The main nuances of facade insulation with stone wool, its main characteristics and disadvantages, surface preparation and material installation, the “wet facade” technique, final finishing. Insulation of a facade with stone wool is a reliable and absolutely environmentally friendly process of creating a heat-insulating layer outside residential or industrial buildings. Stone wool is allowed to be used even in children's and recreational facilities. It is made from natural stone that is melted in a furnace at a high temperature. Thus, a durable and warm material is obtained that will bring a piece of nature into the room.
Features of facade insulation with stone wool
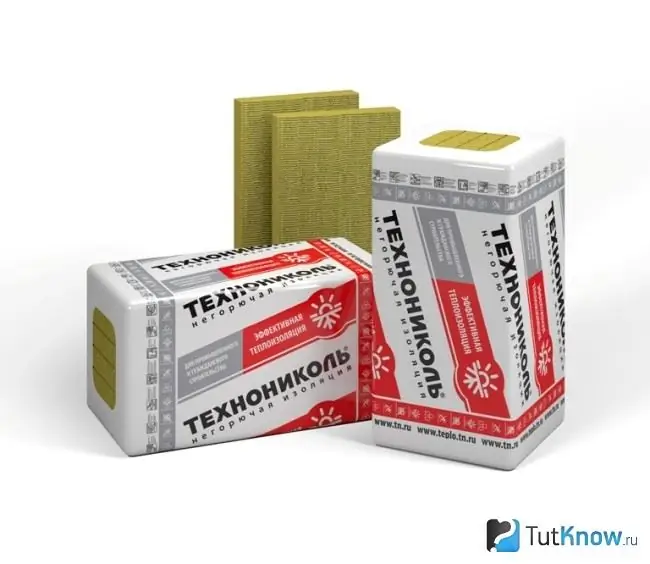
In the process of saving energy resources and their safety, it is difficult to overestimate the role of thermal insulation. Stone wool for the facade of a building allows you to spend less energy on air conditioning and heating, thereby reducing the impact on the environment.
Moreover, this material belongs to the category of the few that can boast of a positive energy balance. This means that the amount of energy that is saved with its help is much higher than what is spent on its production. In addition, the cotton wool used for facade work is water-repellent.
Insulation of this type is made, as a rule, in the form of slabs. They can be of 2 basic sizes: 0, 5 by 1, 0 meter or 0, 6 by 1, 2 m. The thickness of such products can range from 5 to 15 cm, but 10- centimeter.
Insulation of walls with stone wool from the outside is most in demand in the following cases:
- For ventilated curtain walls as a thermal insulation layer;
- To protect production equipment, heating systems and heating plants;
- As a heater for any building structures, buildings of different types and purposes;
- As an internal insulator;
- For external insulation with further plastering;
- For thermal insulation of flat roofs, including without the use of cement screed;
- For floors, roofs, walls and other occasions.
The difference in the cost of this material will depend on the composition of the stone wool. In some varieties, manufacturers add additives and slags, which significantly impair the physical properties of the finished insulator. But the customer is given the opportunity to choose wool for insulation of various sizes, thicknesses and densities.
It is best to purchase stone wool for thermal insulation work, which is released in slabs, and not in rolls, since they are not so susceptible to deformation due to their higher density.
Advantages and disadvantages of stone wool as insulation

Thanks to the special technologies that are used in the production of the material, the insulation of the facade with stone wool gives such a coating the following advantages:
- Durability … The service life of basalt slabs is practically unlimited. Having insulated the premises once, the customer can forget about the existence of such a problem in the future.
- Thermal insulation … According to this indicator, stone wool is one of the warmest materials. This is achieved due to the unique porous structure, in which it retains heat well in the room in winter, and does not let the heat through in summer.
- Soundproofing … It is achieved by the fact that the basalt fibers are closely intertwined, while the space between them is filled with air particles.
- Fire resistance … Unlike expanded polystyrene, stone wool is a completely non-combustible material. It can withstand heat treatment up to 1000 degrees Celsius.
- Moisture resistance … This quality is given to the material by impregnation with a special water-repellent mixture. The increased vapor permeability contributes to the removal of excess vapors.
- Environmental Safety … Stone wool belongs to chemically and biologically resistant materials: it is 100% safe for both humans and the environment.
- Shape retention and ease of processing … These characteristics do not need explanation, because the cotton wool retains its original shape and is also easily influenced by the tool.
Facade insulation technique with stone wool
Insulation of facades with stone wool or other heat-insulating materials must be carried out at an outside air temperature in the range from +5 to +25 degrees Celsius. The air humidity indicator should be at 80%. It is advisable that direct sunlight does not fall on the surface of the unprotected insulation.
Preparatory work before insulating the facade with stone wool
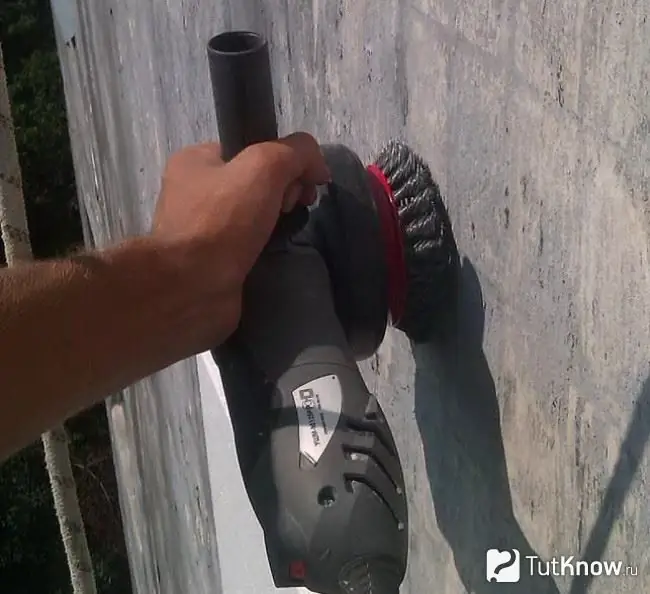
First of all, the facade of any building is cleaned of cement smudges, crumbs, protruding metal pins and other irregularities. Home communications are dismantled without fail, namely any wiring, brackets, pipes and much more. Cracks, chips, depressions must be cleaned and repaired with mortar. Only then can the walls be primed.
If all of the above measures have been completed, you can start installing the guide profiles. He will be entrusted with the task of holding the first row of insulation material, which will make it possible to lay out all the following rows evenly. The metal profile is attached to the wall surface with dowels, 60 cm away from the floor.
Instructions for installing stone wool on the facade
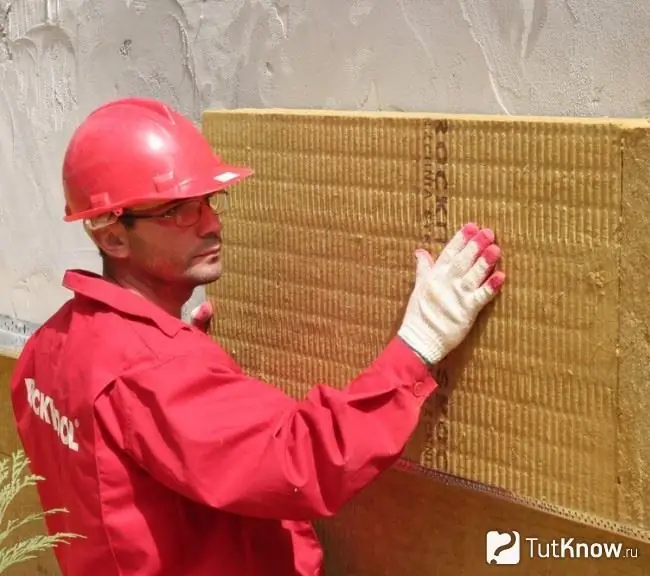
Before starting work on fixing the insulation, it is necessary to prepare an adhesive solution, which is sold in the form of a dry powder, packaged in 25 kg bags. A separate large container is taken (you can have a bucket, a basin), into which the required volume of water is poured, according to the instructions on the package. After that, the required amount of dry glue is poured, and then everything is mixed until a homogeneous state is obtained.
We carry out work on the installation of stone wool according to the following instructions:
- The prepared adhesive is applied to the surface of the product, after which it is pressed against the wall surface. The board should be smoothed and leveled immediately, without waiting for the glue to fully set.
- Each subsequent row can be started to lay out immediately after the previous connection has been grabbed. A bunch is made in approximately the same way as in the case of a brick wall.
- After fixing the boards to the glue solution, they need to be additionally strengthened. For this, dowels of the "fungus" type are used, and holes are drilled under them in the center and edges of each product.
- The procedure for laying stone wool is carried out in the direction from bottom to top, and each piece of insulation will additionally be fixed on the dowels.
So, finally, the installation of stone wool on the facade is finished. On top of it, a thick layer of glue is applied again, into which the reinforcing fiberglass mesh is pressed. You need to start this work from the corners, and for this, special mounting angles are used. You can start reinforcing the remaining walls and plastering in about a day.
If there is a need to carry out insulation for siding instead of plaster, then a different work technology is used. Izospan is attached to the wall, which will protect the insulation from moisture and wind outside. The accumulated moisture will be removed from the material without coming back. In this case, no glue is used - stone wool is fixed on the facade with dowels immediately. On top of it, another layer of Izospan is attached, be sure to leave a free gap. Then you can start decorative siding processing.
Insulation layer protection and finishing
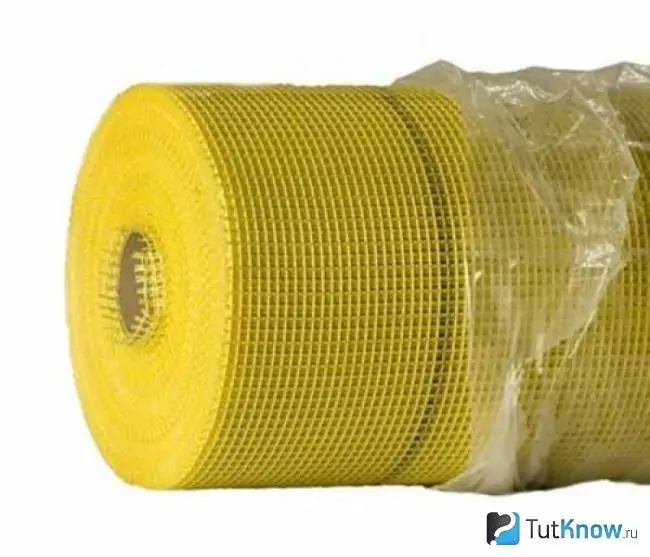
You cannot do without the use of a reinforcing facade mesh. They begin to fix it from the very top of the wall with mortar or special studs. Each cut piece of canvas should lie on adjacent pieces with an overlap of at least 10 cm. This is done in order to avoid further cracking of the plaster.
Even if the wall is not perfectly smooth and even, you can make another layer of rough plastering with a thickness of 4 to 10 mm. After complete drying, the surface can be prepared for decorative coating. First, all flaws are removed with sandpaper, including dried glue drips, and then it is covered with ground paint.
We figured out how to insulate the facade with stone wool. The last type of work is the finishing of the outer walls. It performs 2 tasks at once - protective and decorative. That is, it will protect the thermal insulation of the house from wind, frost, dampness, ultraviolet radiation, on the one hand. On the other hand, it will form the external appearance of the building facade.
For finishing works, various types of decorative plasters can be used, ranging from mineral (based on lime or white cement) to acrylic and binders. The structure of the plaster and the size of the grain will determine its drawing and final appearance. It is prepared in approximately the same way as the glue mixture is kneaded.
The solution is mixed in water until a homogeneous mixture is formed, which is thrown onto the wall with a spatula. However, it is still necessary to give the surface a certain texture pattern. To do this, wait a couple of minutes until the mass begins to dry out. After that, it is smoothed with movements from top to bottom. Since the plaster contains tiny lumps, when ironed, they will begin to press through small grooves. Thanks to this, an interesting texture pattern is obtained.
Upon completion of drying, the surface can be painted in any color, this is especially true for mineral solutions, which are produced completely white. Some people opt for an acrylic finish, which is highly durable and plastic, does not fade, and tolerates temperature extremes well.
Do not forget about facade painting. For this, the industry produces water-based paints. They include acrylic and other polymers, silicone, liquid potassium glass and other components. As for the actual color varieties, there are several thousand different tones and halftones.
Wet facade technology and its features
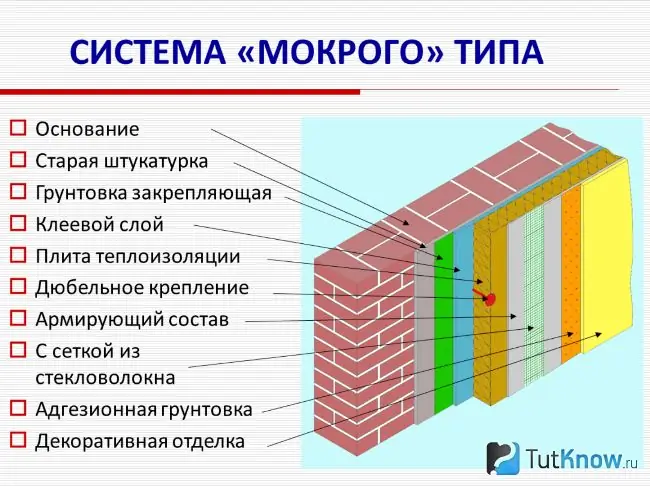
One of the most popular insulation systems. The wet façade technology got its name from the fact that plaster and glue are used for thermal insulation, which are mixed with a large amount of water.
This technique is practical, it is easily used both for repairing the facades of old buildings and for insulating new buildings. It can give an aesthetically pleasing look to interiors of various types of buildings.
With such insulation, the facade of the structure is not exposed to excessive loads, which means that there is no need for additional strengthening of the foundation. The useful area in the rooms will not decrease either, but the "wet method" thermal insulation will reliably protect from heat loss, from freezing, from the appearance of fungus, etc. Even in hot weather, this system reduces the heating of the load-bearing structural elements and thus keeps the temperature in the house at an optimal level.
The structure of such a facade can be represented in the form of several layers:
- The supporting structure on which the insulation and all other layers will be attached;
- Thermal insulation consisting of pieces of stone wool;
- Reinforcement - most often represented by a resistant fiberglass mesh;
- Decorative finishing (at the choice of the owner).
Carrying out preparatory work for a wet facade is no different from other insulation methods. The working areas are thoroughly cleaned of protrusions and debris - plaque is removed, fungus is scraped off, excess solution is knocked off. If there are serious defects in the wall, leveling or reinforcement may be required. After completion of all preparation, the surface is coated with a primer, which should increase its adhesive properties.
After that, the glue is mixed, with the obligatory observance of the proportions, since this can affect the effectiveness of fixing the insulation. A sheet of stone wool is taken and evenly coated with glue using a comb trowel. The greatest amount of glue is applied in the center of the product and along its contour. Experts say that at least 40% of the sheet area should be treated with an adhesive mixture.
You can begin to mount the first element - the quality of fastening of all other sheets will depend on the quality of its installation. The gaps between individual plates should be no wider than 2-3 mm, otherwise the coating will begin to deteriorate over time and cause the appearance of the so-called "cold bridges". If, for one reason or another, the gaps turned out to be too large, they must be blown out with polyurethane foam or even insert an additional insulation strip.
The heat insulator is finally fixed with front dowels, which can be either screw with a screw-type spacer, or driven with a nail-type spacer. They will take on the main load that the facade will experience. Therefore, the stability of the entire finished system may depend on the quality of the fasteners.
To calculate the number of required dowels, you need to take into account the individual characteristics of the facade - its weight, wind load, and so on. There is a rule: for each square meter of area, 5-6 dowels are hammered, if we are talking about a building up to 5 floors in height; for higher buildings, the number of fasteners increases to 8 pieces per 1 m2.
Reinforcement gives the system integrity and serves as the basis for subsequent decorative processing. For this, the heat insulator fixed on the wall is thickly greased with glue, into which a special reinforcing mesh is embedded. At this stage, you also need to pay attention to the quality of the work surface. If necessary, you can once again eliminate all defects and smooth out irregularities. You can use a hard float as a tool.
It is necessary to pay attention to the quality of the reinforced mesh - it must be impregnated with an alkaline composition, which will protect it from the harmful effects of the external environment. The product takes on many loads, so it is important that it is tensile and tear resistant.
When gluing it, it is necessary to overlap up to 10 cm, otherwise cracks and tears will appear at the joints. On the outer corners of the building, it makes sense to fix the profile corners, which can give them the correct shape and protect them from damage during operation.
How to insulate a facade with stone wool - watch the video:

Before starting work on insulation with stone or other mineral wool, you must carefully familiarize yourself with the technical side of the issue. Otherwise, material overruns are possible. For a warm, durable and aesthetically pleasing finish, it is best to opt for a technology called wet façade.