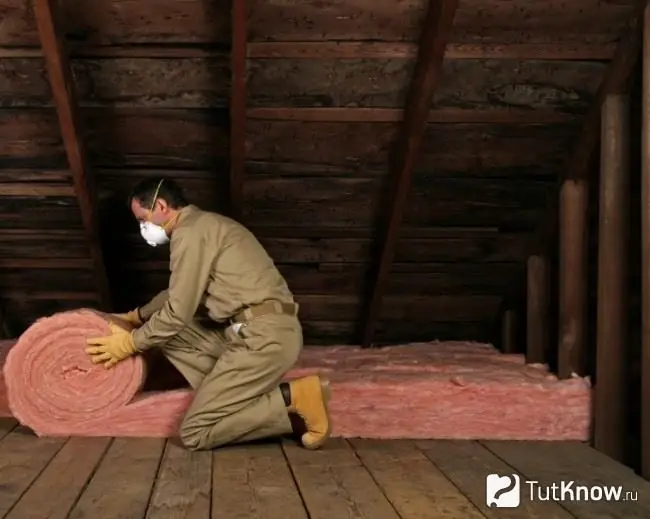
Thermal insulation of these rooms is often performed in low-exploited houses equipped with special roof ventilation. Together with the insulation, there must be a vapor barrier film.
Warm air, together with water vapor, rises to the attic, in the absence of a vapor barrier, it will pass through the cotton wool and condense on the rafters, which will eventually lead to their rotting. Some of the moisture will remain inside and will cause a loss of thermal insulation properties. To avoid problems, perform operations according to the technology of floor insulation with mineral wool in attics:
- On the attic floor, lay a vapor barrier with an overlap on the wall and adjacent areas. Glue the joints with reinforced tape.
- Roll the rolls near the wall, starting from the farthest point of the attic. Press the strips firmly against the partition.
- The second strip is laid in the opposite direction and pressed against the first. No gaps allowed.
- If there is an obstacle, the material is trimmed in front of it, and the next piece is cut to fit the shape of the obstacle.
- A second layer of the product is usually laid on top with the condition that it overlaps the joints of the lower row.
- If there is no under-roof waterproofing in the attic, cover the insulation with a superdiffusion membrane, the vapor permeability of which is not less than 1000 g / m22… It should be laid in compliance with the manufacturer's requirements. she has a one-sided principle. If the roof is waterproofed and the attic is equipped with forced ventilation, it is not necessary to use the top film.
How to insulate the floor with mineral wool - watch the video:

The creation of an insulating layer on the floor using mineral wool is considered a difficult process due to the presence of several materials in its composition. Deviations from the installation technology may result in low room temperatures. If you decide to insulate the floor with mineral wool with your own hands, carefully study the features of the thermal insulation process and analyze the structure of the base.